- お役立ち記事
- Collaborative strategy for mass production of motors and inverters for electric motorcycles and kickboards
月間76,176名の
製造業ご担当者様が閲覧しています*
*2025年3月31日現在のGoogle Analyticsのデータより
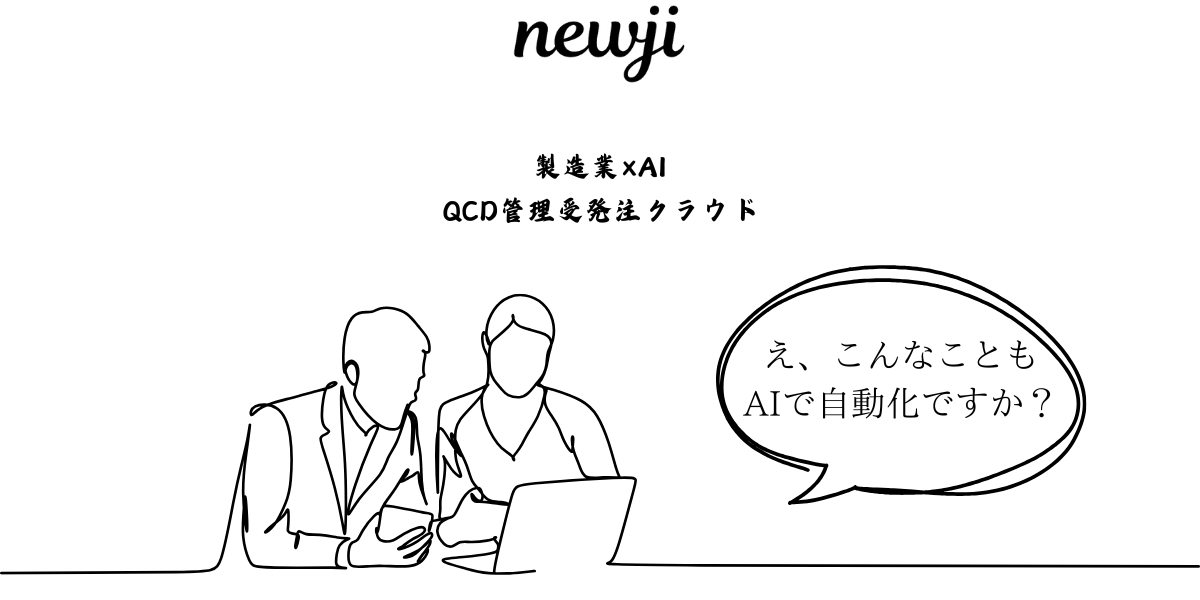
Collaborative strategy for mass production of motors and inverters for electric motorcycles and kickboards
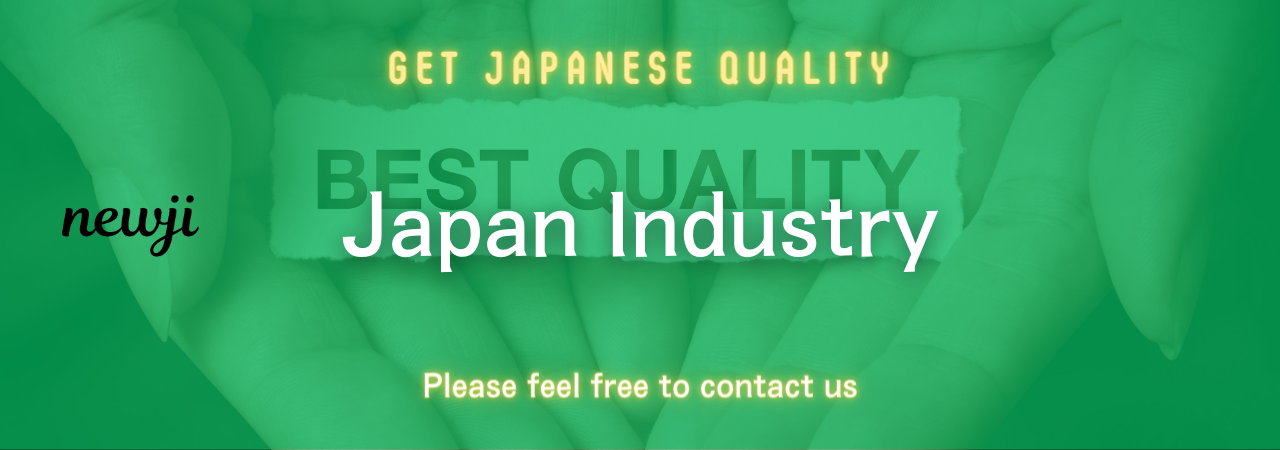
目次
Introduction to Collaborative Strategy
The landscape of transportation is undergoing a revolutionary transformation with the rise of electric vehicles (EVs).
Electric motorcycles and kickboards have gained significant attention as they offer an eco-friendly alternative to traditional gasoline-powered modes of transport.
A key component of these vehicles is their motors and inverters, which are crucial for efficient energy conversion and performance.
To meet the growing demand for these components, companies are turning to collaborative strategies for mass production.
The Growing Demand for Electric Motors and Inverters
As urban populations increase and environmental concerns become more pressing, there is a shift towards sustainable mobility solutions.
Electric motorcycles and kickboards provide a convenient, low-emission transportation option that fits seamlessly into urban areas.
With their increasing popularity, the demand for efficient and reliable electric motors and inverters has surged.
Manufacturers aim to produce these components at a scale that meets market demands, maintaining quality and affordability.
Benefits of Collaborative Production
One of the primary advantages of a collaborative strategy is cost efficiency.
By working together, companies can share resources, technology, and expertise.
This leads to reduced production costs, ultimately making electric motorcycles and kickboards more affordable for consumers.
Collaboration also fosters innovation, as companies can combine their expertise to develop cutting-edge technologies, further improving the performance and efficiency of electric motors and inverters.
Sharing Expertise and Resources
In a collaborative production model, companies can pool their knowledge and resources to achieve common goals.
For instance, a manufacturer with expertise in motor design can partner with a company specializing in inverter technology.
Together, they can create a superior product that leverages their strengths.
This collaborative approach not only accelerates the production process but also enhances the quality of the components produced.
Enhancing Innovation and Technology
Collaboration between companies often results in a vibrant exchange of ideas and innovations.
This synergy can lead to the development of new technologies that push the boundaries of what is possible in the realm of electric mobility.
By working together, companies can conduct joint research and development projects, leading to breakthroughs in motor efficiency, energy conservation, and smart inverter systems.
These advancements contribute to the overall improvement of electric motorcycles and kickboards.
Challenges in Collaborative Production
While collaborative strategies offer numerous benefits, they also come with their own set of challenges.
Coordinating between different companies, aligning goals, and sharing intellectual property can be complex and require careful management.
Coordination and Communication
Effective communication and coordination are critical to the success of any collaborative endeavor.
Companies must establish clear lines of communication to ensure that all parties are on the same page.
Regular meetings and updates can help avoid misunderstandings and keep the project on track.
Additionally, defining roles and responsibilities from the outset helps prevent conflicts and ensures a smooth workflow.
Intellectual Property Concerns
When multiple companies collaborate, the question of intellectual property rights often arises.
Clearly defining ownership of jointly developed technologies and innovations is essential to prevent disputes.
Establishing agreements on how intellectual property will be shared and utilized can protect the interests of all parties involved, fostering a more productive and harmonious collaboration.
Case Studies in Successful Collaboration
Several companies have successfully implemented collaborative strategies for the mass production of motors and inverters in electric motorcycles and kickboards.
Case Study 1: Global Tech and PowerDrive Solutions
Global Tech, a leading motor manufacturer, partnered with PowerDrive Solutions, an innovator in inverter technology.
Together, they combined their strengths to create a highly efficient motor-inverter system.
This collaboration reduced production costs by 20% and improved the performance of electric motorcycles by increasing their range by 15%.
The partnership exemplifies how two companies can pool their expertise to create a superior product that benefits both the industry and consumers.
Case Study 2: GreenMobility Inc. and EcoPower Systems
GreenMobility Inc., a pioneer in electric kickboards, joined hands with EcoPower Systems, known for its sustainable energy solutions.
The collaboration led to the development of an advanced motor system that extended the battery life of kickboards by 30%.
This breakthrough technology increased consumer interest in electric kickboards, propelling both companies to the forefront of the eco-friendly transport market.
The Future of Collaborative Production in Electric Mobility
As the demand for electric vehicles continues to grow, the importance of collaborative production strategies will only increase.
Companies that embrace these strategies can expect to achieve greater efficiency, innovation, and market competitiveness.
The success stories from the industry indicate a promising future for collaborations in electric mobility.
In conclusion, the collaborative strategy for mass production of motors and inverters is a pivotal approach to advancing the electric motorcycle and kickboard industry.
By sharing expertise and resources, companies can meet the growing demand for eco-friendly transportation solutions while driving innovation and reducing costs.
The challenges of coordination and intellectual property must be addressed to ensure successful collaborations, paving the way for a sustainable and green future.
資料ダウンロード
QCD管理受発注クラウド「newji」は、受発注部門で必要なQCD管理全てを備えた、現場特化型兼クラウド型の今世紀最高の受発注管理システムとなります。
ユーザー登録
受発注業務の効率化だけでなく、システムを導入することで、コスト削減や製品・資材のステータス可視化のほか、属人化していた受発注情報の共有化による内部不正防止や統制にも役立ちます。
NEWJI DX
製造業に特化したデジタルトランスフォーメーション(DX)の実現を目指す請負開発型のコンサルティングサービスです。AI、iPaaS、および先端の技術を駆使して、製造プロセスの効率化、業務効率化、チームワーク強化、コスト削減、品質向上を実現します。このサービスは、製造業の課題を深く理解し、それに対する最適なデジタルソリューションを提供することで、企業が持続的な成長とイノベーションを達成できるようサポートします。
製造業ニュース解説
製造業、主に購買・調達部門にお勤めの方々に向けた情報を配信しております。
新任の方やベテランの方、管理職を対象とした幅広いコンテンツをご用意しております。
お問い合わせ
コストダウンが利益に直結する術だと理解していても、なかなか前に進めることができない状況。そんな時は、newjiのコストダウン自動化機能で大きく利益貢献しよう!
(β版非公開)