- お役立ち記事
- Collection of purchasing department best practices to prevent procurement mistakes
月間76,176名の
製造業ご担当者様が閲覧しています*
*2025年3月31日現在のGoogle Analyticsのデータより
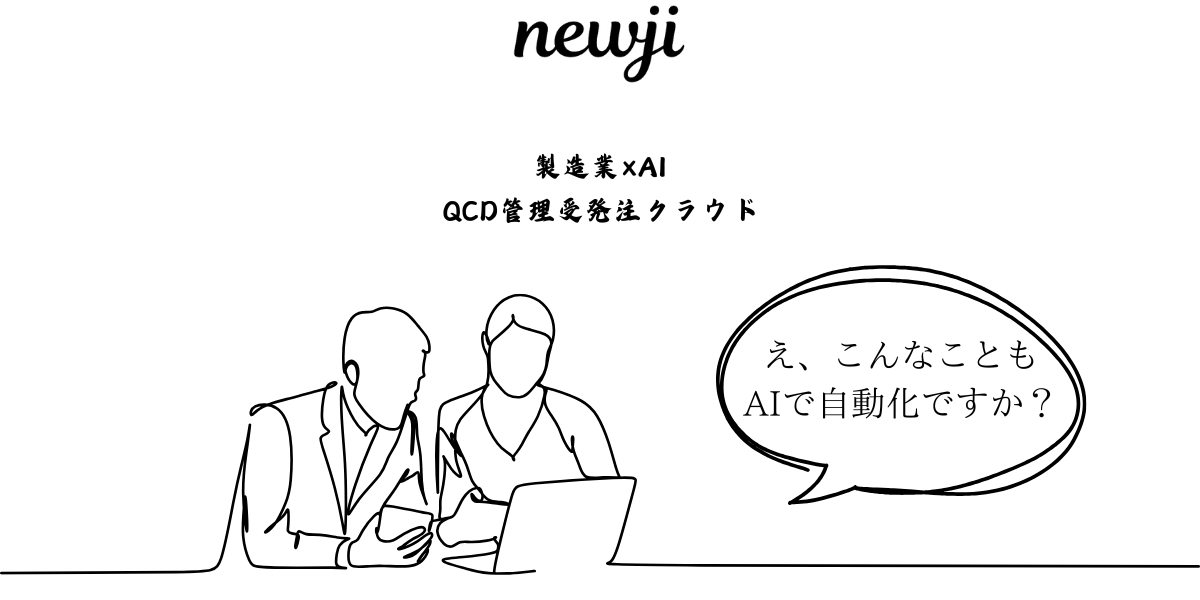
Collection of purchasing department best practices to prevent procurement mistakes
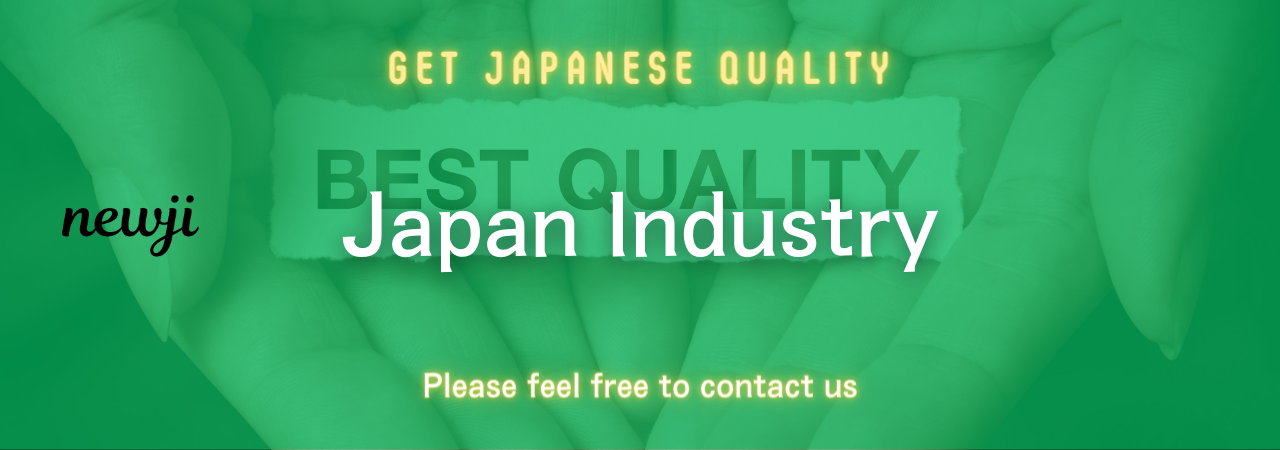
目次
Understanding the Role of the Purchasing Department
The purchasing department plays a critical role in every organization.
Its primary responsibility is to procure the necessary goods and services required for the business to operate effectively.
This department ensures that the company obtains quality products at competitive prices, ultimately impacting the bottom line.
To prevent procurement mistakes, it’s essential to understand the key functions and responsibilities of the purchasing department.
The purchasing department is involved in supplier selection, negotiations, and contract management.
These activities demand strategic thinking and a thorough understanding of the market landscape.
Consequently, they help the organization achieve its procurement goals, minimize costs, and maintain smooth operations.
Implementing Best Practices for Supplier Relationships
One of the most effective ways to prevent procurement mistakes is by establishing strong supplier relationships.
Building a solid rapport with suppliers can lead to improved communication, better pricing, and more reliable delivery schedules.
To maintain these beneficial relationships, it is crucial to implement best practices.
Regular Communication
Regularly communicating with suppliers keeps both parties informed and aligned with each other’s expectations.
Maintaining open channels for dialogue can help quickly resolve any issues and avoid misunderstandings.
Moreover, regular communication builds trust and strengthens the partnership over time.
Performance Reviews
Conducting regular supplier performance reviews is another best practice.
By assessing a supplier’s performance, the purchasing department can identify areas for improvement and recognize when a supplier consistently meets or exceeds expectations.
This information helps in making informed decisions about future procurement activities.
Long-term Partnerships
Instead of frequently changing suppliers, consider cultivating long-term partnerships with select vendors.
This can lead to better pricing agreements, more significant discounts, and consistent quality.
Long-term collaborations enable suppliers to understand the company’s requirements deeply, which can result in more tailored and effective service offerings.
Streamlining the Procurement Process with Technology
Technology plays a pivotal role in enhancing the efficiency and accuracy of the procurement process.
Implementing advanced tools and software can help the purchasing department prevent mistakes and streamline operations.
Automated Purchase Orders
Utilizing software for automated purchase orders is one effective way to prevent errors that might arise from manual entry.
Automation ensures that orders are processed accurately and swiftly, reducing the risk of human mistakes and delays.
This results in a more efficient procurement cycle and faster fulfillment.
Inventory Management Systems
Implementing an inventory management system helps keep track of stock levels and predict future needs accurately.
By having real-time access to inventory data, the purchasing department can avoid over-ordering or stockouts.
This also helps ensure that procurement aligns closely with the company’s operational needs.
Spend Analysis Tools
Using spend analysis tools provides valuable insights into the organization’s spending patterns.
These tools help identify areas for cost savings and highlight potential efficiencies within the procurement process.
Through detailed analysis, the purchasing department can make informed decisions that optimize budget usage.
Prioritizing Quality Control Measures
To prevent procurement mistakes, it is vital to implement robust quality control measures.
Such measures ensure that all procured goods meet the company’s standards and requirements.
Defining Clear Specifications
Before making any purchase, it’s crucial to define clear and precise specifications for the required goods or services.
These specifications serve as guidelines for suppliers and help reduce the risk of receiving substandard or incorrect products.
Detailed specifications also facilitate better communication between the purchasing department and suppliers.
Quality Inspections Upon Delivery
Conducting thorough quality inspections upon delivery ensures that all items meet the established criteria.
This practice helps catch any defects or discrepancies early, allowing immediate corrective actions.
Regular inspections can also identify trends in supplier performance that might require attention.
Supplier Quality Audits
Carrying out periodic supplier quality audits verifies their adherence to the company’s standards.
An audit evaluates various factors like production processes, compliance with industry regulations, and environmental considerations.
These audits confirm that suppliers maintain the quality levels promised during selection and contracting.
Fostering a Culture of Continuous Improvement
A culture of continuous improvement is crucial for minimizing procurement mistakes.
Encouraging team members to seek out better methods and embrace innovation can lead to significant benefits for the purchasing department.
Encourage feedback from team members to identify areas for improvement.
Listening to those directly involved in procurement processes can uncover challenges and offer solutions.
Prioritizing ongoing training ensures the team remains updated on industry trends, technological advancements, and best practices.
Therefore, fostering a culture that values growth and adaptability can propel the purchasing department toward long-term success.
With these practices in place, organizations can cultivate an efficient procurement process that delivers consistent and reliable results.
By emphasizing supplier relationships, leveraging technology, maintaining quality control measures, and nurturing a culture of improvement, businesses can effectively prevent procurement mistakes and drive sustainable growth.
資料ダウンロード
QCD管理受発注クラウド「newji」は、受発注部門で必要なQCD管理全てを備えた、現場特化型兼クラウド型の今世紀最高の受発注管理システムとなります。
ユーザー登録
受発注業務の効率化だけでなく、システムを導入することで、コスト削減や製品・資材のステータス可視化のほか、属人化していた受発注情報の共有化による内部不正防止や統制にも役立ちます。
NEWJI DX
製造業に特化したデジタルトランスフォーメーション(DX)の実現を目指す請負開発型のコンサルティングサービスです。AI、iPaaS、および先端の技術を駆使して、製造プロセスの効率化、業務効率化、チームワーク強化、コスト削減、品質向上を実現します。このサービスは、製造業の課題を深く理解し、それに対する最適なデジタルソリューションを提供することで、企業が持続的な成長とイノベーションを達成できるようサポートします。
製造業ニュース解説
製造業、主に購買・調達部門にお勤めの方々に向けた情報を配信しております。
新任の方やベテランの方、管理職を対象とした幅広いコンテンツをご用意しております。
お問い合わせ
コストダウンが利益に直結する術だと理解していても、なかなか前に進めることができない状況。そんな時は、newjiのコストダウン自動化機能で大きく利益貢献しよう!
(β版非公開)