- お役立ち記事
- Collection of solutions for logistics issues faced by purchasing departments in the global market
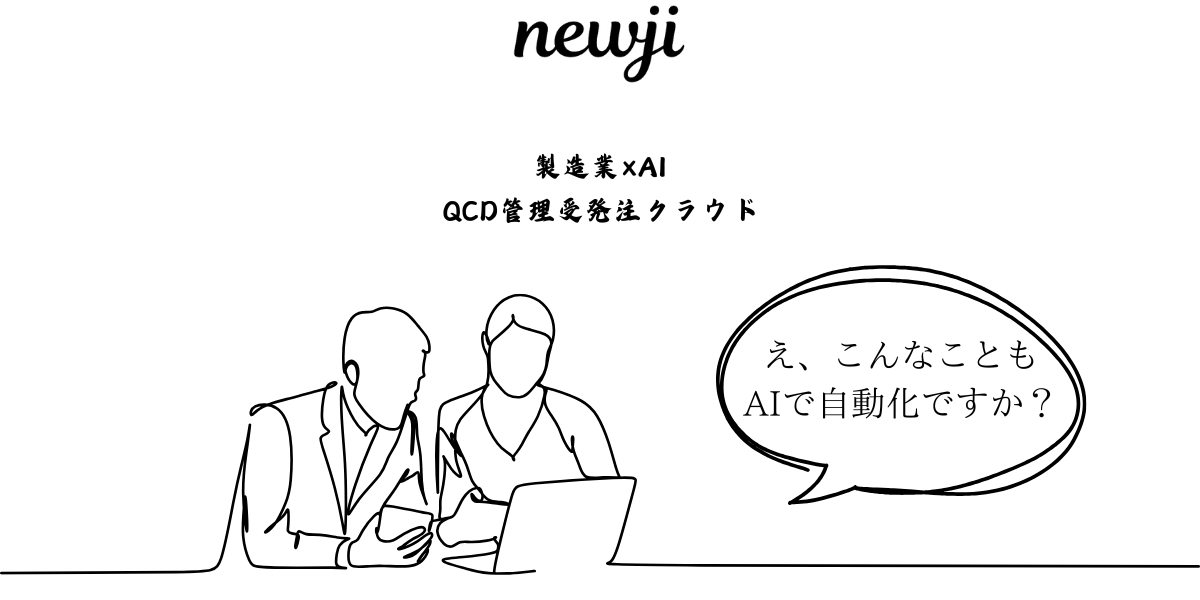
Collection of solutions for logistics issues faced by purchasing departments in the global market
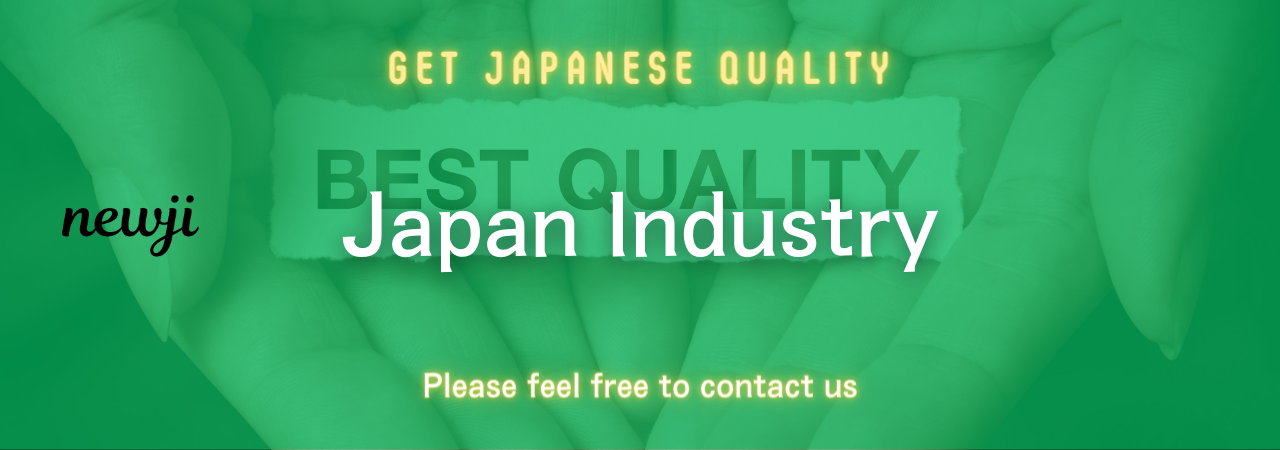
目次
Introduction
In today’s fast-paced global market, purchasing departments face numerous challenges in logistics.
With the ever-growing demand for efficient supply chains, the pressure is on to minimize costs and improve delivery times.
Addressing these logistics issues is crucial for companies to stay competitive and meet customer expectations.
Understanding Logistics Issues
Purchasing departments encounter several logistics issues in the global market.
1. Supply Chain Complexity
The complexity of managing supply chains across multiple countries is a significant hurdle.
Goods travel across various regions, each with its regulations, tariffs, and customs procedures.
This complexity can lead to delays and increased costs.
2. Fluctuating Transportation Costs
Transportation costs can fluctuate due to fuel prices, labor rates, and geopolitical issues.
Purchasing departments must constantly negotiate rates with shipping companies and adjust budgets accordingly.
Managing these variations efficiently is essential to ensure cost-effective logistics solutions.
3. Demand Forecasting
Accurate demand forecasting is essential to optimize inventory levels and reduce excess stock.
Global markets are volatile, and sudden shifts in consumer demand can lead to overstocking or stockouts.
Implementing advanced forecasting tools and strategies can help purchasing departments anticipate demand changes.
4. Supplier Reliability
Reliability and consistency from suppliers are crucial for smooth logistics operations.
Delays or errors from suppliers can cascade through the supply chain, resulting in missed deadlines and customer dissatisfaction.
Building strong relationships and performance management with suppliers can mitigate these risks.
Solutions for Logistics Issues
To tackle these logistics challenges, purchasing departments can explore various solutions.
1. Leverage Technology
Investing in technology is key to optimizing logistics operations.
Adopting supply chain management software can enhance visibility and streamline processes.
These tools enable real-time tracking of shipments, inventory management, and data analytics for better decision-making.
2. Optimize Inventory Management
Implementing just-in-time inventory systems can reduce storage costs and improve efficiency.
By synchronizing production schedules with demand forecasts, companies can minimize excess stock.
This approach requires close coordination with suppliers to ensure timely deliveries.
3. Foster Collaborative Relationships
Collaboration with suppliers, logistics providers, and other stakeholders is crucial for effective logistics management.
Establishing long-term partnerships can lead to better terms, increased reliability, and shared objectives.
Regular communication and performance evaluations can strengthen these relationships.
4. Implement Risk Management Strategies
Identifying and mitigating risks is essential for resilient logistics operations.
Purchasing departments should assess risks such as geopolitical instability, natural disasters, and supplier disruptions.
Developing contingency plans and diversifying suppliers can reduce vulnerabilities and maintain supply chain continuity.
5. Focus on Sustainable Practices
Sustainability is becoming increasingly important in logistics.
Purchasing departments can explore eco-friendly transportation options and packaging materials.
Implementing green practices not only benefits the environment but can also lead to cost savings and brand enhancement.
Case Studies
To understand the real-world application of these solutions, let’s look at some case studies.
1. XYZ Electronics
XYZ Electronics faced issues with fluctuating transportation costs and unreliable suppliers.
By adopting supply chain management software, they gained real-time insights into their logistics network.
This enabled them to negotiate better rates with carriers and improve supplier performance through data-driven evaluations.
2. Global Apparel Co.
Global Apparel Co. struggled with demand forecasting inaccuracies leading to excess inventory.
They implemented advanced forecasting algorithms, which helped align production schedules with market demand.
The result was reduced storage costs and improved cash flow.
Conclusion
Purchasing departments in the global market face persistent logistics issues that require strategic solutions.
By leveraging technology, optimizing inventory management, and fostering collaborative relationships, companies can enhance logistics efficiency.
Implementing risk management strategies and focusing on sustainability further strengthens supply chains.
Embracing these solutions enables purchasing departments to overcome logistics challenges, stay competitive, and deliver exceptional customer service.
資料ダウンロード
QCD調達購買管理クラウド「newji」は、調達購買部門で必要なQCD管理全てを備えた、現場特化型兼クラウド型の今世紀最高の購買管理システムとなります。
ユーザー登録
調達購買業務の効率化だけでなく、システムを導入することで、コスト削減や製品・資材のステータス可視化のほか、属人化していた購買情報の共有化による内部不正防止や統制にも役立ちます。
NEWJI DX
製造業に特化したデジタルトランスフォーメーション(DX)の実現を目指す請負開発型のコンサルティングサービスです。AI、iPaaS、および先端の技術を駆使して、製造プロセスの効率化、業務効率化、チームワーク強化、コスト削減、品質向上を実現します。このサービスは、製造業の課題を深く理解し、それに対する最適なデジタルソリューションを提供することで、企業が持続的な成長とイノベーションを達成できるようサポートします。
オンライン講座
製造業、主に購買・調達部門にお勤めの方々に向けた情報を配信しております。
新任の方やベテランの方、管理職を対象とした幅広いコンテンツをご用意しております。
お問い合わせ
コストダウンが利益に直結する術だと理解していても、なかなか前に進めることができない状況。そんな時は、newjiのコストダウン自動化機能で大きく利益貢献しよう!
(Β版非公開)