- お役立ち記事
- Common Issues in Polypropylene Processing and How to Avoid Them
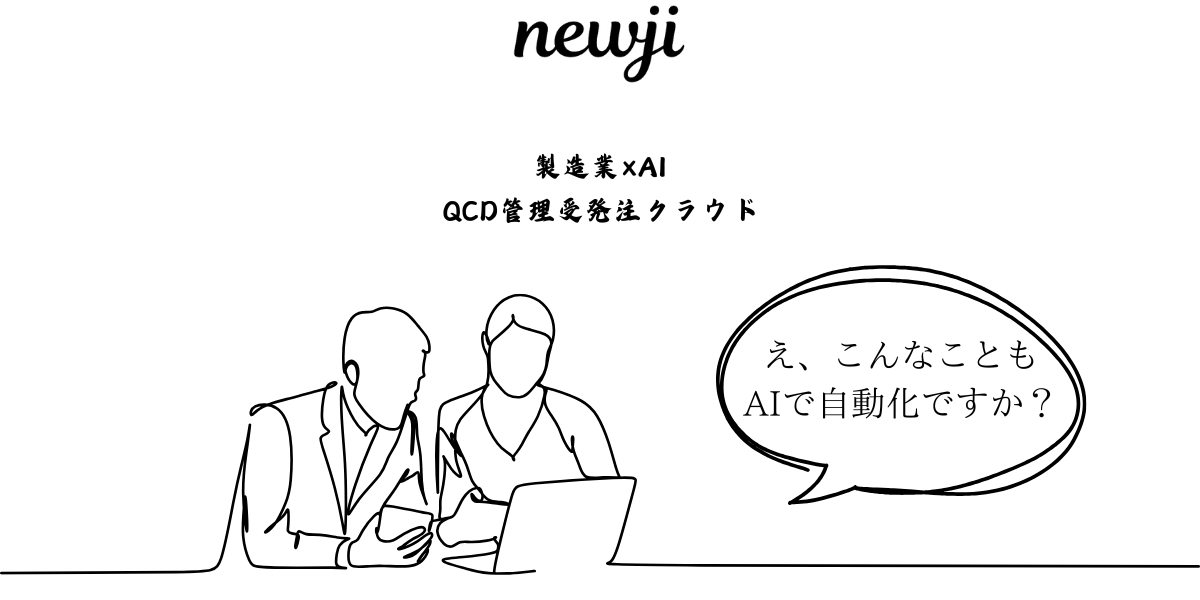
Common Issues in Polypropylene Processing and How to Avoid Them
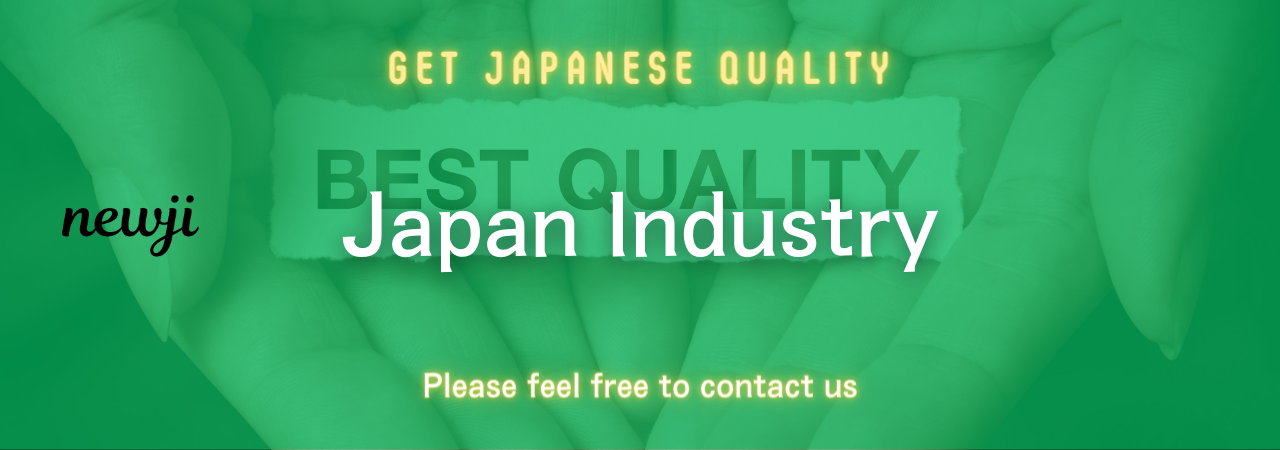
目次
Understanding Polypropylene
Polypropylene is a popular thermoplastic polymer used in a wide range of applications due to its durability, flexibility, and resistance to various chemicals.
It’s prevalent in industries such as automotive, packaging, and textiles.
Despite its versatility, processing polypropylene can present specific challenges that professionals need to address effectively.
Common Processing Issues
1. Warping
Warping is a typical issue encountered with polypropylene products, especially when cooling rates are not uniform.
This problem occurs when different sections of a product cool at different speeds, leading to uneven shrinkage and distortion.
It affects the product’s aesthetic and can compromise its functionality.
2. Poor Surface Finish
Another issue frequently faced is achieving a poor surface finish.
This can be attributed to improper mold temperatures, inadequate mold design, or the use of low-quality polypropylene.
A rough surface not only diminishes the product’s appearance but can also affect its performance.
3. Uneven Distribution of Pigments
Achieving consistent color can be challenging with polypropylene due to its semi-crystalline nature.
This can result in uneven pigment distribution, leaving the final product with blotches of different shades.
Such inconsistencies are often caused by inadequate mixing or incorrect temperature regulation during processing.
4. Brittleness
Brittleness in polypropylene can occur due to inappropriate selection of polymer grade or improper processing conditions.
This issue might lead to product failure under stress or impact, posing significant challenges for manufacturers aiming for high-quality standards.
Ways to Avoid Common Issues
1. Control Cooling Rates
To prevent warping, it’s crucial to manage the cooling rates carefully by ensuring uniform cooling throughout the product.
Use of mold temperature controllers can help maintain consistent temperatures.
Properly designing the flow path and ensuring even wall thickness are crucial steps in avoiding excessive shrinkage.
2. Optimize Mold Design and Material Quality
A high-quality surface finish requires optimal mold design, which includes smooth surfaces and appropriate mold temperatures.
Additionally, using high-grade polypropylene with the right additives can help minimize surface defects.
Working with precise temperature settings is also necessary to achieve a superior finish.
3. Improve Mixing and Temperature Control
To address pigment distribution issues, thorough mixing during the compounding stage is imperative.
This can be achieved by using twin-screw extruders for better mixing uniformity.
Controlling the melt temperature is essential to ensure even flow and distribution of pigments.
4. Select the Appropriate Polymer Grade and Conditions
Choosing the correct grade of polypropylene for the specific application can greatly reduce brittleness issues.
Adjusting processing parameters, such as extrusion speed and shear, is necessary to maintain polymer integrity.
Using elastomer modifiers can enhance flexibility and reduce brittleness in the final product.
Conclusion
Processing polypropylene successfully requires attention to detail and a keen understanding of the material’s properties.
By recognizing common issues such as warping, poor surface finish, uneven pigment distribution, and brittleness, professionals can take proactive measures to mitigate them.
Implementing thoughtful strategies, such as careful management of cooling rates, optimizing mold design, ensuring high-quality material, and precise control over processing parameters, ensures the production of high-quality polypropylene products.
Armed with these insights, manufacturers can effectively meet and exceed industry standards, delivering reliable and visually appealing polypropylene products.
資料ダウンロード
QCD調達購買管理クラウド「newji」は、調達購買部門で必要なQCD管理全てを備えた、現場特化型兼クラウド型の今世紀最高の購買管理システムとなります。
ユーザー登録
調達購買業務の効率化だけでなく、システムを導入することで、コスト削減や製品・資材のステータス可視化のほか、属人化していた購買情報の共有化による内部不正防止や統制にも役立ちます。
NEWJI DX
製造業に特化したデジタルトランスフォーメーション(DX)の実現を目指す請負開発型のコンサルティングサービスです。AI、iPaaS、および先端の技術を駆使して、製造プロセスの効率化、業務効率化、チームワーク強化、コスト削減、品質向上を実現します。このサービスは、製造業の課題を深く理解し、それに対する最適なデジタルソリューションを提供することで、企業が持続的な成長とイノベーションを達成できるようサポートします。
オンライン講座
製造業、主に購買・調達部門にお勤めの方々に向けた情報を配信しております。
新任の方やベテランの方、管理職を対象とした幅広いコンテンツをご用意しております。
お問い合わせ
コストダウンが利益に直結する術だと理解していても、なかなか前に進めることができない状況。そんな時は、newjiのコストダウン自動化機能で大きく利益貢献しよう!
(Β版非公開)