- お役立ち記事
- Common Problems and Solutions in Polycarbonate Processing
月間76,176名の
製造業ご担当者様が閲覧しています*
*2025年3月31日現在のGoogle Analyticsのデータより
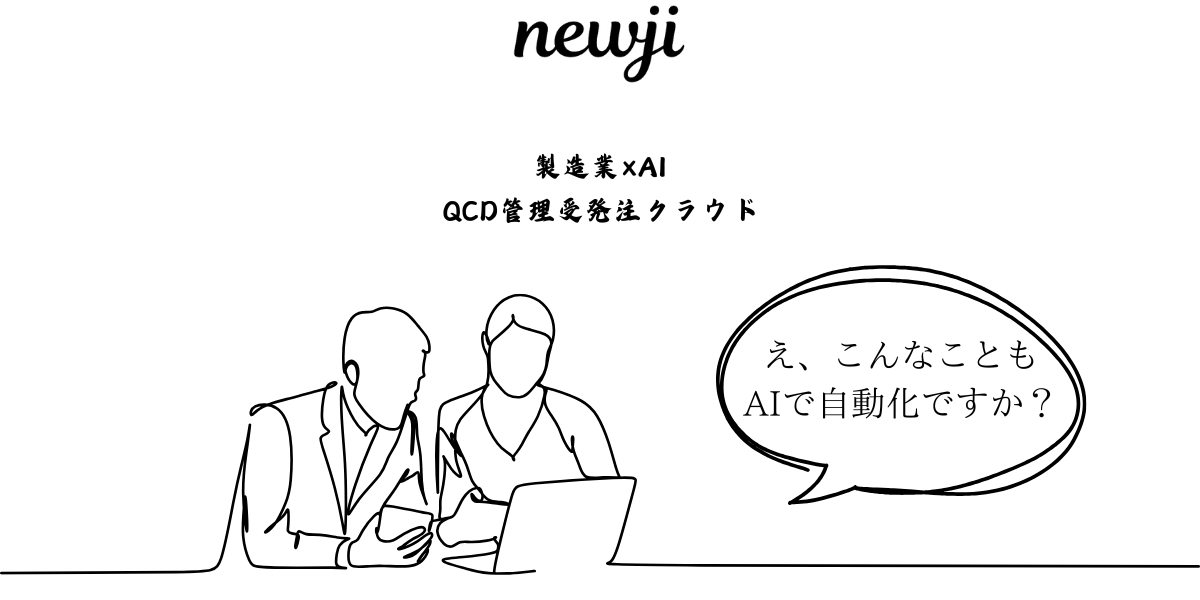
Common Problems and Solutions in Polycarbonate Processing
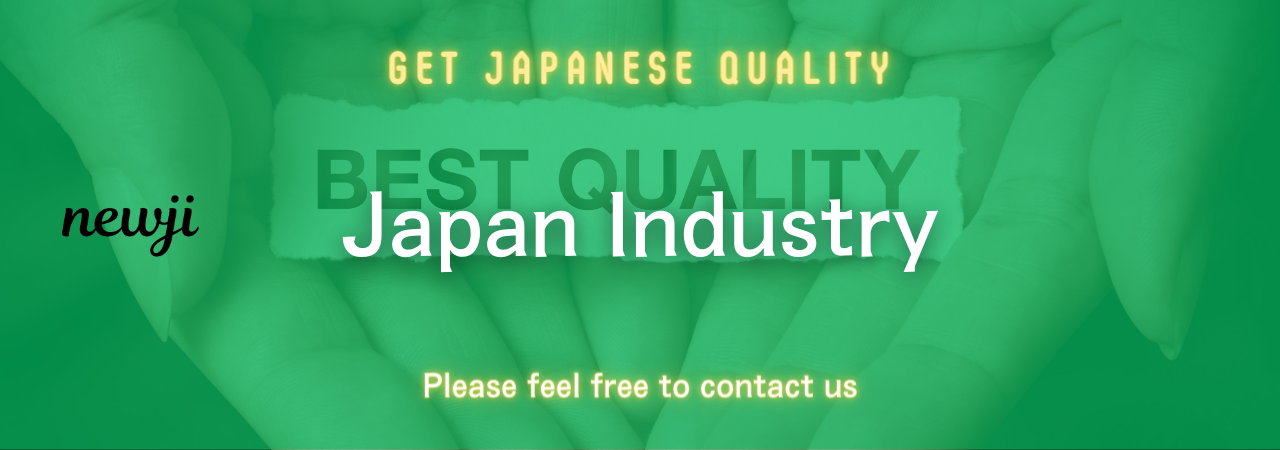
目次
Understanding Polycarbonate Processing
Polycarbonate is a versatile and durable material used in various industries, from automotive to electronics.
It’s known for its toughness, clarity, and impact resistance, making it ideal for manufacturing items like eyewear lenses, CDs, and safety helmets.
Despite its many advantages, processing polycarbonate can pose several challenges.
However, understanding common problems and their solutions can help in achieving optimal results in polycarbonate processing.
Problem: High Processing Temperatures
One of the primary challenges in processing polycarbonate is the high temperature required.
Polycarbonate requires a melting temperature range of around 270-310°C (518-590°F), which is considerably higher than many other plastics.
At such temperatures, there is a risk of degradation if not managed properly.
Solution
To handle high processing temperatures, it is essential to ensure that the machinery is properly calibrated and maintained.
Using high-performance tools specifically designed for high-heat materials can also help.
Additionally, maintaining a stable and consistent temperature throughout the process is crucial to prevent thermal degradation.
Problem: Moisture Sensitivity
Polycarbonate is hygroscopic, meaning it absorbs moisture from the air.
Moisture-sensitive materials like polycarbonate can suffer from hydrolysis or chemical breakdown, causing defects in the final product, such as bubbles or a cloudy appearance.
Solution
Pre-drying the polycarbonate granules before processing can significantly mitigate moisture-related problems.
Using a desiccant air dryer with a dew point of -40°C and maintaining drying times of 3 to 6 hours at temperatures between 120-130°C ensures that the material is free from excess moisture.
Regular monitoring and maintenance of drying equipment can also prevent moisture absorption during storage.
Problem: Thermal Degradation
Thermal degradation is another issue that can occur when polycarbonate is subjected to excessive heat or incorrect processing conditions.
This can lead to a breakdown in the material’s physical properties, resulting in discolored and brittle final products.
Solution
To prevent thermal degradation, it is important to avoid long residence times in machinery and to process polycarbonate at the recommended temperatures.
Adjusting the mold temperature to ensure rapid cooling post-molding can also reduce the risk of thermal degradation.
Using stabilizers that are specifically designed for polycarbonate can protect the material from thermal damage during processing.
Problem: Warping and Dimensional Instability
Warping and instability in the dimensions of polycarbonate products can occur due to uneven cooling or improper mold design.
This can lead to parts that do not fit correctly or function as intended.
Solution
Maintaining uniform thickness in the design phase and using proper mold designs with adequate cooling channels is crucial.
The cooling process should be controlled carefully, allowing even cooling across the entire part.
Furthermore, using mold temperature control units can help regulate and maintain ideal conditions within the mold.
Problem: Difficulty in Coloring
Coloring polycarbonate can be challenging due to its transparency and resistance to pigments.
Improper mixing can result in streaks or inconsistent coloring throughout the product.
Solution
Using color concentrates specifically designed for polycarbonate is recommended for achieving uniformity in coloring.
Thorough mixing and the use of specialized equipment can help in achieving the desired color without affecting the material’s properties.
Testing the colorant in small batches can also help ensure consistent results before large-scale production.
Problem: Surface Defects
Scratches, burns, or splay marks can occur on the surface of polycarbonate products due to improper handling or incorrect machine settings.
These defects can negatively affect the appearance and functional quality of the product.
Solution
To minimize surface defects, ensure that the mold and machinery are clean and free from contaminants.
Adjusting mold temperatures and injection speeds can also reduce the occurrence of surface defects.
Many manufacturers find success by implementing regular quality checks during production to identify and fix issues early.
Conclusion
Polycarbonate processing presents several challenges, but understanding these common problems and employing effective solutions can lead to high-quality products.
Maintaining proper temperature control, minimizing moisture absorption, preventing thermal degradation, and optimizing mold design are essential practices.
It’s also crucial to pay attention to surface finishes and coloring techniques.
By addressing these aspects, the processing of polycarbonate can yield durable, aesthetically pleasing, and functionally robust products.
資料ダウンロード
QCD管理受発注クラウド「newji」は、受発注部門で必要なQCD管理全てを備えた、現場特化型兼クラウド型の今世紀最高の受発注管理システムとなります。
ユーザー登録
受発注業務の効率化だけでなく、システムを導入することで、コスト削減や製品・資材のステータス可視化のほか、属人化していた受発注情報の共有化による内部不正防止や統制にも役立ちます。
NEWJI DX
製造業に特化したデジタルトランスフォーメーション(DX)の実現を目指す請負開発型のコンサルティングサービスです。AI、iPaaS、および先端の技術を駆使して、製造プロセスの効率化、業務効率化、チームワーク強化、コスト削減、品質向上を実現します。このサービスは、製造業の課題を深く理解し、それに対する最適なデジタルソリューションを提供することで、企業が持続的な成長とイノベーションを達成できるようサポートします。
製造業ニュース解説
製造業、主に購買・調達部門にお勤めの方々に向けた情報を配信しております。
新任の方やベテランの方、管理職を対象とした幅広いコンテンツをご用意しております。
お問い合わせ
コストダウンが利益に直結する術だと理解していても、なかなか前に進めることができない状況。そんな時は、newjiのコストダウン自動化機能で大きく利益貢献しよう!
(β版非公開)