- お役立ち記事
- Common Problems and Solutions in Purchasing Management for SMEs
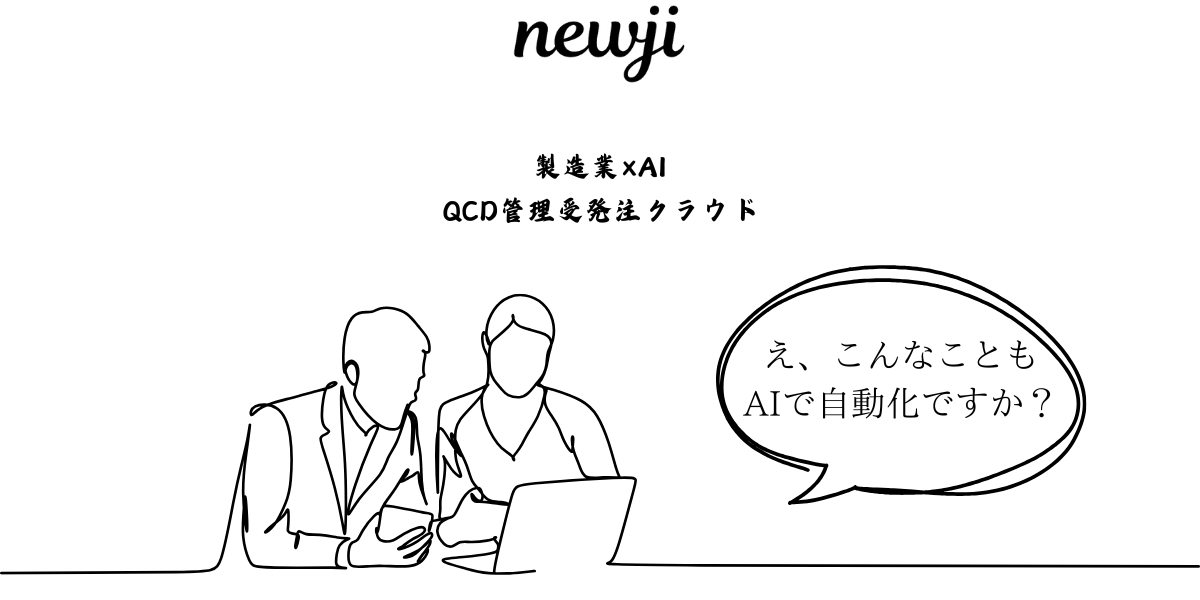
Common Problems and Solutions in Purchasing Management for SMEs
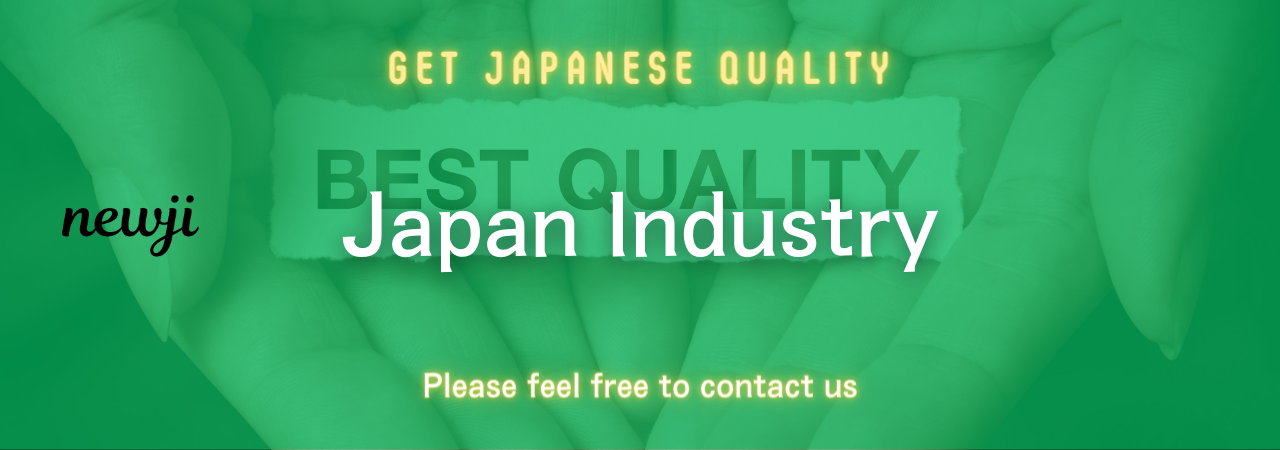
Purchasing management is a critical function for Small and Medium-sized Enterprises (SMEs).
It involves acquiring goods and services essential for operations.
Despite its significance, SMEs often encounter common problems that can hinder efficient purchasing management.
This article explores these issues and provides practical solutions to address them.
目次
Lack of Supplier Relationships
Building strong relationships with suppliers is essential.
SMEs often struggle in this area due to limited resources or networks.
Without established relationships, they may face unreliable delivery times, inflated costs, or subpar product quality.
Solution
To mitigate this, SMEs should invest time in researching and vetting potential suppliers.
Attend industry trade shows, join online forums, and utilize social media platforms like LinkedIn to make connections.
Maintaining constant communication and honoring commitments can further strengthen these relationships.
Establishing long-term contracts may also incentivize suppliers to prioritize your business, leading to more favorable terms.
Inconsistent Ordering Processes
SMEs may lack standardized procedures for placing orders.
This inconsistency can result in over-ordering, under-ordering, and inefficiencies.
Solution
Implementing a standardized ordering system is crucial.
Use digital tools and software to automate and track orders.
Establish clear guidelines and employee training to ensure everyone follows the same procedures.
A well-documented process reduces errors and enhances efficiency.
Limited Financial Resources
Financial constraints are a common challenge for SMEs.
It can affect their ability to negotiate better deals or purchase in bulk.
Solution
Develop a clear purchasing budget, prioritizing essential items.
Explore various financing options, such as trade credit or small business loans, to ease cash flow pressures.
Consider joining buying groups or cooperatives that allow collective purchasing to benefit from bulk discounts and shared resources.
Inventory Management Issues
Poor inventory management can lead to overstocking, stockouts, and increased holding costs.
This is especially problematic for SMEs with limited storage space.
Solution
Invest in inventory management software to monitor stock levels in real-time.
Implement Just-In-Time (JIT) inventory systems to reduce holding costs and minimize waste.
Regularly review inventory performance and adjust purchasing strategies to align with demand trends.
Lack of Data Analysis
SMEs often do not utilize data analytics to inform their purchasing decisions.
Without data-driven insights, they may miss opportunities for cost savings or efficiencies.
Solution
Begin collecting and analyzing relevant purchasing data.
Use Key Performance Indicators (KPIs) to track purchasing efficiency, supplier performance, and cost trends.
Invest in analytics tools and training to better understand these metrics.
Data-driven decisions help optimize purchasing strategies and reduce costs.
Compliance and Regulatory Challenges
Navigating compliance and regulatory requirements can be complex for SMEs.
Non-compliance can result in fines and operational disruptions.
Solution
Stay informed about relevant regulations and standards in your industry.
Implement compliance checks within your purchasing process.
Consider consulting with industry experts or legal advisors to ensure adherence to regulations.
Regular audits can also help maintain compliance.
Supplier Dependence
Relying heavily on a single supplier can pose risks, such as supply chain disruptions or price increases.
Solution
Diversify your supplier base to reduce dependence on any single supplier.
Develop contingency plans and maintain a list of alternative suppliers.
Regularly evaluate supplier performance and market conditions to adapt your strategies accordingly.
Poor Quality Control
Ensuring product quality is crucial.
Inadequate quality control can lead to product returns, customer dissatisfaction, and reputational damage.
Solution
Establish rigorous quality control procedures.
Communicate quality expectations clearly to suppliers.
Conduct regular inspections and audits to ensure compliance with standards.
Feedback from customers can also provide valuable insights for quality improvement.
Technology Integration
Many SMEs struggle with integrating new technologies into their purchasing processes.
Outdated methods can lead to inefficiencies and errors.
Solution
Invest in modern purchasing software and tools.
Training employees on new technologies ensures smooth integration.
Conduct regular assessments to determine areas where technology can enhance efficiency.
Embracing technology streamlines processes and reduces errors.
Conclusion
Purchasing management is an intricate function that significantly impacts the success of SMEs.
By understanding and addressing common problems, SMEs can streamline their purchasing processes and improve overall efficiency.
Investing in relationships, leveraging technology, and utilizing data-driven strategies are key to overcoming these challenges.
With the right solutions, SMEs can optimize their purchasing management and set a strong foundation for growth and sustainability.
資料ダウンロード
QCD調達購買管理クラウド「newji」は、調達購買部門で必要なQCD管理全てを備えた、現場特化型兼クラウド型の今世紀最高の購買管理システムとなります。
ユーザー登録
調達購買業務の効率化だけでなく、システムを導入することで、コスト削減や製品・資材のステータス可視化のほか、属人化していた購買情報の共有化による内部不正防止や統制にも役立ちます。
NEWJI DX
製造業に特化したデジタルトランスフォーメーション(DX)の実現を目指す請負開発型のコンサルティングサービスです。AI、iPaaS、および先端の技術を駆使して、製造プロセスの効率化、業務効率化、チームワーク強化、コスト削減、品質向上を実現します。このサービスは、製造業の課題を深く理解し、それに対する最適なデジタルソリューションを提供することで、企業が持続的な成長とイノベーションを達成できるようサポートします。
オンライン講座
製造業、主に購買・調達部門にお勤めの方々に向けた情報を配信しております。
新任の方やベテランの方、管理職を対象とした幅広いコンテンツをご用意しております。
お問い合わせ
コストダウンが利益に直結する術だと理解していても、なかなか前に進めることができない状況。そんな時は、newjiのコストダウン自動化機能で大きく利益貢献しよう!
(Β版非公開)