- お役立ち記事
- Communication strategy to improve productivity of purchasing department in collaboration with manufacturing site
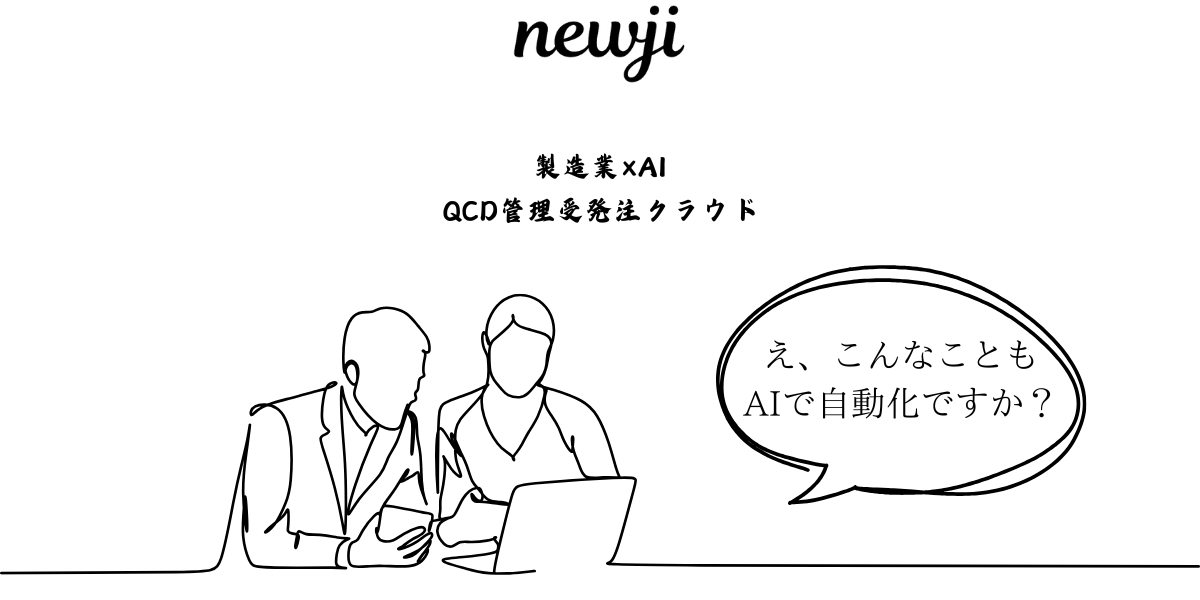
Communication strategy to improve productivity of purchasing department in collaboration with manufacturing site
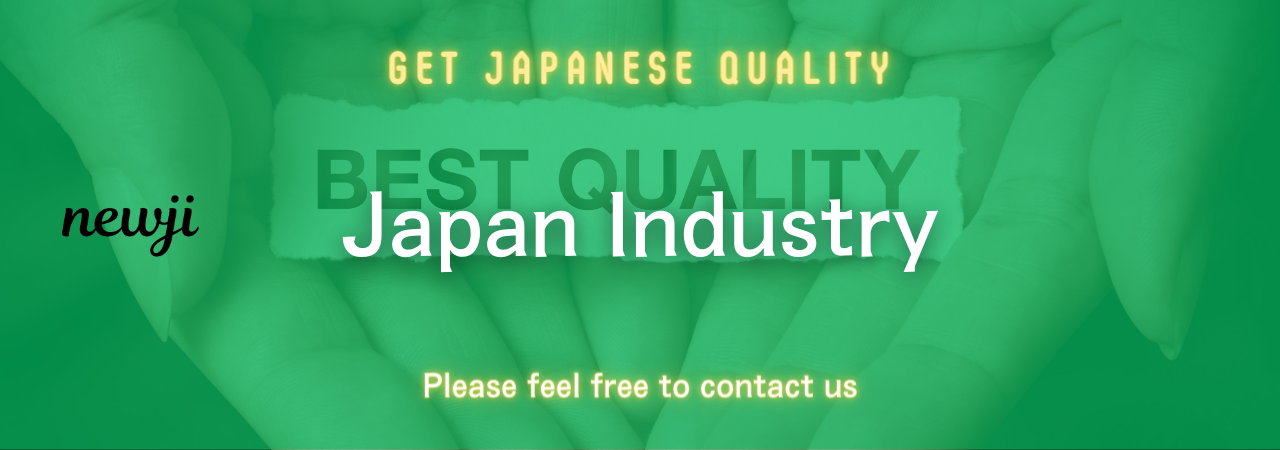
目次
Understanding the Role of Communication in Purchasing
Effective communication within an organization is crucial, especially between the purchasing department and the manufacturing site.
When these two entities work closely, they can significantly improve the overall productivity of the company.
The purchasing department is responsible for procuring materials needed for production, while the manufacturing site transforms these materials into finished products.
Clear and concise communication ensures that the exact materials needed are delivered on time, reducing the likelihood of production delays.
Moreover, streamlined communication helps in managing inventory efficiently, avoiding overstock or stockouts that can interrupt the production process.
Understanding the importance of communication sets the groundwork for formulating a strategy that boosts productivity.
Analyzing Current Communication Methods
Before implementing any strategy, it’s vital to assess the existing communication methods between the purchasing department and the manufacturing site.
You need to identify the channels currently in use, such as emails, phone calls, meetings, or supply chain management software.
Evaluate the effectiveness of these channels by considering aspects like how quickly issues are resolved and how accurately information is shared.
It’s important to involve the employees in this evaluation because they are the ones using these tools daily.
Gather their feedback on what works, what doesn’t, and any challenges they face in communicating.
This analysis serves as a baseline to measure future improvements and helps you understand where enhancements are necessary.
Establishing a Clear Communication Protocol
Once you’ve analyzed the current methods, the next step is to establish a clear communication protocol.
This involves setting guidelines on how and when information should be shared between the purchasing department and manufacturing site.
Create a standard operating procedure (SOP) that outlines the specific steps for communication.
Include details on whom to contact for various issues, the preferred modes of communication, and expected response times.
The protocol should foster open lines of communication, encouraging team members to ask questions and seek clarifications without hesitation.
Having an SOP helps in minimizing misunderstandings and ensures that everyone is on the same page.
Regular training sessions on using these protocols effectively can further bolster collaboration between the teams.
Leveraging Technology for Seamless Communication
In today’s digital age, technology plays a pivotal role in enhancing communication within organizations.
Invest in advanced communication tools and software that facilitate real-time information exchange between the purchasing and manufacturing departments.
Consider implementing collaborative platforms like Slack or Microsoft Teams, which offer instant messaging, video conferencing, and file sharing.
These tools allow for faster decision-making and problem-solving, directly contributing to increased productivity.
Another technological advancement to consider is integrating supply chain management systems that provide visibility into inventory levels and supply chain activities.
This integration lets both departments access updated information, reducing the risk of miscommunication and improving coordination.
Encouraging Regular Collaboration Meetings
In-person interactions, albeit less frequent in the digital world, are still valuable in fostering strong communication between teams.
Regular collaboration meetings should be scheduled, allowing members from the purchasing department and manufacturing site to discuss current projects, challenges, and future goals.
These meetings should have a clear agenda and focus on resolving any issues affecting production and procurement.
Encourage team members to share insights, propose solutions, and collaborate effectively to enhance the overall workflow.
Moreover, these meetings serve as an opportunity to build relationships and trust among team members, which is crucial for effective communication.
Measuring and Evaluating Communication Effectiveness
Once new communication strategies are in place, measuring their effectiveness is essential to ensure they contribute positively to productivity.
Establish key performance indicators (KPIs) that align with your communication goals, such as response time to inquiries, the accuracy of information shared, and reduction in production delays.
Regularly review these metrics to determine if your communication strategies are achieving the desired outcomes.
Gather feedback from team members to understand how the new measures are impacting their daily tasks.
If the metrics indicate areas for improvement, adjust your strategies accordingly.
Continuous evaluation and adaptation are key to maintaining efficient communication that drives productivity.
Fostering a Culture of Open Communication
Creating a culture where open communication is encouraged and valued can significantly enhance the relationship between the purchasing department and the manufacturing site.
When employees feel that their voices are heard and their ideas are valued, they are more likely to engage actively in communication processes.
Leadership plays a key role in fostering this culture by setting the tone for transparency and openness.
This involves encouraging feedback, recognizing contributions, and addressing communication barriers promptly.
Team-building activities can also promote camaraderie, leading to more intuitive and effective communication.
By breaking down silos and promoting collaboration, the organization can achieve greater productivity and efficiency in its operations.
Conclusion
In summary, an effective communication strategy between the purchasing department and the manufacturing site is pivotal for improved productivity.
By understanding the role of communication, analyzing current methods, and leveraging technology, teams can work more cohesively.
Regular collaboration meetings and the establishment of clear protocols further enhance this relationship.
Ultimately, fostering a culture of open communication and continuously measuring its effectiveness ensures that any organizational goals are met smoothly and efficiently.
資料ダウンロード
QCD調達購買管理クラウド「newji」は、調達購買部門で必要なQCD管理全てを備えた、現場特化型兼クラウド型の今世紀最高の購買管理システムとなります。
ユーザー登録
調達購買業務の効率化だけでなく、システムを導入することで、コスト削減や製品・資材のステータス可視化のほか、属人化していた購買情報の共有化による内部不正防止や統制にも役立ちます。
NEWJI DX
製造業に特化したデジタルトランスフォーメーション(DX)の実現を目指す請負開発型のコンサルティングサービスです。AI、iPaaS、および先端の技術を駆使して、製造プロセスの効率化、業務効率化、チームワーク強化、コスト削減、品質向上を実現します。このサービスは、製造業の課題を深く理解し、それに対する最適なデジタルソリューションを提供することで、企業が持続的な成長とイノベーションを達成できるようサポートします。
オンライン講座
製造業、主に購買・調達部門にお勤めの方々に向けた情報を配信しております。
新任の方やベテランの方、管理職を対象とした幅広いコンテンツをご用意しております。
お問い合わせ
コストダウンが利益に直結する術だと理解していても、なかなか前に進めることができない状況。そんな時は、newjiのコストダウン自動化機能で大きく利益貢献しよう!
(Β版非公開)