- お役立ち記事
- Component materials, welding and non-destructive testing
月間76,176名の
製造業ご担当者様が閲覧しています*
*2025年3月31日現在のGoogle Analyticsのデータより
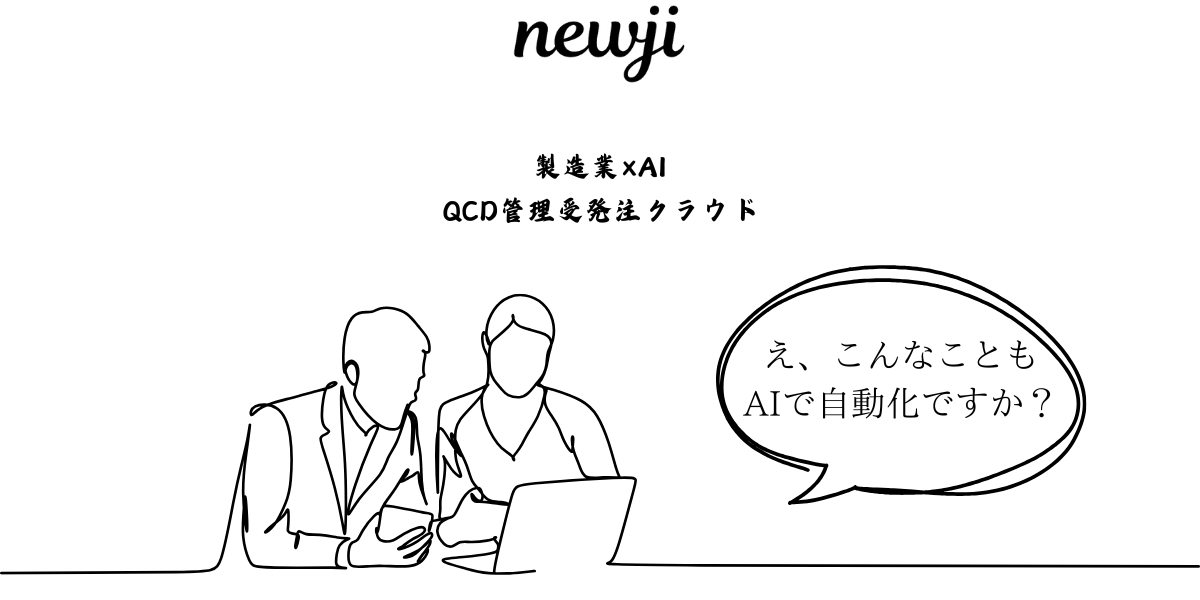
Component materials, welding and non-destructive testing
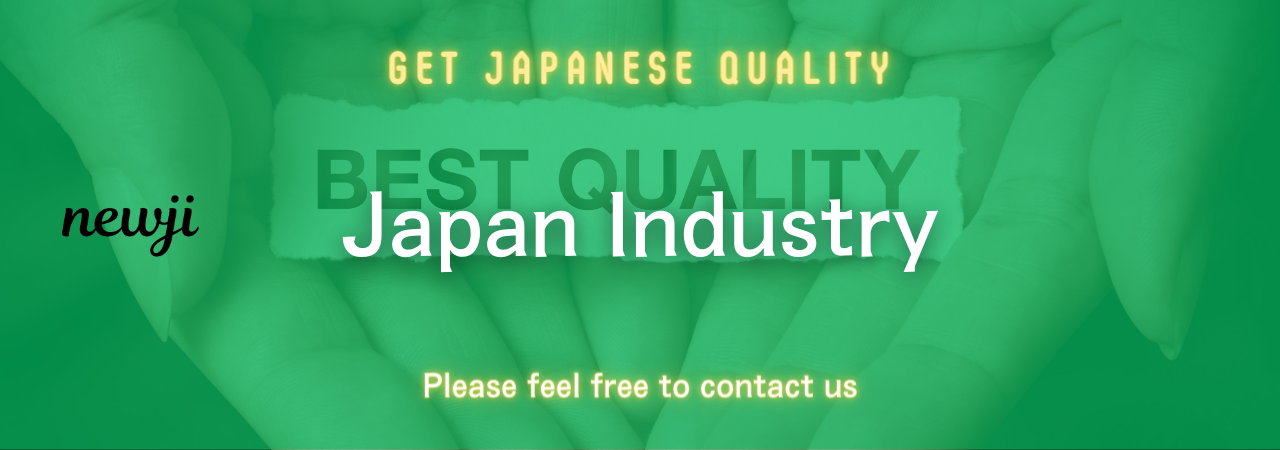
目次
Introduction to Component Materials
Understanding component materials, their properties, and how they interact in various applications is fundamental to engineering and manufacturing.
Component materials are essentially the building blocks of any structure or machine.
They range from metals like steel and aluminum to composites and polymers, each offering unique characteristics suitable for different purposes.
Their selection greatly influences the performance, durability, and longevity of the final product.
Types of Component Materials
Several types of materials are commonly used in the manufacturing and construction industries.
These include:
1. **Metals**: Known for their strength and heat resistance, metals like steel, aluminum, and copper are frequently used in construction, automotive, and machinery applications.
2. **Composites**: These are made by combining two or more materials to enhance the mechanical properties. Examples include carbon-fiber-reinforced composites and fiberglass.
3. **Polymers**: Essentially plastics, they are lightweight and corrosion-resistant, often used in packaging, containers, and electronic components.
4. **Ceramics**: Known for their hardness and thermal stability, ceramics are used in applications such as aerospace and electronics.
The Role of Welding in Component Assemblies
Welding is a crucial process in joining different materials to form a single entity, ensuring structural integrity and functionality.
This process involves fusing materials, typically metals or thermoplastics, by applying heat, pressure, or both.
The importance of welding cannot be overstated because it not only affects the durability of the product but also its overall safety.
Types of Welding Techniques
There are several welding techniques, each suited for specific materials and purposes:
1. **Arc Welding**: Uses an electrical arc to melt the base material along with a filler material.
It’s commonly used for joining heavy metals.
2. **MIG Welding (Metal Inert Gas)**: This uses a continuously fed electrode and is great for rapid welding of thin materials.
3. **TIG Welding (Tungsten Inert Gas)**: Provides precise control over the welds, ideal for complex projects where detail is paramount.
4. **Resistance Welding**: Involves applying pressure and passing current through materials. Suitable for sheet metals and small parts.
5. **Laser Welding**: Utilizes laser beams to create deep welds with minimal distortion.
Often used in high-precision industries.
Non-Destructive Testing: Ensuring Material and Weld Quality
Non-destructive testing (NDT) plays a vital role in evaluating the properties of a material, component, or system without causing damage.
It’s essential for assessing the safety and reliability of products throughout their lifecycle.
Common Non-Destructive Testing Methods
Here are some widely used NDT methods:
1. **Ultrasonic Testing**: Employs high-frequency sound waves to detect internal flaws or characterize materials.
2. **Radiographic Testing**: Utilizes X-rays or gamma rays to view the internal structure, ideal for spotting hidden imperfections.
3. **Magnetic Particle Testing**: Detects surface and near-surface discontinuities in ferromagnetic materials.
4. **Liquid Penetrant Testing**: A dye is applied to the surface to reveal cracks that are open to the surface.
5. **Eddy Current Testing**: Uses electromagnetic induction to detect defects in conductive materials.
Importance of NDT in Maintaining Safety and Quality
The application of NDT is critical in industries like aerospace, automotive, and construction, where safety and quality cannot be compromised.
By allowing for inspections without causing harm to the part or structure, NDT helps in finding defects that could lead to failures.
Further, it ensures compliance with standards and regulations, thereby maintaining the integrity and reputation of a company’s products.
Integrating Material Knowledge, Welding, and NDT for Success
Each stage of the manufacturing process, from selecting materials to choosing the appropriate welding technique and employing NDT, is interrelated.
Together, they form a cohesive workflow that guarantees product quality and performance.
An in-depth understanding of the types of materials available, their behavior during welding, and how to test them without damage is indispensable.
It leads to more informed decisions, reduced risks, and enhanced outcomes.
Conclusion
Component materials, welding techniques, and non-destructive testing form the foundation of modern manufacturing.
Associating the right materials with the correct welding processes and utilizing NDT ensures that products are safe, durable, and of high quality.
In industries where precision and reliability are paramount, such as aerospace and automotive, these elements are crucial.
By mastering them, engineers and manufacturers can drive innovations while maintaining the highest standards of safety and performance.
資料ダウンロード
QCD管理受発注クラウド「newji」は、受発注部門で必要なQCD管理全てを備えた、現場特化型兼クラウド型の今世紀最高の受発注管理システムとなります。
ユーザー登録
受発注業務の効率化だけでなく、システムを導入することで、コスト削減や製品・資材のステータス可視化のほか、属人化していた受発注情報の共有化による内部不正防止や統制にも役立ちます。
NEWJI DX
製造業に特化したデジタルトランスフォーメーション(DX)の実現を目指す請負開発型のコンサルティングサービスです。AI、iPaaS、および先端の技術を駆使して、製造プロセスの効率化、業務効率化、チームワーク強化、コスト削減、品質向上を実現します。このサービスは、製造業の課題を深く理解し、それに対する最適なデジタルソリューションを提供することで、企業が持続的な成長とイノベーションを達成できるようサポートします。
製造業ニュース解説
製造業、主に購買・調達部門にお勤めの方々に向けた情報を配信しております。
新任の方やベテランの方、管理職を対象とした幅広いコンテンツをご用意しております。
お問い合わせ
コストダウンが利益に直結する術だと理解していても、なかなか前に進めることができない状況。そんな時は、newjiのコストダウン自動化機能で大きく利益貢献しよう!
(β版非公開)