- お役立ち記事
- Comprehensive Explanation of the Differences Between Wet and Dry Forming in Ceramics Factories
Comprehensive Explanation of the Differences Between Wet and Dry Forming in Ceramics Factories
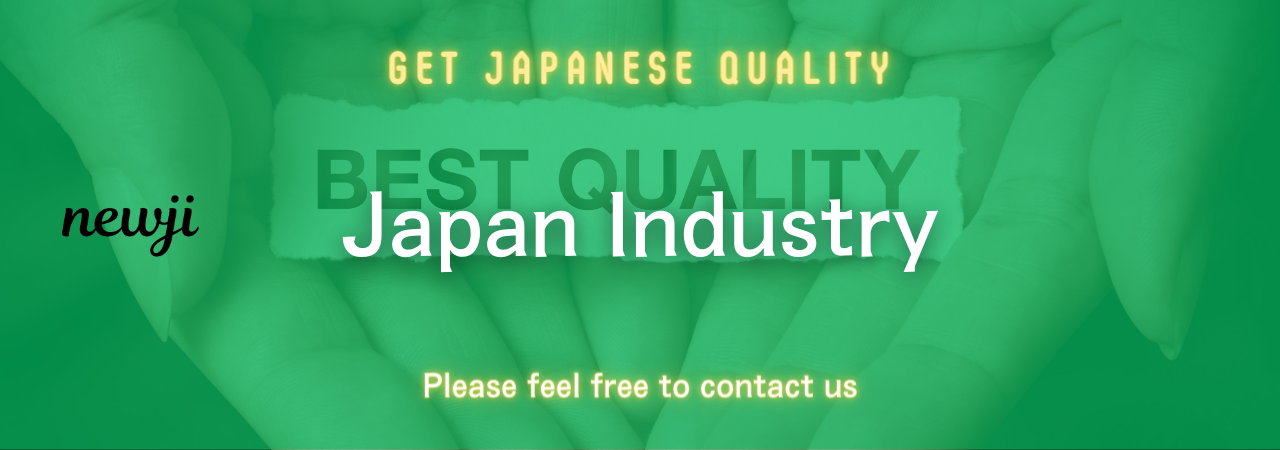
目次
Introduction to Ceramic Forming Processes
Ceramics have been a significant part of human civilization for centuries.
These materials, renowned for their durability, hardness, and thermal resistance, are crafted through a delicate process called ceramic forming.
In factories, this process can unfold in several ways, with wet and dry forming being among the most prevalent methods.
Understanding the differences between these two approaches is crucial for optimizing production efficiency and achieving desired product characteristics.
What is Wet Forming?
Wet forming, sometimes known as wet pressing, is a process wherein ceramic powders are mixed with water to create a moldable slurry or slip.
This wet mixture allows for shaping through a variety of techniques, including slip casting and extrusion.
The increased malleability offered by the water component makes it easier to form complex shapes and detailed designs.
The critical aspect of wet forming is the drying stage, where excess moisture is removed to solidify the shaped ceramic.
This step, if not monitored correctly, can lead to structural weaknesses or deformities from uneven drying shrinkage.
Advantages of Wet Forming
One of the primary benefits of wet forming is the ease with which intricate designs can be created.
The addition of water acts as a lubricant, allowing for finer detail and more complex shapes that might be difficult to achieve using dry methods.
Additionally, wet forming can be less abrasive to the material since the added moisture reduces mechanical stress during shaping.
Challenges of Wet Forming
Despite its advantages, wet forming presents some challenges.
The reliance on water means that the drying process needs careful control to prevent cracking or warping.
The entire process can also take longer because of the necessary drying, which can extend production timelines.
Additionally, the equipment involved might require frequent cleaning and maintenance to prevent clogging and contamination.
Understanding Dry Forming
Dry forming, in contrast, uses minimal or no water in the shaping process.
Instead, ceramic powders are pressed together under high pressure to form a solid shape.
This method is often favored for its ability to produce uniform products quickly and efficiently.
The pressing pressure consolidates the particles into a dense form, and once compacted, the green body is typically ready for further processing without a lengthy drying phase.
Advantages of Dry Forming
A significant advantage of dry forming is its speed.
Since it eliminates the drying step, production times are typically faster.
This method also often results in a more uniform density and size distribution among the ceramic products, which can lead to higher consistency and quality.
Furthermore, dry forming often requires less energy and is less subject to seasonal variability compared to its wet counterpart.
Challenges of Dry Forming
The primary challenge with dry forming lies in the potential for stress within the material, which can lead to cracking during pressing or later stages.
Achieving complex shapes can also be more difficult due to the limited malleability of dry powders.
Moreover, precise control over pressure and particle size distribution is crucial to prevent defects.
Comparing Wet and Dry Forming
Both wet and dry forming have their unique benefits and limitations, making the choice between them dependent on the specific requirements and constraints of a production facility.
Wet forming is excellent for intricate designs and unique shapes, but it demands careful management of the drying process to prevent defects.
Conversely, dry forming excels in efficiency and speed, making it ideal for high-volume production with less downtime, though with limitations in shape complexity.
Material Considerations
The choice between wet and dry forming can heavily depend on the type of ceramic material being used.
Some ceramics behave better under wet conditions, allowing for better bonding and shaping.
Others might hold up more effectively under the pressures of dry forming, especially if brittleness is a concern.
Production Scale and Complexity
For small-scale operations or those producing unique, detailed products, wet forming may present more advantages.
However, for large-scale operations where speed and uniformity are paramount, dry forming may offer better returns.
Conclusion
When it comes to selecting a ceramic forming method, factories must weigh the pros and cons of wet and dry processes carefully.
Understanding the intricacies of each method enables manufacturers to maximize efficiency, minimize waste, and maintain high-quality standards.
Ultimately, the decision may also involve a hybrid approach that leverages the best of both worlds, offering flexibility and innovation in ceramics production.
資料ダウンロード
QCD調達購買管理クラウド「newji」は、調達購買部門で必要なQCD管理全てを備えた、現場特化型兼クラウド型の今世紀最高の購買管理システムとなります。
ユーザー登録
調達購買業務の効率化だけでなく、システムを導入することで、コスト削減や製品・資材のステータス可視化のほか、属人化していた購買情報の共有化による内部不正防止や統制にも役立ちます。
NEWJI DX
製造業に特化したデジタルトランスフォーメーション(DX)の実現を目指す請負開発型のコンサルティングサービスです。AI、iPaaS、および先端の技術を駆使して、製造プロセスの効率化、業務効率化、チームワーク強化、コスト削減、品質向上を実現します。このサービスは、製造業の課題を深く理解し、それに対する最適なデジタルソリューションを提供することで、企業が持続的な成長とイノベーションを達成できるようサポートします。
オンライン講座
製造業、主に購買・調達部門にお勤めの方々に向けた情報を配信しております。
新任の方やベテランの方、管理職を対象とした幅広いコンテンツをご用意しております。
お問い合わせ
コストダウンが利益に直結する術だと理解していても、なかなか前に進めることができない状況。そんな時は、newjiのコストダウン自動化機能で大きく利益貢献しよう!
(Β版非公開)