- お役立ち記事
- Comprehensive Explanation of the Importance and Benefits of Introducing QFD in Manufacturing
Comprehensive Explanation of the Importance and Benefits of Introducing QFD in Manufacturing
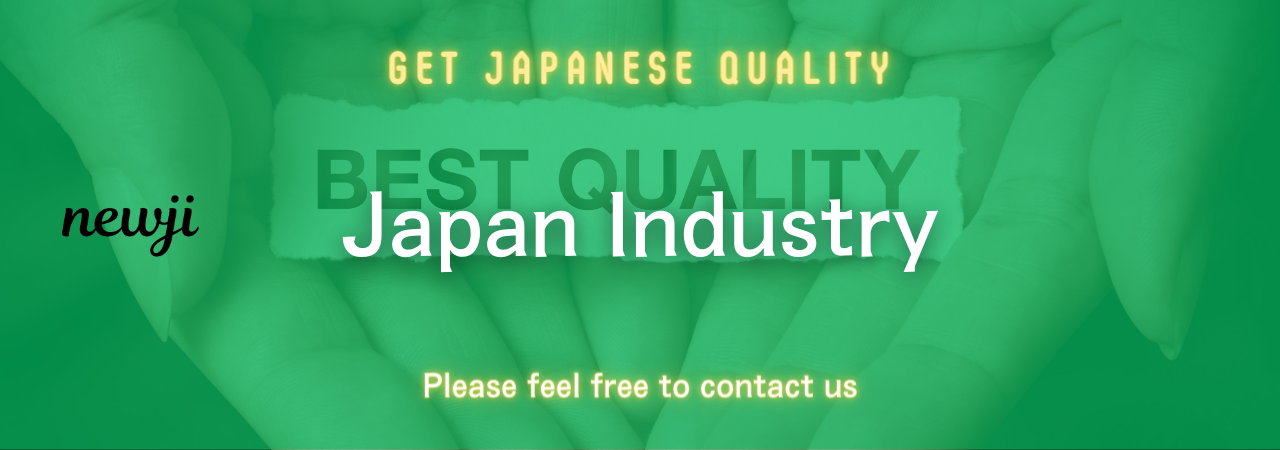
目次
What is QFD?
Quality Function Deployment, commonly abbreviated as QFD, is a method used in manufacturing and product development to transform customer needs and desires into specific engineering and technical requirements.
QFD ensures that the needs of the customer are systematically incorporated into every stage of the product development process.
Developed in Japan in the late 1960s, QFD initially focused on the automotive sector but has since expanded into various industries around the globe.
The goal is to bridge the gap between what customers want and what manufacturers produce, leading to products that are more aligned with customer expectations and market demands.
The Importance of QFD in Manufacturing
Enhancing Customer Satisfaction
The primary advantage of QFD is that it ensures customer satisfaction.
By translating customer needs into specific actions and technical requirements, manufacturers can create products that better meet the expectations of their end-users.
This leads to higher customer satisfaction, which in turn fosters brand loyalty and repeat business.
Reducing Production Costs
QFD helps to identify potential issues early in the development process.
This proactive approach allows for the correction of design flaws before production begins, thereby reducing the need for costly revisions and reworks.
Identifying and addressing problems at the design stage can significantly lower production costs and improve overall efficiency.
Improving Team Collaboration
When implementing QFD, teams from various departments—including engineering, marketing, and production—work closely together.
This collaborative effort ensures that all aspects of the product are considered, from initial design to final production.
By fostering communication and collaboration among different departments, QFD promotes a more cohesive and efficient working environment.
Enhancing Market Competitiveness
Products developed using QFD are more likely to align with market trends and customer preferences, providing a competitive edge.
When a company consistently delivers products that meet or exceed customer expectations, it can more effectively compete in the marketplace.
This competitive advantage can lead to increased market share and business growth.
Steps Involved in QFD
Identifying Customer Needs
The first step in QFD is to gather detailed information about customer expectations and requirements.
This can be done through surveys, interviews, focus groups, and market analysis.
Once the information is collected, it is organized into a structured list of customer needs, often referred to as the “What’s.”
Developing a House of Quality
The core component of the QFD process is the “House of Quality” matrix, a visual representation that helps to prioritize customer needs and match them with corresponding technical requirements.
The matrix is called a House because of its architectural appearance—it has rows and columns that intersect to create a grid.
The horizontal rows list customer needs, while the vertical columns list technical requirements or “How’s.”
Prioritizing Requirements
Not all customer needs are equally important.
Thus, the next step is to prioritize these needs based on their significance to customers.
This prioritization helps to allocate resources and focus efforts on the most critical aspects of product development.
Competitive Analysis
QFD also involves comparing your product against those of competitors.
This competitive analysis helps to identify areas where your product can differentiate itself from others in the market.
By understanding the strengths and weaknesses of competitors, you can better position your product to meet customer needs more effectively.
Establishing Specific Goals
After identifying and prioritizing customer needs and performing a competitive analysis, specific goals and targets are set for the technical requirements.
These goals are aligned with engineering specifications to ensure that the final product meets all identified criteria.
Benefits of Implementing QFD
Higher Product Quality
QFD ensures that every aspect of the product is developed with the customer’s needs in mind.
This focus on quality leads to products that are more reliable and better suited to customer expectations, thereby enhancing overall product quality.
Faster Time-to-Market
By identifying potential issues early and fostering collaboration among different teams, QFD helps to streamline the product development process.
This results in faster time-to-market, allowing companies to capitalize on market opportunities more quickly.
Cost Savings
Avoiding design errors and minimizing rework can result in significant cost savings.
QFD helps to highlight potential problems before they become costly issues, thereby reducing overall production expenses.
Customer Loyalty
When products consistently meet or exceed customer expectations, it leads to higher customer satisfaction and loyalty.
Loyal customers are more likely to make repeat purchases and recommend the product to others, driving long-term business growth.
Challenges of QFD Implementation
Complexity and Time Investment
One of the primary challenges of QFD is that it can be complex and time-consuming to implement.
The process involves gathering extensive customer data, developing detailed matrices, and fostering inter-departmental collaboration.
While the investment of time and resources can be substantial, the long-term benefits often justify the effort.
Requires Skilled Personnel
Effective QFD implementation requires a team of skilled professionals who are well-versed in the methodology.
Training and development may be necessary to ensure that all team members understand the principles and practices involved in QFD.
Ongoing Process
QFD is not a one-time activity; it is an ongoing process that requires continuous monitoring and adjustments.
As market trends and customer needs evolve, the QFD process must be revisited and refined to ensure that products remain competitive and relevant.
Conclusion
Quality Function Deployment (QFD) is a powerful tool in the world of manufacturing and product development.
By ensuring that customer needs are at the heart of every decision, QFD leads to higher product quality, reduced costs, and improved market competitiveness.
While the process can be complex and requires a significant investment of time and resources, the long-term benefits of enhanced customer satisfaction and loyalty make it a valuable strategy for any manufacturing company.
資料ダウンロード
QCD調達購買管理クラウド「newji」は、調達購買部門で必要なQCD管理全てを備えた、現場特化型兼クラウド型の今世紀最高の購買管理システムとなります。
ユーザー登録
調達購買業務の効率化だけでなく、システムを導入することで、コスト削減や製品・資材のステータス可視化のほか、属人化していた購買情報の共有化による内部不正防止や統制にも役立ちます。
NEWJI DX
製造業に特化したデジタルトランスフォーメーション(DX)の実現を目指す請負開発型のコンサルティングサービスです。AI、iPaaS、および先端の技術を駆使して、製造プロセスの効率化、業務効率化、チームワーク強化、コスト削減、品質向上を実現します。このサービスは、製造業の課題を深く理解し、それに対する最適なデジタルソリューションを提供することで、企業が持続的な成長とイノベーションを達成できるようサポートします。
オンライン講座
製造業、主に購買・調達部門にお勤めの方々に向けた情報を配信しております。
新任の方やベテランの方、管理職を対象とした幅広いコンテンツをご用意しております。
お問い合わせ
コストダウンが利益に直結する術だと理解していても、なかなか前に進めることができない状況。そんな時は、newjiのコストダウン自動化機能で大きく利益貢献しよう!
(Β版非公開)