- お役立ち記事
- Comprehensive Troubleshooting: Practical Application of the “5 Whys” Analysis
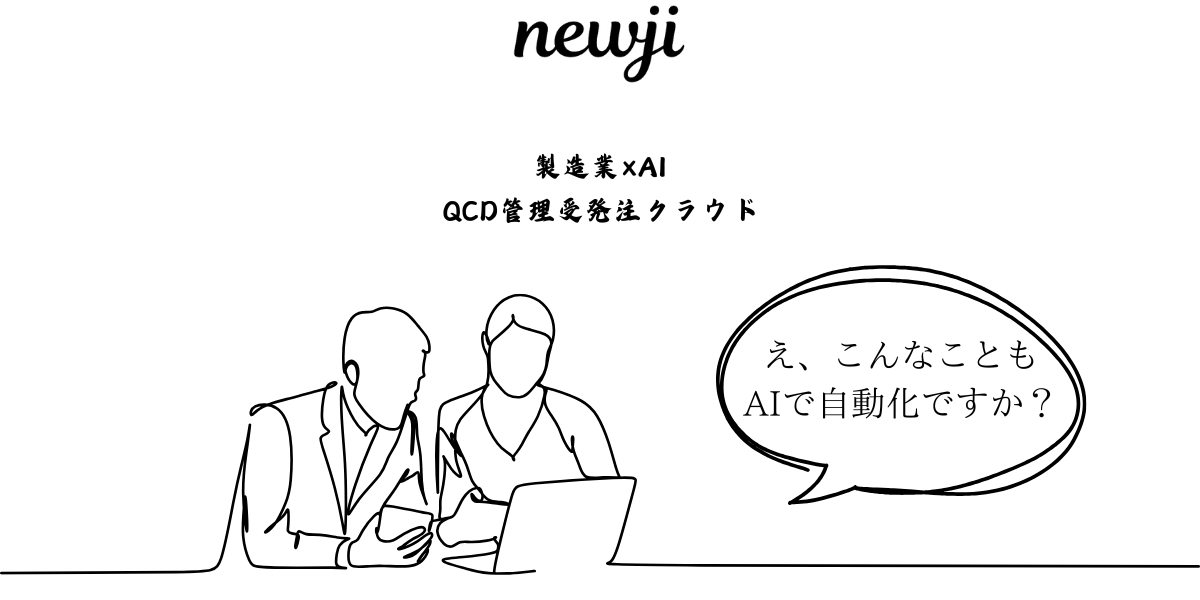
Comprehensive Troubleshooting: Practical Application of the “5 Whys” Analysis
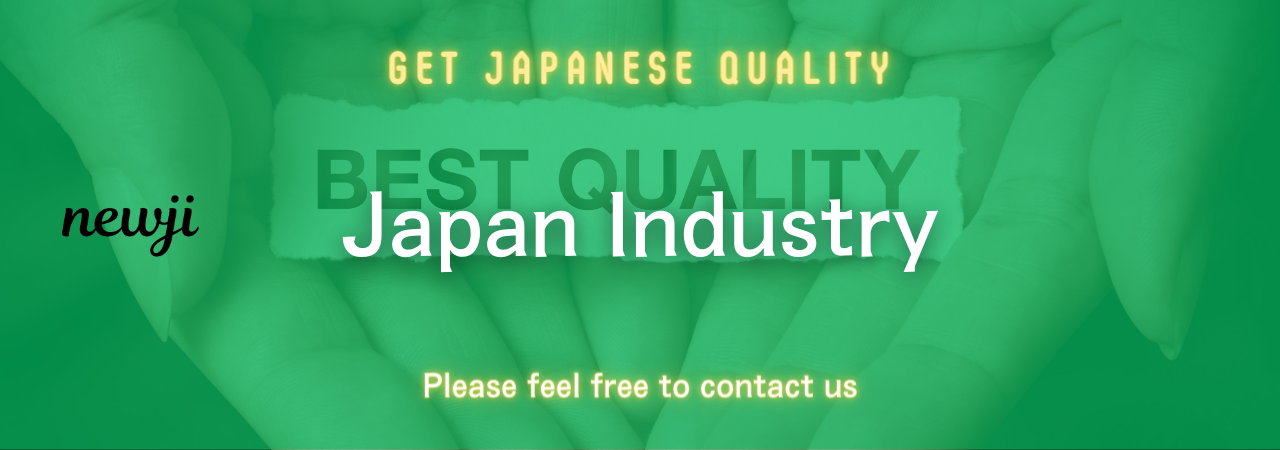
The “5 Whys” analysis is a powerful method for identifying the root cause of problems.
Developed by Sakichi Toyoda for Toyota, this technique is widely used in various industries to solve issues efficiently.
With its simple approach and profound results, the “5 Whys” analysis is something everyone in a problem-solving role should understand.
目次
Understanding the “5 Whys” Analysis
The “5 Whys” method is essentially a form of iterative questioning.
You keep asking “Why?” until you find the fundamental cause of a problem.
Each answer serves as the basis for the next question.
Typically, asking “Why?” five times is sufficient, though it’s not always a rigid rule.
Why Use the “5 Whys” Analysis?
This method is straightforward and user-friendly.
Its primary advantage lies in its simplicity and ability to uncover deep-rooted issues quickly.
Unlike other complex techniques, the “5 Whys” doesn’t require specialized knowledge or training.
It’s accessible to anyone willing to dig deeper into a problem.
The Practical Application of “5 Whys” Analysis
Applying the “5 Whys” technique involves several critical stages.
Let’s break them down for a clearer understanding.
Step 1: Identify the Problem
Firstly, you need to clearly define the problem.
It should be specific and understandable for everyone involved.
For instance, “The production machine stops unexpectedly.”
This statement forms the basis for the first “Why?”.
Step 2: Assemble a Team
The “5 Whys” analysis benefits from diverse perspectives.
Gather a team with varied expertise related to the problem.
The team can include managers, operators, and maintenance personnel, among others.
Step 3: Ask the First “Why?”
Once the problem is identified, ask why it occurred.
For example, “Why did the production machine stop unexpectedly?”
Possible answer: “Because it overloaded.”
Step 4: Ask Why Again
Based on the initial answer, ask the second “Why?”.
“Why did the machine overload?”
Possible answer: “Because there was too much product on the conveyor belt.”
Step 5: Continue Asking “Why?”
Keep on asking “Why?” for each subsequent answer until you reach the root cause.
“Why was there too much product on the conveyor belt?”
“Because the sensor was malfunctioning.”
“Why was the sensor malfunctioning?”
“Because it had not been maintained properly.”
“Why was it not maintained properly?”
“Because there was no routine maintenance schedule.”
Step 6: Implement Solutions
Once you’ve identified the root cause, implement a corrective plan.
In this example, establishing a routine maintenance schedule might solve the problem.
Always ensure that solutions are practical, implementable, and monitored for effectiveness.
Advantages of Using “5 Whys”
The “5 Whys” technique has several key benefits:
Simplicity
The process is easy to understand and conduct.
There’s no need for complex tools or advanced training.
Anyone can perform this analysis with a pen and paper.
Uncovering Root Causes
The method effectively identifies underlying issues.
Superficial solutions are avoided, leading to long-term problem resolution.
Encouraging Team Input
Collaboration fosters a more comprehensive understanding of problems.
Different viewpoints can offer unique insights, making the analysis more robust.
Common Pitfalls and How to Avoid Them
While the “5 Whys” analysis is straightforward, there are common pitfalls to avoid.
Superficial Answers
Sometimes, the answers can be too shallow.
Always dig deeper to ensure the real root cause is identified.
Encourage the team to think critically.
Blame Culture
The objective is not to place blame but to find solutions.
Ensure the team understands this to maintain a positive and productive environment.
Stopping Too Early
It’s crucial not to stop the questioning prematurely.
Stopping after the second or third “Why?” might not bring you to the root cause.
Be persistent and thorough.
Lack of Documentation
Document each step of the “5 Whys” process.
It offers a reference for future problem-solving efforts and helps track implemented solutions.
Real-life Example of “5 Whys” Analysis
To further illustrate, let’s explore a real-life example from the IT industry.
The Problem
A company’s website keeps crashing during peak hours.
First “Why?”
Why does the website crash during peak hours?
Because the server is overloaded.
Second “Why?”
Why is the server overloaded?
Because it’s not handling the traffic efficiently.
Third “Why?”
Why is it not handling traffic efficiently?
Because the underlying code isn’t optimized.
Fourth “Why?”
Why is the code not optimized?
Because there was a rush in deploying the website without proper testing.
Fifth “Why?”
Why was there a rush in deploying the website?
Because the project timeline was unrealistic.
The Solution
Establish a more realistic project timeline, incorporate adequate testing phases, and allocate time for code optimization.
Improvements in these areas could prevent future website crashes.
Conclusion
The “5 Whys” analysis is an invaluable tool for identifying root causes in various scenarios.
Its simplicity and depth make it accessible and effective for everyone from engineers to managers.
By systematically applying the “5 Whys,” you can uncover hidden problems and implement lasting solutions.
It’s an integral technique for anyone serious about resolving issues at their core and improving their operations.
資料ダウンロード
QCD調達購買管理クラウド「newji」は、調達購買部門で必要なQCD管理全てを備えた、現場特化型兼クラウド型の今世紀最高の購買管理システムとなります。
ユーザー登録
調達購買業務の効率化だけでなく、システムを導入することで、コスト削減や製品・資材のステータス可視化のほか、属人化していた購買情報の共有化による内部不正防止や統制にも役立ちます。
NEWJI DX
製造業に特化したデジタルトランスフォーメーション(DX)の実現を目指す請負開発型のコンサルティングサービスです。AI、iPaaS、および先端の技術を駆使して、製造プロセスの効率化、業務効率化、チームワーク強化、コスト削減、品質向上を実現します。このサービスは、製造業の課題を深く理解し、それに対する最適なデジタルソリューションを提供することで、企業が持続的な成長とイノベーションを達成できるようサポートします。
オンライン講座
製造業、主に購買・調達部門にお勤めの方々に向けた情報を配信しております。
新任の方やベテランの方、管理職を対象とした幅広いコンテンツをご用意しております。
お問い合わせ
コストダウンが利益に直結する術だと理解していても、なかなか前に進めることができない状況。そんな時は、newjiのコストダウン自動化機能で大きく利益貢献しよう!
(Β版非公開)