- お役立ち記事
- Compression Strength Testing of Copper Products and Evaluation Methods
月間76,176名の
製造業ご担当者様が閲覧しています*
*2025年3月31日現在のGoogle Analyticsのデータより
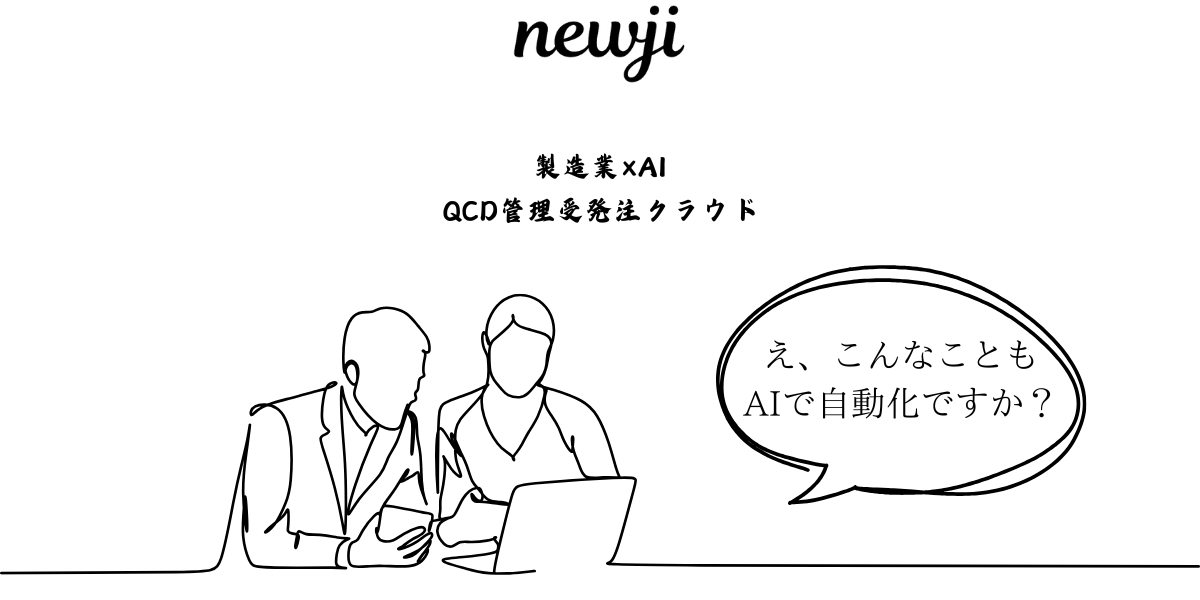
Compression Strength Testing of Copper Products and Evaluation Methods
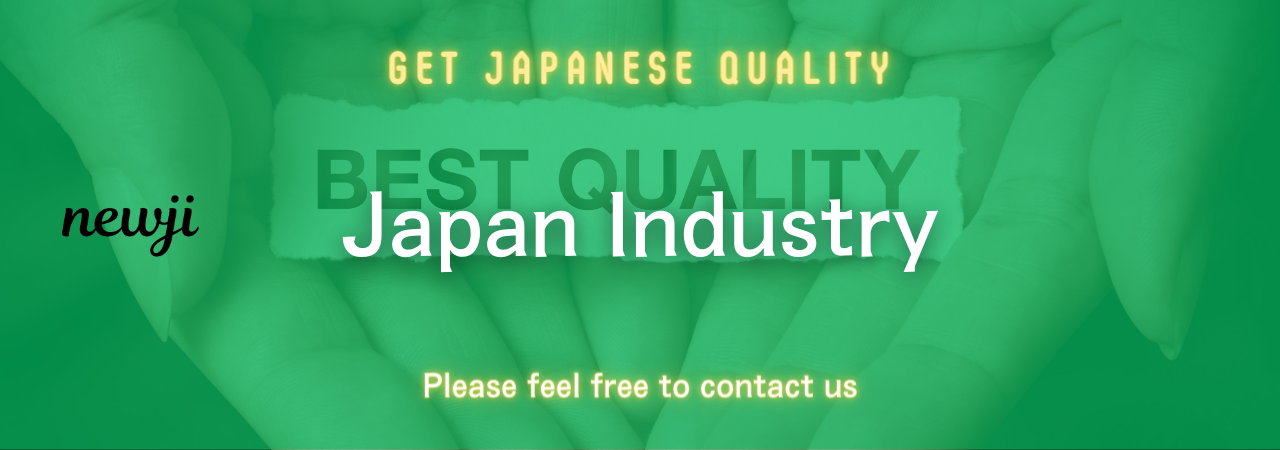
目次
Understanding Compression Strength in Copper Products
Copper is a versatile and widely used metal in various industries due to its excellent electrical and thermal conductivity, corrosion resistance, and malleability.
However, when it comes to structural applications, understanding the compression strength of copper products is crucial.
Compression strength measures the ability of a material to withstand forces that attempt to reduce its size.
This property is especially important in applications where copper components are subjected to loads that push them together.
Importance of Compression Strength Testing
Testing the compression strength of copper products is vital for several reasons.
First, it helps ensure the material’s suitability for intended applications, especially in construction, electronics, and industrial machinery, where mechanical stability is essential.
Secondly, it aids in predicting the performance of copper components under load, providing insights into their durability and safe load-bearing capacities.
Finally, knowing the compression strength helps in quality control during manufacturing, ensuring that the produced copper products meet the required standards and specifications.
Methods of Testing Compression Strength
There are several methods employed to test the compression strength of copper products.
These methods are performed in laboratory settings using advanced equipment and are governed by standardized protocols to ensure accuracy and repeatability.
Universal Testing Machine
A Universal Testing Machine (UTM) is one of the most common tools used for compression testing.
It applies a uniaxial force to the copper sample and measures the amount of stress it can withstand before failure.
The machine compresses the sample between two rigid platens while measuring the load and the change in height of the sample.
The force applied is gradually increased until the sample fails, and the maximum stress it supports is recorded as the compression strength.
Hydraulic Compression Tester
A hydraulic compression tester is another tool widely used in compression strength testing.
This equipment uses hydraulic power to apply a precise compressive load on the copper sample.
The advantage of using a hydraulic testing setup is its ability to apply consistently smooth and controlled loads, reducing any interference from abrupt manual adjustments.
This method is ideal for testing the robustness of copper alloys, given their varying resilience depending on formulation and treatment.
Finite Element Analysis (FEA)
Finite Element Analysis is a computer-aided approach to testing compression strength.
This method simulates the physical behavior of copper products under compressive loads using advanced software programs.
FEA can predict how copper components will react to stress, strain, and deformation without destruction of the sample, making it a cost-effective option for repeated test scenarios.
FEA is particularly beneficial for complex shapes or designs where traditional testing methods are difficult to apply.
Equation of State EOS Model
The Equation of State model offers a theoretical prediction of the compression strength by considering the material properties and conditions.
This analytical approach uses equations to describe the relationship between various states of the copper material (pressure, volume, and temperature).
By applying these equations, researchers can estimate the compression strength under different environmental conditions, which is useful for predicting performance in real-world applications.
Evaluation of Compression Test Results
Once the compression strength tests are conducted, interpreting the results is an essential step to understanding the performance of the copper product.
The data obtained should be assessed against industry standards and figures required for specific applications.
Stress-Strain Curve Analysis
One of the primary outputs of a compression test is the stress-strain curve.
This curve graphically represents the relationship between the stress (applied load) and the strain (deformation) of the copper sample.
By analyzing this curve, engineers can determine key properties such as the yield strength, ultimate strength, and modulus of elasticity.
These properties help in evaluating how the material would behave under application-specific conditions.
Comparative Studies
Comparative studies involve evaluating the test results of copper products against historical data or similar materials.
This method helps in identifying any deviations from expected performance and can guide potential improvements in copper alloy formulations or treatment processes.
Through comparative studies, manufacturers can also benchmark copper against alternative materials, ensuring the selected copper products offer an optimal balance of cost, performance, and durability.
Failure Analysis
In cases where copper samples fail the compression test earlier than expected, a failure analysis is important to determine the cause.
Failures can result from intrinsic material flaws, inappropriate alloy compositions, or defects introduced during manufacturing.
By understanding failure points, engineers and quality control specialists can address potential issues before full-scale production or field deployment, ensuring that copper products meet desired performance levels.
Conclusion
Compression strength testing of copper products is an essential practice to ensure their reliability and safety in various applications.
With several methods available, from traditional to computer-simulated tests, industry professionals can accurately determine the load-bearing capacities of copper materials.
These insights not only ensure compliance with standards but also drive innovation in copper-based applications.
By continually evaluating and improving testing methodologies and their interpretations, the copper industry can meet the ever-evolving demands of modern technology and infrastructure.
資料ダウンロード
QCD管理受発注クラウド「newji」は、受発注部門で必要なQCD管理全てを備えた、現場特化型兼クラウド型の今世紀最高の受発注管理システムとなります。
ユーザー登録
受発注業務の効率化だけでなく、システムを導入することで、コスト削減や製品・資材のステータス可視化のほか、属人化していた受発注情報の共有化による内部不正防止や統制にも役立ちます。
NEWJI DX
製造業に特化したデジタルトランスフォーメーション(DX)の実現を目指す請負開発型のコンサルティングサービスです。AI、iPaaS、および先端の技術を駆使して、製造プロセスの効率化、業務効率化、チームワーク強化、コスト削減、品質向上を実現します。このサービスは、製造業の課題を深く理解し、それに対する最適なデジタルソリューションを提供することで、企業が持続的な成長とイノベーションを達成できるようサポートします。
製造業ニュース解説
製造業、主に購買・調達部門にお勤めの方々に向けた情報を配信しております。
新任の方やベテランの方、管理職を対象とした幅広いコンテンツをご用意しております。
お問い合わせ
コストダウンが利益に直結する術だと理解していても、なかなか前に進めることができない状況。そんな時は、newjiのコストダウン自動化機能で大きく利益貢献しよう!
(β版非公開)