- お役立ち記事
- Concepts for optimizing inventory risk and quality control in purchasing departments
Concepts for optimizing inventory risk and quality control in purchasing departments
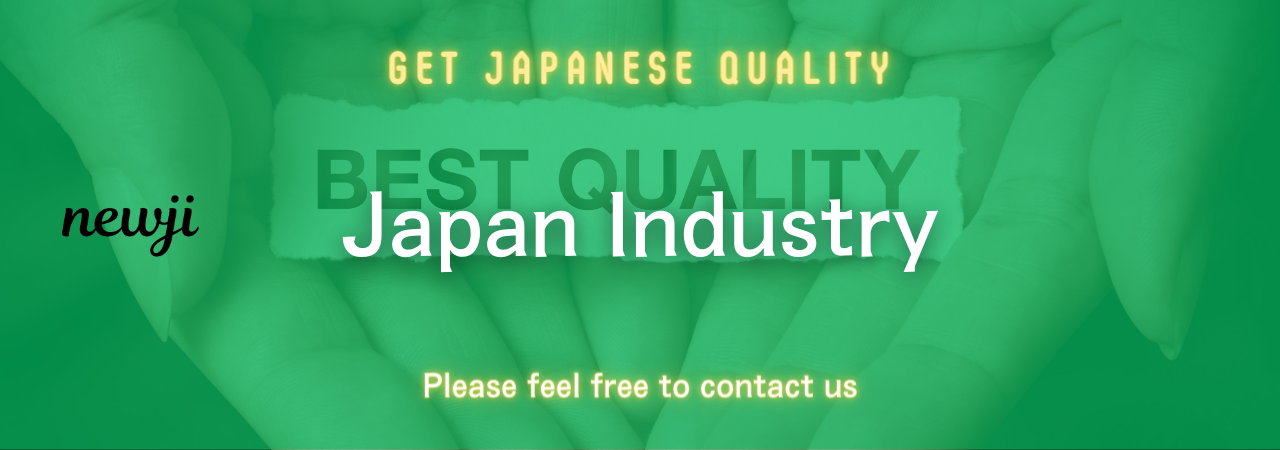
目次
Understanding Inventory Risk
Inventory risk is an essential concept for purchasing departments in any business.
It refers to the potential loss that a company faces related to its products and their management.
Managing inventory risk is crucial because it can directly affect a company’s cash flow, profitability, and customer satisfaction.
There are several types of inventory risks including demand risks, supply risks, and operational risks.
Demand risk arises when there is uncertainty about the market demand for certain products.
If demand is overestimated, excess inventory can lead to increased holding costs and potential obsolescence.
Conversely, underestimating demand can result in stockouts and missed sales opportunities.
Supply risk involves disruptions that can impact the acquisition of raw materials or finished goods.
This can be due to factors such as supplier reliability, geopolitical issues, or transportation challenges.
Effective supply chain management can help mitigate these risks.
Operational risk pertains to the internal processes that affect inventory management, such as order processing errors or inaccurate inventory tracking.
Implementing efficient systems and technology can reduce these risks significantly.
Quality Control in Purchasing Departments
Quality control is a systematic process that ensures products meet specified standards and offer value to customers.
In purchasing departments, quality control focuses on maintaining the quality of products acquired from suppliers.
It involves various activities such as inspection, testing, and quality assurance practices to ensure that purchased products are free from defects and meet performance requirements.
Quality control in purchasing starts with a clear understanding of required product specifications and standards.
Establishing strict vendor criteria and performing regular audits can ensure suppliers maintain consistent quality levels.
Additionally, adopting a quality management system can streamline processes and improve overall product quality.
Strategies for Optimizing Inventory Risk
Balancing the risks associated with inventory management is crucial for business success.
Here are some strategies to optimize inventory risk:
1. **Accurate Demand Forecasting**: Utilizes historical data, market trends, and advanced analytics to predict future demand accurately.
This can help align inventory levels with actual market needs and reduce excess or shortage issues.
2. **Flexible Supply Chain**: Diversifying suppliers and creating contingency plans for supply chain disruptions can minimize supply risks.
Engaging with multiple suppliers ensures a steady flow of materials and reduces dependency on a single source.
3. **Inventory Management Systems**: Implementing robust inventory management software can enhance tracking and visibility.
Real-time data and analytics can aid in making informed decisions and identifying potential risk areas promptly.
4. **Just-in-Time Inventory**: Adopting a just-in-time approach can help reduce inventory holding costs and minimize waste.
This strategy focuses on producing or receiving goods only as needed, based on current demand.
Optimizing Quality Control in Purchasing
The primary goal of quality control is to ensure that purchased products meet required standards and provide value.
Here are some methods to optimize quality control in purchasing departments:
1. **Vendor Selection and Evaluation**: Develop a comprehensive vendor selection process that emphasizes quality.
Regularly evaluate and audit suppliers to ensure compliance with quality standards.
2. **Clear Specifications**: Clearly define product specifications and quality requirements.
Ensure suppliers understand these standards and are equipped to meet them consistently.
3. **Implement Quality Frameworks**: Use quality control frameworks and methodologies like Six Sigma or Total Quality Management (TQM) to enhance processes.
These frameworks provide tools and techniques to reduce defects and improve overall product quality.
4. **Technology Utilization**: Leverage technology for quality inspections and testing.
Automated systems can perform repetitive quality checks efficiently, reducing the likelihood of human error.
The Role of Technology in Managing Inventory and Quality
Technology plays a pivotal role in optimizing both inventory risk and quality control in purchasing departments.
Advanced software solutions provide tools and analytics to manage inventory effectively, reducing risk factors such as overstocking or stockouts.
These technologies enable better tracking, forecasting, and management of inventory throughout the supply chain.
In the realm of quality control, technology offers sophisticated testing and inspection tools that ensure products meet all quality standards.
Machine learning and AI can identify patterns and anomalies, allowing for proactive quality management and swift resolution of potential issues.
Continuous Improvement and Feedback
A culture of continuous improvement is vital for both inventory management and quality control.
Encouraging staff to provide feedback and engage in problem-solving can lead to innovative solutions and process optimizations.
Regular training and development programs ensure that employees stay abreast of the latest best practices and technological advancements.
Supplier collaboration is also crucial in driving continuous improvement.
Sharing quality expectations and performance data with suppliers fosters transparency and a shared commitment to quality excellence.
Conclusion
Optimizing inventory risk and quality control in purchasing departments requires a comprehensive approach that combines effective strategies, technological advancements, and continuous improvement.
By accurately forecasting demand, maintaining a flexible supply chain, and implementing robust quality control measures, businesses can effectively manage these aspects to enhance efficiency and customer satisfaction.
A proactive approach not only minimizes risks but also contributes to achieving long-term business goals and maintaining competitive advantage.
資料ダウンロード
QCD調達購買管理クラウド「newji」は、調達購買部門で必要なQCD管理全てを備えた、現場特化型兼クラウド型の今世紀最高の購買管理システムとなります。
ユーザー登録
調達購買業務の効率化だけでなく、システムを導入することで、コスト削減や製品・資材のステータス可視化のほか、属人化していた購買情報の共有化による内部不正防止や統制にも役立ちます。
NEWJI DX
製造業に特化したデジタルトランスフォーメーション(DX)の実現を目指す請負開発型のコンサルティングサービスです。AI、iPaaS、および先端の技術を駆使して、製造プロセスの効率化、業務効率化、チームワーク強化、コスト削減、品質向上を実現します。このサービスは、製造業の課題を深く理解し、それに対する最適なデジタルソリューションを提供することで、企業が持続的な成長とイノベーションを達成できるようサポートします。
オンライン講座
製造業、主に購買・調達部門にお勤めの方々に向けた情報を配信しております。
新任の方やベテランの方、管理職を対象とした幅広いコンテンツをご用意しております。
お問い合わせ
コストダウンが利益に直結する術だと理解していても、なかなか前に進めることができない状況。そんな時は、newjiのコストダウン自動化機能で大きく利益貢献しよう!
(Β版非公開)