- お役立ち記事
- Contingency plans for purchasing departments to reduce material supply risks
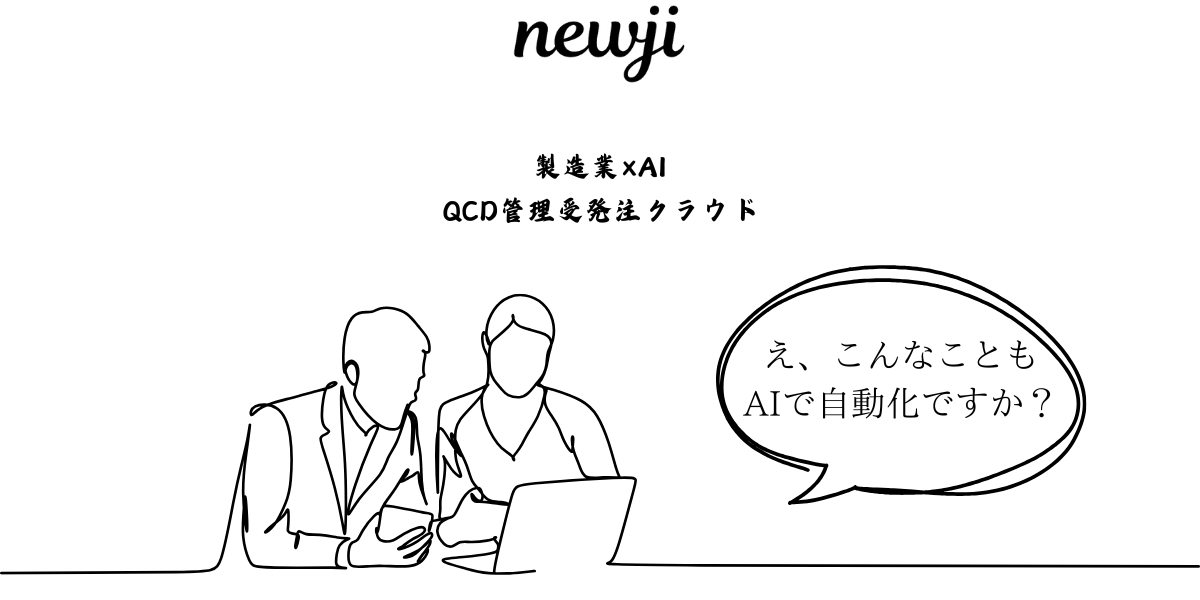
Contingency plans for purchasing departments to reduce material supply risks
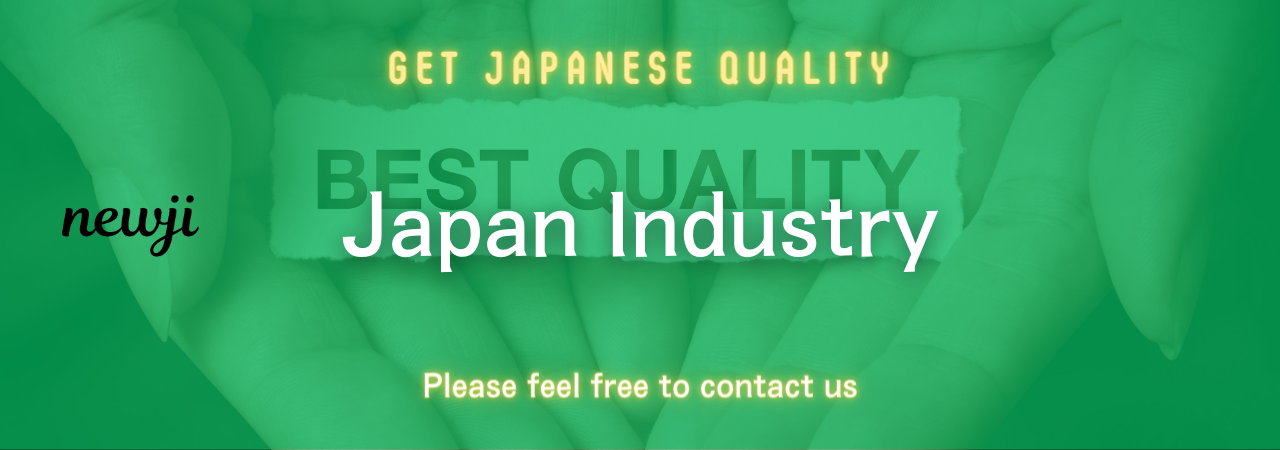
目次
Understanding Supply Risks in Procurement
Purchasing departments play a crucial role in ensuring the smooth operation of any business.
Their primary responsibility is to secure the necessary materials needed for production and service delivery.
However, this task is not without its challenges.
One of the most significant issues that procurement professionals face is the risk associated with material supply disruptions.
These risks can arise from various factors such as environmental disasters, geopolitical tensions, supplier insolvencies, and fluctuating market demands.
Material supply risks can lead to significant setbacks for a business, ranging from production delays to increased costs.
Understanding these risks is the first step in developing effective contingency plans.
By recognizing potential threats, purchasing departments can be better prepared to tackle them head-on, ensuring a steady and reliable flow of materials needed for business continuity.
Strategies for Minimizing Supply Chain Risks
To address material supply risks effectively, purchasing departments need to implement comprehensive strategies.
These strategies focus on minimizing potential disruptions and mitigating the impact of unavoidable incidents.
Diversification of Suppliers
One effective way to reduce supply risk is by diversifying the supplier base.
Relying on a single source for essential materials can be risky.
Businesses should build relationships with multiple suppliers, preferably located in different geographical regions.
This approach not only reduces dependency on a single supplier but also provides an alternative source if one supplier faces issues.
Building Strong Supplier Relationships
Another key strategy is to foster strong relationships with suppliers.
By developing close partnerships, businesses can encourage better communication, foster collaboration, and create a reliable supply network.
Regular communication with suppliers helps in anticipating potential disruptions and allows for joint problem-solving.
Such relationships can also lead to priority treatment in cases where supply shortages occur.
Implementing Inventory Management Systems
Adopting robust inventory management systems can significantly help in handling supply chain disruptions.
These systems enable businesses to monitor stock levels in real time and make informed decisions about reordering materials.
By maintaining optimal inventory levels, purchasing departments can cushion the impact of supply chain disruptions without overstocking, which ties up capital.
Evaluating Suppliers for Reliability and Stability
Before entering into a partnership, purchasing departments should thoroughly evaluate potential suppliers for their reliability and stability.
This includes assessing the supplier’s financial health, production capabilities, and historical performance in terms of timely delivery and quality assurance.
Reliable suppliers are vital in minimizing the risks associated with material supply disruptions.
Developing a Contingency Plan
Having a well-defined contingency plan is crucial for any purchasing department aiming to reduce material supply risks.
A contingency plan outlines the procedures and actions necessary to deal with unforeseen disruptions.
Identifying Critical Materials
The first step in creating a contingency plan is identifying materials critical to the organization’s operations.
These materials should be prioritized in the risk management strategy, with specific plans developed to ensure their continuous supply.
Understanding which materials play a pivotal role in production helps to focus efforts on securing them against unforeseen disruptions.
Risk Assessment and Analysis
Conducting a comprehensive risk assessment allows purchasing departments to understand the potential threats to their supply chain.
This process involves analyzing various risk factors, from market volatility to geopolitical events.
Once these risks are identified, purchasing departments can prioritize them based on impact and likelihood, crafting strategies that address each scenario specifically.
Creating a Flexible Response Framework
An effective contingency plan should include a flexible response framework that enables quick decision-making during a disruption.
This framework should outline the steps to be taken in different scenarios, including alternative sourcing strategies, communication plans with stakeholders, and resource allocation.
Flexibility is key in ensuring that the organization can adapt to changing situations rapidly.
Regular Testing and Updating of the Plan
It’s essential that the contingency plan isn’t static.
Regular testing through drills and simulations will help identify any weaknesses or areas for improvement.
Moreover, as the business environment and market conditions evolve, the plan should be updated to reflect new risks and strategies.
Utilizing Technology for Better Risk Management
In today’s fast-paced world, technology can be a game-changer for purchasing departments striving to manage material supply risks more effectively.
By leveraging advanced tools and software, businesses can enhance visibility, improve communication, and streamline processes.
Supply Chain Visibility Tools
Tools designed to enhance supply chain visibility can provide real-time data on the status of materials, shipments, and suppliers.
Having access to this information allows purchasing departments to anticipate issues before they escalate and respond to them proactively.
Advanced Analytics and Predictive Modeling
Using data analytics and predictive modeling, businesses can better forecast demand, analyze trends, and predict potential supply chain disruptions.
These technologies can help identify patterns that might indicate future supply challenges, allowing organizations to prepare accordingly.
Digital Communication Platforms
Investing in digital communication platforms can facilitate better collaboration between purchasing departments and suppliers.
Seamless communication is crucial in ensuring that everyone is on the same page, expediting decision-making processes during a disruption.
Conclusion
Material supply risks are an inevitable part of the procurement landscape.
However, with well-thought-out contingency plans and effective risk management strategies, purchasing departments can significantly reduce these risks, ensuring business continuity and efficiency.
By diversifying suppliers, building strong relationships, and utilizing technology, companies can create a resilient supply chain that withstands the challenges of today’s dynamic market.
資料ダウンロード
QCD調達購買管理クラウド「newji」は、調達購買部門で必要なQCD管理全てを備えた、現場特化型兼クラウド型の今世紀最高の購買管理システムとなります。
ユーザー登録
調達購買業務の効率化だけでなく、システムを導入することで、コスト削減や製品・資材のステータス可視化のほか、属人化していた購買情報の共有化による内部不正防止や統制にも役立ちます。
NEWJI DX
製造業に特化したデジタルトランスフォーメーション(DX)の実現を目指す請負開発型のコンサルティングサービスです。AI、iPaaS、および先端の技術を駆使して、製造プロセスの効率化、業務効率化、チームワーク強化、コスト削減、品質向上を実現します。このサービスは、製造業の課題を深く理解し、それに対する最適なデジタルソリューションを提供することで、企業が持続的な成長とイノベーションを達成できるようサポートします。
オンライン講座
製造業、主に購買・調達部門にお勤めの方々に向けた情報を配信しております。
新任の方やベテランの方、管理職を対象とした幅広いコンテンツをご用意しております。
お問い合わせ
コストダウンが利益に直結する術だと理解していても、なかなか前に進めることができない状況。そんな時は、newjiのコストダウン自動化機能で大きく利益貢献しよう!
(Β版非公開)