- お役立ち記事
- Continuous Casting in the Steel Industry and Its Benefits
月間76,176名の
製造業ご担当者様が閲覧しています*
*2025年3月31日現在のGoogle Analyticsのデータより
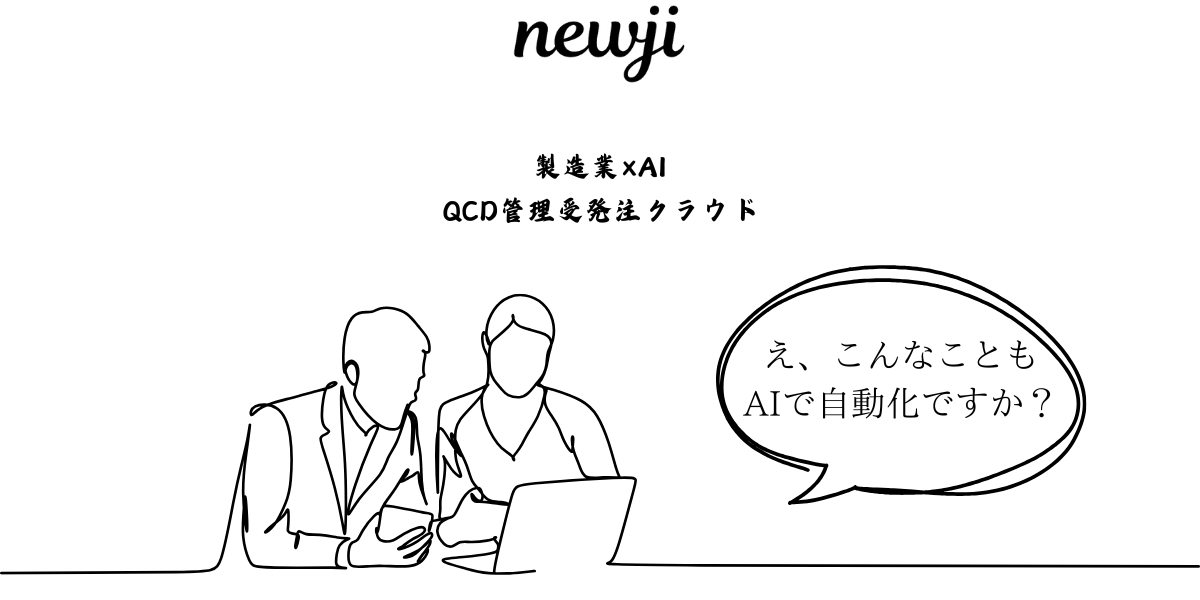
Continuous Casting in the Steel Industry and Its Benefits
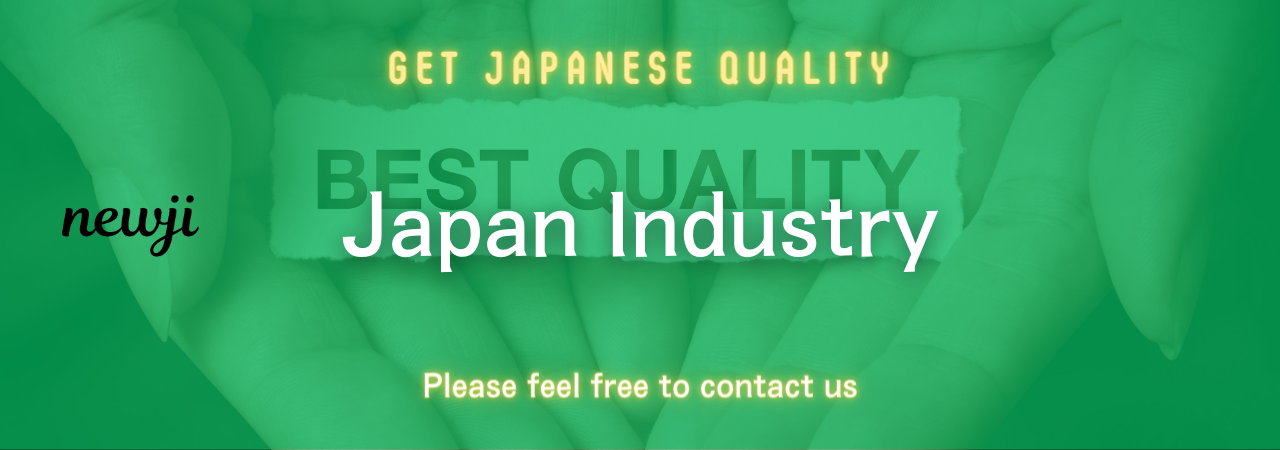
目次
Understanding Continuous Casting
Continuous casting, often referred to as strand casting, is a crucial process in the steel industry that transforms molten steel into semi-finished slabs, billets, or blooms for subsequent rolling in the finishing mills.
This method contrasts with traditional ingot casting and has revolutionized steelmaking by significantly enhancing efficiency, quality, and cost-effectiveness.
The process begins by pouring molten steel from a ladle into a tundish, which acts as a reservoir to feed the molten steel smoothly into the mold.
The mold is water-cooled and open at both ends, allowing the steel to solidify as it descends.
As the steel continues to flow through the mold, it cools and achieves its desired shape.
Rollers guide and support the emerging strand, preventing it from bending under its own weight.
Because the casting is continuous, the process produces long strands of steel that are later cut into desired lengths.
The Benefits of Continuous Casting
Continuous casting offers several advantages over traditional methods, making it a preferred choice in modern steel production.
Improved Quality
One of the primary benefits of continuous casting is the improvement in the quality of the steel produced.
The process significantly reduces the occurrence of segregation and inclusions, common flaws in steel that can reduce its structural integrity.
The steady and controlled cooling process allows for a uniform microstructure, which enhances the mechanical properties of the steel.
Furthermore, continuous casting results in a fine surface quality with minimal defects, reducing the need for extensive surface conditioning.
Enhanced Efficiency
Continuous casting is highly efficient compared to ingot casting.
The process reduces the labor and time required to cast steel, leading to quicker production cycles.
This efficiency is largely due to the reduction in handling and reheating steps that are necessary in traditional casting methods.
As a result, steel plants can produce more steel in the same amount of time, meeting high demands without compromising on quality.
Cost-Effectiveness
Due to its efficient nature, continuous casting helps in reducing production costs.
The process minimizes energy consumption, as it eliminates the need for ingot reheating.
Additionally, the reduced scrap and defect rates contribute to lower material costs.
Continuous casting also leads to savings in manpower and maintenance, further enhancing its economic viability for large-scale steel production.
Continuous Casting Process and Machinery
The machinery used in continuous casting is a sophisticated array of components designed to handle high temperatures and moving materials efficiently.
The Mold
At the heart of the continuous casting machine is the mold.
This water-cooled component shapes the steel into the desired initial form.
The mold oscillates during casting to prevent the steel from sticking, and it also helps in controlling the initial solidification structure.
The Tundish
The tundish serves as an intermediary vessel that regulates the flow of molten steel from the ladle to the mold.
It helps in distributing the steel evenly, maintaining consistency in product quality, and acts as a buffer to absorb changes in flow rates.
Cooling and Support Systems
As the newly cast steel strand exits the mold, it is supported by a series of rollers which guide it through various cooling stages.
Water sprays or air-mist cooling are often used to control the cooling rate, preventing cracks or other defects in the steel.
These systems are crucial in maintaining the integrity of the casting process and ensuring the final product meets quality standards.
Environmental Impact
The steel industry is constantly working towards reducing its environmental footprint, and continuous casting plays a significant role in these efforts.
The efficiency of the continuous casting process translates to reduced energy consumption and lower carbon emissions compared to ingot casting.
By minimizing waste and improving yield, continuous casting contributes to more sustainable steel production practices.
Applications in the Steel Industry
Continuous casting is integral in the production of various steel products, ranging from construction materials to automotive parts.
Steel Sheets and Plates
A vast majority of steel sheets and plates are produced using continuous casting.
These materials are essential in the construction industry for building infrastructure and in manufacturing sectors for creating durable goods.
Long Products
Steel bars and rods, used in construction and manufacturing, are often produced via continuous casting.
The process enables the production of long and consistent product sizes, crucial for projects requiring specific dimensions and strength.
Specialty Steels
Apart from standard products, continuous casting can also be adapted for the production of specialty steels, including high-alloy and stainless steels.
The precision and control offered by this method are advantageous in achieving the specific properties required for these advanced materials.
Continuous Casting: A Key to Future Innovations
As the steel industry evolves, continuous casting remains at the forefront of technological advancements.
Research and development continue to enhance the process, promising even greater efficiencies and environmental benefits.
Exploring new cooling techniques, advanced monitoring systems, and automation technologies are some of the ways continuous casting is being improved.
These innovations not only bolster the performance of steelmaking operations but also pave the way for new applications in emerging industries.
In conclusion, continuous casting is an essential process in the steel industry that brings numerous benefits including improved quality, enhanced efficiency, and cost-effectiveness.
As technology advances, this casting method will continue to play a critical role in shaping the future of steel production, making it more sustainable and efficient.
資料ダウンロード
QCD管理受発注クラウド「newji」は、受発注部門で必要なQCD管理全てを備えた、現場特化型兼クラウド型の今世紀最高の受発注管理システムとなります。
ユーザー登録
受発注業務の効率化だけでなく、システムを導入することで、コスト削減や製品・資材のステータス可視化のほか、属人化していた受発注情報の共有化による内部不正防止や統制にも役立ちます。
NEWJI DX
製造業に特化したデジタルトランスフォーメーション(DX)の実現を目指す請負開発型のコンサルティングサービスです。AI、iPaaS、および先端の技術を駆使して、製造プロセスの効率化、業務効率化、チームワーク強化、コスト削減、品質向上を実現します。このサービスは、製造業の課題を深く理解し、それに対する最適なデジタルソリューションを提供することで、企業が持続的な成長とイノベーションを達成できるようサポートします。
製造業ニュース解説
製造業、主に購買・調達部門にお勤めの方々に向けた情報を配信しております。
新任の方やベテランの方、管理職を対象とした幅広いコンテンツをご用意しております。
お問い合わせ
コストダウンが利益に直結する術だと理解していても、なかなか前に進めることができない状況。そんな時は、newjiのコストダウン自動化機能で大きく利益貢献しよう!
(β版非公開)