- お役立ち記事
- Continuous Casting Processes and Efficiency Improvement Methods in Copper Products
Continuous Casting Processes and Efficiency Improvement Methods in Copper Products
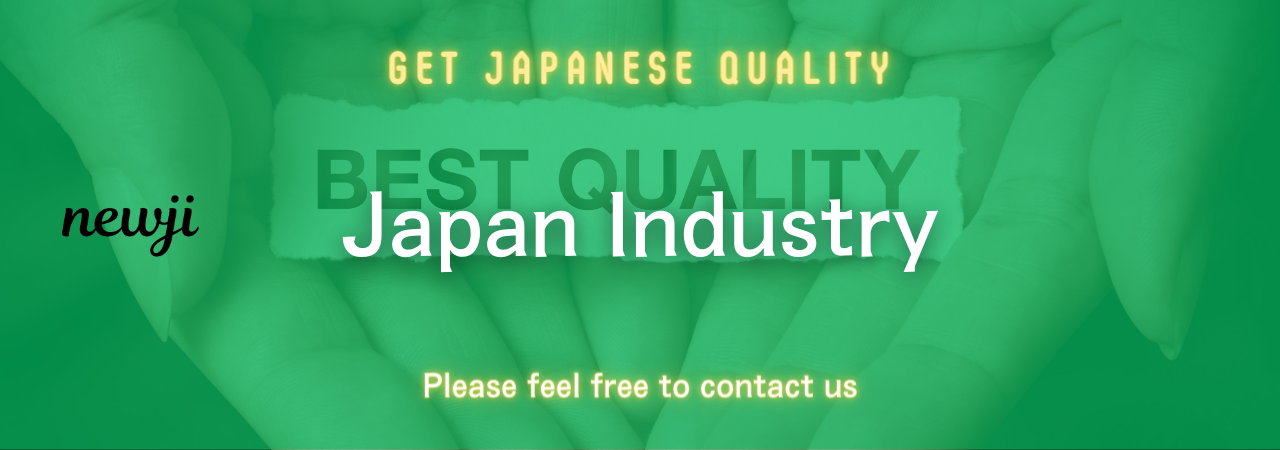
目次
Introduction to Continuous Casting in Copper Production
Continuous casting is a revolutionary process in the copper industry, offering efficiency and improved product quality.
The copper production industry relies heavily on this method, which allows for the seamless creation of products with minimal interruption.
Understanding the basics of continuous casting helps in comprehending its significance in modern manufacturing processes.
What is Continuous Casting?
Continuous casting is a process where molten metal is solidified into a semi-finished billet, bloom, or slab for subsequent rolling.
It essentially replaces the traditional ingot casting, providing enhanced efficiency and output quality.
In the context of copper production, continuous casting ensures a uniform composition and reduces the need for additional rolling and reheating.
The process is automated, making it both time-efficient and cost-effective for large-scale production.
The Process of Continuous Casting in Copper
The continuous casting process begins with molten copper being poured into a water-cooled mold.
The mold is open at the bottom, allowing the metal to solidify as it moves downward.
Once the metal solidifies enough, it is continuously extracted from the mold at a controlled rate.
The newly formed solid strand is then cut into desired lengths, ready for further processing.
This method allows for the control of product dimensions and offers superior surface quality.
Equipment Used in Continuous Casting
Several key components are essential in the continuous casting process for copper.
These include the tundish, which acts as a reservoir to hold the molten metal before it’s fed into the mold.
The mold itself is crucial as it shapes the copper as it solidifies.
Cooling systems are vital to control the temperature and facilitate proper solidification.
Additionally, rollers and withdrawal systems help in extracting the solid copper seamlessly from the mold.
Advantages of Continuous Casting
Continuous casting in copper production offers multiple benefits.
One major advantage is improved energy efficiency.
Since the process requires less reheating, energy consumption is reduced considerably.
The process also minimizes waste as it reduces the need for cutting and machining, leading to efficient use of raw materials.
Moreover, continuous casting results in products with enhanced structural integrity and fewer internal defects.
Efficiency Improvement Methods
Improvements in continuous casting processes can significantly impact the efficiency and quality of copper products.
Here are some methods used to enhance efficiency:
Optimizing Mold Design
Mold design is critical to the success of the continuous casting process.
An optimized mold design can improve the heat extraction during the casting process, leading to faster solidification times and improved product quality.
Computer-aided design (CAD) technology can be used to simulate and optimize mold geometries.
Implementing Advanced Cooling Systems
Efficient cooling is paramount in the continuous casting process.
Advanced cooling systems that provide uniform cooling rates can enhance the microstructures of the copper.
This involves using modern cooling agents and techniques that minimize thermal stress and improve the long-term reliability of products.
Utilizing Sensors and Automation
The incorporation of sensors and automation in continuous casting allows for real-time monitoring and adjustments.
This technology helps in maintaining consistent quality by making instant corrections in the process.
Automated systems can control various parameters like temperature, speed, and cooling rates, ensuring optimized production.
Regular Maintenance and Training
Regular maintenance of equipment is essential for preventing unexpected shutdowns and prolonging the machinery’s lifespan.
In parallel, consistent training programs for operators ensure that personnel are aware of the latest techniques and safety protocols.
These practices lead to smoother operations, reduced errors, and improved efficiency.
Impact of Continuous Casting on Copper Product Quality
Continuous casting significantly influences the quality of copper products.
The controlled nature of this process results in high-purity copper with fewer impurities.
Consistent grain size and uniform composition are achieved, enhancing the mechanical properties of the final product.
Moreover, surface quality is superior, reducing the need for additional surface treatments.
Applications of Continuous Cast Copper Products
The use of continuous casting in copper production facilitates a wide range of applications.
Copper wires, pipes, and sheets produced by this method are widely used in electrical applications due to their superior conductivity.
Additionally, continuous cast copper is used in plumbing, roofing, and various industrial applications where material strength and corrosion resistance are critical.
Future Trends in Continuous Casting
The future of continuous casting in copper production looks promising, with technological advancements paving the way for further improvements.
Innovations in material science can lead to even more efficient cooling and mold designs.
The focus will also increasingly be on sustainable practices, aiming to minimize environmental impacts while maintaining high productivity levels.
Conclusion
Continuous casting has transformed the landscape of copper production.
Through constant innovation and improvements, it can achieve greater efficiency and quality in manufactured products.
As the industry moves forward, embracing new technologies and methods will be key to maintaining competitiveness and meeting the rising demand for high-quality copper products.
資料ダウンロード
QCD調達購買管理クラウド「newji」は、調達購買部門で必要なQCD管理全てを備えた、現場特化型兼クラウド型の今世紀最高の購買管理システムとなります。
ユーザー登録
調達購買業務の効率化だけでなく、システムを導入することで、コスト削減や製品・資材のステータス可視化のほか、属人化していた購買情報の共有化による内部不正防止や統制にも役立ちます。
NEWJI DX
製造業に特化したデジタルトランスフォーメーション(DX)の実現を目指す請負開発型のコンサルティングサービスです。AI、iPaaS、および先端の技術を駆使して、製造プロセスの効率化、業務効率化、チームワーク強化、コスト削減、品質向上を実現します。このサービスは、製造業の課題を深く理解し、それに対する最適なデジタルソリューションを提供することで、企業が持続的な成長とイノベーションを達成できるようサポートします。
オンライン講座
製造業、主に購買・調達部門にお勤めの方々に向けた情報を配信しております。
新任の方やベテランの方、管理職を対象とした幅広いコンテンツをご用意しております。
お問い合わせ
コストダウンが利益に直結する術だと理解していても、なかなか前に進めることができない状況。そんな時は、newjiのコストダウン自動化機能で大きく利益貢献しよう!
(Β版非公開)