- お役立ち記事
- Control design points for each stage of model-based control
月間76,176名の
製造業ご担当者様が閲覧しています*
*2025年3月31日現在のGoogle Analyticsのデータより
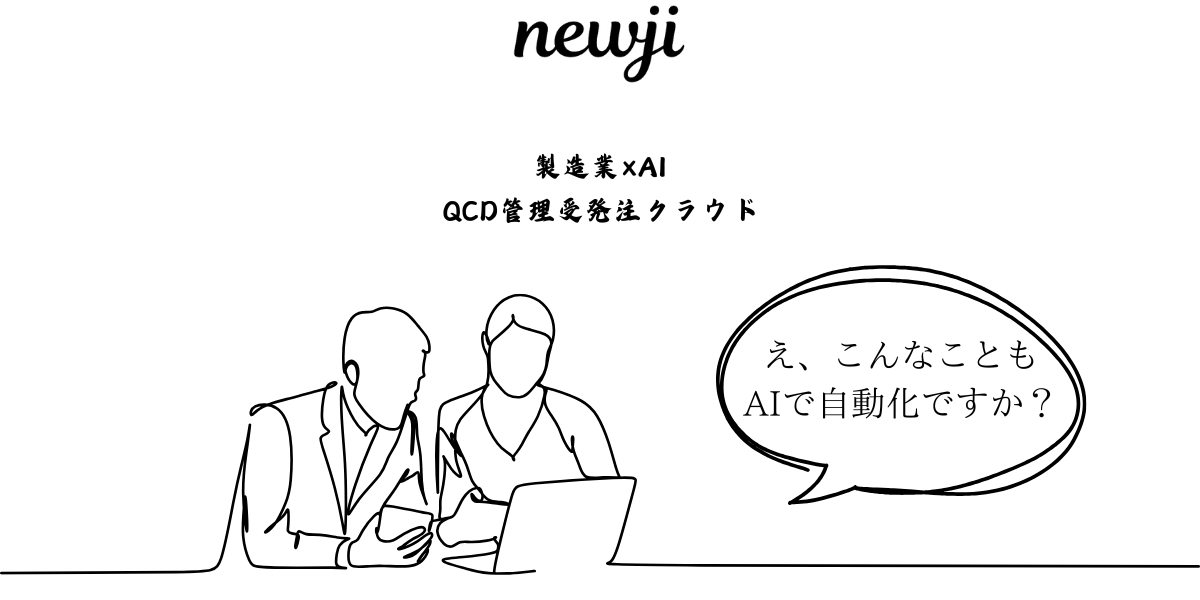
Control design points for each stage of model-based control
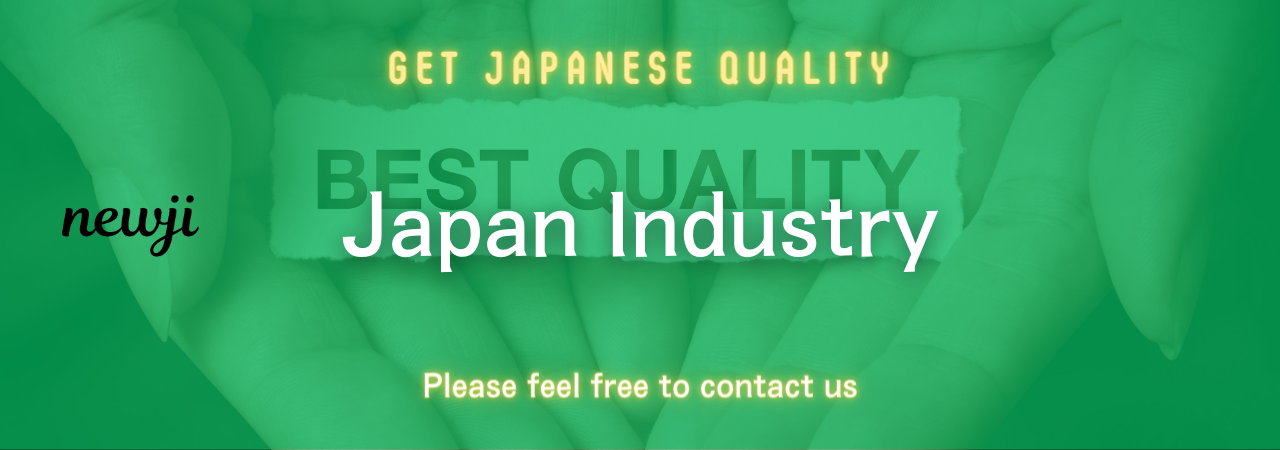
目次
Introduction to Model-Based Control
Model-based control is a method used in control engineering to design controllers using a mathematical model of a system.
This approach offers significant advantages over traditional methods, as it allows for precise control and can predict how a system will respond to different inputs.
The process involves various stages, each requiring careful consideration of specific design points to ensure optimal performance.
Understanding the Basics of Model-Based Control
Before diving into the control design points for each stage, it’s essential to have a solid understanding of the basics of model-based control.
This approach leverages mathematical models that represent real-world systems, including their dynamics and interactions.
These models can be linear or non-linear, depending on the system’s complexity and behavior.
Model-based control offers numerous benefits, including improved accuracy and the ability to handle complex systems with multiple inputs and outputs.
Additionally, it enables engineers to simulate and predict system behavior before implementing a control strategy, reducing the chances of error or unexpected outcomes.
Stages of Model-Based Control Design
The process of designing a model-based control system can be divided into several distinct stages.
Each stage requires careful consideration of specific factors to ensure the overall system operates efficiently and effectively.
1. Modeling the System
The first stage involves developing a mathematical model of the system to be controlled.
This model must accurately represent the system’s dynamics, inputs, and outputs.
It’s crucial to consider the system’s physical properties, such as mass, friction, or resistance, and include them in the model.
Selecting the appropriate level of detail is vital during this stage.
A model that’s too simple may not capture the system’s behavior accurately, while an overly complex model can be difficult to analyze and control.
The goal is to create a model that balances complexity with accuracy, enabling effective control design.
2. Choosing the Control Strategy
Once the model is developed, the next stage is selecting an appropriate control strategy.
There are various control strategies available, including Proportional-Integral-Derivative (PID) control, state-space control, and predictive control.
The choice of control strategy depends on the system’s characteristics and the performance objectives.
PID control is widely used for its simplicity and robustness, making it suitable for systems with straightforward dynamics.
State-space control is ideal for multi-input, multi-output systems, while predictive control is beneficial for systems with constraints or time delays.
3. Controller Design and Parameter Tuning
After selecting the control strategy, the focus shifts to designing the controller and tuning its parameters.
This involves determining the values of control parameters such as gains in a PID controller or the state feedback matrix in state-space control.
Parameter tuning is a critical step, as it directly impacts the system’s performance and stability.
Trial and error may be used initially, but tools like computer-aided design software and optimization algorithms can streamline the process by finding optimal parameter values.
4. Simulation and Validation
Simulating and validating the control design is a crucial stage to ensure the controller’s performance before implementation.
Simulation involves using software to test the controller on the system model, allowing engineers to observe its behavior under various conditions.
During validation, it’s essential to test the controller’s robustness and stability, ensuring it can handle disturbances, noise, and changes in system parameters.
Any issues identified during simulation can be addressed by revising the model or refining the control strategy.
5. Implementation and Testing
The final stage involves implementing the control design on the actual system and conducting thorough testing.
This step ensures that the controller functions as expected in a real-world environment, often requiring minor adjustments post-implementation.
Testing helps identify any discrepancies between the model and the actual system, which can lead to further refinements in the model or control strategy.
It’s also essential to monitor the system’s performance continuously, enabling proactive adjustments and maintenance.
Conclusion
Model-based control offers a sophisticated approach to system control, providing accuracy and adaptability that traditional methods may lack.
By following a structured design process and paying attention to control design points at each stage, engineers can create efficient and robust control systems.
From modeling the system to implementing and testing the control design, every stage demands careful consideration and detailed analysis.
Understanding these stages and control points will equip engineers to tackle complex systems effectively, ensuring optimized performance and reliability in model-based control applications.
資料ダウンロード
QCD管理受発注クラウド「newji」は、受発注部門で必要なQCD管理全てを備えた、現場特化型兼クラウド型の今世紀最高の受発注管理システムとなります。
ユーザー登録
受発注業務の効率化だけでなく、システムを導入することで、コスト削減や製品・資材のステータス可視化のほか、属人化していた受発注情報の共有化による内部不正防止や統制にも役立ちます。
NEWJI DX
製造業に特化したデジタルトランスフォーメーション(DX)の実現を目指す請負開発型のコンサルティングサービスです。AI、iPaaS、および先端の技術を駆使して、製造プロセスの効率化、業務効率化、チームワーク強化、コスト削減、品質向上を実現します。このサービスは、製造業の課題を深く理解し、それに対する最適なデジタルソリューションを提供することで、企業が持続的な成長とイノベーションを達成できるようサポートします。
製造業ニュース解説
製造業、主に購買・調達部門にお勤めの方々に向けた情報を配信しております。
新任の方やベテランの方、管理職を対象とした幅広いコンテンツをご用意しております。
お問い合わせ
コストダウンが利益に直結する術だと理解していても、なかなか前に進めることができない状況。そんな時は、newjiのコストダウン自動化機能で大きく利益貢献しよう!
(β版非公開)