- お役立ち記事
- Control the manufacturing site with DCS system! Improvement of stable operation and safety
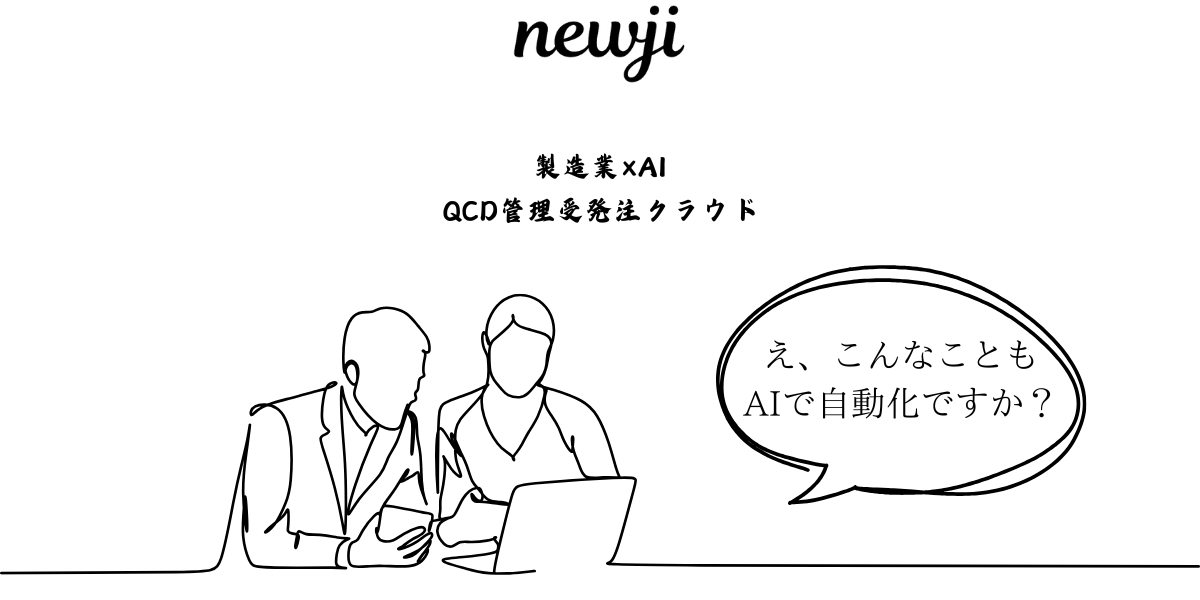
Control the manufacturing site with DCS system! Improvement of stable operation and safety
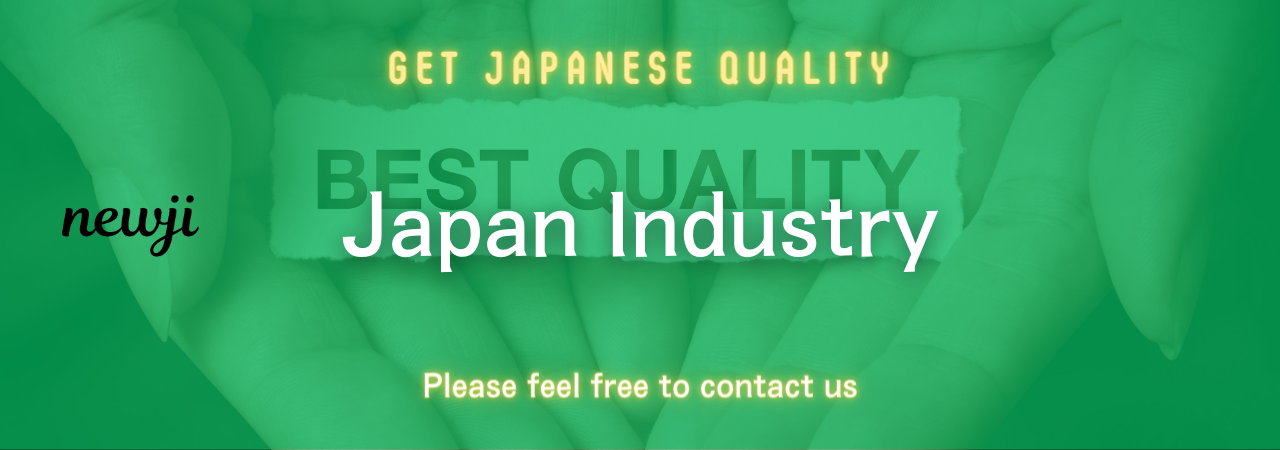
In today’s rapidly evolving industrial landscape, the quest for stability, safety, and efficiency in manufacturing processes is paramount. One of the most powerful tools to achieve these objectives is the Distributed Control System (DCS).
Understanding DCS
A Distributed Control System (DCS) is an advanced computer system that controls industrial processes and ensures the seamless operation of manufacturing sites. Unlike traditional control systems that rely on a central controller, a DCS disperses the control functions across various interconnected controllers. This decentralized approach is pivotal in enhancing the robustness and efficiency of manufacturing operations.
The Core Components of DCS
A DCS typically comprises several crucial components, which work in harmony to manage industrial processes:
1. Controllers: These are the brains of the DCS, executing control strategies and managing process variables.
2. Human-Machine Interface (HMI): This interface allows operators to interact with the system, monitor processes, and make adjustments as necessary.
3. Field Devices: Including sensors and actuators, these devices gather real-time data and implement control actions.
4. Communication Network: Ensures seamless data transfer and coordination between various DCS components.
Enhancing Stability with DCS
Stability in manufacturing processes is fundamental to maintaining product quality and operational efficiency. Here’s how DCS contributes to it:
1. Real-Time Data Monitoring: DCS systems continuously collect data from various field devices, providing operators with a real-time snapshot of the entire manufacturing site. This continuous monitoring helps promptly detect and rectify any deviations from the desired operational parameters.
2. Advanced Control Algorithms: Modern DCS systems employ sophisticated control algorithms that can predict and mitigate potential process disruptions. These algorithms adjust process variables to ensure stability, even under changing operational conditions.
3. Fault Tolerance: The decentralized nature of DCS provides inherent fault tolerance. If a single controller fails, other controllers can take over its tasks, preventing process disruptions and ensuring uninterrupted operation.
Boosting Safety through DCS
Safety is a critical concern in manufacturing environments, where the slightest mishap can lead to significant damage and endanger lives. DCS systems play a vital role in enhancing safety through the following methods:
1. Enhanced Monitoring Capabilities: Through continuous monitoring of process variables, DCS systems can promptly identify hazardous conditions. For instance, if a temperature sensor detects a dangerous rise in temperature, the DCS can trigger automated alarms and shutdown procedures to prevent accidents.
2. Emergency Response: In critical situations, DCS systems can execute predefined emergency protocols. Rapid response mechanisms ensure that processes are safely shut down or adjusted to mitigate risks, protecting both personnel and equipment.
3. Data Logging and Analysis: DCS systems log extensive data related to process operations and incidents. This historical data can be analyzed to identify recurring issues and improve safety protocols, thereby reducing the likelihood of future accidents.
The Role of DCS in Operational Efficiency
Efficiency in manufacturing processes translates to cost savings and increased productivity. Here’s how DCS contributes to operational efficiency:
1. Optimal Resource Management: DCS systems provide comprehensive insights into resource utilization, helping manufacturers optimize the use of raw materials, energy, and labor. Efficient resource management minimizes waste and maximizes productivity.
2. Streamlined Automation: DCS systems enable the automation of complex processes, reducing reliance on manual intervention. Automated processes are not only faster but also more consistent and precise, leading to enhanced operational efficiency.
3. Predictive Maintenance: By continuously monitoring equipment conditions, DCS systems can predict maintenance needs before failures occur. This proactive approach minimizes downtime and extends the lifespan of critical machinery.
Implementing DCS: Key Considerations
While the benefits of DCS are substantial, successful implementation requires careful planning and consideration. Here are some key steps to ensure a smooth transition:
1. Thorough Needs Assessment: Begin by conducting a comprehensive assessment of your manufacturing site’s needs. Identify critical processes that could benefit from DCS integration and outline specific goals you aim to achieve.
2. Vendor Selection: Choose a reputable DCS vendor with a proven track record in your industry. Collaborate with the vendor to customize the system according to your unique requirements.
3. Integration and Training: Ensure seamless integration of the DCS with existing processes and infrastructure. Provide extensive training to your workforce to familiarize them with the new system, fostering confidence and competence.
4. Continuous Monitoring and Improvement: Post-implementation, maintain a rigorous monitoring regime to assess the system’s performance. Gather feedback from operators and make necessary adjustments to optimize the DCS’s functionality continuously.
Real-World Success Stories
Numerous industries have leveraged DCS systems to achieve remarkable improvements in their operations. Here are some real-world success stories:
1. Chemical Manufacturing: A leading chemical manufacturer implemented a DCS to manage complex chemical reactions. This resulted in consistent product quality, reduced process variability, and enhanced safety through automated shutdown mechanisms in case of deviations.
2. Energy Production: An energy production facility employed a DCS to monitor and control power generation processes. The system’s real-time data monitoring capabilities enabled operators to optimize energy output, resulting in significant cost savings and reduced environmental impact.
3. Food and Beverage Industry: A food processing plant integrated a DCS to manage intricate production lines. The system’s advanced control algorithms ensured precise ingredient mixing, leading to uniform product quality and heightened consumer satisfaction.
Conclusion
In the competitive world of manufacturing, ensuring stable operation, safety, and efficiency is key to staying ahead. Implementing a Distributed Control System (DCS) can revolutionize the way you manage your manufacturing site, offering unparalleled benefits through real-time monitoring, advanced control algorithms, and enhanced safety protocols.
By harnessing the power of DCS, manufacturers can achieve not only stable and safe operations but also substantial improvements in operational efficiency. Through careful planning, diligent implementation, and continuous monitoring, the transformative potential of DCS can be fully realized, setting the stage for a more secure, efficient, and productive future.
Whether you’re in chemical manufacturing, energy production, or the food and beverage industry, embracing a DCS can pave the way for new levels of excellence in your operations. Take the leap today, and propel your manufacturing site into a future of stability, safety, and efficiency.
資料ダウンロード
QCD調達購買管理クラウド「newji」は、調達購買部門で必要なQCD管理全てを備えた、現場特化型兼クラウド型の今世紀最高の購買管理システムとなります。
ユーザー登録
調達購買業務の効率化だけでなく、システムを導入することで、コスト削減や製品・資材のステータス可視化のほか、属人化していた購買情報の共有化による内部不正防止や統制にも役立ちます。
NEWJI DX
製造業に特化したデジタルトランスフォーメーション(DX)の実現を目指す請負開発型のコンサルティングサービスです。AI、iPaaS、および先端の技術を駆使して、製造プロセスの効率化、業務効率化、チームワーク強化、コスト削減、品質向上を実現します。このサービスは、製造業の課題を深く理解し、それに対する最適なデジタルソリューションを提供することで、企業が持続的な成長とイノベーションを達成できるようサポートします。
オンライン講座
製造業、主に購買・調達部門にお勤めの方々に向けた情報を配信しております。
新任の方やベテランの方、管理職を対象とした幅広いコンテンツをご用意しております。
お問い合わせ
コストダウンが利益に直結する術だと理解していても、なかなか前に進めることができない状況。そんな時は、newjiのコストダウン自動化機能で大きく利益貢献しよう!
(Β版非公開)