- お役立ち記事
- Cooling optimization for injection molds that design leaders in the plastic molding industry need to know
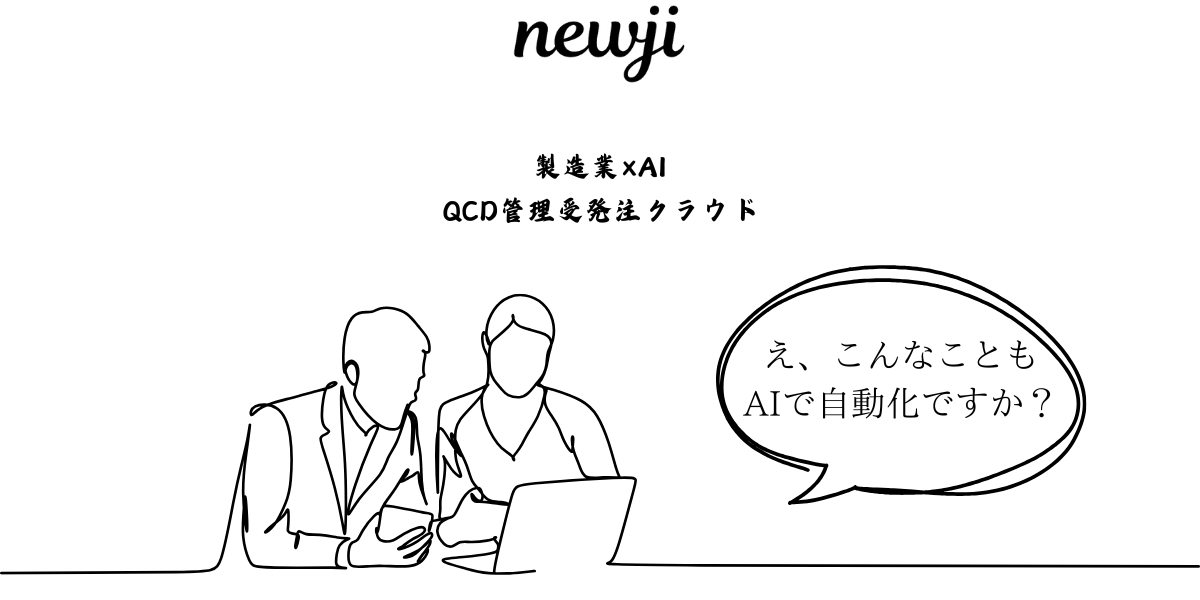
Cooling optimization for injection molds that design leaders in the plastic molding industry need to know
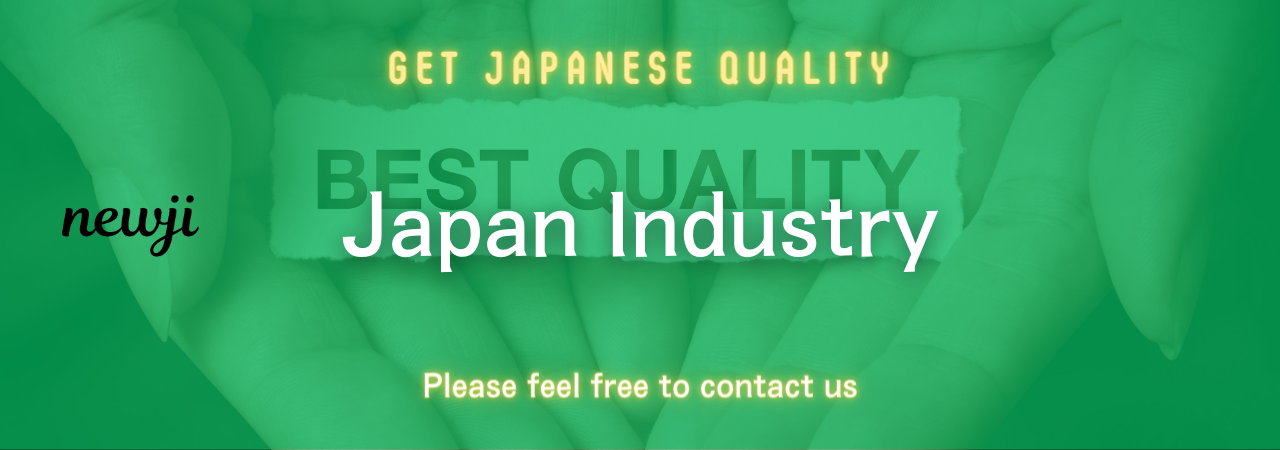
目次
Understanding the Importance of Cooling Optimization
In the world of plastic molding, efficiency is paramount.
Design leaders in the industry are constantly seeking ways to improve the production process, reduce costs, and enhance the quality of the final product.
Among the various factors affecting the molding process, cooling optimization stands out as a critical aspect to consider.
Cooling optimization involves refining the cooling phase of the injection molding process, which has a significant impact on cycle times, production efficiency, and the physical properties of the molded parts.
Efficient cooling is a game-changer that can lead to shorter cycle times, reduced energy consumption, and improved part quality.
Let’s delve deeper into how design leaders can benefit from optimizing cooling in injection molds.
The Cooling Phase: A Crucial Component
The injection molding process involves several stages, including filling, packing, cooling, and ejection.
Among these, the cooling phase accounts for the largest portion of the cycle time.
During this phase, the molten material solidifies within the mold cavity.
Effective cooling is essential to ensure the part achieves the desired dimensional stability, mechanical properties, and appearance.
Poor cooling can lead to numerous issues such as warping, sink marks, and residual stress in the final product.
By optimizing the cooling process, these potential defects are minimized, resulting in a product that meets high-quality standards.
Strategies for Cooling Optimization
Design leaders can implement several strategies to enhance cooling in injection molds.
These strategies not only improve the efficiency of the production process but also contribute to the overall sustainability of the operation.
1. Designing Efficient Cooling Channels
The design of cooling channels within the mold plays a pivotal role in cooling optimization.
Uniform cooling can be achieved by strategically placing these channels to ensure even heat distribution and rapid cooling.
Advanced software tools help design leaders simulate different cooling channel configurations to determine the most effective setup.
Conformal cooling channels, which align with the contours of the part, offer better heat transfer compared to traditional straight-line channels.
This innovative approach enhances cooling efficiency, reduces cycle time, and improves part quality.
2. Utilizing High Conductivity Materials
The choice of materials for mold construction can significantly impact the cooling process.
Using materials with high thermal conductivity facilitates faster heat transfer, leading to quicker cooling.
Beryllium copper, for example, is an excellent choice for mold inserts due to its superior thermal conductivity, enhancing cooling efficiency and reducing cycle time.
3. Implementing Advanced Cooling Techniques
Innovation in cooling technology continues to evolve.
Design leaders can adopt advanced cooling techniques such as rapid heat cycle molding (RHCM) and variotherm technology.
These methods involve controlling the mold temperature dynamically, optimizing the cooling phase and improving part surface quality.
Additionally, the use of thermal analysis software enables precise control and monitoring of the mold temperature, allowing for real-time adjustments to optimize cooling performance.
4. Enhancing Mold Temperature Control
Accurate temperature control is a fundamental aspect of cooling optimization.
Utilizing modern temperature control units that provide flexible configuration and precise control can make a significant difference.
This approach ensures the mold maintains the optimal temperature throughout the production process, facilitating consistent cooling and reducing cycle time.
Benefits of Cooling Optimization
Investing in cooling optimization yields numerous benefits for design leaders in the plastic molding industry.
Reduced Cycle Time
By enhancing the cooling process, cycle time can be significantly reduced.
This leads to increased production output, allowing manufacturers to meet higher demand without compromising on quality.
Shorter cycle times also mean reduced energy consumption, contributing to a more sustainable production process.
Improved Part Quality
Effective cooling ensures that the molded parts maintain dimensional stability and meet stringent quality standards.
The risk of defects such as warping and shrinkage is minimized, resulting in superior product quality and less waste.
Cost Efficiency
Optimizing the cooling process can lead to cost savings in several areas, including energy consumption and material waste.
A more efficient process reduces operational costs and increases profit margins, providing a competitive edge in the industry.
Environmental Impact
Sustainability is becoming increasingly important across all industries.
By reducing cycle times and energy consumption, cooling optimization contributes to a smaller carbon footprint.
Design leaders who prioritize sustainable practices are better positioned to meet the growing demand for environmentally responsible manufacturing.
The Future of Cooling Optimization in Injection Molding
As technology continues to advance, the scope for cooling optimization will expand further.
Emerging technologies such as artificial intelligence and machine learning offer exciting possibilities for enhancing injection molding processes.
Design leaders can leverage these technologies to analyze data, predict optimal cooling parameters, and improve overall efficiency.
Furthermore, collaboration between manufacturers, material suppliers, and software developers will drive innovation in cooling solutions.
The integration of smart technologies into the injection molding process will provide real-time insights and automated adjustments, further enhancing cooling optimization.
In conclusion, cooling optimization is a vital consideration for design leaders in the plastic molding industry.
By implementing effective strategies and embracing new technologies, manufacturers can achieve significant improvements in production efficiency, part quality, and sustainability.
The future holds immense potential for advancements in cooling techniques, paving the way for more streamlined and eco-friendly manufacturing processes.
資料ダウンロード
QCD調達購買管理クラウド「newji」は、調達購買部門で必要なQCD管理全てを備えた、現場特化型兼クラウド型の今世紀最高の購買管理システムとなります。
ユーザー登録
調達購買業務の効率化だけでなく、システムを導入することで、コスト削減や製品・資材のステータス可視化のほか、属人化していた購買情報の共有化による内部不正防止や統制にも役立ちます。
NEWJI DX
製造業に特化したデジタルトランスフォーメーション(DX)の実現を目指す請負開発型のコンサルティングサービスです。AI、iPaaS、および先端の技術を駆使して、製造プロセスの効率化、業務効率化、チームワーク強化、コスト削減、品質向上を実現します。このサービスは、製造業の課題を深く理解し、それに対する最適なデジタルソリューションを提供することで、企業が持続的な成長とイノベーションを達成できるようサポートします。
オンライン講座
製造業、主に購買・調達部門にお勤めの方々に向けた情報を配信しております。
新任の方やベテランの方、管理職を対象とした幅広いコンテンツをご用意しております。
お問い合わせ
コストダウンが利益に直結する術だと理解していても、なかなか前に進めることができない状況。そんな時は、newjiのコストダウン自動化機能で大きく利益貢献しよう!
(Β版非公開)