- お役立ち記事
- Correct design drawings for mechanical designers, how to represent geometric tolerances, and application to accuracy assurance
Correct design drawings for mechanical designers, how to represent geometric tolerances, and application to accuracy assurance
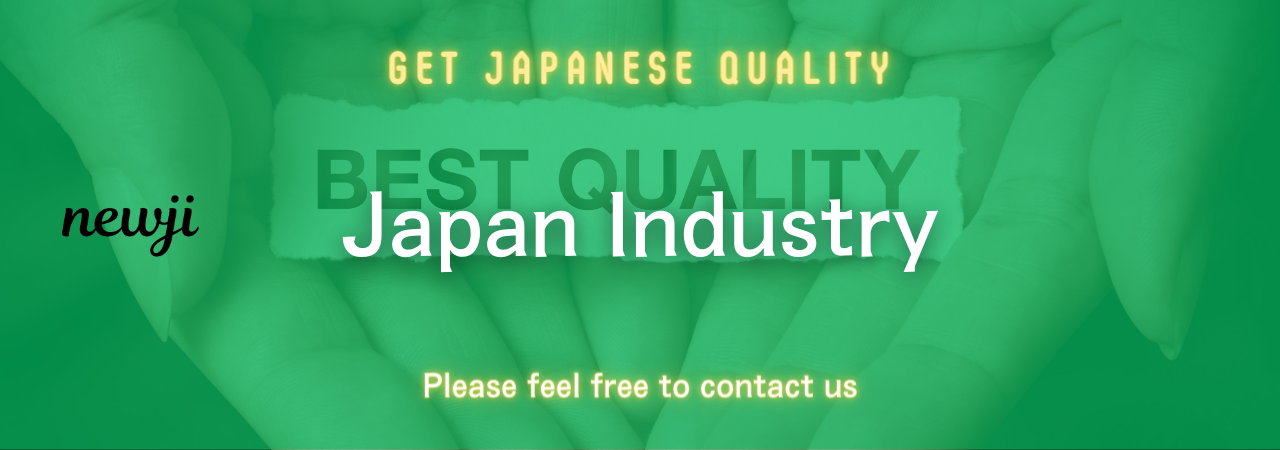
Understanding Design Drawings for Mechanical Designers
In the realm of mechanical design, understanding how to accurately interpret design drawings is crucial.
Design drawings serve as the blueprint for creating machinery and parts, detailing every critical feature to ensure functionality once the product is completed.
For mechanical designers, these drawings are not just sketches; they are a precise communication tool that dictates every dimension and specification required.
One of the vital aspects of design drawings is geometric tolerances which play a significant role in ensuring that parts fit and function together as intended.
The Importance of Geometric Tolerances
Geometric tolerances are essential parameters defined within design drawings that ensure mechanical parts perform reliably.
These tolerances dictate the allowable variation in the shape and location of features in the component.
By specifying geometric tolerances, mechanical designers can convey the required precision with which a part must be manufactured or assembled.
This involves clearly defining potential deviation limits from the ideal version of the design, ensuring that parts can interchangeably fit together and operate efficiently.
Types of Geometric Tolerances
There are several types of geometric tolerances that designers utilize to communicate part specifications, including form tolerances, orientation tolerances, profile tolerances, location tolerances, and run-out tolerances.
– **Form Tolerances** deal with the shape of a feature, such as flatness, circularity, cylindricity, and straightness.
– **Orientation Tolerances** cover the direction of features like perpendicularity, angularity, and parallelism.
– **Profile Tolerances** define the variable limits for surfaces or lines.
– **Location Tolerances** relate to the exact placement of features and include position, concentricity, and symmetry.
– **Run-out Tolerances** handle the control over the deviation of a circular feature and include circular and total run-out.
Correct Representation in Design Drawings
The correct representation of geometric tolerances in design drawings is a critical task for a mechanical designer.
This requires a comprehensive understanding of GD&T (Geometric Dimensioning and Tolerancing), which standardizes the notation used to represent tolerances.
Within a drawing, tolerances are denoted using symbols and are typically displayed in feature control frames that detail the specific tolerance type and value.
Understanding how to effectively utilize these symbols ensures that everyone involved in the manufacturing process understands the design intentions and requirements.
A feature control frame, for example, typically includes the geometric characteristic, tolerance value, any modifiers, and datum references when needed.
The clarity and accuracy of this representation ensure that the manufacturing team can achieve the necessary quality and functionality in the finished product.
Application to Precision and Accuracy Assurance
Applying geometric tolerances accurately within design drawings is directly tied to ensuring precision and accuracy during manufacturing.
Tolerances define the limits within which a product must be produced and assembled to function as intended.
By clearly specifying these parameters, designers ensure that the final product meets quality standards and performance requirements.
When geometric tolerances are correctly applied, they contribute not only to the interchangeability of parts but also to reducing waste and rework during production.
A proper understanding of tolerances allows designers to predict how deviations might affect their designs and to plan accordingly for acceptable variability.
Tolerance Analysis and Design Optimization
Incorporating geometric tolerances requires tolerance analysis and design optimization as part of the design process.
Tolerance analysis involves assessing the accumulated variations within a design to predict how these might affect the product’s overall performance.
This involves utilizing mathematical models and software that examine the potential deviations and help in defining achievable tolerances across various components.
Conversely, design optimization entails making necessary adjustments to a design to enhance performance and reduce manufacturing costs, while ensuring all tolerance requirements are met.
This process can involve redesigning parts, altering dimensions, or updating material selection to better align with geometric tolerance requirements without compromising functionality or quality.
Communicating with a Multidisciplinary Team
For mechanical designers, communicating geometric tolerances and design drawings accurately is pivotal in a multidisciplinary team setting.
Since these design drawings are essential for manufacturing, assembly, engineering, quality control, and more, everyone must understand and interpret them in the same way.
Clear communication reduces the risk of misinterpretations that could lead to costly errors in manufacturing and assembly processes.
Therefore, standardizing the interpretation of design drawings across all teams involved in product development is vital for seamless collaboration and effective production.
Conclusion
Understanding geometric tolerances and their correct representation in design drawings is an indispensable skill for mechanical designers.
These tolerances ensure that parts are manufactured accurately to fit and function as intended, minimizing errors and maximizing efficiency.
By mastering the application and communication of geometric tolerances, designers support the production of high-quality, reliable products and maintain consistent collaboration with engineering and manufacturing teams.
Through proper analysis and optimization, designers can refine their designs to achieve both precision and accuracy with cost-effective methods.
資料ダウンロード
QCD調達購買管理クラウド「newji」は、調達購買部門で必要なQCD管理全てを備えた、現場特化型兼クラウド型の今世紀最高の購買管理システムとなります。
ユーザー登録
調達購買業務の効率化だけでなく、システムを導入することで、コスト削減や製品・資材のステータス可視化のほか、属人化していた購買情報の共有化による内部不正防止や統制にも役立ちます。
NEWJI DX
製造業に特化したデジタルトランスフォーメーション(DX)の実現を目指す請負開発型のコンサルティングサービスです。AI、iPaaS、および先端の技術を駆使して、製造プロセスの効率化、業務効率化、チームワーク強化、コスト削減、品質向上を実現します。このサービスは、製造業の課題を深く理解し、それに対する最適なデジタルソリューションを提供することで、企業が持続的な成長とイノベーションを達成できるようサポートします。
オンライン講座
製造業、主に購買・調達部門にお勤めの方々に向けた情報を配信しております。
新任の方やベテランの方、管理職を対象とした幅広いコンテンツをご用意しております。
お問い合わせ
コストダウンが利益に直結する術だと理解していても、なかなか前に進めることができない状況。そんな時は、newjiのコストダウン自動化機能で大きく利益貢献しよう!
(Β版非公開)