- お役立ち記事
- Corrosion mechanisms and examples of electronic components and corrosion prevention techniques
月間77,185名の
製造業ご担当者様が閲覧しています*
*2025年2月28日現在のGoogle Analyticsのデータより
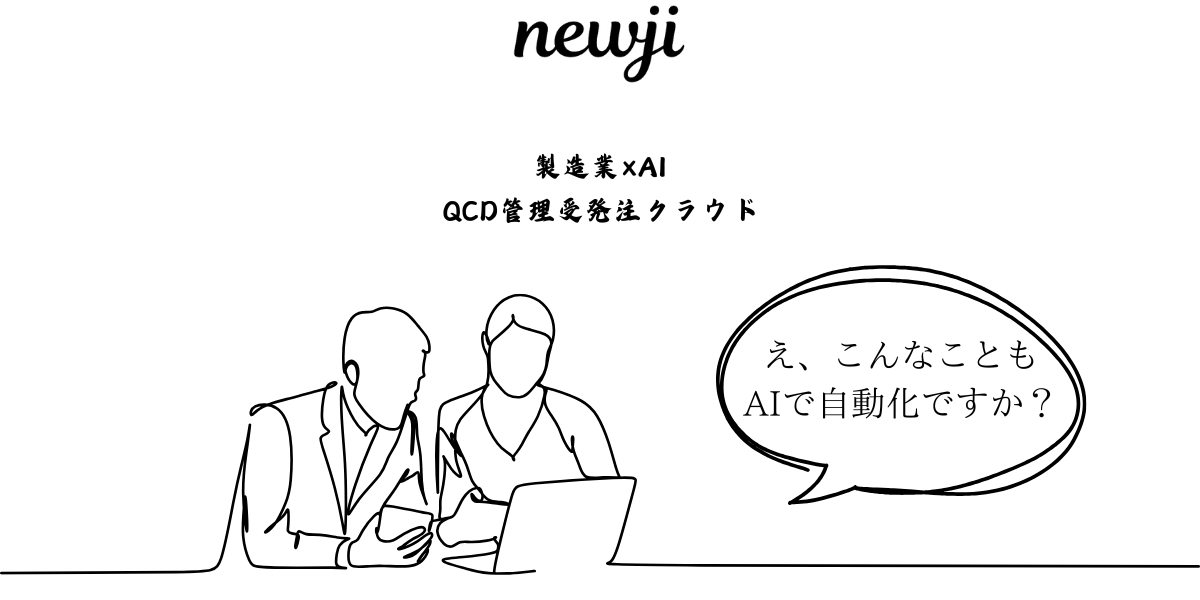
Corrosion mechanisms and examples of electronic components and corrosion prevention techniques
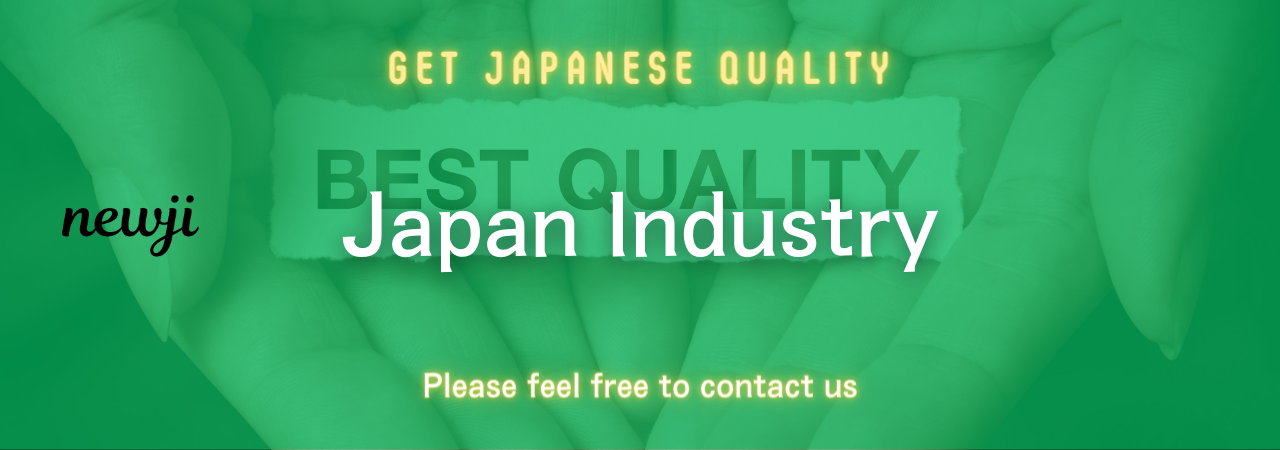
目次
Understanding Corrosion in Electronic Components
Electronic components play a crucial role in our daily lives, powering everything from smartphones to industrial machinery.
Despite their importance, these components are vulnerable to a silent and often invisible enemy: corrosion.
Understanding the mechanisms behind corrosion, the examples of how it can affect electronic components, and the strategies for prevention is essential to ensure the longevity and reliability of electronic devices.
What is Corrosion?
Corrosion is a natural process that involves the deterioration of materials, primarily metals, due to chemical reactions with their environment.
For electronic components, corrosion can manifest as metal dissolution, oxidation, or the formation of rust, among other forms.
This degradation can lead to poor electrical performance, short circuits, and ultimately, device failure.
Mechanisms of Corrosion in Electronics
Corrosion mechanisms in electronic components are influenced by various environmental factors, including moisture, temperature, pollutants, and chemical agents.
Electrolytic Corrosion
Electrolytic corrosion is a common type that occurs when metal parts of electronic components are in contact with an electrolyte, such as water with dissolved ions.
The presence of an electric current accelerates corrosion, breaking down metal surfaces and forming conductive pathways that can cause short circuits.
Galvanic Corrosion
Galvanic corrosion happens when two dissimilar metals are in contact with each other and an electrolyte.
The more anodic metal corrodes while the cathodic metal remains protected, leading to material degradation.
This type of corrosion is notable in connectors and circuit boards where different metals are in proximity.
Atmospheric Corrosion
Atmospheric corrosion occurs when metal surfaces react with moisture and oxygen in the air.
This form of corrosion is particularly problematic in environments with high humidity and pollution, leading to rust and oxidation on exposed metal parts.
Sulphide Corrosion
Sulphide corrosion is notable in environments with sulfur compounds, such as industrial areas.
Sulfur compounds can react with metals like silver and copper, forming tarnish and other corrosive products that impact conductivity.
Examples of Corrosion in Electronic Components
Corrosion can affect a variety of electronic components, each with unique symptoms and consequences.
Printed Circuit Boards (PCBs)
PCBs are particularly vulnerable to corrosion due to their fine copper traces.
Moisture ingress can lead to copper oxidation, causing trace failures and intermittent connections.
The use of solder mask reduces exposure, but defects and prolonged exposure remain a risk.
Connectors and Contacts
Corrosion on metal connectors and contacts can lead to increased contact resistance or complete failure.
This issue is prevalent in devices exposed to high humidity or corrosive gases, such as those in industrial environments.
Integrated Circuits (ICs)
While ICs are typically encapsulated to prevent corrosion, seal breaches or prolonged exposure to harsh environments can cause lead frame corrosion, compromising performance.
Sensors and Relays
These components often have exposed metal parts susceptible to atmospheric and electrolytic corrosion.
Corrosion can lead to erroneous readings in sensors or failure of relays, disrupting operations.
Corrosion Prevention Techniques
Preventing corrosion in electronic components involves a combination of materials selection, protective measures, and environmental controls.
Material Selection
Using corrosion-resistant materials, such as gold or nickel coatings, can significantly diminish the risk of corrosion.
Selecting appropriate alloys for connectors and contacts can further enhance durability.
Environmental Control
Managing the environment where electronic components operate is crucial.
Employing dehumidifiers, air filters, and protective enclosures can minimize exposure to moisture and pollutants.
Conformal Coating
Applying a conformal coating on PCBs and other components can shield them from moisture and corrosive agents.
These coatings act as insulators, protecting the surfaces from direct exposure.
Regular Maintenance and Inspection
Routine maintenance and inspection can help detect early signs of corrosion, allowing for timely intervention.
Cleaning connectors and replacing damaged parts proactively can extend the lifespan of electronic devices.
Combating Galvanic Corrosion
To combat galvanic corrosion, engineers can ensure that dissimilar metals are isolated, using appropriate insulating materials or galvanic corrosion inhibitors.
Design considerations, such as avoiding the contact of dissimilar metals, are also beneficial.
Conclusion
Corrosion in electronic components is a challenging issue that requires attention to detail and strategic planning.
By understanding the mechanisms behind corrosion, recognizing how it affects electronic components, and implementing preventive measures, manufacturers and users alike can reduce the risk of device failure.
Prioritizing corrosion prevention will ensure that electronic components remain reliable and effective, matching the demands of our technology-driven world.
資料ダウンロード
QCD管理受発注クラウド「newji」は、受発注部門で必要なQCD管理全てを備えた、現場特化型兼クラウド型の今世紀最高の受発注管理システムとなります。
ユーザー登録
受発注業務の効率化だけでなく、システムを導入することで、コスト削減や製品・資材のステータス可視化のほか、属人化していた受発注情報の共有化による内部不正防止や統制にも役立ちます。
NEWJI DX
製造業に特化したデジタルトランスフォーメーション(DX)の実現を目指す請負開発型のコンサルティングサービスです。AI、iPaaS、および先端の技術を駆使して、製造プロセスの効率化、業務効率化、チームワーク強化、コスト削減、品質向上を実現します。このサービスは、製造業の課題を深く理解し、それに対する最適なデジタルソリューションを提供することで、企業が持続的な成長とイノベーションを達成できるようサポートします。
製造業ニュース解説
製造業、主に購買・調達部門にお勤めの方々に向けた情報を配信しております。
新任の方やベテランの方、管理職を対象とした幅広いコンテンツをご用意しております。
お問い合わせ
コストダウンが利益に直結する術だと理解していても、なかなか前に進めることができない状況。そんな時は、newjiのコストダウン自動化機能で大きく利益貢献しよう!
(β版非公開)