- お役立ち記事
- Corrosion Resistance Testing and Evaluation Standards in Non-Ferrous Metal Manufacturing
月間76,176名の
製造業ご担当者様が閲覧しています*
*2025年3月31日現在のGoogle Analyticsのデータより
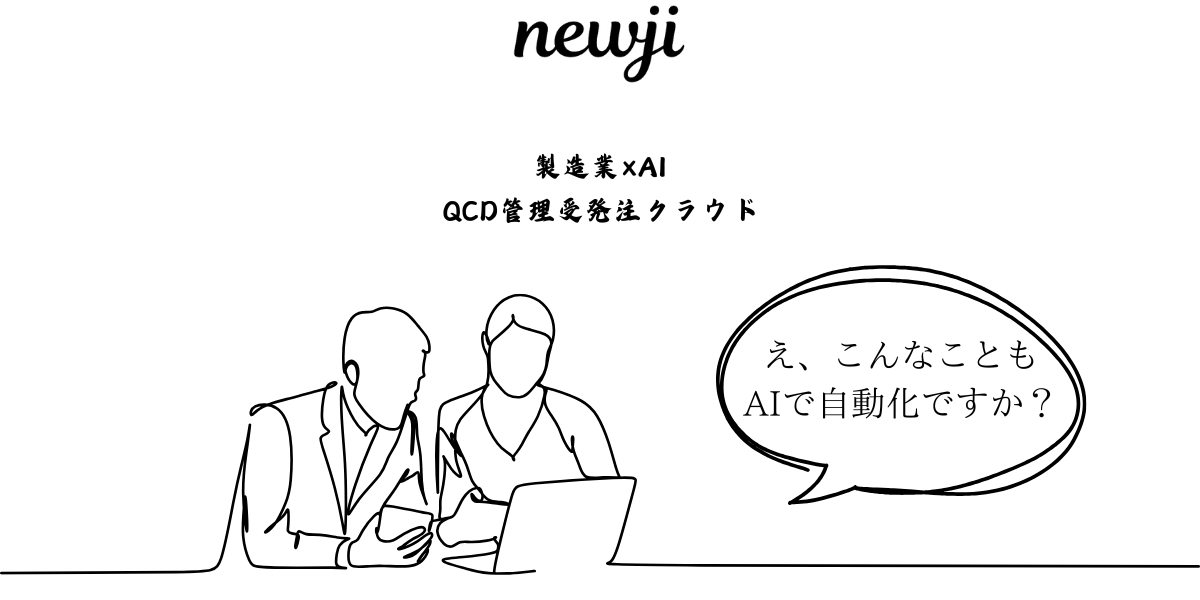
Corrosion Resistance Testing and Evaluation Standards in Non-Ferrous Metal Manufacturing
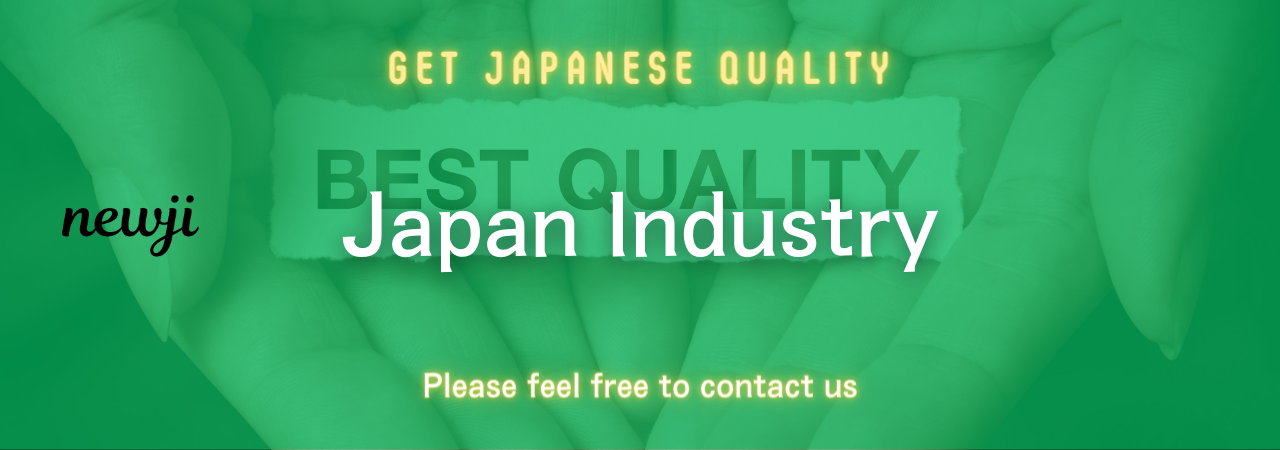
目次
Understanding Corrosion Resistance in Non-Ferrous Metals
Corrosion resistance is a crucial factor in the manufacturing and application of non-ferrous metals.
These metals, which do not contain iron, often exhibit superior resistance to rust and corrosion compared to ferrous metals like steel.
Non-ferrous metals such as aluminum, copper, titanium, and nickel are commonly used in various industries, including construction, automotive, and aerospace, due to their durability and resistance to environmental factors.
The process of corrosion involves the gradual deterioration of materials, typically metals, through chemical reactions with their environment.
This can lead to significant structural and functional failures if not properly managed.
Therefore, understanding and improving the corrosion resistance of non-ferrous metals is vital for extending the lifespan and performance of products and infrastructures.
Common Non-Ferrous Metals and Their Corrosion Resistance
Different non-ferrous metals exhibit varying levels of corrosion resistance.
Here, we’ll explore some common non-ferrous metals and how they withstand corrosive environments.
Aluminum
Aluminum is renowned for its lightweight and excellent corrosion resistance, particularly due to the formation of a natural oxide layer that protects the underlying metal from further oxidation.
This makes aluminum ideal for applications in the transportation and construction sectors, where durability against weathering is crucial.
However, aluminum can be prone to galvanic corrosion when in contact with more noble metals.
Copper
Copper and its alloys, such as bronze and brass, are appreciated for their corrosion resistance and antimicrobial properties.
Copper forms a protective patina over time, which enhances its resistance to atmospheric and marine environments.
This characteristic makes copper a preferred choice for plumbing, electrical, and architectural applications.
Titanium
Titanium is known for its outstanding resistance to corrosion, particularly in harsh and corrosive environments like seawater and acidic conditions.
Its high strength-to-weight ratio and biocompatibility make titanium valuable in the aerospace, medical, and chemical processing industries.
The formation of a stable titanium oxide layer grants it long-lasting protection from corrosion.
Nickel
Nickel and its alloys, such as Inconel and Monel, exhibit impressive corrosion resistance to a wide range of conditions, including high temperatures and reducing environments.
These metals are often used in the chemical industry due to their ability to withstand aggressive chemicals and corrosive gases.
Corrosion Resistance Testing Methods
To ensure the longevity and safety of non-ferrous metals in various applications, manufacturers routinely perform corrosion resistance tests.
These standardized tests help evaluate how well a material can withstand corrosive environments and identify potential weaknesses.
Salt Spray Test
The salt spray test is one of the most common methods for assessing the corrosion resistance of metals.
In this accelerated aging test, a sample is exposed to a fine mist of saltwater for a predetermined period, simulating marine or coastal conditions.
The result provides insight into how well the metal can resist corrosion from salty environments.
Electrochemical Tests
Electrochemical tests, such as potentiodynamic polarization and electrochemical impedance spectroscopy, are used to analyze the corrosion behavior of metals in detail.
These tests involve applying an electric current to the metal and measuring its response, which helps identify corrosion rates and resistance capabilities.
Immersion Testing
In immersion testing, metal samples are submerged in a corrosive solution for a specific duration.
This test evaluates the material’s resistance to specific chemicals and environments, such as acids, bases, and solvents.
It is particularly useful for determining performance in industrial and chemical processing applications.
Atmospheric Corrosion Testing
Atmospheric corrosion testing involves exposing materials to natural outdoor environments and monitoring their performance over time.
This long-term test evaluates the metal’s ability to withstand real-world conditions, such as varying temperatures, humidity, and pollutants.
Standards for Corrosion Resistance Evaluation
To ensure consistency and reliability in corrosion resistance testing, several international and industry standards provide guidelines for conducting evaluations.
ASTM Standards
The American Society for Testing and Materials (ASTM) has developed numerous standards for corrosion testing, such as ASTM B117 for salt spray testing and ASTM G31 for immersion corrosion testing.
These standards outline specific procedures, conditions, and criteria for evaluating the corrosion performance of various materials.
ISO Standards
The International Organization for Standardization (ISO) offers a wide range of corrosion testing standards, including ISO 9227 for salt spray testing.
ISO standards are widely recognized and used globally to ensure consistency and quality in corrosion resistance evaluations.
NACE Standards
The National Association of Corrosion Engineers (NACE) provides industry-specific standards and guidelines aimed at preventing corrosion across various sectors, including oil and gas, marine, and infrastructure.
NACE standards focus on best practices for material selection, testing, and inspection to mitigate corrosion-related risks.
Importance of Corrosion Resistance Testing
Corrosion resistance testing is essential for ensuring the safety, reliability, and performance of non-ferrous metals in demanding applications.
By understanding how materials behave in corrosive environments, manufacturers can make informed decisions regarding material selection, protective coatings, and design considerations.
These tests not only help prevent costly failures and maintenance but also contribute to product and infrastructure longevity.
In conclusion, as non-ferrous metals continue to play a vital role in modern manufacturing and infrastructure, understanding their corrosion resistance is paramount.
Through careful testing and adherence to established standards, manufacturers can ensure that these materials perform optimally in their respective environments, maintaining safety and functionality for years to come.
資料ダウンロード
QCD管理受発注クラウド「newji」は、受発注部門で必要なQCD管理全てを備えた、現場特化型兼クラウド型の今世紀最高の受発注管理システムとなります。
ユーザー登録
受発注業務の効率化だけでなく、システムを導入することで、コスト削減や製品・資材のステータス可視化のほか、属人化していた受発注情報の共有化による内部不正防止や統制にも役立ちます。
NEWJI DX
製造業に特化したデジタルトランスフォーメーション(DX)の実現を目指す請負開発型のコンサルティングサービスです。AI、iPaaS、および先端の技術を駆使して、製造プロセスの効率化、業務効率化、チームワーク強化、コスト削減、品質向上を実現します。このサービスは、製造業の課題を深く理解し、それに対する最適なデジタルソリューションを提供することで、企業が持続的な成長とイノベーションを達成できるようサポートします。
製造業ニュース解説
製造業、主に購買・調達部門にお勤めの方々に向けた情報を配信しております。
新任の方やベテランの方、管理職を対象とした幅広いコンテンツをご用意しております。
お問い合わせ
コストダウンが利益に直結する術だと理解していても、なかなか前に進めることができない状況。そんな時は、newjiのコストダウン自動化機能で大きく利益貢献しよう!
(β版非公開)