- お役立ち記事
- “Cost breakdown analysis” in the manufacturing industry: Basics and practices that purchasing departments should know
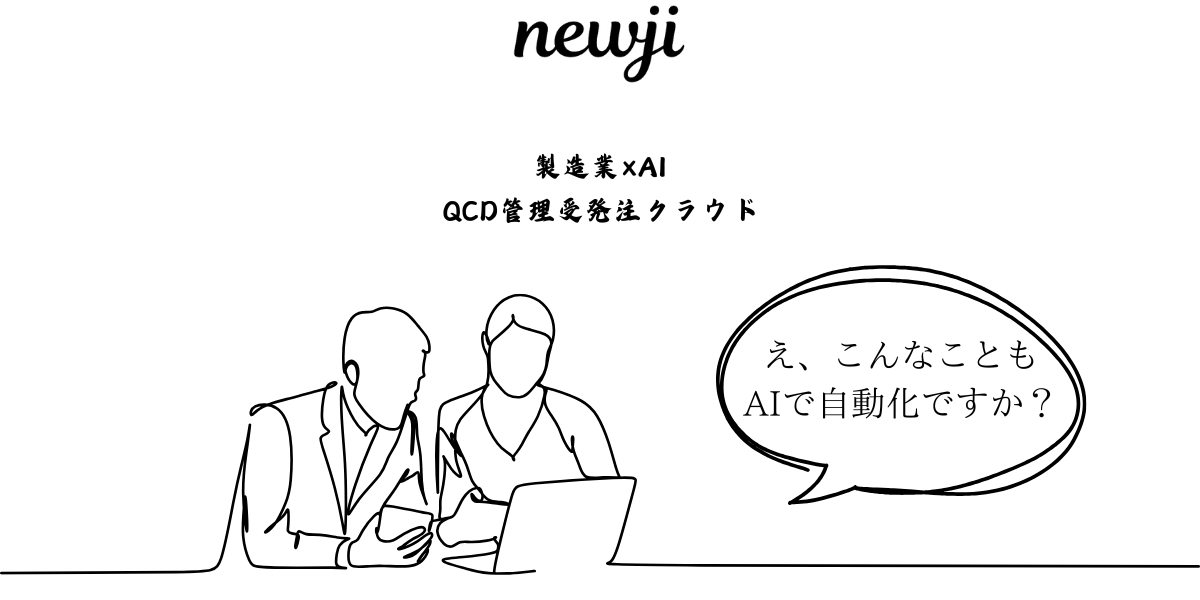
“Cost breakdown analysis” in the manufacturing industry: Basics and practices that purchasing departments should know
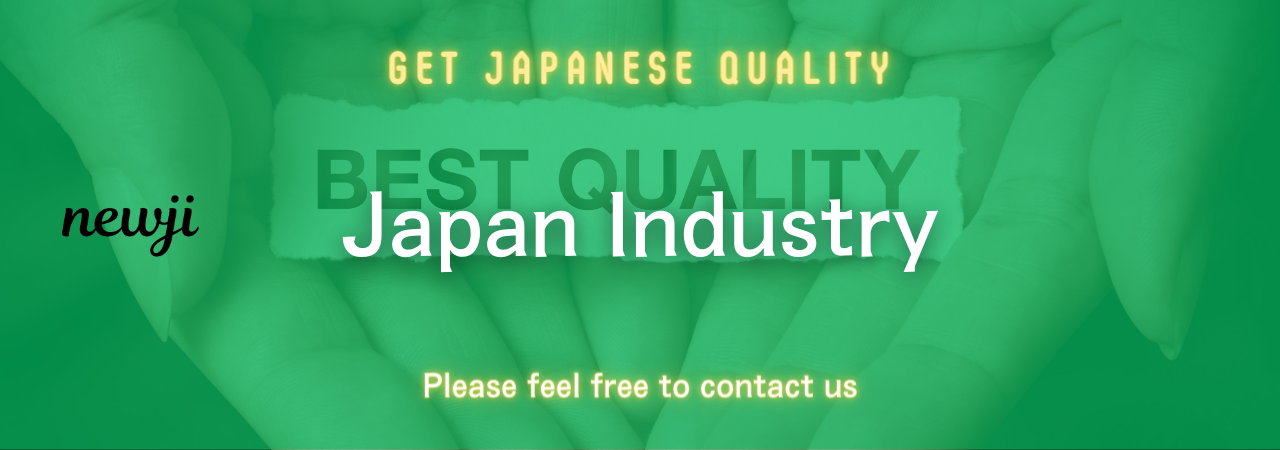
目次
Understanding Cost Breakdown Analysis
In the manufacturing industry, cost breakdown analysis plays a crucial role in ensuring profitability and operational efficiency.
For purchasing departments, the ability to analyze cost structures helps in making informed decisions about pricing, budgeting, and vendor selection.
This tool is essential for identifying various cost components associated with manufacturing a product, enabling businesses to target areas for cost reduction and optimization.
Cost breakdown analysis involves dissecting the entire price of a product or service into its individual cost elements.
These typically include direct materials, direct labor, overhead costs, and sometimes additional factors such as research, development, or marketing expenses.
By analyzing these detailed elements, companies can gain a deeper understanding of their expenses and how to manage them effectively.
Importance of Cost Breakdown Analysis
For purchasing departments, understanding the breakdown of costs is vital for several reasons.
Firstly, it allows them to negotiate better with suppliers by having a clear picture of what components contribute to the total cost.
With this information, they can discuss specific areas to achieve price reductions or negotiate better terms.
Secondly, cost breakdown analysis helps in identifying variances between estimated costs and actual spending.
This insight is vital for refining budgeting processes and improving cost control measures.
Analyzing discrepancies can highlight inefficiencies or unexpected changes in the cost structure that require attention.
Moreover, this analysis aids in the strategic decision-making process.
Knowing cost components and distribution patterns helps purchasing managers to decide whether to continue buying from existing suppliers or to switch to more cost-effective alternatives.
Components of Cost Breakdown Analysis
Direct Material Costs
Direct material costs are the raw materials that are consumed to manufacture a product.
These costs are often variable and can fluctuate based on factors such as market demand, supplier pricing, and production volume.
For purchasing departments, it’s critical to maintain a good relationship with suppliers to ensure consistent quality and pricing.
Sourcing raw materials at competitive prices plays a significant role in controlling overall manufacturing costs.
Direct Labor Costs
These costs are associated with employees who are directly involved in the production of goods.
Direct labor costs can include salaries, wages, benefits, and any other compensation paid to workers who are hands-on with product creation.
Purchasing departments need to consider labor costs when evaluating the cost-effectiveness of producing in-house versus outsourcing to third-party manufacturers.
Overhead Costs
Overhead costs refer to the indirect expenses incurred in the manufacturing process.
These can include utility bills, equipment depreciation, facilities maintenance, and administrative expenses.
Understanding overhead is essential for comprehending the full cost implications of production activities.
While harder to control than direct costs, efficient management of overhead can significantly impact profit margins.
Additional Costs
In some cases, other cost components may need to be considered.
These can include research and development expenses, marketing, packaging, and distribution costs.
These factors vary depending on industry-specific practices and product types, but incorporating them into the cost analysis provides a more comprehensive view.
Best Practices for Cost Breakdown Analysis in Purchasing
Effective Supplier Communication
Maintaining open lines of communication with suppliers is essential.
Engage in regular discussions to understand cost fluctuations and explore avenues for reducing expenses.
By collaborating directly with suppliers, purchasing departments can uncover opportunities for cost savings, such as bulk purchasing discounts or flexible payment terms.
Regular Cost Reviews
Performing regular cost reviews and comparisons against industry benchmarks helps in identifying inefficiencies and potential savings.
Tracking cost trends over time allows purchasing managers to make data-driven decisions and ensures that cost structures remain aligned with business strategies.
Utilizing Technology
Leverage technology solutions to streamline the cost analysis process.
Software tools can automate data collection, perform detailed analyses, and generate comprehensive reports, saving time and minimizing human errors.
Utilizing technology also enhances the visibility and accessibility of cost data across departments.
Vendor Evaluation and Selection
Cost breakdown analysis should be a key consideration in the vendor evaluation and selection process.
By understanding each vendor’s cost components, purchasing departments can choose suppliers who offer the best value while aligning with company standards and expectations.
Conclusion
In the manufacturing industry, cost breakdown analysis is an essential tool for purchasing departments aiming to optimize expenses and improve profitability.
By dissecting cost structures into their fundamental components, businesses can gain valuable insights into their cost drivers, negotiate better with suppliers, and make informed strategic decisions.
Understanding and implementing best practices in cost breakdown analysis will empower purchasing departments to effectively manage and control costs, ultimately contributing to a healthier bottom line.
資料ダウンロード
QCD調達購買管理クラウド「newji」は、調達購買部門で必要なQCD管理全てを備えた、現場特化型兼クラウド型の今世紀最高の購買管理システムとなります。
ユーザー登録
調達購買業務の効率化だけでなく、システムを導入することで、コスト削減や製品・資材のステータス可視化のほか、属人化していた購買情報の共有化による内部不正防止や統制にも役立ちます。
NEWJI DX
製造業に特化したデジタルトランスフォーメーション(DX)の実現を目指す請負開発型のコンサルティングサービスです。AI、iPaaS、および先端の技術を駆使して、製造プロセスの効率化、業務効率化、チームワーク強化、コスト削減、品質向上を実現します。このサービスは、製造業の課題を深く理解し、それに対する最適なデジタルソリューションを提供することで、企業が持続的な成長とイノベーションを達成できるようサポートします。
オンライン講座
製造業、主に購買・調達部門にお勤めの方々に向けた情報を配信しております。
新任の方やベテランの方、管理職を対象とした幅広いコンテンツをご用意しております。
お問い合わせ
コストダウンが利益に直結する術だと理解していても、なかなか前に進めることができない状況。そんな時は、newjiのコストダウン自動化機能で大きく利益貢献しよう!
(Β版非公開)