- お役立ち記事
- Cost optimization and quality improvement in manufacturing and production of high-performance glazes for clay pots
月間77,185名の
製造業ご担当者様が閲覧しています*
*2025年2月28日現在のGoogle Analyticsのデータより
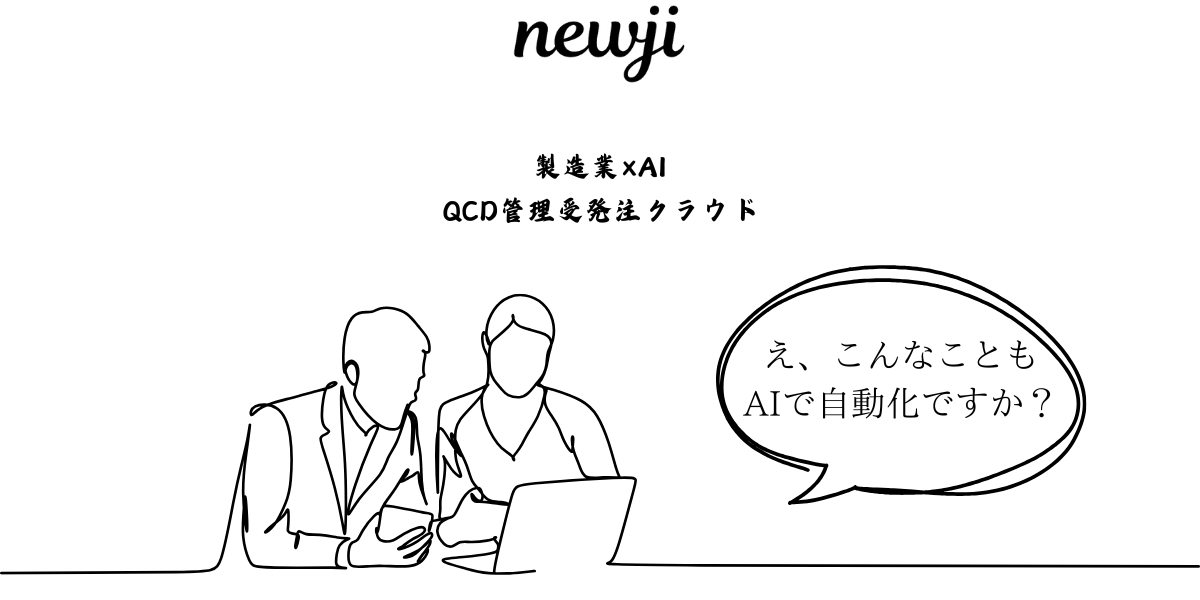
Cost optimization and quality improvement in manufacturing and production of high-performance glazes for clay pots
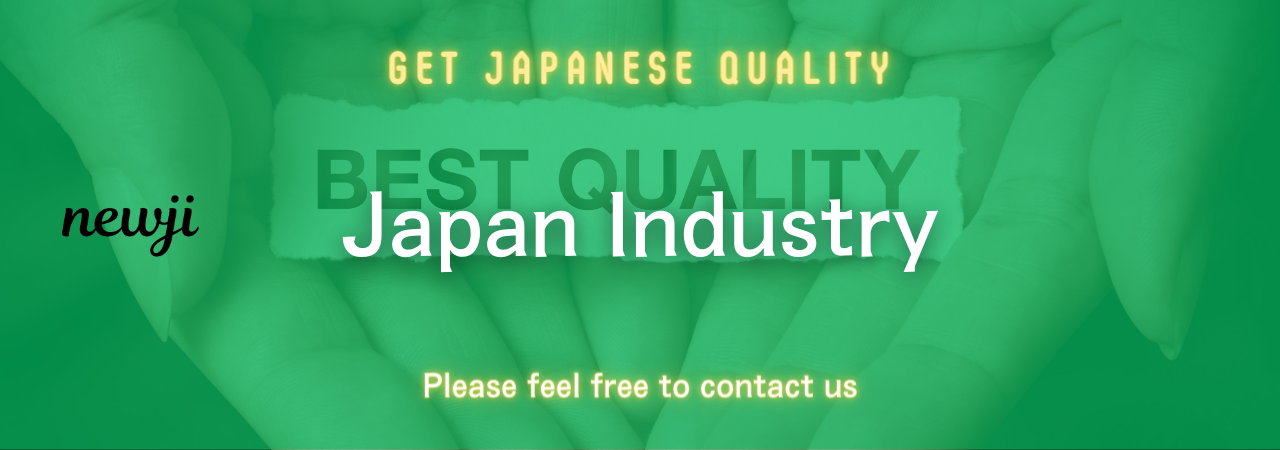
目次
Understanding High-Performance Glazes
High-performance glazes play a critical role in the manufacturing and production of clay pots, creating an appealing aesthetic and enhancing the durability of the product.
Glazes serve not only as a decorative element but also as a functional coating, providing a waterproof layer and sometimes even adding specific thermal or mechanical properties to the clay pot.
As a result, manufacturers are continuously working on optimizing these glazes to improve quality while keeping costs in check.
Factors Affecting the Cost of Glazes
The cost components of high-performance glazes primarily include raw materials, energy consumption, and production processes.
Raw materials are the first major cost factor.
They consist of minerals and additives like silica, alumina, and colorants, which are necessary to achieve the desired finish and properties of the glaze.
The cost of these materials can fluctuate based on availability and market demand, impacting the overall cost of glaze production.
Energy consumption is another significant component.
The kilns used for firing glazes require substantial energy input, often accounting for a considerable portion of the manufacturing costs.
Ensuring energy efficiency in kiln operations is crucial for reducing costs.
Finally, the production process itself entails labor and overhead costs, involving skilled technicians and advanced equipment.
Improving Quality through Innovative Techniques
Quality improvement in glazes can be achieved through research and development in materials science and formulation techniques.
One approach is to explore novel raw materials or synthetic alternatives that can mimic the desired properties of traditional minerals at a lower cost.
By experimenting with different mineral compositions, manufacturers can develop glazes that provide better adhesion, color uniformity, and increased resistance to wear and thermal stress.
Advanced techniques like computer simulations and process modeling can enhance the understanding of glaze behavior during application and firing.
These tools allow precise control over factors such as temperature cycles and cooling rates, significantly improving the quality and consistency of the glaze finish.
Adopting Sustainable Practices
Sustainability is a growing concern in the manufacturing sector, and glaze production is no exception.
Incorporating sustainable practices not only reduces environmental impact but also offers cost-saving opportunities.
This includes using recycled materials in glaze formulations, reducing waste through improved production processes, and minimizing energy consumption with efficient kiln technologies.
Additionally, water usage during glaze preparation and application can be optimized to reduce waste, thus lowering costs and conserving resources.
Implementing Cost Optimization Strategies
To address the cost challenges in high-performance glazes, manufacturers can leverage several strategies.
Sourcing raw materials from multiple suppliers can offer better price negotiations and ensure a steady supply, minimizing the risk of cost surges.
Collaborating with suppliers on joint research initiatives can lead to innovative materials that improve glaze performance and reduce costs.
Investing in energy-efficient kilns and optimizing firing schedules can significantly lower energy expenses.
Such investments, although initially costly, often lead to long-term savings and better quality production.
Furthermore, automating processes and employing advanced analytics can streamline operations, reduce labor costs, and increase throughput.
Balancing Quality and Cost
Striking the right balance between quality and cost involves continuous evaluation and refinement of practices across the production lifecycle.
Quality control measures, such as rigorous testing of raw materials and finished products, ensure that the standards are consistently met.
At the same time, identifying process inefficiencies and optimizing them where possible contributes to cost savings.
Fostering a culture of innovation within the organization encourages employees to contribute ideas for efficiency and quality improvements, offering a competitive edge in the marketplace.
The Future of High-Performance Glazes
The landscape of high-performance glazes for clay pots is rapidly evolving.
As technology advances and market demands shift towards more sustainable and cost-effective solutions, manufacturers are likely to see an increase in the adoption of smart technologies such as AI and IoT in glaze production.
These technologies promise to revolutionize the way glazes are developed and applied, offering higher precision, better product quality, and reduced costs.
Investing in research and development will be critical for manufacturers to stay ahead in this competitive field.
In conclusion, by understanding and addressing the factors affecting cost and quality in glaze production, manufacturers can achieve significant improvements in their processes.
Through the integration of new materials, sustainable practices, and innovative technologies, the industry can continue to thrive, creating beautiful, durable, and environmentally-friendly clay pots.
資料ダウンロード
QCD管理受発注クラウド「newji」は、受発注部門で必要なQCD管理全てを備えた、現場特化型兼クラウド型の今世紀最高の受発注管理システムとなります。
ユーザー登録
受発注業務の効率化だけでなく、システムを導入することで、コスト削減や製品・資材のステータス可視化のほか、属人化していた受発注情報の共有化による内部不正防止や統制にも役立ちます。
NEWJI DX
製造業に特化したデジタルトランスフォーメーション(DX)の実現を目指す請負開発型のコンサルティングサービスです。AI、iPaaS、および先端の技術を駆使して、製造プロセスの効率化、業務効率化、チームワーク強化、コスト削減、品質向上を実現します。このサービスは、製造業の課題を深く理解し、それに対する最適なデジタルソリューションを提供することで、企業が持続的な成長とイノベーションを達成できるようサポートします。
製造業ニュース解説
製造業、主に購買・調達部門にお勤めの方々に向けた情報を配信しております。
新任の方やベテランの方、管理職を対象とした幅広いコンテンツをご用意しております。
お問い合わせ
コストダウンが利益に直結する術だと理解していても、なかなか前に進めることができない状況。そんな時は、newjiのコストダウン自動化機能で大きく利益貢献しよう!
(β版非公開)