- お役立ち記事
- Cost planning and effective cost reduction at the design stage
月間77,185名の
製造業ご担当者様が閲覧しています*
*2025年2月28日現在のGoogle Analyticsのデータより
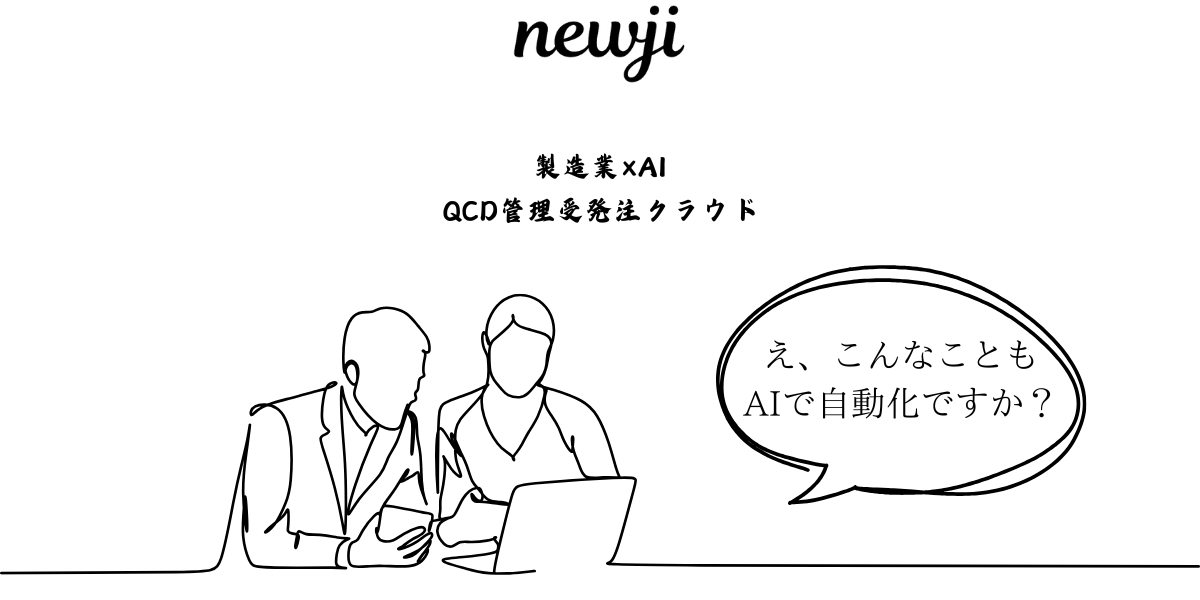
Cost planning and effective cost reduction at the design stage
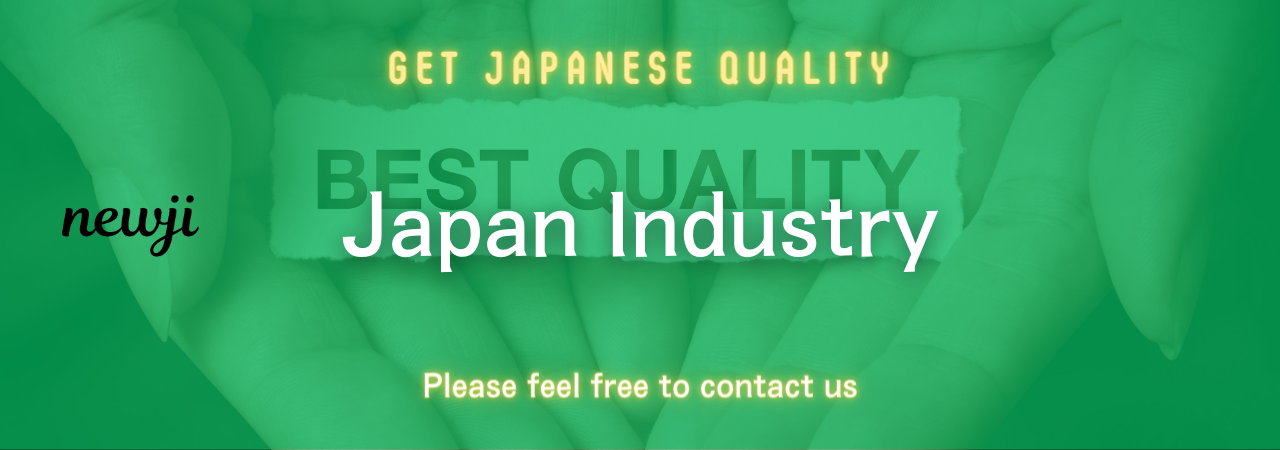
Cost planning and effective cost reduction are key components of successful project management, especially during the design stage. Proper planning at this crucial phase can result in significant savings, helping companies stay within budget and improve profitability. In this article, we will explore the principles of cost planning and effective techniques for reducing costs during the design stage of a project.
目次
Understanding Cost Planning at the Design Stage
Cost planning involves estimating the total costs associated with a project, from its inception to completion. It aims to provide a framework for managing expenses and ensuring that they do not exceed predefined budgets. During the design stage, cost planning is critical because it sets the foundation for all subsequent phases of the project.
Project managers start by identifying all potential costs, including labor, materials, equipment, and overheads. By thoroughly assessing each of these cost elements, managers can create a detailed budget. This helps in making informed decisions about project design, resource allocation, and scheduling.
Importance of Accurate Cost Estimation
Accurate cost estimation is the cornerstone of effective cost planning. It allows businesses to forecast expenditure, prepare for financial risks, and allocate resources efficiently. During the design stage, estimations should be as precise as possible to prevent unnecessary financial strain later on.
Cost estimation typically involves historical data analysis, market research, and consultation with industry experts. When estimates are grounded in reality, project teams can anticipate potential challenges and deviations, allowing for timely interventions.
Strategies for Effective Cost Reduction at the Design Stage
Reducing costs during the design stage can significantly impact the financial viability of a project. By considering cost reduction early on, businesses can avoid costly alterations and errors during implementation.
1. Value Engineering
Value engineering involves analyzing the functions of project components and materials to find cost-effective alternatives. By reevaluating design specifications, teams can identify less expensive options without compromising on quality or performance.
This process encourages creative thinking and innovation, pushing teams to optimize resources and achieve value for money. Regular value engineering assessments can prevent over-engineering and ensure that all project elements serve a necessary purpose.
2. Collaborative Design Process
Collaboration among different stakeholders, including designers, engineers, and procurement specialists, can lead to cost reductions. By working together during the design stage, teams can identify and address potential issues early, avoiding costly redesigns later on.
Open communication helps align goals, enhances decision-making, and ensures that cost-saving opportunities are maximized. Teams are encouraged to share insights and expertise, leading to more efficient designs and resource use.
3. Detailed Life-Cycle Cost Analysis
Considering the life-cycle costs of a project can lead to more informed design choices. A life-cycle cost analysis examines the total cost of ownership, including initial construction, operation, maintenance, and eventual disposal.
Prioritizing designs that reduce long-term operational and maintenance expenses can result in significant savings. Using energy-efficient technologies, durable materials, and maintainable designs contributes to both immediate and future cost reductions.
Leveraging Technology for Cost Reduction
Modern technology offers numerous tools that enhance cost reduction efforts during the design stage. Digital modeling and simulation, for example, enable designers to test different variables and scenarios without incurring physical costs.
Building Information Modeling (BIM)
Building Information Modeling (BIM) is a digital representation of a building’s characteristics, utilized across various project stages. BIM facilitates better visualization, enhanced collaboration among stakeholders, and more accurate predictions of costs and timelines.
By simulating construction processes and exploring design alternatives in a virtual environment, teams can identify opportunities to streamline operations and reduce waste. BIM also minimizes the risk of errors, ensuring efficiency and cost coherence from the outset.
Innovative Materials and Techniques
Exploring new materials and construction techniques can contribute to cost reductions. Materials such as prefabricated components or 3D-printed elements can reduce labor costs and accelerate project timelines.
Staying informed about technological advancements and market trends allows project teams to adopt innovative solutions that can enhance overall efficiency and cut costs.
Risk Management and Its Cost Implications
Effective cost reduction at the design stage also requires thorough risk management. Understanding potential risks allows for proactive measures that prevent significant cost overruns.
Project teams are tasked with identifying, analyzing, and addressing risks that might affect both the design and financial aspects of a project. By establishing contingency plans and buffer allowances, teams can mitigate adverse impacts and ensure uninterrupted progress.
Allocating Contingency Reserves
Having contingency reserves within the budget provides a financial safety net for unexpected expenses. These reserves are calculated based on assessed risks and serve as a buffer to accommodate unforeseen changes.
This strategy helps maintain budget discipline, ensuring that unplanned costs do not derail the project. By carefully managing reserves, teams can confidently address challenges without impacting overall financial stability.
Conclusion
Cost planning and effective cost reduction at the design stage are essential for successful project management. By implementing thorough cost estimation, engaging in collaborative processes, leveraging technology, and managing risks, project teams can achieve significant savings.
Focusing on these strategies ensures value for the client while keeping projects financially viable. With careful planning and informed decision-making, businesses can navigate the complexities of the design stage and seize opportunities for optimization throughout the project lifecycle.
資料ダウンロード
QCD管理受発注クラウド「newji」は、受発注部門で必要なQCD管理全てを備えた、現場特化型兼クラウド型の今世紀最高の受発注管理システムとなります。
ユーザー登録
受発注業務の効率化だけでなく、システムを導入することで、コスト削減や製品・資材のステータス可視化のほか、属人化していた受発注情報の共有化による内部不正防止や統制にも役立ちます。
NEWJI DX
製造業に特化したデジタルトランスフォーメーション(DX)の実現を目指す請負開発型のコンサルティングサービスです。AI、iPaaS、および先端の技術を駆使して、製造プロセスの効率化、業務効率化、チームワーク強化、コスト削減、品質向上を実現します。このサービスは、製造業の課題を深く理解し、それに対する最適なデジタルソリューションを提供することで、企業が持続的な成長とイノベーションを達成できるようサポートします。
製造業ニュース解説
製造業、主に購買・調達部門にお勤めの方々に向けた情報を配信しております。
新任の方やベテランの方、管理職を対象とした幅広いコンテンツをご用意しております。
お問い合わせ
コストダウンが利益に直結する術だと理解していても、なかなか前に進めることができない状況。そんな時は、newjiのコストダウン自動化機能で大きく利益貢献しよう!
(β版非公開)