- お役立ち記事
- Cost Reduction Through Digitalization: New Manufacturing Norms
Cost Reduction Through Digitalization: New Manufacturing Norms
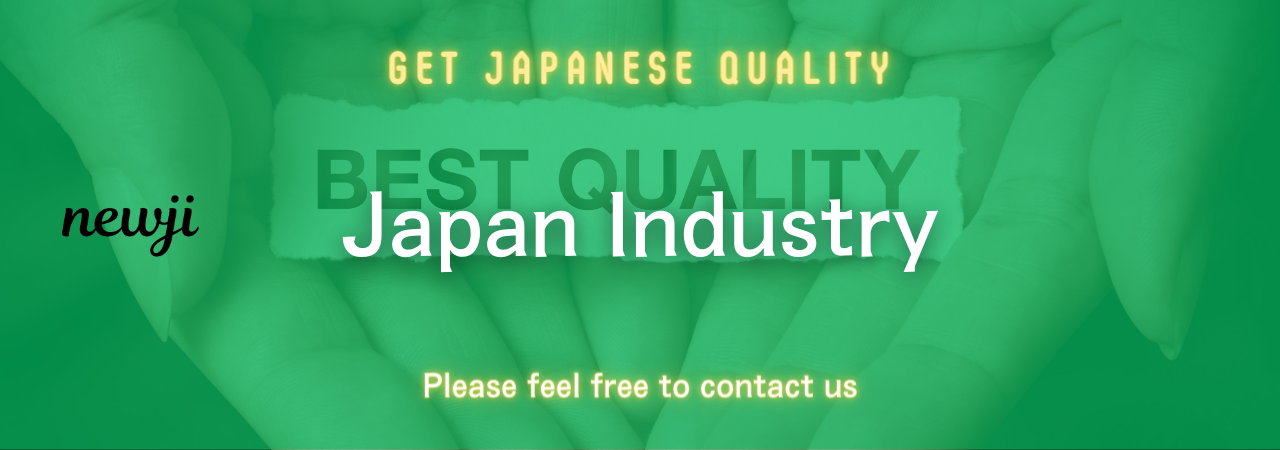
In today’s rapidly changing manufacturing landscape, digitalization has emerged as a game-changer.
Many industries are now embracing this shift to stay competitive and reduce operational costs.
By adopting advanced technologies, manufacturers can streamline processes, improve efficiency, and maintain high-quality output.
目次
Why Digitalization Matters
Digitalization refers to the use of digital technologies to transform traditional manufacturing processes.
This includes the adoption of tools such as automation, data analytics, and the Internet of Things (IoT).
The primary goal is to enhance productivity and reduce costs.
Improved Efficiency
One of the most significant benefits of digitalizing manufacturing processes is improved efficiency.
Automation and data analytics play a crucial role in minimizing errors and speeding up production.
Machines can work continuously without the need for breaks, drastically reducing downtime.
Reduced Waste
Digital tools help in monitoring every step of the production process.
This ensures that resources are used optimally, thereby reducing waste.
Predictive maintenance, for example, can identify potential issues before they become significant problems.
This preemptive approach helps in avoiding costly repairs and halts in production.
Cost Reduction Strategies Through Digitalization
Now, let’s dive into the specific strategies manufacturers can employ to cut costs through digitalization.
Automation
Automation involves using machines and software to perform tasks that were previously done manually.
This not only speeds up production but also improves accuracy.
Tasks such as assembly, packaging, and quality control can be automated, freeing up human resources for more complex tasks.
Predictive Maintenance
Traditional maintenance methods often involve regular inspections and fixed schedules.
However, digitalization enables predictive maintenance, which relies on real-time data to identify the exact moments when maintenance is needed.
This reduces unnecessary downtime and extends the life of equipment.
Supply Chain Optimization
A digital supply chain leverages technologies like AI and IoT for real-time tracking and analytics.
Manufacturers can optimize inventory levels, forecast demand more accurately, and reduce lead times.
This results in lower storage costs and better resource allocation.
The Role of Data Analytics
Data is the backbone of the digital transformation in manufacturing.
Collecting, analyzing, and interpreting data helps manufacturers make informed decisions.
Enhanced Decision-Making
Data analytics provides insights that are crucial for decision-making.
By analyzing data from various sources, manufacturers can identify trends, track performance, and pinpoint areas that need improvement.
This leads to better strategic planning and resource management.
Quality Control
Digital tools can monitor the production process in real time, ensuring that products meet quality standards.
Any deviations can be quickly identified and corrected, reducing the chances of defective products reaching the market.
This not only saves costs but also enhances customer satisfaction.
Challenges in Digitalization
While the benefits of digitalization are numerous, it is essential to be aware of the challenges involved.
Initial Investment
The initial cost of implementing digital technologies can be high.
However, it is crucial to view this as a long-term investment.
The cost savings and efficiency improvements that follow often justify the upfront expenditure.
Training and Skill Development
The workforce must be trained to operate new digital tools effectively.
Investing in skill development programs is essential to ensure a smooth transition.
This also helps in maximizing the benefits of digitalization.
Data Security
With digitalization comes the challenge of ensuring data security.
Manufacturers must implement robust cybersecurity measures to protect sensitive information from breaches and cyberattacks.
Real-World Examples
Here are some real-world examples of how companies are leveraging digitalization to reduce costs:
General Electric (GE)
GE has implemented digital twin technology across its manufacturing plants.
A digital twin is a virtual replica of physical assets, processes, or systems, allowing GE to simulate scenarios and optimize operations.
This has led to significant cost reductions and enhanced operational efficiency.
Siemens
Siemens has integrated IoT and AI across its supply chain.
This digital transformation has enabled continuous monitoring and real-time decision-making.
The result is a more agile and cost-effective supply chain.
Conclusion
Digitalization is no longer an option but a necessity for manufacturers aiming to stay competitive and reduce costs.
By embracing technologies such as automation, data analytics, and IoT, manufacturers can achieve significant efficiency improvements and cost savings.
While the initial investment and challenges may seem daunting, the long-term benefits make digitalization a worthwhile endeavor.
資料ダウンロード
QCD調達購買管理クラウド「newji」は、調達購買部門で必要なQCD管理全てを備えた、現場特化型兼クラウド型の今世紀最高の購買管理システムとなります。
ユーザー登録
調達購買業務の効率化だけでなく、システムを導入することで、コスト削減や製品・資材のステータス可視化のほか、属人化していた購買情報の共有化による内部不正防止や統制にも役立ちます。
NEWJI DX
製造業に特化したデジタルトランスフォーメーション(DX)の実現を目指す請負開発型のコンサルティングサービスです。AI、iPaaS、および先端の技術を駆使して、製造プロセスの効率化、業務効率化、チームワーク強化、コスト削減、品質向上を実現します。このサービスは、製造業の課題を深く理解し、それに対する最適なデジタルソリューションを提供することで、企業が持続的な成長とイノベーションを達成できるようサポートします。
オンライン講座
製造業、主に購買・調達部門にお勤めの方々に向けた情報を配信しております。
新任の方やベテランの方、管理職を対象とした幅広いコンテンツをご用意しております。
お問い合わせ
コストダウンが利益に直結する術だと理解していても、なかなか前に進めることができない状況。そんな時は、newjiのコストダウン自動化機能で大きく利益貢献しよう!
(Β版非公開)