- お役立ち記事
- Countermeasures against quality problems in the inspection process and problem solving methods
Countermeasures against quality problems in the inspection process and problem solving methods
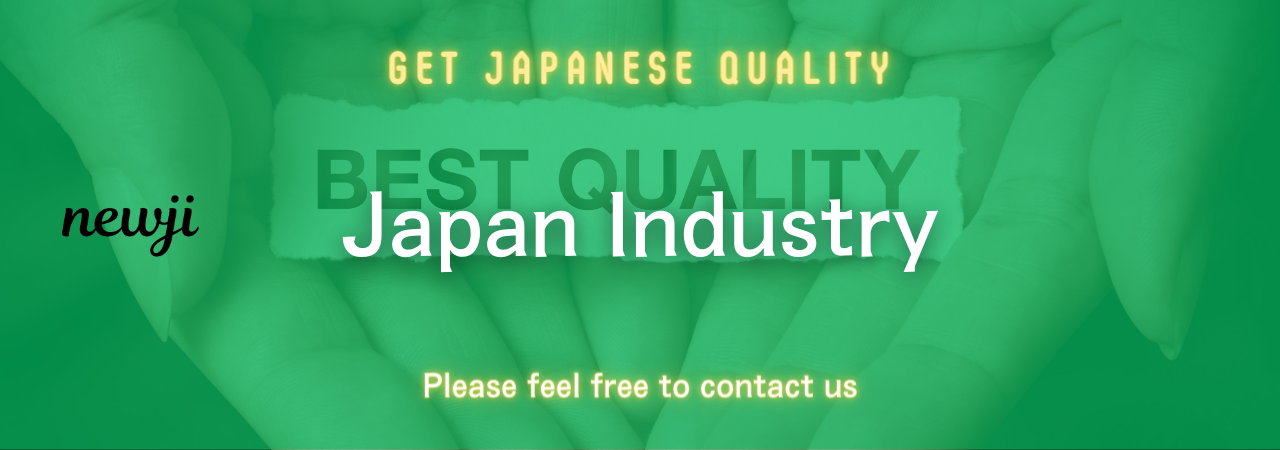
目次
Understanding Quality Problems in Inspection
Maintaining quality is a key factor for any industry as it directly impacts customer satisfaction and business success.
Quality problems in the inspection process can inevitably arise, posing challenges for companies aiming to deliver the best products or services.
These issues can stem from various sources such as human error, equipment malfunction, or inadequate inspection protocols, making it essential to identify and address them promptly.
Despite rigorous quality control measures, flaws in the inspection process can lead to defective products entering the market, resulting in costly recalls or damage to brand reputation.
By taking proactive measures to detect and eliminate quality issues, businesses can enhance productivity and reduce losses while ensuring customer trust.
Common Quality Inspection Issues
Quality inspection issues can manifest in different ways, and understanding these problems is critical in developing effective countermeasures.
Some of the common inspection issues include:
Inconsistent Inspection Standards
One common issue is the lack of uniform inspection standards.
Inconsistencies arise when inspection protocols vary across different teams or facilities, leading to disparate results.
Without clear guidelines and standardized practices, maintaining quality and consistency across products becomes challenging.
Human Error
Human error is a frequent occurrence in the inspection process, particularly when manual methods are employed.
Errors such as oversight or misinterpretation of inspection criteria can lead to incorrect assessments and faulty products slipping through the cracks.
Equipment Malfunction
Inspection relies heavily on equipment and technology.
Malfunctions or outdated inspection tools can provide inaccurate results, thus affecting overall product quality.
Regular maintenance and upgrading of inspection equipment are necessary to prevent such issues.
Inadequate Training
A lack of adequate training for inspection personnel can also lead to quality problems.
If inspectors are not well-versed in quality standards or inspection techniques, they may fail to detect defects accurately, which can result in subpar outputs.
Effective Countermeasures for Quality Problems
Addressing quality problems in the inspection process requires a multifaceted approach, focusing on prevention, detection, and correction of issues.
Here are some effective countermeasures to consider:
Standardizing Inspection Processes
Developing and implementing standardized inspection procedures is essential in minimizing inconsistencies.
These procedures should be documented and accessible to all relevant personnel, ensuring everyone is on the same page during inspections.
Moreover, regular audits should be conducted to ensure compliance with these standards.
Investing in Automation
Leveraging automation technologies can significantly reduce the risk of human error and enhance the accuracy of inspections.
Automated systems can consistently apply predefined criteria, allowing for more reliable and efficient inspections.
While initial investment in automation may be high, the long-term benefits in terms of quality assurance and cost savings are substantial.
Regular Equipment Maintenance
To mitigate the risk of equipment-related errors, regular maintenance and calibration of inspection tools are imperative.
Organizations should establish a maintenance schedule that includes routine checks and servicing to keep equipment functioning optimally.
Enhancing Training Programs
Providing comprehensive training programs for inspection personnel is vital to improving inspection quality.
Training should cover not only inspection techniques but also methods for troubleshooting common issues and staying updated with industry standards.
Continual professional development should be encouraged to ensure inspectors are equipped with the latest skills and knowledge.
Implementing Feedback Mechanisms
Creating feedback mechanisms allows inspection teams to share insights and learnings, fostering an environment of continuous improvement.
Conducting regular reviews and discussions about inspection outcomes can identify recurring issues and opportunities for enhancements.
Problem Solving Methods for Inspection Quality
Once problems are identified, implementing effective problem-solving methods is crucial to address the root causes and prevent recurrence.
Here are some approaches to consider:
Root Cause Analysis
Identifying the root cause of quality problems is essential for developing targeted solutions.
Root cause analysis (RCA) involves systematically investigating the issue to pinpoint the underlying cause, allowing teams to address it directly rather than treating symptoms.
Utilizing Statistical Process Control
Statistical process control (SPC) uses statistical methods to monitor and control inspection processes.
By analyzing data and identifying variations, SPC can help in understanding process behavior and making informed decisions to improve quality.
Applying Corrective Action and Preventive Action (CAPA)
CAPA processes involve identifying, documenting, and resolving issues, as well as implementing preventive measures to avoid future occurrences.
Effective CAPA involves collaborative efforts among different departments, ensuring that corrective actions are comprehensive and sustainable.
Encouraging a Quality-Focused Culture
Fostering a culture that emphasizes quality is crucial in instilling a sense of responsibility and accountability among team members.
Regularly communicating the importance of quality and recognizing the contributions of those who enhance it can motivate others to follow suit.
Incorporating these countermeasures and problem-solving methods can significantly improve the quality of inspection processes, ensuring consistent delivery of top-notch products or services.
Ultimately, businesses that prioritize quality not only meet customer expectations but also gain a competitive edge in the market.
資料ダウンロード
QCD調達購買管理クラウド「newji」は、調達購買部門で必要なQCD管理全てを備えた、現場特化型兼クラウド型の今世紀最高の購買管理システムとなります。
ユーザー登録
調達購買業務の効率化だけでなく、システムを導入することで、コスト削減や製品・資材のステータス可視化のほか、属人化していた購買情報の共有化による内部不正防止や統制にも役立ちます。
NEWJI DX
製造業に特化したデジタルトランスフォーメーション(DX)の実現を目指す請負開発型のコンサルティングサービスです。AI、iPaaS、および先端の技術を駆使して、製造プロセスの効率化、業務効率化、チームワーク強化、コスト削減、品質向上を実現します。このサービスは、製造業の課題を深く理解し、それに対する最適なデジタルソリューションを提供することで、企業が持続的な成長とイノベーションを達成できるようサポートします。
オンライン講座
製造業、主に購買・調達部門にお勤めの方々に向けた情報を配信しております。
新任の方やベテランの方、管理職を対象とした幅広いコンテンツをご用意しております。
お問い合わせ
コストダウンが利益に直結する術だと理解していても、なかなか前に進めることができない状況。そんな時は、newjiのコストダウン自動化機能で大きく利益貢献しよう!
(Β版非公開)