- お役立ち記事
- Countermeasures for supply chain disruption faced by purchasing departments in the manufacturing industry
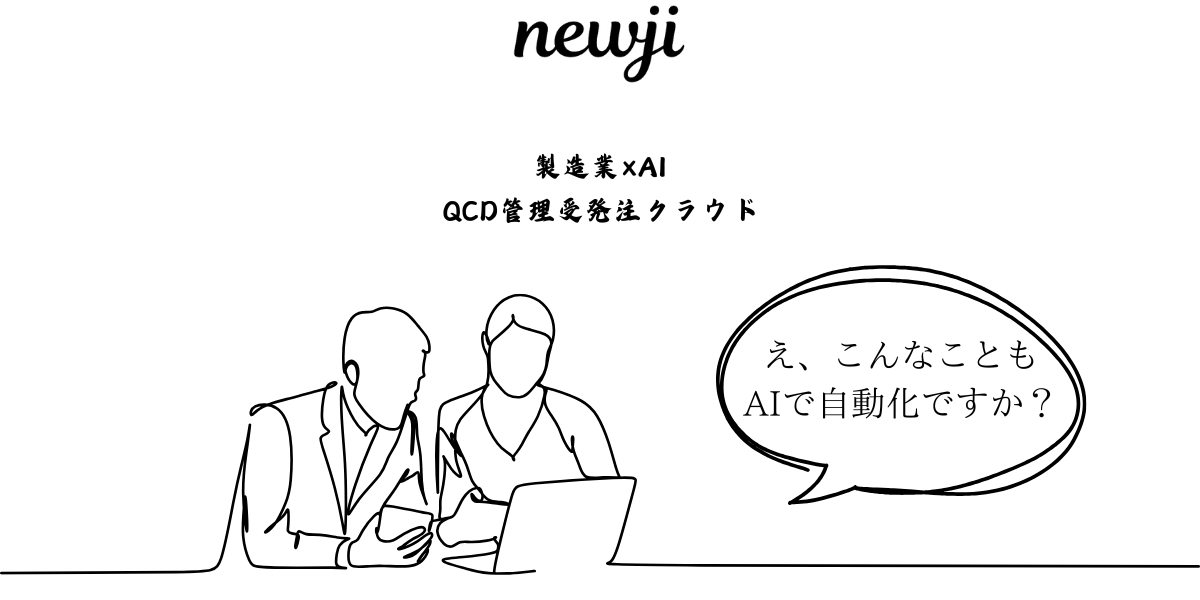
Countermeasures for supply chain disruption faced by purchasing departments in the manufacturing industry
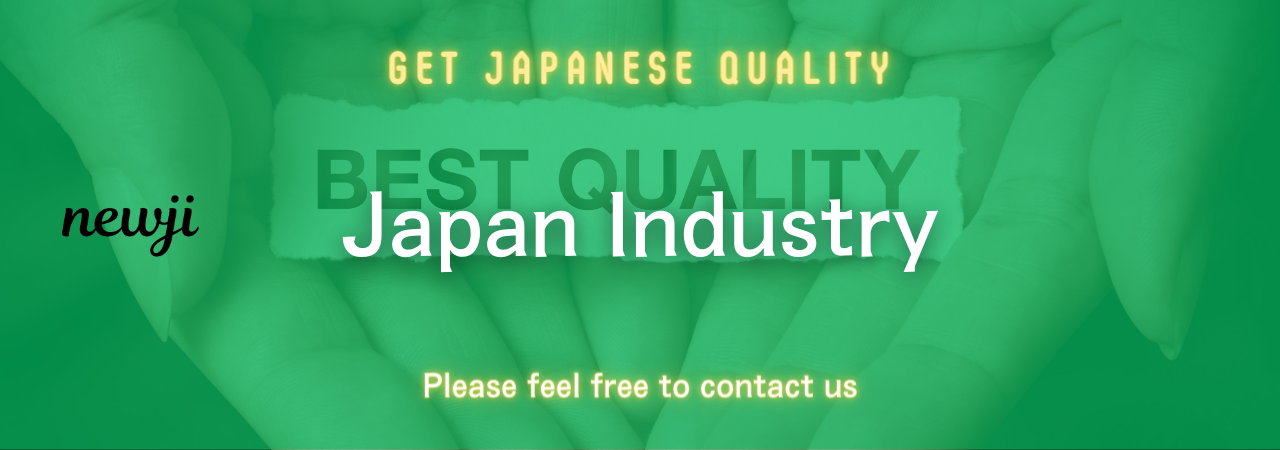
目次
Understanding Supply Chain Disruptions
Supply chain disruptions can occur for various reasons, from natural disasters and geopolitical tensions to sudden surges in demand and pandemics.
For the manufacturing industry, any disruption can lead to delays, increased costs, and even a halt in production.
To navigate these challenges, purchasing departments must employ effective countermeasures to maintain the smooth functioning of the supply chain.
Identifying Key Vulnerabilities
The first step in countering supply chain disruption is identifying vulnerabilities within the supply chain.
A detailed analysis of all components, from raw materials to finished products, helps in pinpointing potential weaknesses.
This may include suppliers that are reliant on geographically risk-prone areas or specialized components that have a limited number of suppliers.
By recognizing these weak points, purchasing departments can create strategies that mitigate risk, such as diversifying suppliers or increasing inventory levels for critical components.
Building Strong Supplier Relationships
Another essential countermeasure is establishing robust relationships with suppliers.
A collaborative and transparent relationship allows for better communication, quicker response times, and more flexibility during disruptions.
By regularly engaging with suppliers, purchasing departments can gain insights into potential issues before they become critical.
Additionally, forming partnerships can lead to favorable terms and priority treatment during widespread disruptions.
Diversifying the Supplier Base
Relying on a single supplier or a limited number of suppliers for crucial components can be risky.
Diversification is key to reducing this risk.
Purchasing departments should consider working with multiple suppliers from different geographical locations.
This not only lessens the impact of regional disruptions but also fosters competitive pricing.
Furthermore, having alternate suppliers ready ensures continuity should a primary supplier face unexpected challenges.
Implementing Technology Solutions
Technology plays a pivotal role in managing supply chain disruptions.
Implementing advanced systems like AI-driven supply chain management software can provide real-time insights into potential disruptions.
These systems can help forecast demand, optimize inventory levels, and manage supplier performance.
Additionally, IoT devices and blockchain technology can offer increased transparency, traceability, and accountability within the supply chain.
Enhancing Inventory Management
Effective inventory management can serve as a buffer during supply chain disruptions.
Maintaining optimal stock levels for critical components ensures that production can continue even if supply is temporarily affected.
Purchasing departments should analyze demand patterns to manage lead times and safety stock levels effectively.
This approach requires a balance between minimizing holding costs and ensuring enough stock to weather disruption periods.
Developing a Contingency Plan
Every purchasing department should have a contingency plan in place for potential disruptions.
Such a plan details specific actions to take during different disruption scenarios, ensuring quick and decisive responses.
Regularly reviewing and updating the plan based on new risks or changes in the supply chain landscape is essential.
This preparation enables the department to respond promptly and reduce the disruption’s impact.
Focusing on Demand Planning
Accurate demand forecasting can significantly reduce the effects of supply chain disruptions.
Purchasing departments must leverage historical data, market trends, and predictive analytics to anticipate changes in demand.
This forecasting allows for better alignment of supply chain activities with customer expectations and drives more effective inventory management.
Aligning production schedules with supplier capabilities based on demand forecasts can also prevent over-stocking or under-stocking scenarios.
Building Resilience through Training
Training staff within the purchasing department is critical to building a resilient supply chain.
Personnel should be well-versed in risk management, negotiation with suppliers, and the use of technological tools.
Regular training sessions can improve decision-making skills and ensure that staff are prepared for unexpected supply chain challenges.
In addition, cross-functional training can ensure that teams can support each other and maintain operations even when faced with disruptions.
Utilizing Financial Hedging
Financial hedging is a useful strategy to manage the cost impact of supply chain disruptions.
Purchasing departments can explore options like forward contracts, futures, and options to mitigate price volatility for key materials.
These financial instruments can provide predictability and stability in pricing, helping companies stay competitive even during unforeseen disruptions in the supply chain.
Conclusion
Countering supply chain disruptions requires a proactive approach that encompasses a blend of strategic sourcing, technology integration, and effective risk management.
Purchasing departments in the manufacturing industry play a crucial role in maintaining a resilient supply chain.
By understanding vulnerabilities, fostering supplier relationships, and employing diverse strategies, these departments can better navigate disruptions and ensure the continuity of operations.
Staying adaptable and prepared is essential to overcoming the challenges posed by an ever-evolving global landscape.
資料ダウンロード
QCD調達購買管理クラウド「newji」は、調達購買部門で必要なQCD管理全てを備えた、現場特化型兼クラウド型の今世紀最高の購買管理システムとなります。
ユーザー登録
調達購買業務の効率化だけでなく、システムを導入することで、コスト削減や製品・資材のステータス可視化のほか、属人化していた購買情報の共有化による内部不正防止や統制にも役立ちます。
NEWJI DX
製造業に特化したデジタルトランスフォーメーション(DX)の実現を目指す請負開発型のコンサルティングサービスです。AI、iPaaS、および先端の技術を駆使して、製造プロセスの効率化、業務効率化、チームワーク強化、コスト削減、品質向上を実現します。このサービスは、製造業の課題を深く理解し、それに対する最適なデジタルソリューションを提供することで、企業が持続的な成長とイノベーションを達成できるようサポートします。
オンライン講座
製造業、主に購買・調達部門にお勤めの方々に向けた情報を配信しております。
新任の方やベテランの方、管理職を対象とした幅広いコンテンツをご用意しております。
お問い合わせ
コストダウンが利益に直結する術だと理解していても、なかなか前に進めることができない状況。そんな時は、newjiのコストダウン自動化機能で大きく利益貢献しよう!
(Β版非公開)