- お役立ち記事
- Crack detection and residual stress evaluation
月間77,185名の
製造業ご担当者様が閲覧しています*
*2025年2月28日現在のGoogle Analyticsのデータより
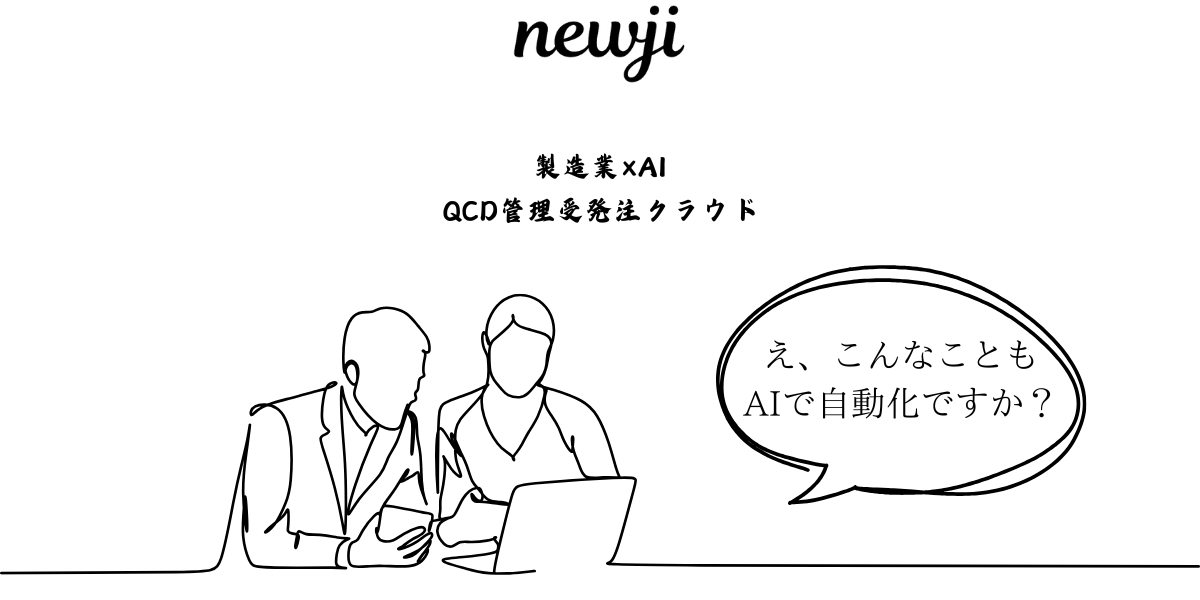
Crack detection and residual stress evaluation
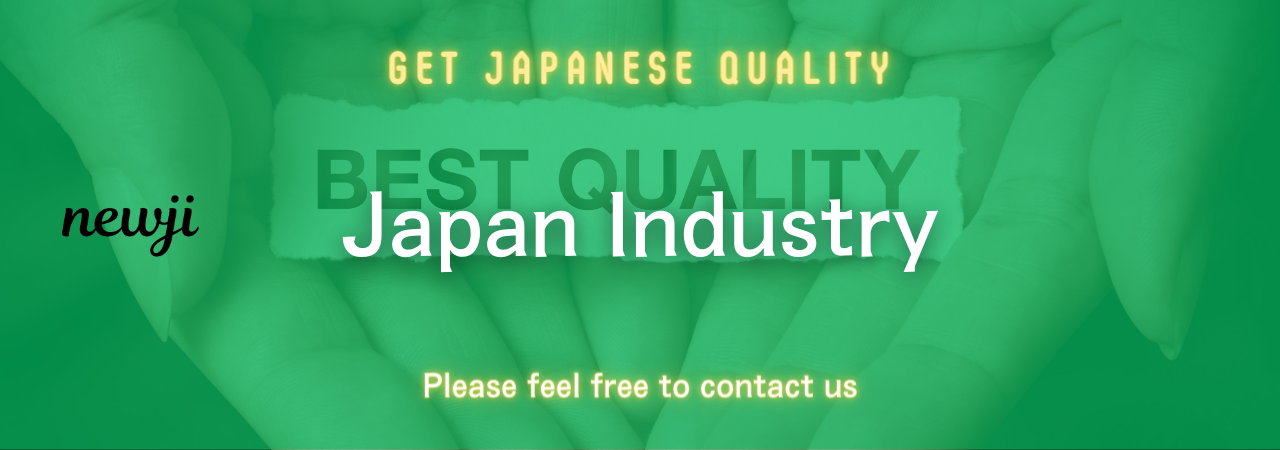
目次
Understanding Crack Detection
Crack detection is a crucial process in maintaining the structural integrity of various materials and infrastructures.
From bridges and buildings to smaller components used in machinery, identifying cracks early can prevent potential failures and ensure safety.
Understanding how crack detection works allows industries to avert disasters by identifying areas that require repair or reinforcement.
There are several methods for detecting cracks in materials, each with its own advantages and limitations.
Visual inspection is the most basic form of crack detection.
It involves a trained inspector examining the surface of a structure to look for visible signs of cracking.
However, this method can be limited by the inspector’s ability to access all areas of the material and may not be effective for detecting cracks that are not visible to the naked eye.
To overcome these limitations, technological advancements have introduced more sophisticated methods for crack detection.
Non-destructive testing (NDT) techniques, such as ultrasonic testing, magnetic particle inspection, and dye penetrant testing, play a crucial role.
Ultrasonic testing uses sound waves to detect irregularities within a material, which can indicate the presence of a crack.
Magnetic particle inspection involves applying magnetic particles to a material and observing how they accumulate to reveal crack patterns.
Dye penetrant testing uses a liquid dye that seeps into surface-breaking cracks, allowing inspectors to see the cracks after the excess dye is removed.
The Importance of Early Detection
Early crack detection is vital to maintaining the safety and longevity of structures.
Small cracks can worsen over time due to exposure to elements, mechanical stress, or environmental factors, leading to significant structural issues.
By catching these cracks early, repairs can be made before they develop into larger problems that could compromise the entire structure.
Early detection also contributes to cost savings.
Repairing a small crack is generally less expensive than addressing a major structural failure.
Moreover, timely interventions can extend the lifespan of materials and minimize downtime in operations, whether it’s a production line or public infrastructure like roads and bridges.
What is Residual Stress?
Residual stress refers to the stress present in a material after the original cause of stress has been removed.
This can result from various processes such as welding, casting, or machining.
Residual stresses are locked into the material and can affect its mechanical properties and performance throughout its lifecycle.
Residual stresses can be beneficial or detrimental.
In some cases, intentional induction of residual stress can increase material strength.
However, detrimental residual stress can lead to warping, cracking, or other unwanted deformations.
Understanding and managing residual stress is crucial to ensuring that materials perform optimally over time.
Evaluating Residual Stress
Residual stress evaluation is critical for assessing the quality and durability of materials.
Several techniques can be used to measure these stresses, with varying degrees of complexity and accuracy.
The most common methods include X-ray diffraction, neutron diffraction, and the hole-drilling method.
X-ray diffraction is a non-destructive technique that measures strain on the atomic level, allowing the calculation of residual stress.
It is useful for thin sections and surface layers.
Neutron diffraction penetrates deeper into the material and provides comprehensive measurements.
This method is particularly useful for thicker materials and provides valuable data on stresses deep within an object.
The hole-drilling method involves drilling a small hole into the material and measuring the deformation around the hole.
It is a semi-destructive method but provides detailed information about surface and subsurface stresses.
The Role of Residual Stress in Crack Formation
Residual stress can significantly influence crack formation and propagation.
In regions where tensile residual stress exists, cracks are more likely to form and grow.
The stress concentration at crack tips drives the propagation of these cracks under load or environmental factors.
Conversely, compressive residual stresses can help to arrest crack growth.
By evaluating residual stresses, engineers can understand how a material might behave under different conditions, predict potential failure points, and implement strategies to mitigate risks.
This might include altering the manufacturing process to reduce detrimental stresses or conducting regular inspections to ensure safety.
Combining Crack Detection and Residual Stress Evaluation
Integrating crack detection with residual stress evaluation provides a comprehensive approach to material assessment.
This combination allows for a more thorough understanding of the material’s condition and helps to identify potential areas of concern before they become critical.
By leveraging both techniques, industries can better predict material behavior, optimize maintenance schedules, reduce downtime, and improve overall safety.
With technological advancements, methodologies are becoming more precise, paving the way for more effective management of structural health.
In conclusion, understanding and evaluating cracks and residual stress are key components in preserving the integrity of structures and materials.
Early detection and assessment can prevent significant issues, safeguard investments, and, most importantly, ensure safety.
As technology continues to evolve, so too will the methods and tools used, leading to further enhancements in how we assess and manage material health.
資料ダウンロード
QCD管理受発注クラウド「newji」は、受発注部門で必要なQCD管理全てを備えた、現場特化型兼クラウド型の今世紀最高の受発注管理システムとなります。
ユーザー登録
受発注業務の効率化だけでなく、システムを導入することで、コスト削減や製品・資材のステータス可視化のほか、属人化していた受発注情報の共有化による内部不正防止や統制にも役立ちます。
NEWJI DX
製造業に特化したデジタルトランスフォーメーション(DX)の実現を目指す請負開発型のコンサルティングサービスです。AI、iPaaS、および先端の技術を駆使して、製造プロセスの効率化、業務効率化、チームワーク強化、コスト削減、品質向上を実現します。このサービスは、製造業の課題を深く理解し、それに対する最適なデジタルソリューションを提供することで、企業が持続的な成長とイノベーションを達成できるようサポートします。
製造業ニュース解説
製造業、主に購買・調達部門にお勤めの方々に向けた情報を配信しております。
新任の方やベテランの方、管理職を対象とした幅広いコンテンツをご用意しております。
お問い合わせ
コストダウンが利益に直結する術だと理解していても、なかなか前に進めることができない状況。そんな時は、newjiのコストダウン自動化機能で大きく利益貢献しよう!
(β版非公開)