- お役立ち記事
- Crankshaft Technology and Benefits in OEM Manufacturing
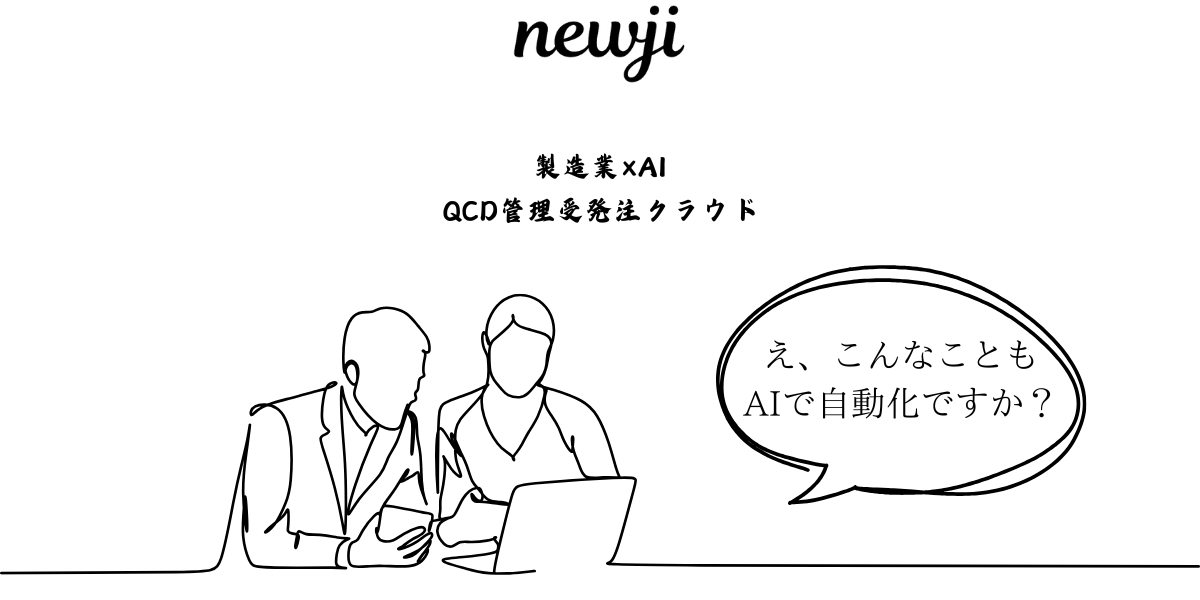
Crankshaft Technology and Benefits in OEM Manufacturing
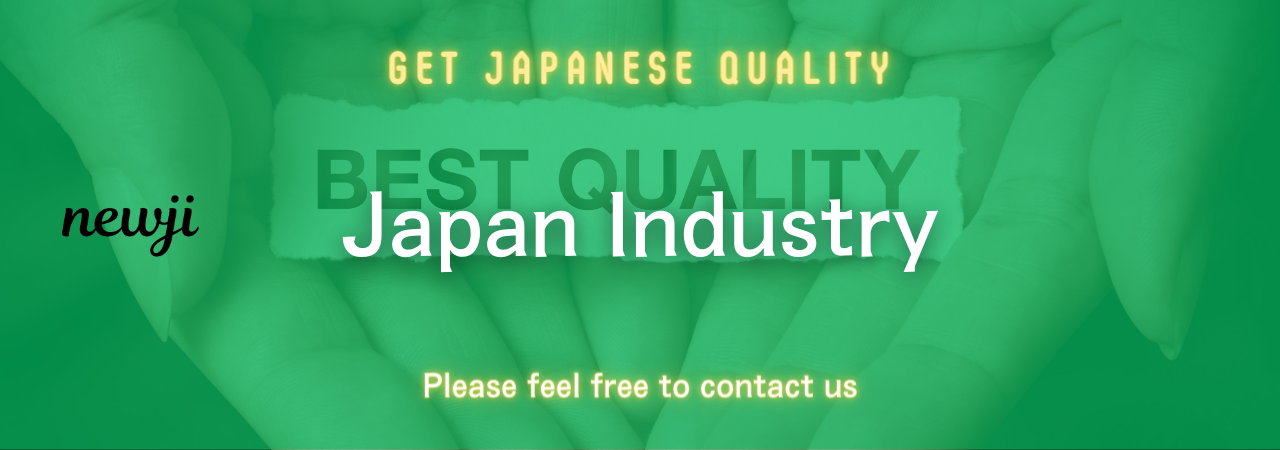
When it comes to car engines, many essential components work together to ensure a smooth and efficient performance.
One of these vital components is the crankshaft.
While it might be overlooked by some, its role is paramount.
Crankshaft technology and its benefits in Original Equipment Manufacturer (OEM) manufacturing hold a special place in the automotive industry.
This article dives deep into the world of crankshafts, their technology, and why they are crucial in OEM manufacturing.
目次
Understanding the Crankshaft
The crankshaft is a fundamental part of an engine.
It converts the linear motion of the pistons into rotational motion, which ultimately drives the vehicle’s wheels.
Constructed from robust materials, typically forged steel or cast iron, the crankshaft withstands considerable forces during engine operation.
Its primary parts include the main journals, rod journals, counterweights, and the crank web.
Main Functions of the Crankshaft
The crankshaft performs several essential functions in an engine:
1. **Motion Conversion:** Turning the piston’s linear movement into rotational motion.
2. **Power Distribution:** Helping distribute power from the engine to other parts of the vehicle.
3. **Engine Timing:** Ensuring accurate timing for the engine’s operational cycles.
Technological Developments in Crankshaft Manufacturing
Crankshaft technology has evolved significantly over the years, leading to improved engine performance and durability.
Innovations in materials, manufacturing processes, and design have paved the way for advanced crankshaft technology.
Material Advances
Earlier crankshafts were primarily made from cast iron.
However, modern crankshafts often use forged steel, which offers significantly better strength and durability.
The latest advancements involve the use of micro-alloyed steels and composite materials to further enhance performance.
These materials offer superior resistance to wear and fatigue, ensuring a longer lifespan for the crankshaft.
Precision Manufacturing
Advanced manufacturing processes like precision forging, machining, and heat treatment have drastically improved crankshaft quality.
Computer Numerical Control (CNC) machining helps achieve exact dimensional tolerances and ensures a perfect balance.
Additionally, techniques like nitriding and induction hardening add a hardened layer to the crankshaft, enhancing wear resistance and longevity.
Design Innovations
Modern crankshaft designs incorporate several features that improve engine efficiency and reduce weight.
For instance, engineers now use fillet rolling, which increases the strength of the crankshaft by producing a compressive stress region.
In addition, hollow or drilled crankshafts reduce the overall weight and rotational inertia, resulting in better fuel efficiency and engine performance.
Benefits of Advanced Crankshaft Technology
The technological advancements in crankshaft engineering offer numerous benefits, especially in OEM manufacturing.
These benefits ultimately translate into better performance, durability, and cost-efficiency.
Enhanced Engine Performance
Precision-manufactured crankshafts contribute to smoother engine operation.
They ensure perfect timing and motion conversion, resulting in improved combustion efficiency.
This not only enhances the vehicle’s horsepower but also leads to better fuel economy.
Durability and Reliability
Advanced materials and manufacturing techniques boost the crankshaft’s durability.
With higher resistance to wear and fatigue, modern crankshafts have a longer service life and require less frequent replacements.
This reliability is crucial for OEMs looking to build vehicles with long-lasting engines.
Cost Efficiency
Although the initial costs of advanced crankshafts might be higher, the benefits outweigh these expenses in the long run.
Enhanced durability and reduced maintenance translate into lower overall costs for OEMs and end-users.
Additionally, the efficiency gains in fuel consumption contribute to cost savings over the vehicle’s lifetime.
Environmental Benefits
Improved crankshaft technology also has environmental advantages.
Better fuel efficiency means lower greenhouse gas emissions.
Furthermore, the longer lifespan and reduced need for replacements result in less industrial waste, contributing to a greener manufacturing process.
The Role of OEMs in Crankshaft Manufacturing
OEMs play a pivotal role in the integration of advanced crankshaft technology.
Their adoption of these advancements ultimately determines the quality and performance of the vehicles they produce.
Quality Control
OEMs implement stringent quality control measures to ensure each crankshaft meets specified standards.
This includes rigorous testing protocols to assess material integrity, dimensional accuracy, and performance under stress.
Such measures ensure that the final product delivers optimal performance and reliability.
Innovation and Collaboration
OEMs often collaborate with specialized crankshaft manufacturers and R&D teams to drive innovation.
This collaboration fosters the development of new technologies and materials, pushing the boundaries of what’s possible in engine performance and efficiency.
Customization for Specific Applications
OEMs can also customize crankshafts to meet the unique requirements of specific vehicle models.
This involves tailoring the design, materials, and manufacturing processes to achieve desired performance characteristics.
Such customization is vital for optimizing engine performance in various vehicle categories, from compact cars to heavy-duty trucks.
Conclusion
Crankshaft technology plays a critical role in the overall performance, durability, and efficiency of car engines.
Advancements in materials, manufacturing processes, and design have significantly enhanced the quality and functionality of modern crankshafts.
For OEMs, integrating these advanced crankshafts into their production lines offers numerous benefits, including enhanced engine performance, reliability, cost efficiency, and environmental advantages.
As the automotive industry continues to evolve, ongoing innovation in crankshaft technology will undoubtedly contribute to further improvements in engine design and manufacturing.
Understanding and leveraging these advancements is essential for OEMs aiming to produce high-quality, efficient, and durable vehicles that meet the demands of today’s discerning consumers.
資料ダウンロード
QCD調達購買管理クラウド「newji」は、調達購買部門で必要なQCD管理全てを備えた、現場特化型兼クラウド型の今世紀最高の購買管理システムとなります。
ユーザー登録
調達購買業務の効率化だけでなく、システムを導入することで、コスト削減や製品・資材のステータス可視化のほか、属人化していた購買情報の共有化による内部不正防止や統制にも役立ちます。
NEWJI DX
製造業に特化したデジタルトランスフォーメーション(DX)の実現を目指す請負開発型のコンサルティングサービスです。AI、iPaaS、および先端の技術を駆使して、製造プロセスの効率化、業務効率化、チームワーク強化、コスト削減、品質向上を実現します。このサービスは、製造業の課題を深く理解し、それに対する最適なデジタルソリューションを提供することで、企業が持続的な成長とイノベーションを達成できるようサポートします。
オンライン講座
製造業、主に購買・調達部門にお勤めの方々に向けた情報を配信しております。
新任の方やベテランの方、管理職を対象とした幅広いコンテンツをご用意しております。
お問い合わせ
コストダウンが利益に直結する術だと理解していても、なかなか前に進めることができない状況。そんな時は、newjiのコストダウン自動化機能で大きく利益貢献しよう!
(Β版非公開)