- お役立ち記事
- Creating a system for preventing design problems and preventing recurrence to improve design quality and its key points
月間76,176名の
製造業ご担当者様が閲覧しています*
*2025年3月31日現在のGoogle Analyticsのデータより
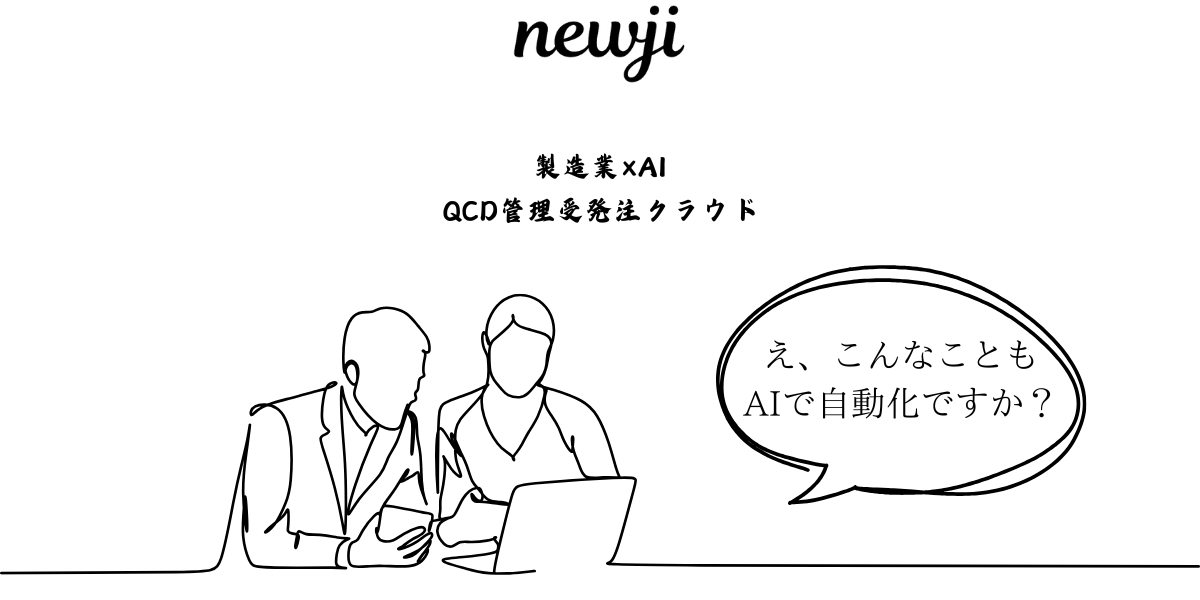
Creating a system for preventing design problems and preventing recurrence to improve design quality and its key points
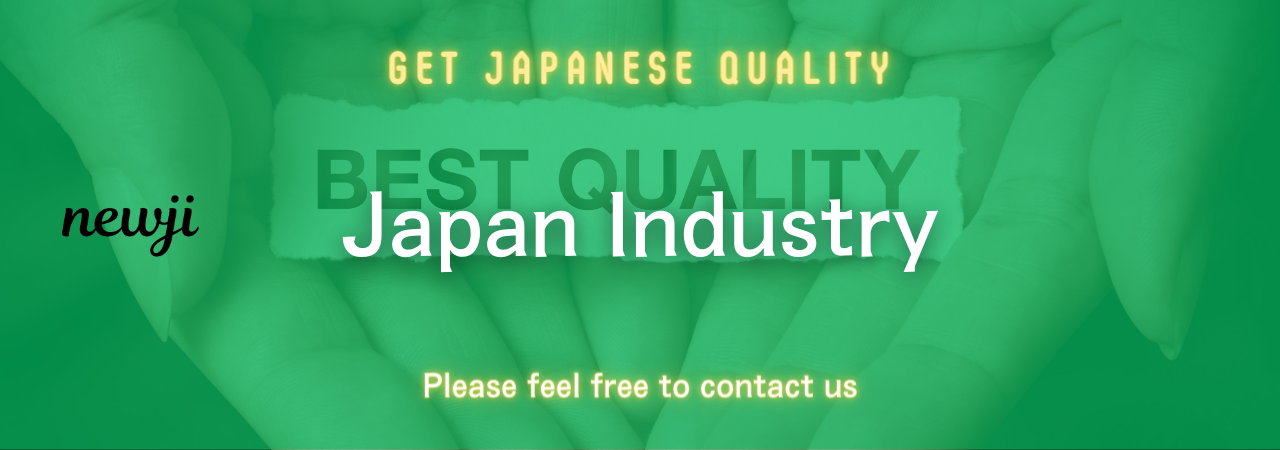
Creating a robust system for preventing design problems and ensuring that past issues do not recur is crucial for improving design quality.
A well-structured approach not only enhances the final product but also elevates the team’s overall efficiency and satisfaction.
Below, we delve into some of the key points and methodologies that can aid in crafting such a system.
目次
Understanding the Root Causes
Before implementing a system to prevent design problems, it’s important to identify the root causes.
Understanding what leads to design flaws is the first step toward improvement.
Conducting thorough post-mortems or retrospectives on past projects where issues were identified can reveal valuable insights.
These sessions should focus on understanding both technical and process-related problems that contributed to lower design quality.
The Five Whys Technique
One effective method for identifying root causes is the Five Whys technique.
By continuously asking “why” a problem occurred, you can delve deeper into underlying causes.
This iterative question-asking process often uncovers systemic issues that, once addressed, can prevent similar problems in the future.
Implementing a Design Review Process
Regular design reviews are an essential component of any system aimed at preventing design problems.
These reviews should be scheduled at various stages of the design process to ensure the project is on the right track.
Peer Reviews and Feedback Loops
Involving peers in the review process can bring fresh perspectives and identify issues that might have been overlooked.
Feedback loops help keep the design process dynamic and adaptable, fostering a collaborative environment where designers can improve their work collectively.
Utilizing Checklists
Introducing checklists for each phase of the design process ensures that all necessary steps are completed and no critical aspect is overlooked.
Checklists can act as reminders for best practices, from concept development to final verification.
Standardizing Design Processes
Standardizing design processes through guidelines and best practices can significantly reduce the occurrence of design issues.
Design standards ensure consistency across projects and provide a clear framework within which designers can operate.
Creating Design Guidelines
A comprehensive set of design guidelines acts as a roadmap for team members.
These guidelines should cover the principles of good design, the use of common elements, and any specific requirements unique to your organization or industry.
Training and Skill Development
Regular training sessions help keep the design team updated on the latest tools, techniques, and industry trends.
Skill development is crucial in ensuring that the team is well-equipped to tackle evolving design challenges.
Utilizing Technology and Tools
Leveraging the right technology and tools can make a significant difference in preventing design problems.
Modern design software often includes features that can help identify potential issues early in the process.
Design Validation Tools
Tools that offer design validation can automatically check for compliance with established standards and flag potential issues.
These tools can serve as an initial screening process, allowing designers to make adjustments before deeper peer reviews.
Version Control and Documentation
Implementing a robust version control system is critical for tracking changes and ensuring that design iterations are well-documented.
Proper documentation allows for easy referencing of previous designs, thereby preventing the recurrence of past problems.
Establishing a Culture of Continuous Improvement
Finally, a culture that values continuous improvement is essential for maintaining high design quality.
Encouraging team members to actively seek feedback and suggestions can lead to continuous enhancements in both design processes and outcomes.
Celebrating Successes and Analyzing Failures
Recognizing successful implementations and thoroughly analyzing failures both play crucial roles.
While success stories boost morale, analyzing failures provides invaluable lessons that can be shared with the entire team.
Encouraging Open Communication
Creating an environment where team members feel comfortable voicing concerns and sharing ideas fosters collaboration and problem-solving.
Open communication channels allow for the timely identification and resolution of potential issues.
These practices lay the foundation for a system that enhances design quality by preemptively addressing design problems and ensuring that past issues do not recur.
When teams work together toward common quality goals, the likelihood of achieving exceptional design outcomes is significantly increased.
資料ダウンロード
QCD管理受発注クラウド「newji」は、受発注部門で必要なQCD管理全てを備えた、現場特化型兼クラウド型の今世紀最高の受発注管理システムとなります。
ユーザー登録
受発注業務の効率化だけでなく、システムを導入することで、コスト削減や製品・資材のステータス可視化のほか、属人化していた受発注情報の共有化による内部不正防止や統制にも役立ちます。
NEWJI DX
製造業に特化したデジタルトランスフォーメーション(DX)の実現を目指す請負開発型のコンサルティングサービスです。AI、iPaaS、および先端の技術を駆使して、製造プロセスの効率化、業務効率化、チームワーク強化、コスト削減、品質向上を実現します。このサービスは、製造業の課題を深く理解し、それに対する最適なデジタルソリューションを提供することで、企業が持続的な成長とイノベーションを達成できるようサポートします。
製造業ニュース解説
製造業、主に購買・調達部門にお勤めの方々に向けた情報を配信しております。
新任の方やベテランの方、管理職を対象とした幅広いコンテンツをご用意しております。
お問い合わせ
コストダウンが利益に直結する術だと理解していても、なかなか前に進めることができない状況。そんな時は、newjiのコストダウン自動化機能で大きく利益貢献しよう!
(β版非公開)