- お役立ち記事
- Creating High-Performance Materials for Manufacturing with CVD Technology
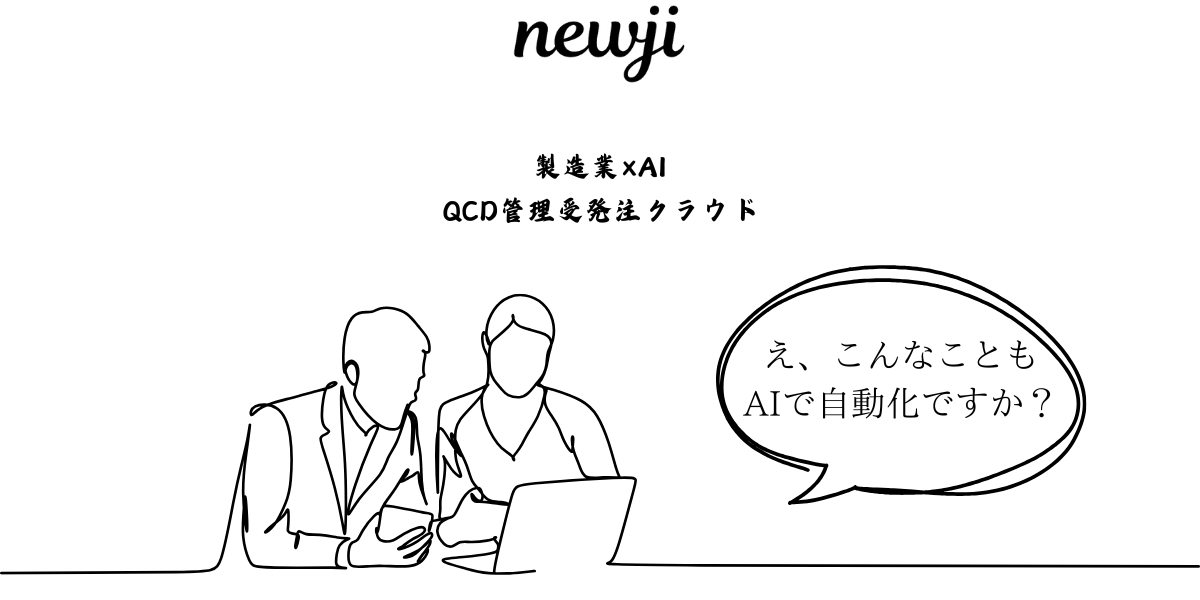
Creating High-Performance Materials for Manufacturing with CVD Technology
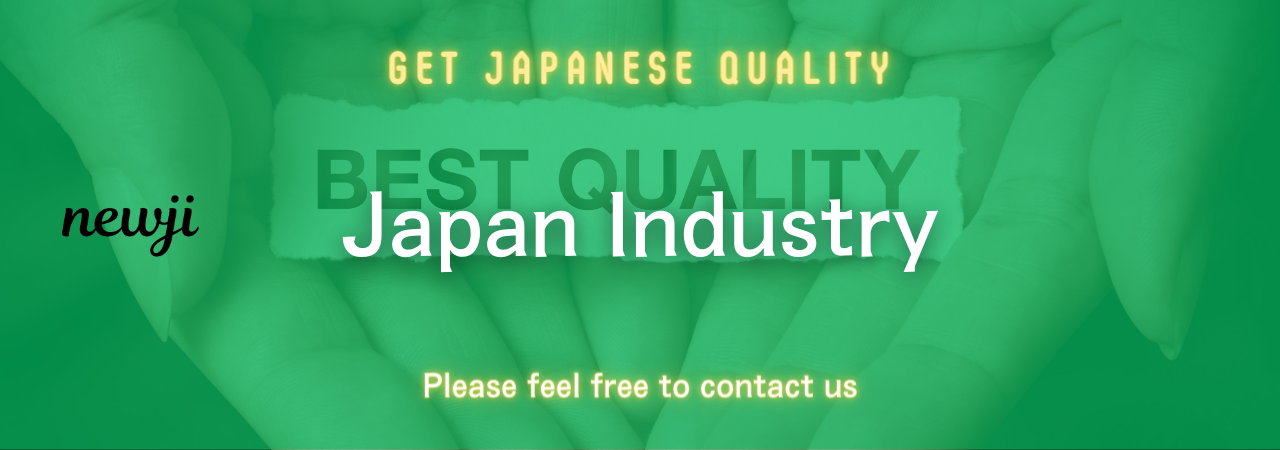
Chemical Vapor Deposition (CVD) technology is revolutionizing the manufacturing industry by enabling the creation of high-performance materials. This innovative process is not only enhancing the quality of products but also increasing their durability and efficiency. In this article, we will explore how CVD technology is being used to craft advanced materials and why it is becoming an integral part of modern manufacturing.
目次
Understanding Chemical Vapor Deposition (CVD)
Chemical Vapor Deposition, commonly known as CVD, is a process used to produce high-quality, high-performance solid materials.
The technique involves depositing a thin film on a substrate through chemical reactions of vapor-phase precursors.
This creates a highly uniform and durable coating, essential for various industrial applications.
How CVD Works
In the CVD process, chemical reactants are introduced into a reaction chamber in their vapor form.
These reactants undergo chemical reactions on the substrate’s surface, forming a solid material layer.
The unreacted precursor gases and by-products are then removed from the chamber, leaving behind a pristine thin film.
The process parameters—such as temperature, pressure, and reactant concentration—are carefully controlled to ensure the desired material properties.
Applications of CVD in Manufacturing
CVD technology is highly versatile and employed across a variety of industries.
Its applications range from electronics to aerospace, offering significant advancements in material performance.
Semiconductor Industry
One of the primary users of CVD technology is the semiconductor industry.
CVD is crucial in fabricating integrated circuits and other electronic components.
By applying thin films of materials like silicon dioxide and silicon nitride, manufacturers can achieve the precise electrical properties needed for high-performance electronic devices.
Aerospace and Defense
The aerospace and defense sectors also benefit significantly from CVD technology.
In these industries, materials need to withstand extreme conditions such as high temperatures and corrosive environments.
CVD is used to create protective coatings for turbine blades and other critical components, enhancing their performance and lifespan.
Medical Devices
Medical device manufacturing relies on CVD for producing biocompatible materials.
Titanium and other metals can be coated with thin films using CVD, providing improved wear resistance and reducing the risk of implant rejection.
This technology ensures that medical implants and devices are safe and effective for long-term use.
Optics and Photonics
CVD is instrumental in the optics and photonics industry for producing antireflective coatings, mirrors, and lenses.
These coatings improve optical performance and durability, making them essential for applications ranging from consumer electronics to advanced scientific instruments.
Advantages of CVD Technology
The adoption of CVD technology in manufacturing is largely due to its numerous advantages.
These benefits make CVD a preferred method for producing high-performance materials.
Precise Control Over Material Properties
CVD allows for the precise control of material properties such as thickness, composition, and microstructure.
This level of control is critical in applications where specific material characteristics are necessary for optimal performance.
Uniform Coatings
One of the standout features of CVD is its ability to produce highly uniform coatings.
This uniformity ensures consistent performance and reliability of the manufactured components, which is particularly important in industries like electronics and aerospace.
Versatility
CVD can be used with a wide range of materials, including metals, ceramics, and polymers.
This versatility makes it suitable for a broad spectrum of applications, allowing manufacturers to tailor the coating properties to meet specific requirements.
Improved Durability and Performance
Components coated with materials deposited using CVD exhibit enhanced durability and performance.
These improvements translate to longer service life and reduced maintenance costs, providing significant economic benefits.
Challenges and Future Developments
While CVD technology offers numerous benefits, it is not without its challenges.
However, ongoing research and development are addressing these issues, paving the way for future advancements.
Complexity of the Process
The CVD process can be complex and requires precise control of various parameters.
Maintaining consistent results can be challenging, especially for large-scale production.
However, advancements in process control technologies are helping to mitigate these issues, making CVD more reliable and accessible.
Environmental Concerns
The use of potentially hazardous chemicals in CVD processes raises environmental and safety concerns.
Researchers are exploring alternative, environmentally friendly precursors and developing methods to minimize waste and emissions.
These efforts aim to make CVD a more sustainable manufacturing technology.
Cost Considerations
Initial setup costs for CVD equipment can be high, which may deter small and medium-sized enterprises from adopting the technology.
However, the long-term benefits—such as reduced maintenance and improved product performance—often outweigh the initial investment.
As the technology continues to evolve, it is expected that costs will decrease, making CVD more accessible to a wider range of manufacturers.
Conclusion
Chemical Vapor Deposition (CVD) technology is transforming the manufacturing landscape by enabling the creation of high-performance, durable materials.
Its applications span various industries, from semiconductors to aerospace, medical devices, and optics.
By offering precise control over material properties, producing uniform coatings, and improving durability, CVD is becoming an essential tool for manufacturers.
While challenges remain, ongoing research and technological advancements are addressing these issues, ensuring that CVD technology continues to play a critical role in the future of manufacturing.
Overall, the adoption of CVD in manufacturing promises to drive innovation, enhance product quality, and deliver significant economic and environmental benefits.
資料ダウンロード
QCD調達購買管理クラウド「newji」は、調達購買部門で必要なQCD管理全てを備えた、現場特化型兼クラウド型の今世紀最高の購買管理システムとなります。
ユーザー登録
調達購買業務の効率化だけでなく、システムを導入することで、コスト削減や製品・資材のステータス可視化のほか、属人化していた購買情報の共有化による内部不正防止や統制にも役立ちます。
NEWJI DX
製造業に特化したデジタルトランスフォーメーション(DX)の実現を目指す請負開発型のコンサルティングサービスです。AI、iPaaS、および先端の技術を駆使して、製造プロセスの効率化、業務効率化、チームワーク強化、コスト削減、品質向上を実現します。このサービスは、製造業の課題を深く理解し、それに対する最適なデジタルソリューションを提供することで、企業が持続的な成長とイノベーションを達成できるようサポートします。
オンライン講座
製造業、主に購買・調達部門にお勤めの方々に向けた情報を配信しております。
新任の方やベテランの方、管理職を対象とした幅広いコンテンツをご用意しております。
お問い合わせ
コストダウンが利益に直結する術だと理解していても、なかなか前に進めることができない状況。そんな時は、newjiのコストダウン自動化機能で大きく利益貢献しよう!
(Β版非公開)