- お役立ち記事
- Creating High-Performance Materials in Manufacturing Using CVD Technology
Creating High-Performance Materials in Manufacturing Using CVD Technology
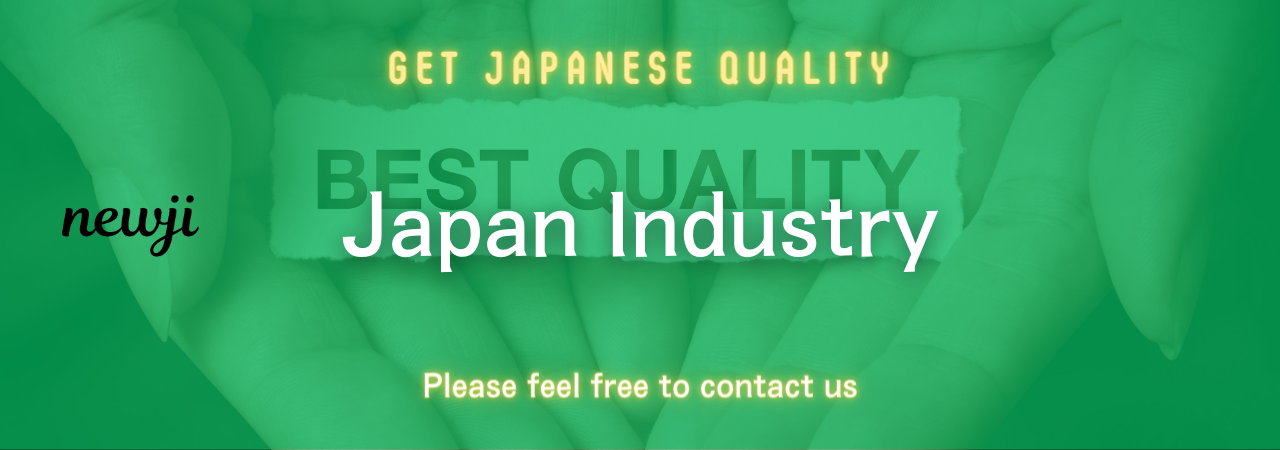
Chemical vapor deposition (CVD) technology has revolutionized the manufacturing industry by enabling the creation of high-performance materials with exceptional properties. This technology has become an essential tool in producing coatings, thin films, and other advanced materials used in various applications. In this article, we will explore how CVD technology works, its advantages, and its importance in manufacturing processes.
目次
Understanding Chemical Vapor Deposition (CVD)
Chemical Vapor Deposition (CVD) is a process used to produce high-quality, high-performance solid materials. Typically, the process involves the chemical reaction of gaseous precursors inside a reaction chamber, where a substrate surface acts as the deposition site. The precursor gases are introduced into the chamber, and at the right temperature settings, they react and form a thin film on the substrate.
The type of material deposited and its properties are determined by the choice of precursor gases, reaction conditions, and process parameters. The resulting thin films are used in a variety of industries, including semiconductor manufacturing, aerospace, and automotive sectors.
How CVD Technology Works
The CVD process involves several steps, and understanding these steps is essential to grasp how CVD technology works.
1. Introduction of Precursors
The process begins with the introduction of precursor gases into the reaction chamber. These gases are specially selected based on the desired material to be deposited. For example, in depositing silicon, silane (SiH4) or dichlorosilane (SiH2Cl2) may be used as the silicon source.
2. Chemical Reactions
Inside the CVD reactor, the precursor gases undergo thermal decomposition or chemical reactions. The energy required for these reactions is typically provided by heating the substrate to a high temperature. As the gases react, they form solid byproducts, which deposit as thin films on the substrate surface.
3. Film Growth
The solid byproducts form a continuous layer of material on the substrate. Depending on the process conditions, such as temperature, pressure, and gas flow rates, the films can have different properties and thicknesses. This allows for precise control over the final product.
Types of CVD Processes
Several variants of the CVD process have been developed to suit different applications and materials. Some of the most common types of CVD processes include:
1. Thermal CVD
In this process, the substrate is heated to a high temperature to facilitate the decomposition of the precursor gases. Thermal CVD is widely used to deposit silicon, silicon dioxide, and other materials in the semiconductor industry.
2. Plasma-Enhanced CVD (PECVD)
PECVD uses plasma to enhance the chemical reactions at lower temperatures. This allows for the deposition of materials that might decompose if exposed to high temperatures. PECVD is frequently used for depositing silicon nitride and amorphous silicon films.
3. Metal-Organic CVD (MOCVD)
MOCVD utilizes metal-organic precursors to deposit thin films of metals, metal oxides, and other compounds. This technique is widely used in producing compound semiconductors, such as gallium arsenide (GaAs) and indium phosphide (InP).
Advantages of CVD Technology
CVD technology offers several advantages that make it a preferred choice in various manufacturing applications.
1. High Quality and Performance
CVD enables the deposition of materials with excellent uniformity and high-purity levels. The resulting films are often dense and adherent, providing excellent mechanical and chemical properties. This makes them ideal for use in high-performance applications.
2. Flexibility in Material Selection
CVD can be used to deposit a wide range of materials, including metals, ceramics, and polymers. This flexibility allows manufacturers to tailor the properties of coatings and films to meet specific application requirements.
3. Precise Control
The CVD process provides precise control over the thickness and composition of the deposited films. By adjusting process parameters, manufacturers can achieve the desired film characteristics. This level of control is crucial in applications like semiconductor fabrication, where even slight variations can impact performance.
4. Scalability
CVD is a scalable process that can be adapted to different production volumes. From small-scale research to large-scale industrial production, CVD technology can meet various manufacturing needs.
Applications of CVD Technology
The versatility of CVD technology has led to its adoption in numerous industries. Here are some key applications:
1. Semiconductor Manufacturing
CVD plays a vital role in the semiconductor industry by enabling the deposition of critical materials used in integrated circuits and microelectronics. These include silicon dioxide, silicon nitride, and metal films.
2. Aerospace and Defense
In the aerospace and defense sectors, CVD is used to create coatings that enhance the durability and performance of components exposed to extreme conditions. Thermal barrier coatings and protective ceramic coatings are common examples.
3. Solar Cells
The production of thin-film solar cells often relies on CVD technology to deposit materials like cadmium telluride (CdTe) and copper indium gallium selenide (CIGS). These materials are essential for improving the efficiency and performance of solar cells.
4. Medical Devices
CVD is also used in the medical field to produce biocompatible coatings for implants and medical devices. These coatings improve the longevity and functionality of implants, enhancing patient outcomes.
Challenges and Future Directions
While CVD technology offers many benefits, it also presents certain challenges. These include high energy consumption, complex equipment, and the need for precise process control. Nonetheless, ongoing research and advancements in CVD technology aim to address these challenges and unlock new possibilities.
In conclusion, CVD technology has transformed the manufacturing landscape by enabling the creation of high-performance materials with exceptional properties. From semiconductors to aerospace components, the impact of CVD is evident across various industries. As research and innovation continue, CVD technology will likely play an increasingly important role in producing the advanced materials of the future.
資料ダウンロード
QCD調達購買管理クラウド「newji」は、調達購買部門で必要なQCD管理全てを備えた、現場特化型兼クラウド型の今世紀最高の購買管理システムとなります。
ユーザー登録
調達購買業務の効率化だけでなく、システムを導入することで、コスト削減や製品・資材のステータス可視化のほか、属人化していた購買情報の共有化による内部不正防止や統制にも役立ちます。
NEWJI DX
製造業に特化したデジタルトランスフォーメーション(DX)の実現を目指す請負開発型のコンサルティングサービスです。AI、iPaaS、および先端の技術を駆使して、製造プロセスの効率化、業務効率化、チームワーク強化、コスト削減、品質向上を実現します。このサービスは、製造業の課題を深く理解し、それに対する最適なデジタルソリューションを提供することで、企業が持続的な成長とイノベーションを達成できるようサポートします。
オンライン講座
製造業、主に購買・調達部門にお勤めの方々に向けた情報を配信しております。
新任の方やベテランの方、管理職を対象とした幅広いコンテンツをご用意しております。
お問い合わせ
コストダウンが利益に直結する術だと理解していても、なかなか前に進めることができない状況。そんな時は、newjiのコストダウン自動化機能で大きく利益貢献しよう!
(Β版非公開)