- お役立ち記事
- Creating the Future of Manufacturing with Digital Twin! Quality Improvement and Cost Reduction through Simulation
Creating the Future of Manufacturing with Digital Twin! Quality Improvement and Cost Reduction through Simulation
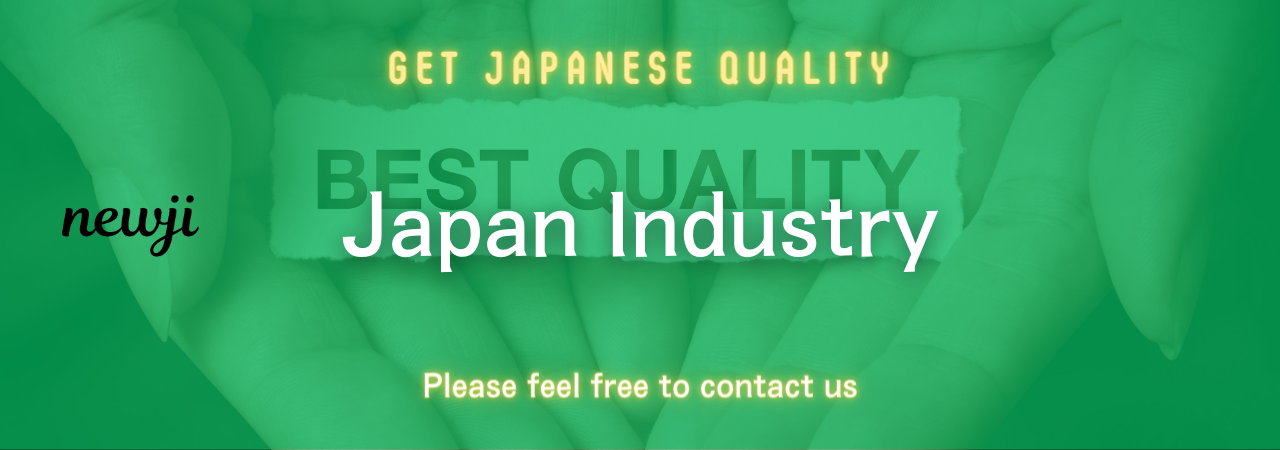
In today’s rapidly evolving technological landscape, the concept of a digital twin is gaining significant traction, especially in the manufacturing sector.
Simply put, a digital twin is a virtual replica of a physical object or system.
This sophisticated technology allows manufacturers to simulate, predict, and optimize the production processes without any physical constraints.
By leveraging digital twins, companies can significantly improve product quality and reduce costs.
Let’s dive deeper into the world of digital twins and explore how they are revolutionizing manufacturing.
目次
What is a Digital Twin?
A digital twin serves as a digital counterpart of a physical object or system.
It captures real-time data through sensors and other IoT devices.
This information is then used to create a detailed digital model that mirrors the actual conditions and performance of the physical entity.
This technology enables continuous updating and synchronization between the physical and digital models.
As a result, it provides real-time insights and predictive analytics.
How Digital Twins Work
Digital twins work by utilizing a combination of sensors, data analytics, and cloud computing.
Sensors embedded in physical objects continuously collect data related to performance, environmental conditions, and other relevant metrics.
This data is then fed into the cloud, where it is processed and analyzed through advanced algorithms and machine learning techniques.
The result is an accurate digital representation that can simulate the behavior of the physical object under various scenarios.
The Benefits of Digital Twins in Manufacturing
Digital twin technology offers numerous advantages for the manufacturing industry.
Some key benefits include:
Improved Product Quality
By simulating entire production processes, digital twins help identify potential issues and bottlenecks before they occur.
This ensures that products are manufactured to the highest standards.
Manufacturers can tweak and optimize processes in the virtual environment, thus eliminating defects and enhancing overall product quality.
Cost Reduction
Digital twins drastically reduce the need for physical prototypes and real-world testing.
This cuts down material and labor costs.
Additionally, predictive maintenance enabled by digital twins can minimize downtime and extend the lifespan of machinery, providing further cost savings.
Enhanced Decision-Making
Real-time data and analytics offered by digital twins allow managers to make more informed decisions.
They can assess various manufacturing scenarios, predict outcomes, and choose the most efficient path forward.
This level of insight is invaluable for strategic planning and resource allocation.
Faster Time-to-Market
By streamlining the design and testing phases, digital twins can significantly shorten the time needed to bring a product to market.
Simulations enable rapid iteration and optimization, ensuring that the final product meets market demands without unnecessary delays.
Applications of Digital Twins in Manufacturing
The versatility of digital twin technology allows it to be employed across various facets of manufacturing:
Product Design and Development
Digital twins enable engineers to create highly detailed virtual models of products and test them under different conditions.
This leads to more innovative designs and quicker identification of potential issues.
Production Process Optimization
Manufacturers can use digital twins to simulate entire production lines and workflows.
This helps in optimizing operations for efficiency and productivity.
Virtual simulations can reveal inefficiencies and suggest improvements without interrupting actual production.
Supply Chain Management
Digital twins can also be applied to monitor and manage supply chains.
By creating a digital representation of the supply network, manufacturers can anticipate disruptions, optimize inventory levels, and ensure timely deliveries.
Challenges and Considerations
Despite its numerous benefits, implementing digital twin technology comes with certain challenges.
Data Integration
Accurate digital twins rely on the seamless integration of data from various sources.
Ensuring that the correct data is collected, processed, and analyzed in real-time can be complex and requires robust IT infrastructure.
High Initial Costs
The setup and implementation of digital twin technology can be expensive.
While the long-term benefits often outweigh the initial investment, smaller manufacturers may find it challenging to allocate the necessary resources upfront.
Data Security
With the extensive use of IoT devices and cloud computing, ensuring data security and privacy becomes crucial.
Manufacturers must invest in robust cybersecurity measures to protect sensitive information from breaches.
The Future of Digital Twins in Manufacturing
As technology continues to advance, the role of digital twins in manufacturing is set to expand.
More industries are likely to adopt this technology, driven by the promising results it delivers.
Integration with AI and Machine Learning
The powerful combination of digital twins and artificial intelligence will unlock new possibilities.
AI and machine learning algorithms can further enhance the predictive capabilities of digital twins, offering even deeper insights and smarter automation.
Edge Computing
With the advent of edge computing, digital twins can process data closer to the source, reducing latency and enabling faster decision-making.
This is especially valuable for real-time applications in manufacturing environments.
Sustainability
Digital twins can play a crucial role in promoting sustainability.
By optimizing resource usage and minimizing waste, manufacturers can reduce their environmental impact without compromising on productivity.
The digital twin technology is transforming the manufacturing industry, offering unprecedented levels of insight, efficiency, and cost savings.
By embracing digital twins, manufacturers can create higher-quality products, optimize production processes, and drive innovation.
While challenges remain, the long-term benefits of digital twins undoubtedly make them a worthwhile investment for the future of manufacturing.
資料ダウンロード
QCD調達購買管理クラウド「newji」は、調達購買部門で必要なQCD管理全てを備えた、現場特化型兼クラウド型の今世紀最高の購買管理システムとなります。
ユーザー登録
調達購買業務の効率化だけでなく、システムを導入することで、コスト削減や製品・資材のステータス可視化のほか、属人化していた購買情報の共有化による内部不正防止や統制にも役立ちます。
NEWJI DX
製造業に特化したデジタルトランスフォーメーション(DX)の実現を目指す請負開発型のコンサルティングサービスです。AI、iPaaS、および先端の技術を駆使して、製造プロセスの効率化、業務効率化、チームワーク強化、コスト削減、品質向上を実現します。このサービスは、製造業の課題を深く理解し、それに対する最適なデジタルソリューションを提供することで、企業が持続的な成長とイノベーションを達成できるようサポートします。
オンライン講座
製造業、主に購買・調達部門にお勤めの方々に向けた情報を配信しております。
新任の方やベテランの方、管理職を対象とした幅広いコンテンツをご用意しております。
お問い合わせ
コストダウンが利益に直結する術だと理解していても、なかなか前に進めることができない状況。そんな時は、newjiのコストダウン自動化機能で大きく利益貢献しよう!
(Β版非公開)