- お役立ち記事
- Creation and management procedures for material approval requests in manufacturing
月間76,176名の
製造業ご担当者様が閲覧しています*
*2025年3月31日現在のGoogle Analyticsのデータより
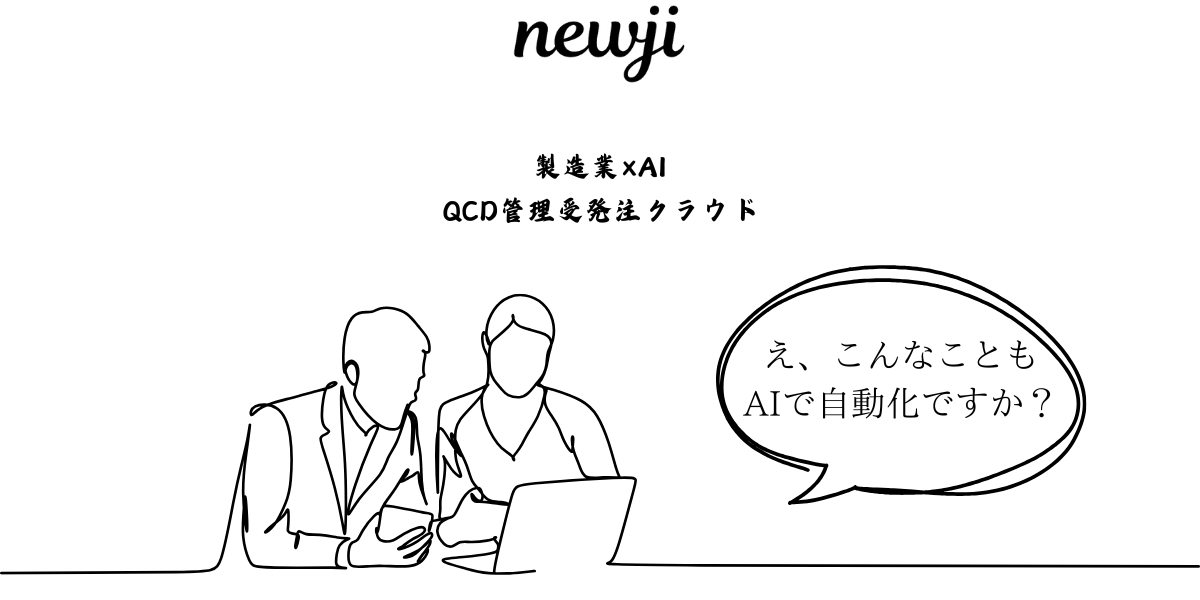
Creation and management procedures for material approval requests in manufacturing
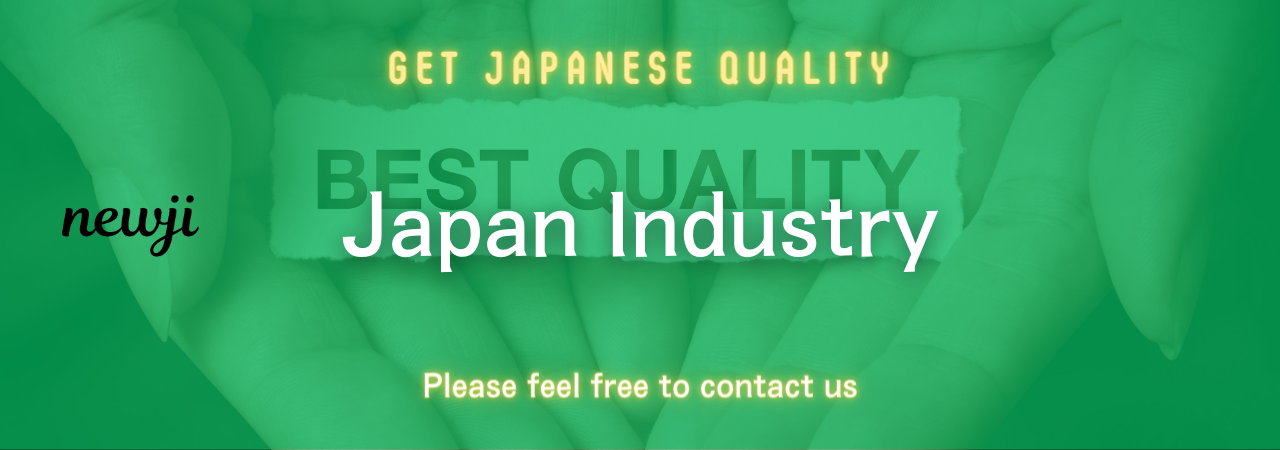
When working in manufacturing, handling materials properly is crucial.
One significant aspect is the approval process for these materials.
Here, we’ll discuss the creation and management procedures for material approval requests.
Understanding these procedures helps ensure the quality and reliability of the final products.
目次
Understanding Material Approval Requests
Before diving into the steps, it’s essential to comprehend what a material approval request (MAR) is.
A MAR is a formal document used to confirm that a particular material meets the required standards and specifications before it is used in production.
This ensures that the materials are suitable for their intended purpose and helps avoid potential issues down the line.
Why MARs are Important
MARs are vital in manufacturing for several reasons.
Firstly, they help maintain the quality of the products by ensuring that only approved materials are used.
This can prevent defects and ensure customer satisfaction.
Additionally, MARs facilitate compliance with industry standards and regulations, which can be crucial for avoiding legal issues.
Creating a Material Approval Request
The first step in the MAR process is to create the request.
This involves gathering all necessary information and documentation to support the approval.
Here are the key components typically included in a MAR:
1. Material Description
This section should provide a detailed description of the material.
Include the material name, manufacturer, part number, and any other identifying details.
Having precise and accurate descriptions helps avoid confusion and ensures that everyone involved understands what is being referred to.
2. Specifications and Requirements
List the specific standards and requirements that the material needs to meet.
This can include physical properties, chemical composition, performance criteria, and any relevant industry standards.
Providing clear specifications helps the approver understand what to look for when reviewing the material.
3. Test Results and Certificates
Attach any relevant test results and certificates that demonstrate the material’s compliance with the required standards.
These can include lab test reports, quality certificates, and inspection records.
These documents provide evidence that the material meets the necessary criteria.
4. Supplier Information
Include information about the supplier of the material.
This should consist of the supplier’s name, contact details, and any relevant credentials or certifications.
Having this information readily available can facilitate communication and verification if any questions or issues arise.
Submitting and Approving the Request
Once the MAR has been created, the next step is to submit it for approval.
Here are the steps for submitting and getting the request approved:
1. Routing the Request
Determine who needs to review and approve the MAR.
This can include quality control personnel, engineering teams, and management.
The request should be routed to the appropriate individuals or departments for their review and approval.
2. Reviewing the Request
Reviewers should carefully examine the MAR, considering all the information and documentation provided.
They should verify that the material meets all specified requirements and standards.
If any discrepancies or issues are found, they should be documented, and the request may need to be returned for further clarification or modification.
3. Providing Feedback
After reviewing the MAR, approvers should provide feedback on whether the material is approved or if additional information is needed.
If the material is approved, the feedback should include any conditions or notes that need to be addressed.
If the material is not approved, clear reasons and required actions should be provided.
Managing Approved Materials
Once a material is approved, it’s essential to manage it effectively to ensure continued compliance and quality.
Here are some key steps for managing approved materials:
1. Documenting Approvals
Keep detailed records of all approved materials, including the MAR and any supporting documents.
This helps maintain an audit trail and ensures that there is a reference if any issues arise in the future.
Documentation should be organized and easily accessible.
2. Regular Monitoring and Inspection
Even after a material is approved, regular monitoring and inspection are crucial.
Conduct periodic tests and inspections to ensure the material continues to meet the required standards.
Any changes in the material’s properties or performance should be documented and addressed promptly.
3. Updating Approvals
If there are any changes to the material or its specifications, an updated MAR should be submitted for review and approval.
This ensures that all materials in use continue to meet the necessary criteria.
Keeping approvals up to date helps maintain product quality and avoids potential issues down the line.
4. Communication and Training
Ensure that all relevant personnel are aware of the approved materials and any conditions associated with their use.
Provide training on the proper handling and use of the materials to avoid any compliance issues.
Effective communication helps ensure that everyone is on the same page and can adhere to the approved standards.
Understanding and following the creation and management procedures for material approval requests is critical in the manufacturing industry.
By creating detailed and accurate MARs, submitting them for proper review, and managing approved materials effectively, companies can maintain high product quality and compliance with industry standards.
This not only helps in producing reliable products but also fosters trust and satisfaction among customers.
資料ダウンロード
QCD管理受発注クラウド「newji」は、受発注部門で必要なQCD管理全てを備えた、現場特化型兼クラウド型の今世紀最高の受発注管理システムとなります。
ユーザー登録
受発注業務の効率化だけでなく、システムを導入することで、コスト削減や製品・資材のステータス可視化のほか、属人化していた受発注情報の共有化による内部不正防止や統制にも役立ちます。
NEWJI DX
製造業に特化したデジタルトランスフォーメーション(DX)の実現を目指す請負開発型のコンサルティングサービスです。AI、iPaaS、および先端の技術を駆使して、製造プロセスの効率化、業務効率化、チームワーク強化、コスト削減、品質向上を実現します。このサービスは、製造業の課題を深く理解し、それに対する最適なデジタルソリューションを提供することで、企業が持続的な成長とイノベーションを達成できるようサポートします。
製造業ニュース解説
製造業、主に購買・調達部門にお勤めの方々に向けた情報を配信しております。
新任の方やベテランの方、管理職を対象とした幅広いコンテンツをご用意しております。
お問い合わせ
コストダウンが利益に直結する術だと理解していても、なかなか前に進めることができない状況。そんな時は、newjiのコストダウン自動化機能で大きく利益貢献しよう!
(β版非公開)