- お役立ち記事
- Crisis management strategy for purchasing department in response to supply chain disruption
Crisis management strategy for purchasing department in response to supply chain disruption|newji
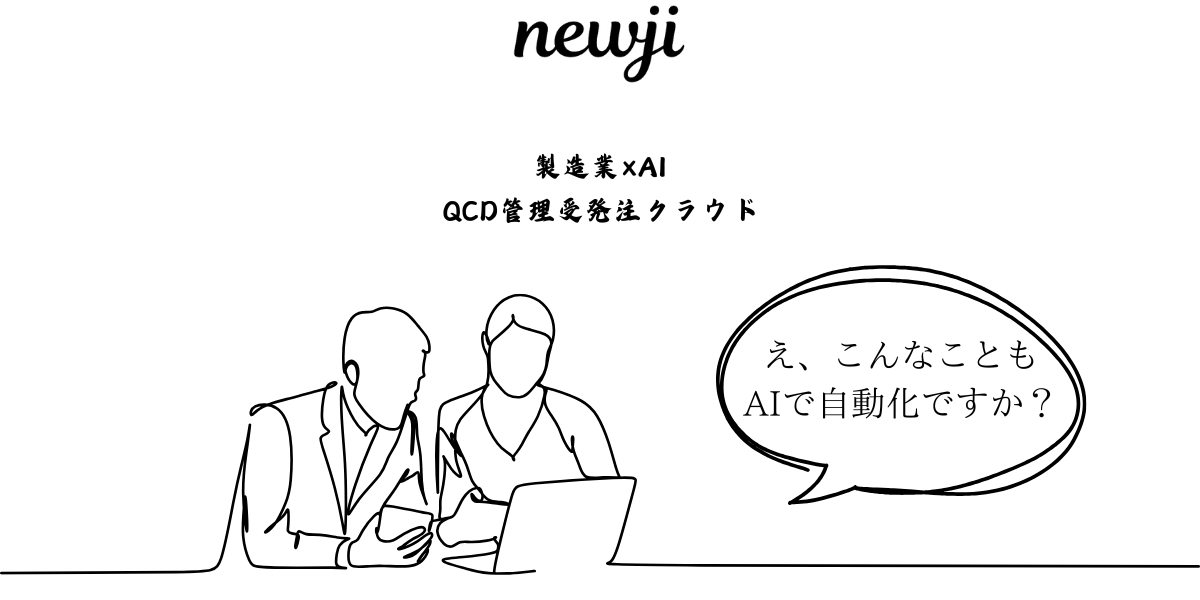
Crisis management strategy for purchasing department in response to supply chain disruption
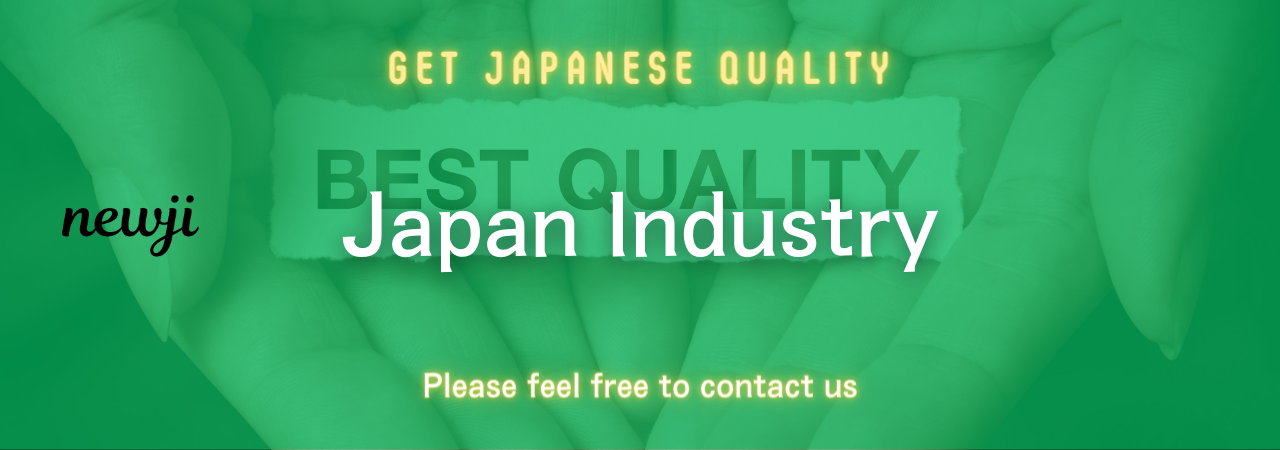
目次
Understanding Supply Chain Disruption
Supply chain disruptions are becoming an increasingly common challenge faced by purchasing departments across industries.
These disruptions can stem from various factors, including natural disasters, geopolitical tensions, pandemics, or unexpected changes in demand and supply dynamics.
Understanding the root causes of these disruptions is essential for developing a proactive crisis management strategy.
Disruptions not only delay the procurement process but can also lead to increased costs, reduced customer satisfaction, and loss of revenue.
For purchasing departments, the key to handling these challenges lies in developing a well-rounded crisis management strategy that addresses the complexities of the modern supply chain.
Importance of a Crisis Management Strategy
A crisis management strategy enables purchasing departments to navigate supply chain disruptions effectively.
By having a strategy in place, companies can mitigate risks, minimize operational impacts, and ensure continuity during turbulent times.
This proactive approach helps in maintaining strong supplier relationships, safeguarding brand reputation, and upholding customer trust.
An effective crisis management strategy involves a mix of risk assessment, contingency planning, supplier management, and continuous improvement.
These elements work together to enhance the department’s resilience against unforeseen events, thus enabling quicker recovery and adaptability.
Risk Assessment and Identification
The first step towards creating a robust crisis management strategy is identifying the potential risks that could disrupt the supply chain.
This process involves analyzing historical data, market trends, and geopolitical factors that may influence the sourcing and procurement process.
Risk assessment helps in categorizing risks into different tiers, such as critical, high, medium, and low.
Understanding the severity and likelihood of each risk allows purchasing departments to prioritize their responses and allocate resources more efficiently.
By identifying vulnerabilities, companies can work on strengthening weak links in the supply chain, whether they relate to specific suppliers, geographic regions, or logistical challenges.
Developing a Contingency Plan
Once risks have been assessed, the next step is to create a detailed contingency plan.
This plan outlines the procedures to follow in the event of a supply chain disruption, detailing roles, responsibilities, and communication channels for all stakeholders involved.
Contingency planning involves outlining alternate sourcing strategies, such as identifying secondary suppliers or considering different geographical locations for procurement.
Having multiple options reduces dependency on a single source and spreads the risk across different suppliers.
Additionally, the contingency plan should include inventory management strategies, like increasing safety stock levels for critical components, to buffer against supply interruptions.
Leveraging Technology
Technology plays a crucial role in effective contingency planning.
Advanced supply chain management tools provide real-time data analytics, offering visibility across the entire supply chain network.
These tools help in early detection of potential disruptions and enable quick decision-making.
Further, technologies like artificial intelligence and machine learning can enhance predictive analytics, enabling companies to anticipate and mitigate risks before they evolve into major disruptions.
Supplier Relationship Management
Strong supplier relationships are vital in managing supply chain disruptions effectively.
Purchasing departments should focus on building and maintaining strong partnerships with suppliers through regular communication, collaborative planning, and transparency.
Developing trust and cooperation with suppliers ensures that companies receive timely information about potential disruptions or delays.
This proactive communication allows purchasing departments to take preventive measures or make necessary adjustments in their procurement plans.
It’s also important to contractually define terms related to crisis management with suppliers.
This includes defining expectations around responsiveness, flexibility, and support that suppliers must provide during disruptions.
Continuous Improvement and Adaptation
The world of supply chains is dynamic, and risks continually evolve.
Therefore, a crisis management strategy should be a living document that is regularly reviewed, updated, and tested.
Continuous improvement processes involve post-crisis evaluations to identify successes, gaps, and areas for improvement.
Organizations should conduct regular training and simulation exercises to ensure readiness.
These exercises prepare teams to respond effectively in real-life scenarios, ensuring that everyone knows their roles and responsibilities during a disruption.
Moreover, staying updated with industry best practices and emerging trends in supply chain management can help departments refine their strategies and remain competitive.
Conclusion
In today’s connected world, supply chain disruptions are inevitable.
Purchasing departments that anticipate potential disruptions and prepare accordingly can significantly minimize their impact.
By focusing on risk assessment, contingency planning, supplier management, and continuous improvement, companies can develop a robust crisis management strategy.
This proactive approach not only helps in overcoming immediate challenges but also enhances the overall resilience of the supply chain.
As a result, purchasing departments can ensure continuity, maintain customer trust, and protect their organization’s brand reputation, even in the face of adversity.
資料ダウンロード
QCD調達購買管理クラウド「newji」は、調達購買部門で必要なQCD管理全てを備えた、現場特化型兼クラウド型の今世紀最高の購買管理システムとなります。
ユーザー登録
調達購買業務の効率化だけでなく、システムを導入することで、コスト削減や製品・資材のステータス可視化のほか、属人化していた購買情報の共有化による内部不正防止や統制にも役立ちます。
NEWJI DX
製造業に特化したデジタルトランスフォーメーション(DX)の実現を目指す請負開発型のコンサルティングサービスです。AI、iPaaS、および先端の技術を駆使して、製造プロセスの効率化、業務効率化、チームワーク強化、コスト削減、品質向上を実現します。このサービスは、製造業の課題を深く理解し、それに対する最適なデジタルソリューションを提供することで、企業が持続的な成長とイノベーションを達成できるようサポートします。
オンライン講座
製造業、主に購買・調達部門にお勤めの方々に向けた情報を配信しております。
新任の方やベテランの方、管理職を対象とした幅広いコンテンツをご用意しております。
お問い合わせ
コストダウンが利益に直結する術だと理解していても、なかなか前に進めることができない状況。そんな時は、newjiのコストダウン自動化機能で大きく利益貢献しよう!
(Β版非公開)