- お役立ち記事
- Criteria and points for selecting outsourced manufacturers for advanced board production
月間77,185名の
製造業ご担当者様が閲覧しています*
*2025年2月28日現在のGoogle Analyticsのデータより
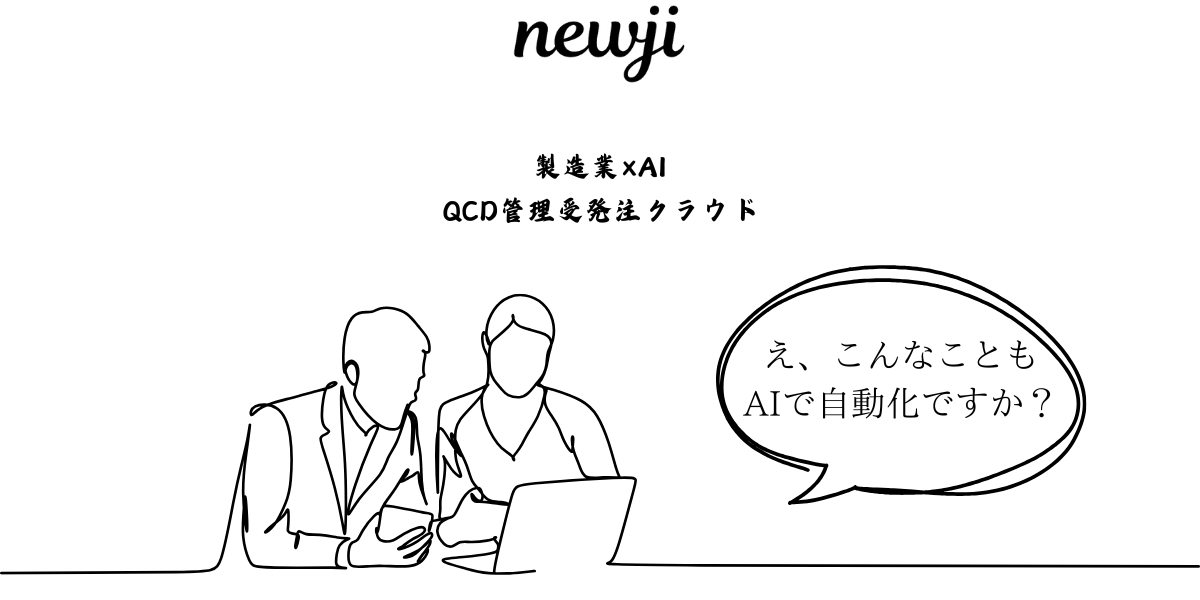
Criteria and points for selecting outsourced manufacturers for advanced board production
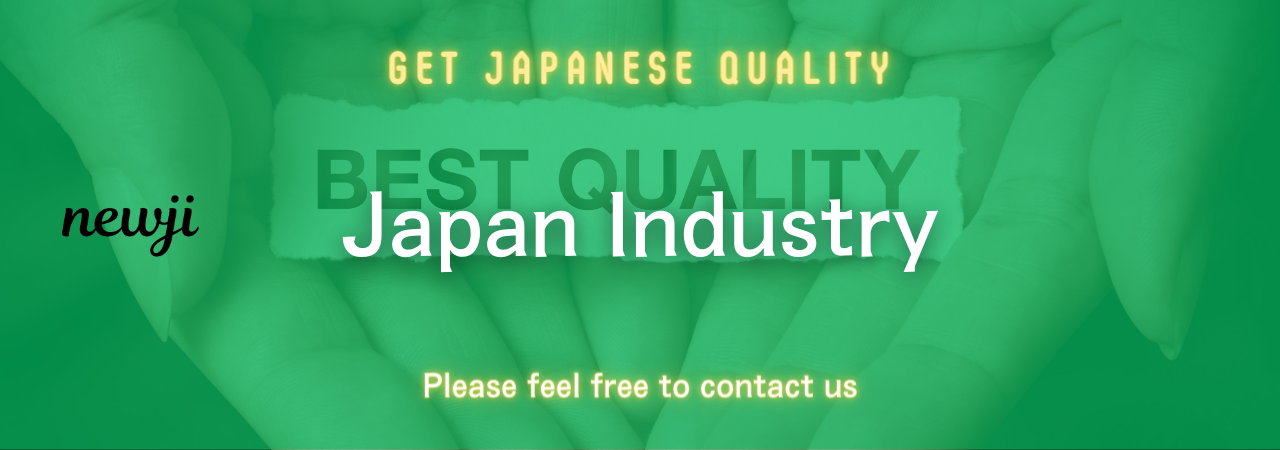
When it comes to advanced board production, choosing the right manufacturer to outsource your needs can be a challenging task. With the growing demand for high-quality and innovative electronic components, the selection of a manufacturing partner becomes crucial. There are several criteria and points that businesses should consider to ensure they select the most suitable partner for their production needs.
目次
Understanding Your Requirements
Before you start looking for a manufacturing partner, it’s essential to have a clear understanding of your production requirements. Start by defining the type of boards you need, the volume of production, and any specific technical specifications. This will help in filtering out manufacturers who lack the necessary capabilities or experience.
Additionally, consider any specialized requirements, such as environmental concerns, compliance with specific industry standards, or unique design needs. Clearly outlining these requirements will not only help you in choosing the right partner but also in communicating effectively with potential manufacturers.
Evaluating Manufacturing Capabilities
The next step involves evaluating the manufacturing capabilities of potential partners. It is vital to ensure that the manufacturer has the technical expertise and equipment necessary to produce advanced boards to your specifications. Consider the following points:
- Technology and Equipment: Does the manufacturer have the latest technology and tools required for PCB production? Modern equipment often leads to more reliable and precise production processes.
- Quality Assurance: What quality control processes do they have in place? A robust quality assurance system is critical to ensuring that the final products meet your standards.
- Experience and Expertise: Look for manufacturers with proven experience in advanced board production. An experienced partner is more likely to anticipate challenges and provide innovative solutions.
- Capacity: Can the manufacturer handle your order volume? Whether you need a small batch or large-scale production, ensure the manufacturer can meet your demands without compromising on quality or deadlines.
Assessing Compliance and Certifications
Ensuring that your manufacturing partner complies with industry standards and holds relevant certifications is crucial. Certifications like ISO 9001, ISO/TS 16949, or IPC standards indicate a commitment to quality and consistency.
Compliance with environmental regulations, such as RoHS (Restriction of Hazardous Substances), is also important, especially if you are producing boards for industries like automotive or healthcare where safety is paramount.
Checking Past Performance and References
Past performance is a critical indicator of future success. Request references and case studies from potential manufacturers. By speaking with previous clients, you can gain insights into their experiences, the quality of service provided, and any challenges they faced.
Don’t hesitate to ask for examples of similar projects they’ve completed in the past. This information can provide a clearer picture of the manufacturer’s capabilities and reliability.
Considering Cost and Value
While cost is an undeniable factor when choosing a manufacturer, it is essential to focus on value rather than just the price. The cheapest option might not always be the best.
Evaluate the total cost of ownership, which includes not only the price per unit but also any potential costs related to rework, quality issues, or delays. A higher initial cost might be justified by superior quality, faster delivery times, or enhanced support services.
It’s beneficial to have open discussions about pricing structures and potential discounts for larger or repeat orders. Transparency in pricing can help build a more trustworthy relationship between you and your manufacturing partner.
Communication and Customer Service
Effective communication is a cornerstone of successful partnerships. The manufacturer should be reachable and responsive to your queries and concerns. Good manufacturers will provide dedicated account managers or customer service representatives to address your needs.
Look for partners who offer proactive communication, such as regular updates on production status and potential issues. Open communication lines help in quickly resolving any challenges that might arise during the production process.
Location and Logistics
The geographical location of your manufacturing partner can influence lead times and shipping costs. While local manufacturers might offer quicker turnaround times and lower shipping costs, overseas options could provide cost advantages.
Consider the logistics involved in shipping and any potential customs issues if dealing with international manufacturers. Ensuring that logistics and supply chain networks are reliable can drastically reduce the risk of delays.
Flexibility and Scalability
Choose a manufacturing partner that can offer flexibility in their production processes. As your business grows, you might need to adjust your production needs.
A manufacturer that can easily scale up or down based on your requirements will be beneficial in the long run. The ability to rapidly respond to changing demands or incorporate design changes efficiently is a valuable asset.
Environmental and Social Responsibility
Finally, consider the environmental and social practices of potential manufacturing partners. Many businesses today prioritize partners who follow sustainable practices and contribute positively to their communities.
Evaluate the manufacturer’s environmental policies, waste management practices, and energy usage. A commitment to corporate social responsibility can be a deciding factor in aligning with your business values.
Careful evaluation of these criteria and points will guide you in selecting the right outsourced manufacturer for your advanced board production. By investing the time and resources into this decision, you set the foundation for a successful manufacturing partnership that meets your business goals and needs.
資料ダウンロード
QCD管理受発注クラウド「newji」は、受発注部門で必要なQCD管理全てを備えた、現場特化型兼クラウド型の今世紀最高の受発注管理システムとなります。
ユーザー登録
受発注業務の効率化だけでなく、システムを導入することで、コスト削減や製品・資材のステータス可視化のほか、属人化していた受発注情報の共有化による内部不正防止や統制にも役立ちます。
NEWJI DX
製造業に特化したデジタルトランスフォーメーション(DX)の実現を目指す請負開発型のコンサルティングサービスです。AI、iPaaS、および先端の技術を駆使して、製造プロセスの効率化、業務効率化、チームワーク強化、コスト削減、品質向上を実現します。このサービスは、製造業の課題を深く理解し、それに対する最適なデジタルソリューションを提供することで、企業が持続的な成長とイノベーションを達成できるようサポートします。
製造業ニュース解説
製造業、主に購買・調達部門にお勤めの方々に向けた情報を配信しております。
新任の方やベテランの方、管理職を対象とした幅広いコンテンツをご用意しております。
お問い合わせ
コストダウンが利益に直結する術だと理解していても、なかなか前に進めることができない状況。そんな時は、newjiのコストダウン自動化機能で大きく利益貢献しよう!
(β版非公開)