- お役立ち記事
- Criteria for deciding between in-house production and outsourcing Cost comparison methods that purchasing departments should know
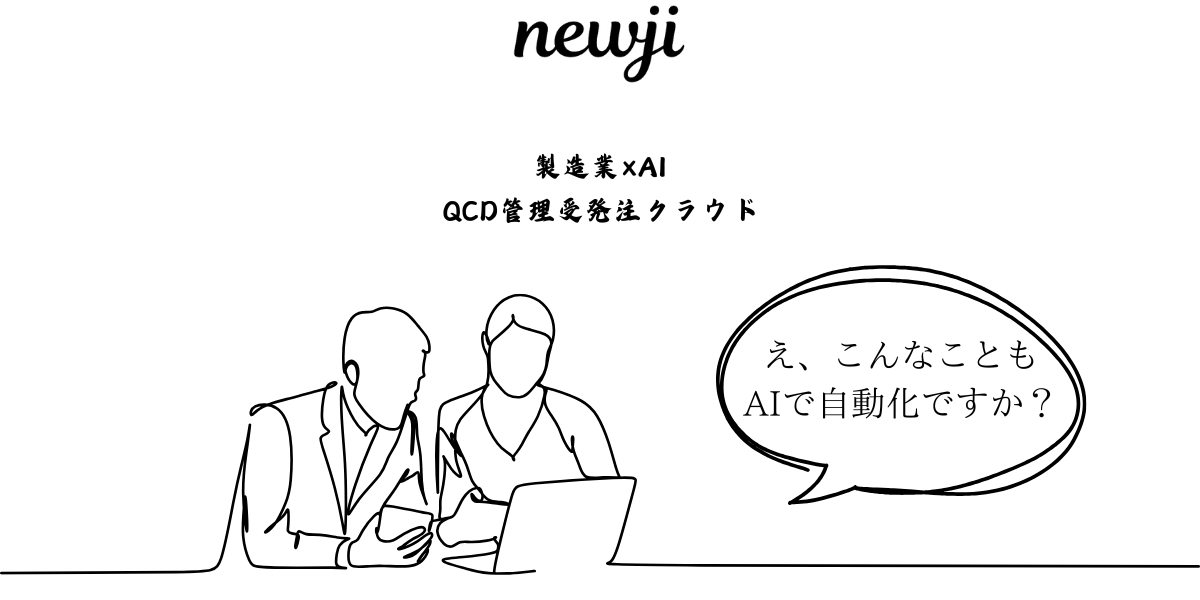
Criteria for deciding between in-house production and outsourcing Cost comparison methods that purchasing departments should know
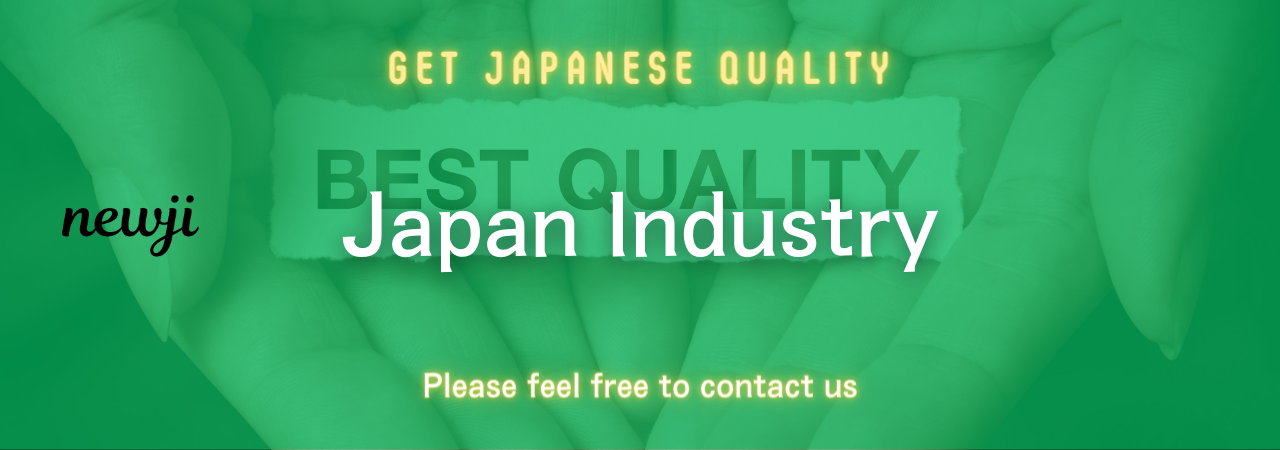
目次
Understanding In-House Production vs. Outsourcing
In today’s dynamic business environment, companies are continually faced with the decision of whether to produce goods and services internally (in-house) or to rely on external suppliers (outsourcing).
This decision can significantly impact a company’s operational efficiency, cost structure, and competitiveness.
Therefore, understanding the criteria for deciding between in-house production and outsourcing is critical for purchasing departments and decision-makers looking to enhance their company’s strategic edge.
Defining In-House Production and Outsourcing
Before delving into the criteria and cost comparison methods, it’s essential to clearly define in-house production and outsourcing.
In-house production involves leveraging a company’s internal resources to design, manufacture, or deliver products and services.
This approach allows companies to maintain direct control over the entire production process, ensuring quality and timeliness.
On the other hand, outsourcing involves delegating certain business functions or processes to external suppliers.
These suppliers specialize in specific areas, offering expertise that your company may not possess internally.
Outsourcing can provide access to specialized skills and potentially lower production costs.
Key Criteria for Decision Making
When deciding between in-house production and outsourcing, several criteria can guide purchasing departments in making informed choices.
1. Cost Efficiency
Cost is often the most critical factor when deciding whether to keep a function in-house or outsource it.
Companies must thoroughly analyze both fixed and variable costs associated with each option.
If outsourcing can offer the same quality at a lower cost, it might be the preferred option.
However, the cost of outsourcing should encompass all aspects, such as supplier selection, contract management, and potential transport or logistics costs.
2. Core Competencies
Companies should assess whether the tasks or processes in question are part of their core competencies.
Core competencies represent what the company does best and are integral to competitive advantage.
If a task is outside your core competency, outsourcing might free up resources to focus on areas where your business excels.
3. Quality Control
Maintaining high-quality standards is crucial for customer satisfaction and brand reputation.
When considering outsourcing, ensure that the potential supplier can meet your quality standards.
If in-house control is required to maintain quality, it may be better to keep the process internal.
4. Flexibility and Scalability
A company’s need for flexibility and scalability can significantly influence the decision between in-house production and outsourcing.
Outsourcing can offer scalability as external suppliers may have the capacity to increase production volume quickly without the need for additional investments in infrastructure.
However, in-house production might provide more flexibility in terms of tailoring solutions to specific customer needs.
5. Risk Management
Evaluating risks associated with both in-house production and outsourcing is necessary for making an informed decision.
Consider potential risks such as supply chain disruptions, dependency on suppliers, and confidentiality concerns.
Maintaining control over sensitive processes or technologies might necessitate in-house production to reduce such risks.
Cost Comparison Methods
Purchasing departments must adopt systematic approaches to compare the costs associated with in-house production and outsourcing.
Here are some methods to consider:
1. Total Cost Analysis
A comprehensive total-cost analysis involves evaluating all direct and indirect costs related to each option.
This includes manufacturing costs, transportation, warehousing, and overhead expenses.
It also involves considering hidden costs such as transition costs, supplier relationship management, and potential loss of in-house expertise.
2. Cost-Benefit Analysis
Cost-benefit analysis involves comparing the projected costs of in-house production with those of outsourcing, weighing them against the anticipated benefits.
This method helps outline the financial implications and the strategic advantages or disadvantages of each option.
Consider long-term benefits such as market responsiveness, process improvements, and innovation potential.
3. Break-Even Analysis
A break-even analysis helps determine the volume at which in-house production becomes more cost-effective than outsourcing, or vice versa.
This method requires careful consideration of fixed and variable costs associated with each option.
A clear understanding of production volumes is essential for making the right decision.
4. Lifecycle Costing
Lifecycle costing takes into account the total cost of ownership over the lifecycle of the product or service.
By assessing the costs associated from production to disposal, companies can make decisions based on the broader economic implications.
This is particularly useful in industries where product longevity and sustainability are crucial.
Conclusion
Choosing between in-house production and outsourcing is a strategic decision that requires careful consideration of numerous factors, including cost efficiency, core competencies, quality control, flexibility, and risk management.
Purchasing departments play a pivotal role in conducting thorough cost comparisons using methods such as total cost analysis, cost-benefit analysis, break-even analysis, and lifecycle costing.
By understanding these criteria and methods, companies can make informed decisions that align with their strategic goals and operational capabilities.
Ultimately, whether opting for in-house production or outsourcing, the overarching objective should be to enhance efficiency, reduce costs, and maintain competitive advantage in the market.
資料ダウンロード
QCD調達購買管理クラウド「newji」は、調達購買部門で必要なQCD管理全てを備えた、現場特化型兼クラウド型の今世紀最高の購買管理システムとなります。
ユーザー登録
調達購買業務の効率化だけでなく、システムを導入することで、コスト削減や製品・資材のステータス可視化のほか、属人化していた購買情報の共有化による内部不正防止や統制にも役立ちます。
NEWJI DX
製造業に特化したデジタルトランスフォーメーション(DX)の実現を目指す請負開発型のコンサルティングサービスです。AI、iPaaS、および先端の技術を駆使して、製造プロセスの効率化、業務効率化、チームワーク強化、コスト削減、品質向上を実現します。このサービスは、製造業の課題を深く理解し、それに対する最適なデジタルソリューションを提供することで、企業が持続的な成長とイノベーションを達成できるようサポートします。
オンライン講座
製造業、主に購買・調達部門にお勤めの方々に向けた情報を配信しております。
新任の方やベテランの方、管理職を対象とした幅広いコンテンツをご用意しております。
お問い合わせ
コストダウンが利益に直結する術だと理解していても、なかなか前に進めることができない状況。そんな時は、newjiのコストダウン自動化機能で大きく利益貢献しよう!
(Β版非公開)