- お役立ち記事
- Cutting-Edge Precision Machining Techniques with NC Lathes
月間76,176名の
製造業ご担当者様が閲覧しています*
*2025年3月31日現在のGoogle Analyticsのデータより
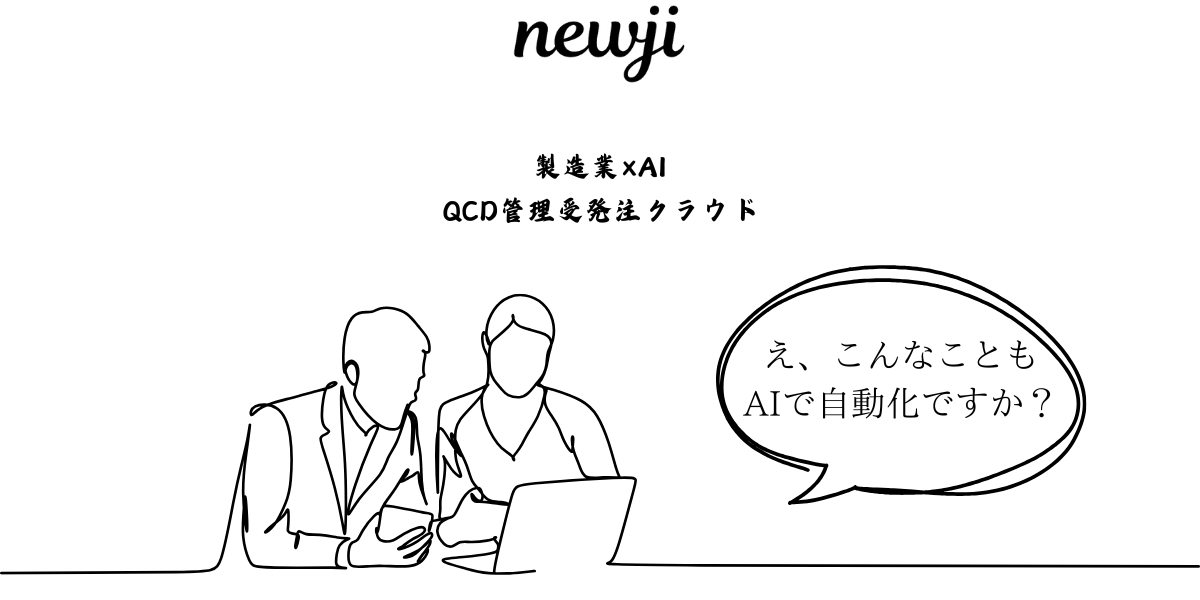
Cutting-Edge Precision Machining Techniques with NC Lathes
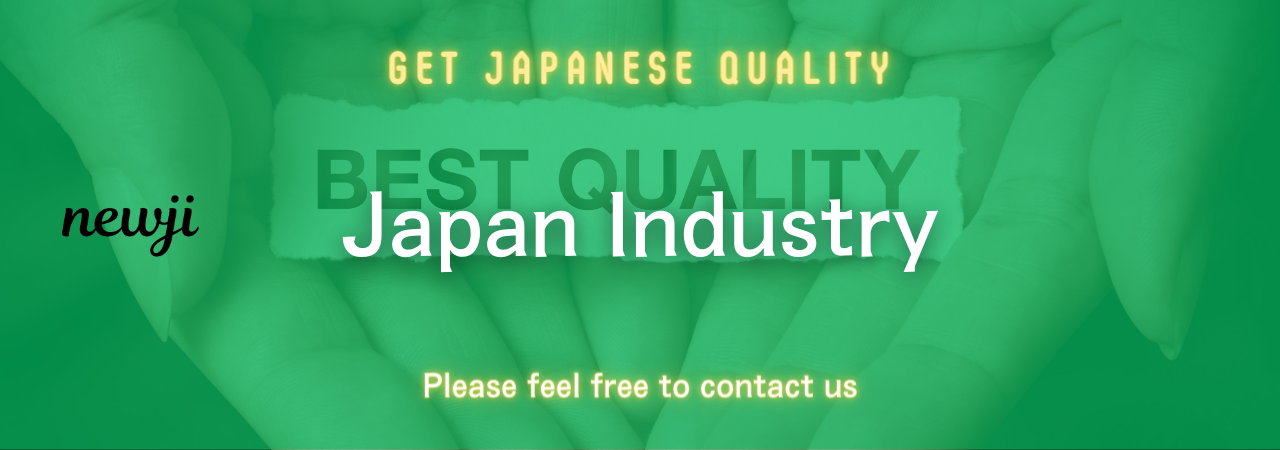
In today’s fast-paced manufacturing world, precision machining is crucial.
Among the many tools used, NC (Numerical Control) lathes stand out due to their incredible accuracy and efficiency.
The advent of advanced precision machining techniques has revolutionized industries and facilitated the creation of highly accurate and complex components.
In this article, we will delve into some of the cutting-edge precision machining techniques used with NC lathes.
目次
Understanding NC Lathes
NC lathes are a staple in the manufacturing industry.
They are used to automate the cutting, drilling, and shaping of materials.
With an NC lathe, a computer program controls the movement of the machinery, ensuring that each cut is perfect and consistent.
This automation reduces human error and increases efficiency, making NC lathes an indispensable tool in modern machining.
NC lathes work with various materials, including metals, plastics, and composites.
They can produce components with incredibly tight tolerances, which is essential for industries like aerospace, automotive, and medical devices, where precision is paramount.
Advanced Techniques in Precision Machining
1. Multi-Axis Machining
Multi-axis machining is a technique where NC lathes operate on multiple axes simultaneously.
Traditional lathes typically operate on two axes, but with advancements, modern NC lathes can work on three, four, or even five axes.
This capability allows for the production of more complex and precise components.
By working on multiple axes, NC lathes can perform various operations without having to reposition the workpiece.
This reduces the time required for production and improves overall accuracy.
2. High-Speed Machining (HSM)
High-Speed Machining (HSM) is another revolutionary technique.
It involves operating NC lathes at much higher speeds than traditional methods.
HSM reduces the time required to produce a component and improves surface finish quality.
This technique also reduces the amount of heat generated during machining, which can improve the longevity of both the cutting tools and the workpiece.
In high-speed machining, the feed rates and spindle speeds are optimized to achieve the highest efficiency.
The reduced cutting forces ensure better dimensional accuracy and surface integrity.
Industries that require high precision and fast production times, such as aerospace and automotive, particularly benefit from HSM.
3. Adaptive Machining
Adaptive machining is a technique in which the NC lathe adjusts its operations based on real-time data.
Sensors monitor various parameters such as cutting forces, temperatures, and vibrations.
This data is then used to modify the machining process on-the-fly, ensuring optimal performance and precision.
This technique is particularly useful when working with materials that have varying properties or when producing complex geometries.
By adjusting in real-time, adaptive machining can compensate for unforeseen issues, reducing the chance of errors and increasing the overall quality of the finished product.
4. Micro-Machining
Micro-machining is an advanced technique used to create extremely small and precise components.
This technique is indispensable for industries requiring miniature parts with exceptionally tight tolerances, such as electronics and medical devices.
In micro-machining, NC lathes are equipped with specialized tools that can handle the fine cuts needed for small parts.
The machinery operates with incredibly high accuracy, often down to a few micrometers.
This level of precision is achieved through stringent control of machine movements and customized tooling.
Benefits of Using Advanced Techniques with NC Lathes
The advent of advanced precision machining techniques brings numerous benefits to the table:
1. Improved Accuracy
The precision offered by advanced techniques like multi-axis machining and high-speed machining is unmatched.
These methods ensure that each component produced meets exact specifications, reducing the need for rework and scrap.
2. Enhanced Efficiency
Techniques such as HSM and adaptive machining significantly reduce production time.
By optimizing various parameters in real-time and operating at higher speeds, NC lathes can produce more components in less time without compromising quality.
3. Cost Savings
Higher efficiency and reduced waste translate to cost savings.
The ability to produce precise components with minimal error reduces material costs and energy consumption.
Additionally, improved tool life through techniques like HSM cuts down on the expenses associated with tool replacements.
4. Versatility
Advanced precision techniques expand the range of materials and component types that NC lathes can handle.
From metals to composites, and from small to large parts, these techniques make NC lathes versatile machines capable of meeting the diverse needs of modern manufacturing.
Future Trends in Precision Machining with NC Lathes
As technology continues to evolve, so does the field of precision machining.
Several emerging trends are set to shape the future of NC lathes and precision techniques:
1. Artificial Intelligence (AI)
Integrating AI with NC lathes will further improve their capabilities.
AI algorithms can analyze enormous amounts of data to optimize machining processes, predict tool wear, and detect potential issues before they occur.
This will lead to even higher levels of precision and efficiency.
2. Internet of Things (IoT)
IoT technology can connect NC lathes to a network of devices, facilitating better monitoring, control, and data analysis.
This connectivity can improve maintenance schedules, reduce downtime, and enhance overall productivity.
3. Additive Manufacturing Integration
The combination of additive manufacturing (3D printing) and precision machining techniques can lead to innovative production methods.
NC lathes can be used for final machining on 3D printed components, ensuring they meet the required tolerances and surface finishes.
Conclusion
The integration of advanced precision machining techniques with NC lathes has significantly transformed the manufacturing landscape.
From multi-axis machining to adaptive and high-speed machining, these techniques offer unprecedented accuracy, efficiency, and versatility.
By staying abreast of emerging trends such as AI, IoT, and additive manufacturing, the future of precision machining looks promising.
Companies that embrace these advanced techniques will undoubtedly maintain a competitive edge and continue to meet the growing demands of modern industries.
資料ダウンロード
QCD管理受発注クラウド「newji」は、受発注部門で必要なQCD管理全てを備えた、現場特化型兼クラウド型の今世紀最高の受発注管理システムとなります。
ユーザー登録
受発注業務の効率化だけでなく、システムを導入することで、コスト削減や製品・資材のステータス可視化のほか、属人化していた受発注情報の共有化による内部不正防止や統制にも役立ちます。
NEWJI DX
製造業に特化したデジタルトランスフォーメーション(DX)の実現を目指す請負開発型のコンサルティングサービスです。AI、iPaaS、および先端の技術を駆使して、製造プロセスの効率化、業務効率化、チームワーク強化、コスト削減、品質向上を実現します。このサービスは、製造業の課題を深く理解し、それに対する最適なデジタルソリューションを提供することで、企業が持続的な成長とイノベーションを達成できるようサポートします。
製造業ニュース解説
製造業、主に購買・調達部門にお勤めの方々に向けた情報を配信しております。
新任の方やベテランの方、管理職を対象とした幅広いコンテンツをご用意しております。
お問い合わせ
コストダウンが利益に直結する術だと理解していても、なかなか前に進めることができない状況。そんな時は、newjiのコストダウン自動化機能で大きく利益貢献しよう!
(β版非公開)