- お役立ち記事
- Cycle Time Reduction Techniques in Injection Molding: Tips for Productivity Improvement
Cycle Time Reduction Techniques in Injection Molding: Tips for Productivity Improvement
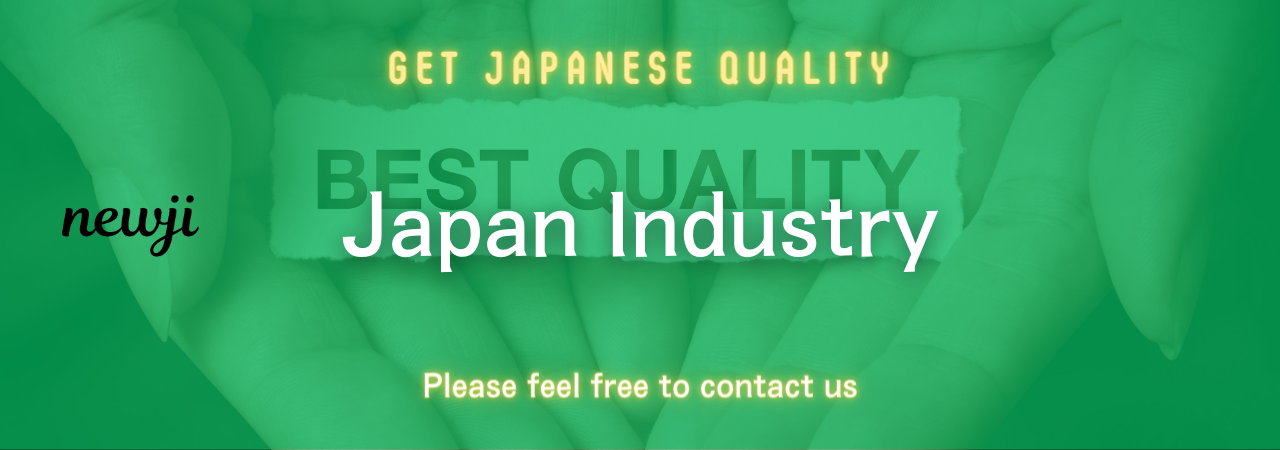
Injection molding is a widely used manufacturing process that can produce complex plastic parts with high precision and repeatability.
One of the key factors in optimizing injection molding operations is reducing cycle time.
Cycle time directly influences production efficiency, costs, and overall productivity.
In this article, we’ll explore various techniques for reducing cycle time in injection molding, helping you achieve higher throughput and improved profitability.
目次
Understanding Injection Molding Cycle Time
Cycle time in injection molding refers to the total time taken to complete one production cycle, including mold closing, material injection, cooling, mold opening, and part ejection.
Each phase of the cycle contributes to the overall time, impacting the speed and efficiency of the production process.
Reducing cycle time involves optimizing each of these phases to minimize idle time and maximize productivity.
Optimizing Mold Design
Effective mold design is crucial for reducing cycle time without compromising part quality.
Several strategies can be employed to achieve this:
Use of Hot Runners
Hot runner systems keep the plastic material in a molten state throughout the injection process, eliminating the need for runners and sprues that solidify and waste material.
By maintaining a consistent temperature, hot runners reduce injection and cooling time, contributing significantly to cycle time reduction.
Improved Cooling Channels
Efficient cooling is essential for reducing cycle time.
Incorporating conformal cooling channels within the mold, which follow the contours of the part, ensures even and faster cooling.
This can greatly reduce the cooling phase, which typically takes up a significant portion of the cycle time.
High-Speed Injection Molding
Adopting high-speed injection molding techniques can accelerate the process.
This involves using advanced injection molding machines capable of faster injection speeds, higher clamping forces, and quicker response times.
These machines help in shortening the injection and packing phases, thus reducing the overall cycle time.
Optimizing Material Selection and Handling
The choice of material and its handling can impact the cycle time tremendously.
Here are some ways to optimize this aspect:
Using Fast-Cooling Materials
Selecting materials with faster cooling rates can decrease the cooling time within the mold.
Materials like certain thermoplastics cool quicker than others, making them ideal for high-speed production environments.
Proper Material Conditioning
Pre-drying and conditioning materials before injection can reduce cycle time by ensuring consistent flow and reducing the likelihood of defects caused by moisture.
This practice leads to smoother injection and reduced need for extended cooling times.
Advanced Process Control
Implementing advanced process control techniques can enhance the efficiency of the injection molding cycle.
Consider the following methods:
Scientific Molding
Scientific molding involves using data and analytics to optimize the injection molding process.
By closely monitoring variables like temperature, pressure, and flow rates, you can make precise adjustments that minimize cycle time and improve part quality.
Automation and Robotics
Integrating automation and robotic systems can significantly reduce cycle time by streamlining the handling of molds and parts.
Robots can quickly remove finished parts, insert molds, and perform secondary operations, all of which reduce manual intervention and idle time.
Maintenance and Mold Care
Regular maintenance and proper care of molds and machinery are essential for efficient cycle time management.
Neglecting maintenance can lead to unexpected downtime and extended cycle times.
Regular Mold Inspection
Conduct routine inspections to identify and address any issues such as wear and tear, clogging of cooling channels, or misalignment.
Addressing these issues promptly ensures smooth operation and quicker cycles.
Lubrication and Cleaning
Keep molds and machine components well-lubricated and clean to prevent any malfunction or delay in the production process.
Proper lubrication ensures smooth opening and closing of molds, reducing cycle time.
Continuous Improvement and Monitoring
To achieve long-term cycle time reduction, adopt a culture of continuous improvement and regular monitoring.
Employee Training
Ensure that operators and technicians are well-trained in the latest techniques and technologies for cycle time reduction.
Knowledgeable staff can quickly identify and address any issues that may extend cycle time.
Data Analysis
Utilize data from your injection molding processes to identify trends and potential areas for improvement.
Employing software tools for real-time monitoring and analysis can provide valuable insights for continuous optimization efforts.
Reducing cycle time in injection molding is a multifaceted approach that involves optimizing mold design, material handling, process control, maintenance, and continuous improvement.
Implementing these techniques can lead to higher throughput, lower production costs, and improved overall productivity.
By focusing on these aspects, manufacturers can stay competitive and meet the increasing demands of the market.
資料ダウンロード
QCD調達購買管理クラウド「newji」は、調達購買部門で必要なQCD管理全てを備えた、現場特化型兼クラウド型の今世紀最高の購買管理システムとなります。
ユーザー登録
調達購買業務の効率化だけでなく、システムを導入することで、コスト削減や製品・資材のステータス可視化のほか、属人化していた購買情報の共有化による内部不正防止や統制にも役立ちます。
NEWJI DX
製造業に特化したデジタルトランスフォーメーション(DX)の実現を目指す請負開発型のコンサルティングサービスです。AI、iPaaS、および先端の技術を駆使して、製造プロセスの効率化、業務効率化、チームワーク強化、コスト削減、品質向上を実現します。このサービスは、製造業の課題を深く理解し、それに対する最適なデジタルソリューションを提供することで、企業が持続的な成長とイノベーションを達成できるようサポートします。
オンライン講座
製造業、主に購買・調達部門にお勤めの方々に向けた情報を配信しております。
新任の方やベテランの方、管理職を対象とした幅広いコンテンツをご用意しております。
お問い合わせ
コストダウンが利益に直結する術だと理解していても、なかなか前に進めることができない状況。そんな時は、newjiのコストダウン自動化機能で大きく利益貢献しよう!
(Β版非公開)