- お役立ち記事
- Cylindrical gear design method and its application to reduce gear noise and improve strength
月間76,176名の
製造業ご担当者様が閲覧しています*
*2025年3月31日現在のGoogle Analyticsのデータより
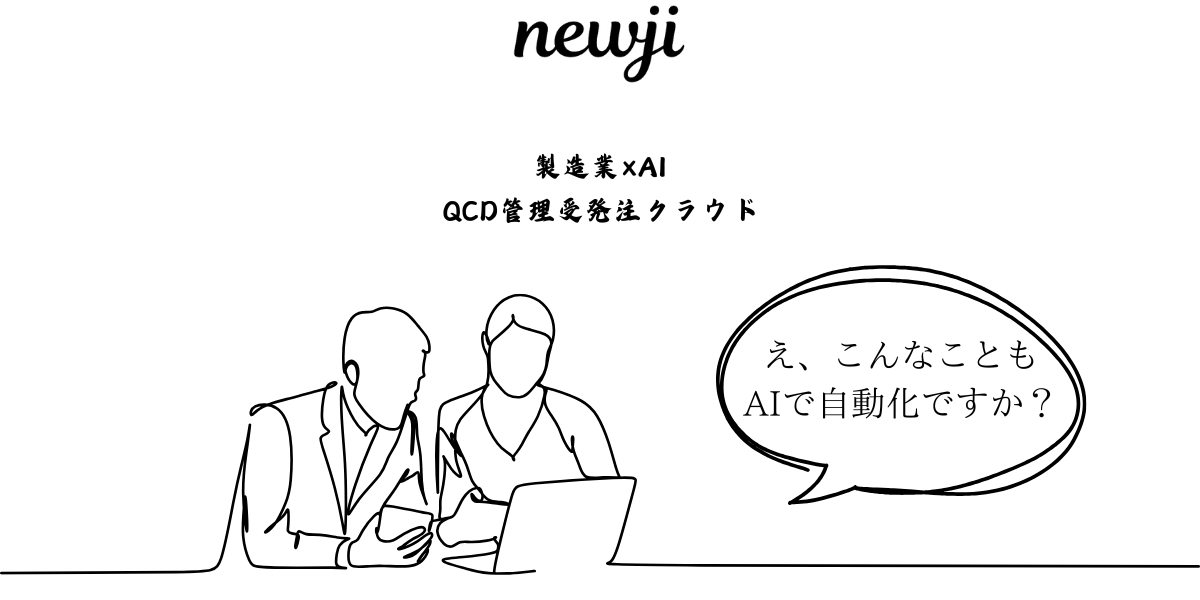
Cylindrical gear design method and its application to reduce gear noise and improve strength
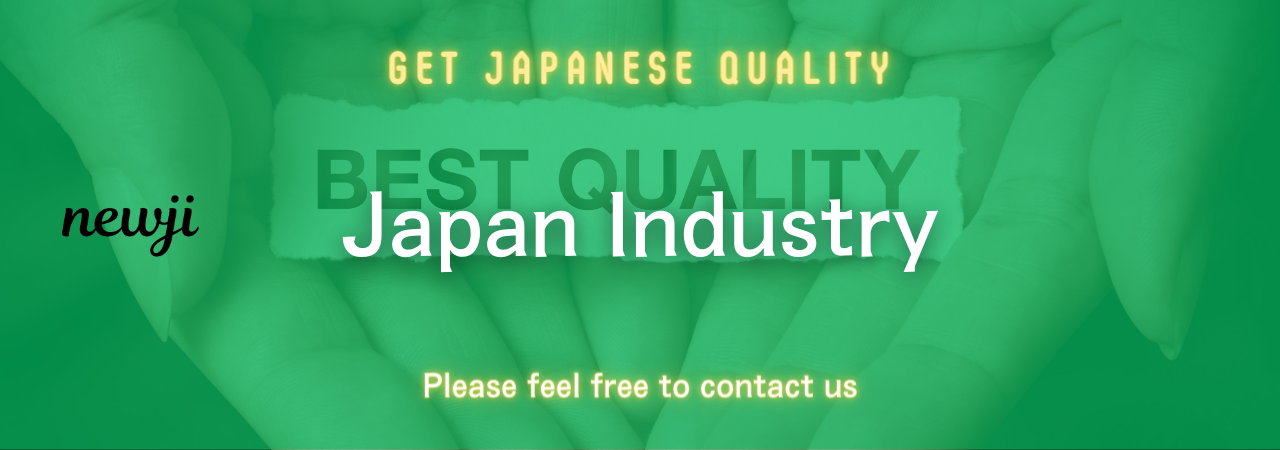
目次
Understanding Cylindrical Gear Design
Cylindrical gears are essential in various mechanical systems, transmitting power and motion between shafts.
These gears come in different forms, such as spur and helical gears, each suited to specific applications.
The process of designing cylindrical gears involves multiple considerations, ensuring their functionality and longevity in machines.
The design of cylindrical gears focuses primarily on the geometry of the teeth, which are responsible for transferring motion efficiently.
The two main types of cylindrical gears—spur and helical—each present unique design challenges and opportunities.
Spur gears feature straight teeth and are typically used in lower-speed applications due to their simplicity and ease of production.
Helical gears, on the other hand, have angled teeth which allow for smoother and quieter operation at higher speeds.
The choice between these gear types significantly impacts the gear’s performance and its application.
Key Considerations in Gear Design
Designing cylindrical gears requires a comprehensive understanding of several factors.
Firstly, material selection is critical in ensuring the gears can withstand the forces they encounter.
Common materials include steel, brass, and plastic, each offering different properties like strength, durability, and noise absorption.
Another crucial aspect is the gear ratio, which determines the relationship between the input and output speeds of the gears.
The gear ratio affects the efficiency and performance of the entire mechanical system.
Additionally, the pitch of the gear—defined as the distance between identical points on adjacent teeth—must be carefully calculated.
The pitch impacts the gear’s ability to transfer power smoothly and quietly.
Finally, consideration of the gear’s operating conditions, such as load, speed, and environment, is vital in the design process.
Designers must account for these factors to prevent gear failure and ensure optimal performance.
Reducing Gear Noise
Gear noise can be a significant issue in mechanical systems, affecting comfort and efficiency.
Designers employ various strategies to minimize this noise, enhancing the overall performance of gears.
One effective method is the use of helical gears instead of spur gears.
The angled teeth of helical gears engage more gradually than the straight teeth of spur gears, resulting in quieter operation.
Additionally, precision manufacturing techniques, such as grinding and lapping, can produce smoother gear surfaces, reducing noise during operation.
Material choice also plays a role in noise reduction.
Materials with vibration-dampening properties can help minimize the sound generated by gear operation.
Furthermore, modifications in gear tooth profile, such as using asymmetric teeth, can improve the distribution of forces during operation, thereby reducing noise.
Improving Gear Strength
Ensuring the strength of cylindrical gears is crucial for their longevity and reliability.
Several methods can be applied to enhance the strength of these gears.
Firstly, selecting high-strength materials, such as alloy steels, can greatly improve gear resilience against wear and tear.
Another approach is surface hardening through techniques like carburizing or nitriding.
These processes increase the surface hardness of the gears, making them more resistant to wear.
Optimizing the gear design itself can also contribute to increased strength.
This includes refining the gear geometry to distribute loads more evenly across the teeth.
Additionally, careful control of the manufacturing process helps prevent defects that could compromise gear strength.
Applications of Cylindrical Gear Design
Cylindrical gears are utilized in countless applications across various industries.
In the automotive sector, these gears are critical in transmission systems, enabling vehicles to operate efficiently at different speeds.
Industrial machinery often relies on cylindrical gears to transfer motion and power between machinery parts.
Furthermore, cylindrical gears find applications in the aerospace industry, where precision and reliability are paramount.
In each of these applications, reducing gear noise and improving strength are continuous priorities to enhance system performance and durability.
Future Trends in Gear Design
As technology progresses, the design and application of cylindrical gears continue to evolve.
Trends point towards the integration of advanced materials, such as composites, which offer unique benefits like reduced weight and increased strength.
Furthermore, the advent of digital design tools and simulations allows for more precise and efficient gear design processes.
These tools help engineers predict gear performance and optimize designs before physical production, saving time and resources.
The focus on sustainability also influences gear design, with efforts to create more energy-efficient systems reducing material waste.
Overall, the future of cylindrical gear design promises increased efficiency, performance, and environmental considerations.
資料ダウンロード
QCD管理受発注クラウド「newji」は、受発注部門で必要なQCD管理全てを備えた、現場特化型兼クラウド型の今世紀最高の受発注管理システムとなります。
ユーザー登録
受発注業務の効率化だけでなく、システムを導入することで、コスト削減や製品・資材のステータス可視化のほか、属人化していた受発注情報の共有化による内部不正防止や統制にも役立ちます。
NEWJI DX
製造業に特化したデジタルトランスフォーメーション(DX)の実現を目指す請負開発型のコンサルティングサービスです。AI、iPaaS、および先端の技術を駆使して、製造プロセスの効率化、業務効率化、チームワーク強化、コスト削減、品質向上を実現します。このサービスは、製造業の課題を深く理解し、それに対する最適なデジタルソリューションを提供することで、企業が持続的な成長とイノベーションを達成できるようサポートします。
製造業ニュース解説
製造業、主に購買・調達部門にお勤めの方々に向けた情報を配信しております。
新任の方やベテランの方、管理職を対象とした幅広いコンテンツをご用意しております。
お問い合わせ
コストダウンが利益に直結する術だと理解していても、なかなか前に進めることができない状況。そんな時は、newjiのコストダウン自動化機能で大きく利益貢献しよう!
(β版非公開)