- お役立ち記事
- Daily inspections and equipment maintenance that should be practiced at the site to improve operating rates
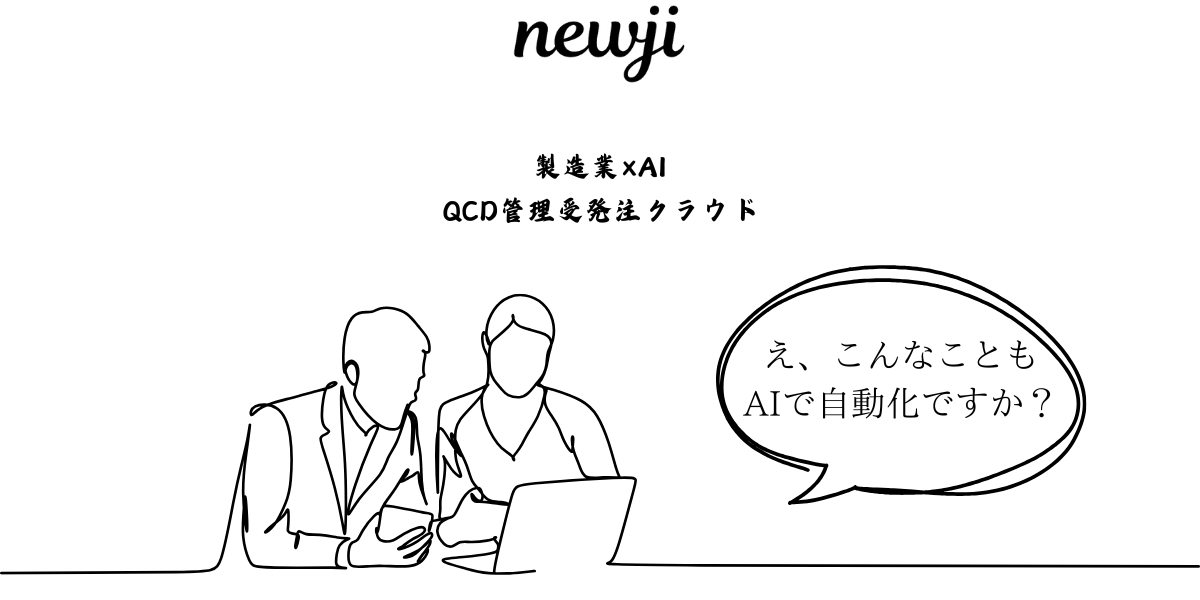
Daily inspections and equipment maintenance that should be practiced at the site to improve operating rates
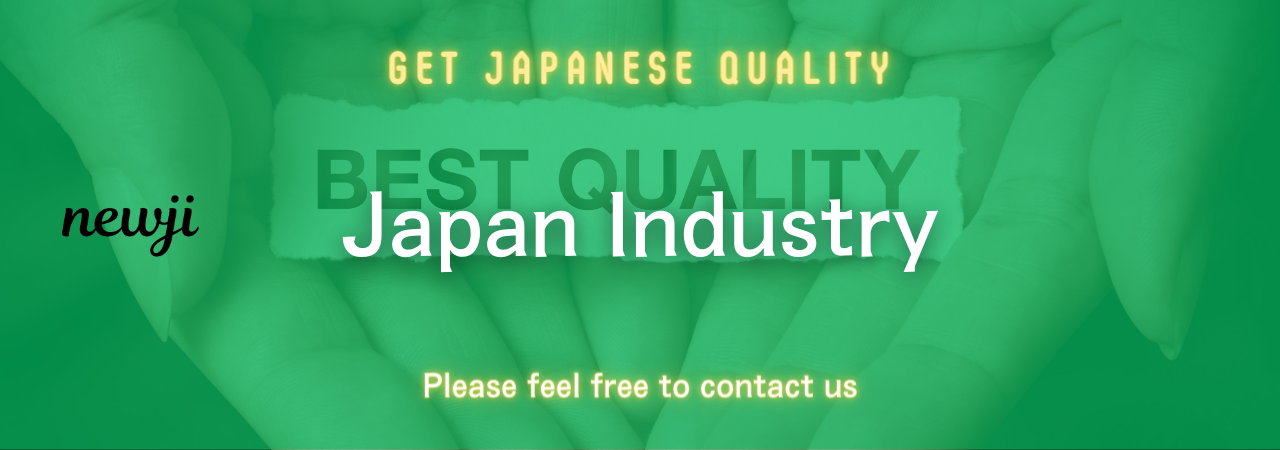
目次
Introduction to Daily Inspections and Equipment Maintenance
In any industry, maintaining operational efficiency is crucial for achieving optimal productivity.
A key factor in ensuring this is the regular maintenance and inspection of equipment.
Daily inspections and preventative maintenance practices are essential steps that can significantly enhance the operating rates of machinery on site.
Whether you’re working in manufacturing, construction, or any field that relies on heavy machinery, incorporating a routine check can make a huge difference.
The Importance of Daily Inspections
Daily inspections are a proactive approach to identify potential issues before they escalate into major problems.
By conducting checks regularly, operators can spot minor faults early, reducing the risk of breakdowns that can halt production.
These inspections lead to increased machinery life, ensuring components are in proper working order.
This not only minimizes downtime but also extends the longevity of the equipment.
Regular checks also ensure compliance with safety regulations and industry standards, protecting workers from accidents due to equipment failures.
Furthermore, a well-maintained machine operates more efficiently, reducing fuel consumption and improving overall performance.
Key Components to Check During Daily Inspections
When performing daily inspections, there are essential components and areas that should be closely examined:
1. **Fluid Levels:** Check engine oil, hydraulic fluid, coolant, and other essential fluids.
Adequate fluid levels are critical for smooth operation.
2. **Brakes and Controls:** Ensure that all control systems are functioning without delay.
The brakes should be checked for responsiveness and efficiency.
3. **Belts and Hoses:** Inspect for any signs of cracking or wear.
These components can lead to significant issues if they fail during operation.
4. **Tires and Tracks:** Check the condition and pressure of the tires or tracks.
Proper inflation and wear patterns are essential for stability and function.
5. **Attachments and Tools:** If the machinery uses attachments, verify they are securely connected and fully functional.
6. **Electrical Systems:** Test lights, sensors, and any electrical components for proper operation.
Effective Equipment Maintenance Practices
Incorporating comprehensive maintenance protocols is vital for the operational health of machinery.
Effective maintenance involves not just reactive repairs but preventative measures that keep equipment in peak condition.
Creating a Maintenance Schedule
A well-structured maintenance schedule is an indispensable tool for maximizing operating rates.
1. **Routine Check-ups:** Set intervals for basic inspections depending on equipment usage and manufacturer recommendations.
These checks should involve more detailed inspections than the daily scrutiny.
2. **Component Replacement:** Components have specific life expectancies.
Replace them as recommended by the manufacturer to prevent unexpected failures.
3. **Lubrication:** Ensuring all moving parts have adequate lubrication reduces friction and wear.
Regular greasing is essential for parts like bearings and joints.
4. **Calibration and Adjustments:** Machines need adjustments to maintain precision.
Regular calibration ensures that equipment meets performance standards.
5. **Cleaning:** Keeping machinery clean prevents the build-up of debris that can impede operation.
It also allows for easier inspection of parts.
Training and Documentation
Training operators and technicians on the importance of inspections and maintenance practices ensures that the tasks are performed correctly.
1. **Train Operators:** Operators must be familiar with the machinery they handle.
Regularly update them on new procedures or changes to existing equipment.
2. **Document Procedures:** Keep detailed records of all inspections and maintenance activities.
Documentation helps with scheduling, trend analysis, and planning for future maintenance.
3. **Foster a Maintenance Culture:** Encourage a culture where maintenance is seen as a critical part of operations rather than a reaction to issues.
This mindset can significantly enhance the effectiveness of maintenance programs.
Benefits of Regular Inspections and Maintenance
The adoption of rigorous inspection and maintenance protocols has numerous advantages.
1. **Reduced Downtime:** Regular checks decrease the likelihood of unexpected failures, minimizing stoppages and downtime.
2. **Cost Savings:** Preventative maintenance is generally more cost-effective than emergency repairs.
Keeping equipment running smoothly also helps avoid the costly need for early replacement.
3. **Improved Safety:** Ensuring all systems operate correctly improves safety for the operators and on-site personnel.
4. **Asset Value Retention:** Proper care retains the value of machinery.
This is beneficial for asset management and potential resale or trade-in value.
5. **Environmental Impact:** Well-maintained machines are energy-efficient and emit fewer pollutants.
Conclusion
Daily inspections and routine maintenance of equipment are not just optional practices but are essential for any industry dependent on machinery.
By investing time and resources into regular checks and maintenance, companies can significantly enhance operating rates, ensuring optimal production efficiency.
Incorporating these practices leads to sustained operational success, contributing to a safer and more productive work environment.
Remember, the consistency and thoroughness of these practices ultimately determine their effectiveness.
So, ensure you develop and adhere to a strategic maintenance plan tailored to your specific operational needs.
資料ダウンロード
QCD調達購買管理クラウド「newji」は、調達購買部門で必要なQCD管理全てを備えた、現場特化型兼クラウド型の今世紀最高の購買管理システムとなります。
ユーザー登録
調達購買業務の効率化だけでなく、システムを導入することで、コスト削減や製品・資材のステータス可視化のほか、属人化していた購買情報の共有化による内部不正防止や統制にも役立ちます。
NEWJI DX
製造業に特化したデジタルトランスフォーメーション(DX)の実現を目指す請負開発型のコンサルティングサービスです。AI、iPaaS、および先端の技術を駆使して、製造プロセスの効率化、業務効率化、チームワーク強化、コスト削減、品質向上を実現します。このサービスは、製造業の課題を深く理解し、それに対する最適なデジタルソリューションを提供することで、企業が持続的な成長とイノベーションを達成できるようサポートします。
オンライン講座
製造業、主に購買・調達部門にお勤めの方々に向けた情報を配信しております。
新任の方やベテランの方、管理職を対象とした幅広いコンテンツをご用意しております。
お問い合わせ
コストダウンが利益に直結する術だと理解していても、なかなか前に進めることができない状況。そんな時は、newjiのコストダウン自動化機能で大きく利益貢献しよう!
(Β版非公開)