- お役立ち記事
- Damage countermeasures for rolling bearings, life prediction, and application to diagnostic technology
月間77,185名の
製造業ご担当者様が閲覧しています*
*2025年2月28日現在のGoogle Analyticsのデータより
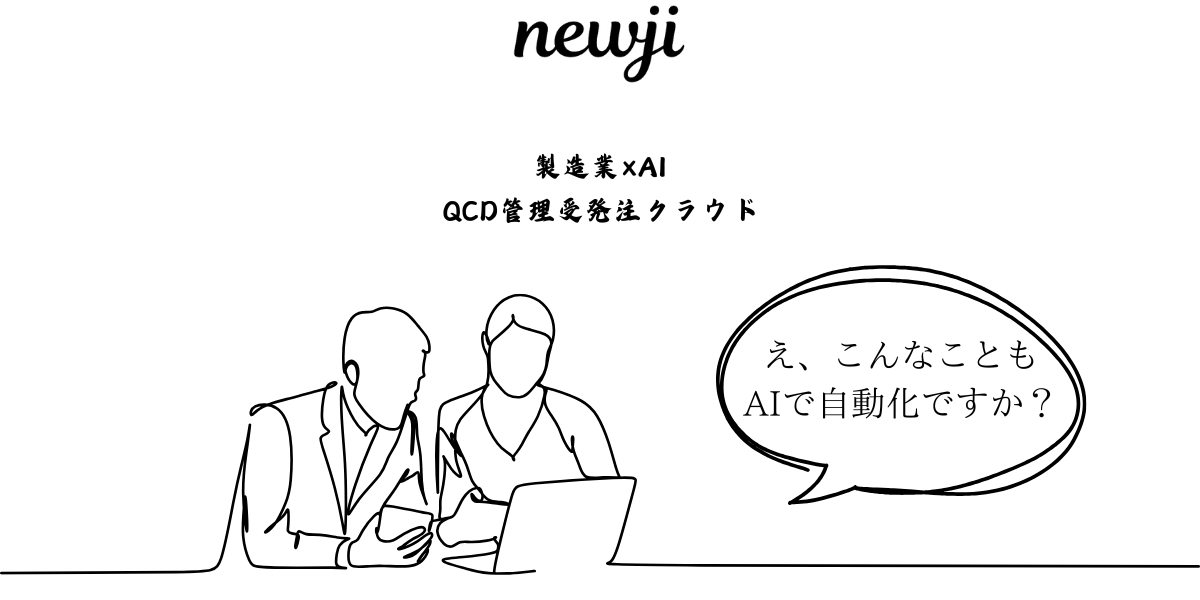
Damage countermeasures for rolling bearings, life prediction, and application to diagnostic technology
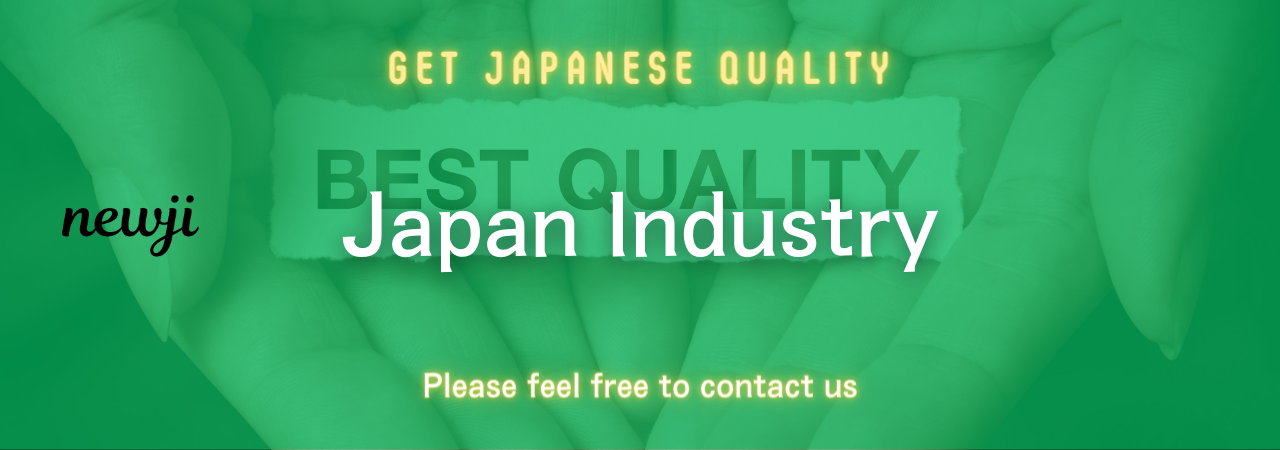
目次
Understanding Rolling Bearings
Rolling bearings are essential components in a wide range of mechanical systems, playing a critical role in reducing friction, supporting loads, and ensuring smooth operation of machinery.
They consist of a series of balls or rollers sandwiched between two concentric rings, allowing the inner and outer rings to move smoothly over each other with minimal resistance.
Given their pivotal role in countless applications, from industrial machinery to automotive engines, ensuring their reliability and longevity is paramount.
Common Damage and Failures in Rolling Bearings
While rolling bearings are designed to last for thousands of hours, they are not immune to damage and failure.
Understanding the types of damage that can occur can help in taking preventive action.
Common types of damage include:
– **Fatigue Failure:** Often results from repeated stress over time.
This wears down the material and can lead to spalling, where pieces of the bearing surface flake off.
– **Contamination:** Dirt, dust, or debris can infiltrate the bearing assembly, causing abrasions and impacting performance.
– **Corrosion:** Exposure to moisture or corrosive substances can cause rust, which degrades the surfaces of the bearing.
– **Overheating:** Excessive heat can result from inadequate lubrication or excessive loads, leading to the breakdown of bearing material.
– **Misalignment:** Incorrect installation or external forces can misalign bearings, causing uneven distribution of load and stress concentration.
Damage Countermeasures for Rolling Bearings
To maximize the lifespan of rolling bearings, several measures can be implemented to mitigate the risk of damage:
– **Regular Maintenance:** Establishing a routine inspection schedule is one of the easiest ways to detect potential issues before they become significant problems.
This includes checking for signs of wear and tear, ensuring proper lubrication, and clean conditions.
– **Adequate Lubrication:** Lubrication reduces friction and wear on the surfaces of the bearings.
Choosing the right lubricant is crucial, based on the operating environment and load conditions.
It’s also important to monitor and replace lubricants regularly to maintain their efficacy.
– **Proper Installation:** Incorrect installation can lead to a host of problems, including misalignment and undue stress on the bearing.
Using appropriate tools and following installation guidelines can help prevent these issues.
– **Seal Solutions:** Effective sealing can protect bearings from contamination by dust and dirt.
Seals should be checked regularly for integrity and replaced if damaged.
– **Temperature Control:** Monitoring temperature is essential, as overheating can quickly lead to damage.
Cooling mechanisms or heat-shields can be implemented in environments with high thermal loads.
Predicting Rolling Bearing Life
Predicting the lifespan of a rolling bearing involves understanding the load parameters it will experience during its operation.
A widely used method is the L10 life calculation, which estimates the number of revolutions or hours at a particular speed that 90% of a sufficiently large group of identical bearings will complete before the first sign of metal fatigue appears.
Factors influencing bearing life prediction include:
– **Load Magnitude and Type:** Both the size and type (compressive, tensile, axial, etc.) of the load affect bearing life.
Bearings under higher loads typically have shorter lifespans.
– **Operating Speed:** Increased speeds can reduce bearing life due to added centrifugal forces.
– **Environmental Conditions:** Harsh environments, like exposure to contaminants or extreme temperatures, can accelerate wear.
– **Material Quality:** High-quality materials provide greater resistance to wear and fatigue, extending bearing life.
Advances in Predictive Technologies
With advances in technology, predictive maintenance for rolling bearings has become more sophisticated.
Techniques such as vibration analysis, thermal imaging, and sound diagnostics enable early detection of issues, often even before they manifest as physical damage.
– **Vibration Analysis:** Changes in vibration patterns can indicate bearing wear or imbalance.
This non-invasive method allows for real-time monitoring of machinery, enabling quick response to abnormalities.
– **Thermal Imaging:** An increase in temperature often signals a lubrication problem or misalignment.
Thermal imaging cameras can detect these heat anomalies, allowing for prompt corrective action.
– **Acoustic Emission:** High-frequency sounds emitted by bearings can be monitored to detect the initiation of cracks or deformations.
Incorporating these technologies into maintenance strategies can significantly reduce downtime and repair costs, ensuring that bearings operate efficiently throughout their expected lifespan.
Application of Diagnostic Technology
The application of diagnostic technology in bearing maintenance is a game-changer for industries reliant on rotating machinery.
By integrating smart sensors and real-time data analytics, companies can predict bearing failures before they occur, thus avoiding costly shutdowns.
– **Smart Sensors:** Install sensors on machinery to collect data on parameters such as vibration, temperature, and noise levels.
These sensors provide continuous monitoring and feeding data into a centralized system for analysis.
– **Data Analytics and Machine Learning:** With the data acquired from smart sensors, machine learning algorithms can be applied to predict future failures.
By training algorithms on historical data, patterns leading to failures can be detected early, allowing for timely intervention.
– **Remote Monitoring Systems:** Utilize cloud-based platforms to allow for the remote analysis of bearings’ health.
This approach ensures that even geographically dispersed operations are consistently monitored and maintained.
In conclusion, the importance of effective damage countermeasures, accurate life prediction, and the application of diagnostic technologies cannot be understated in the management of rolling bearings.
These practices not only enhance reliability and performance but also reduce operational costs and extend the useful life of machinery.
Embracing technology and implementing comprehensive maintenance programs are essential steps toward achieving optimal performance in any sector relying on rotating equipments.
資料ダウンロード
QCD管理受発注クラウド「newji」は、受発注部門で必要なQCD管理全てを備えた、現場特化型兼クラウド型の今世紀最高の受発注管理システムとなります。
ユーザー登録
受発注業務の効率化だけでなく、システムを導入することで、コスト削減や製品・資材のステータス可視化のほか、属人化していた受発注情報の共有化による内部不正防止や統制にも役立ちます。
NEWJI DX
製造業に特化したデジタルトランスフォーメーション(DX)の実現を目指す請負開発型のコンサルティングサービスです。AI、iPaaS、および先端の技術を駆使して、製造プロセスの効率化、業務効率化、チームワーク強化、コスト削減、品質向上を実現します。このサービスは、製造業の課題を深く理解し、それに対する最適なデジタルソリューションを提供することで、企業が持続的な成長とイノベーションを達成できるようサポートします。
製造業ニュース解説
製造業、主に購買・調達部門にお勤めの方々に向けた情報を配信しております。
新任の方やベテランの方、管理職を対象とした幅広いコンテンツをご用意しております。
お問い合わせ
コストダウンが利益に直結する術だと理解していても、なかなか前に進めることができない状況。そんな時は、newjiのコストダウン自動化機能で大きく利益貢献しよう!
(β版非公開)