- お役立ち記事
- Damage countermeasures, life prediction and diagnostic technology for rolling bearings
月間77,185名の
製造業ご担当者様が閲覧しています*
*2025年2月28日現在のGoogle Analyticsのデータより
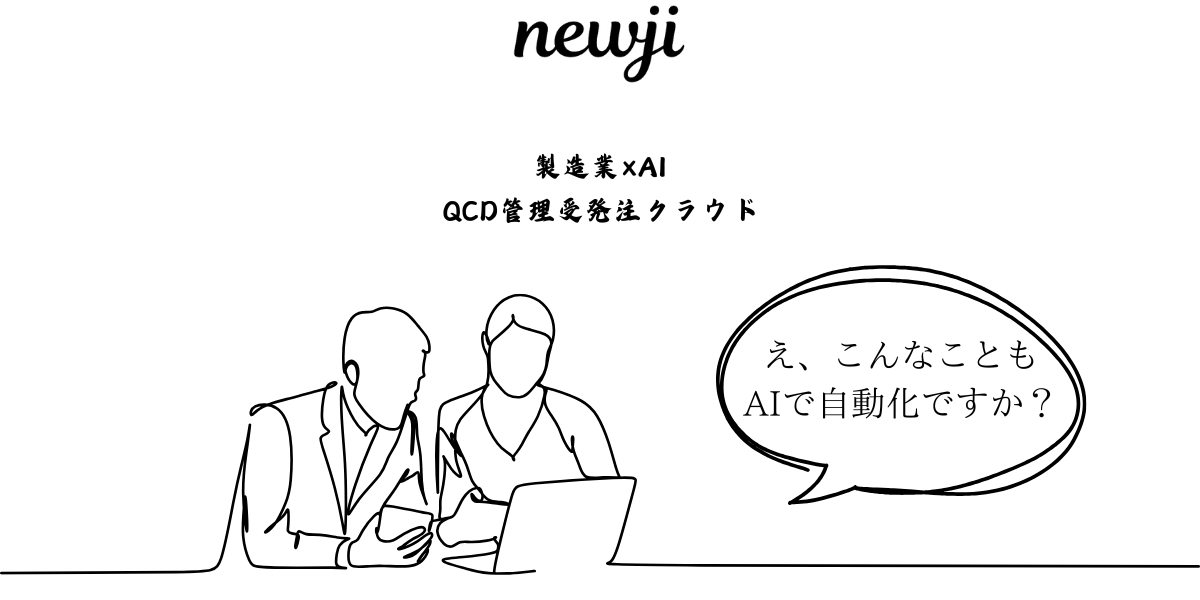
Damage countermeasures, life prediction and diagnostic technology for rolling bearings
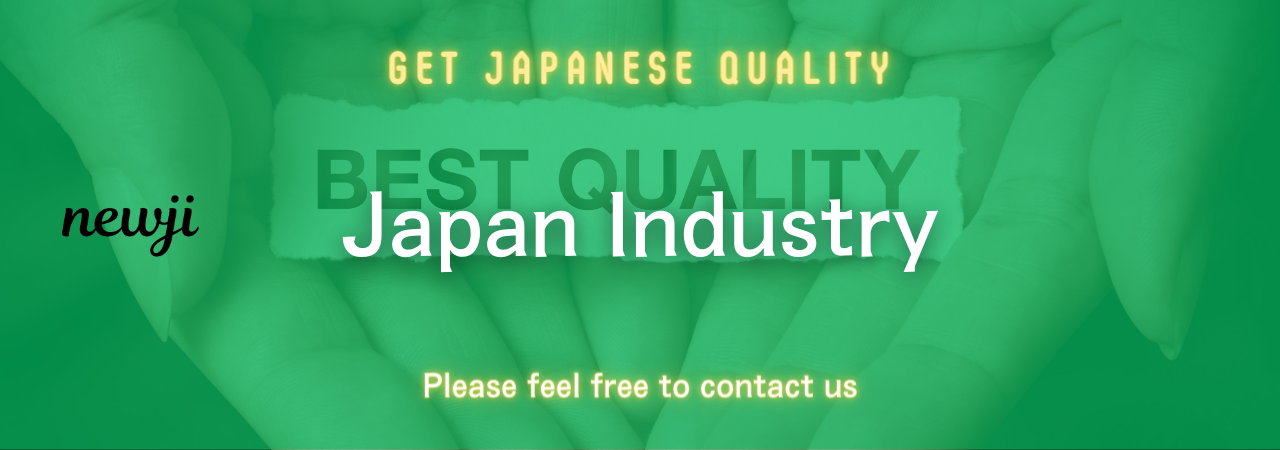
目次
Understanding Rolling Bearings
Rolling bearings are a crucial component in countless machines and devices.
They support rotational or axial loads and provide smooth and efficient movement, reducing friction and wear.
Though often small in size, their role is significant in ensuring the proper function of machinery in industries such as automotive, aerospace, and manufacturing.
Despite their efficiency, rolling bearings are susceptible to damage and degradation over time.
Factors such as load, lubrication, temperature, and environment all influence their performance and lifespan.
Understanding these factors is the first step in implementing effective countermeasures against bearing damage.
Common Causes of Bearing Damage
There are multiple factors that contribute to the wear and failure of rolling bearings.
1. Inadequate Lubrication
Lubrication is crucial for reducing friction between the moving parts of a bearing.
When lubrication is insufficient or has degraded, it can lead to excessive friction and heat.
This results in wear and, eventual, bearing failure.
2. Contamination
The presence of dirt, moisture, or other foreign particles can have a detrimental effect on bearing performance.
Contaminants can physically damage the bearing surfaces, leading to increased wear and reduced efficiency.
3. Overloading
Excessive loads can cause deformation of the bearing components.
This can result in an uneven distribution of stress and potential failure.
Overloading not only shortens the lifespan of a bearing but also affects the performance and safety of the machine.
Countermeasures for Bearing Damage
Proactively addressing the factors that contribute to bearing damage can prolong the lifespan of rolling bearings and enhance their performance.
1. Proper Lubrication
Ensuring consistent and adequate lubrication is vital.
Using the right type of lubricant for the specific application can reduce friction and wear, ensuring smooth operation.
Regular inspection and replacement of the lubricant can prevent issues arising from degradation and contamination.
2. Sealing and Shields
Implementing effective sealing and shields can keep contaminants at bay.
These barriers prevent dirt, moisture, and other foreign substances from entering the bearing assembly, thus reducing the risk of damage.
3. Load Optimization
Properly analyzing and optimizing the load conditions can prevent overloading.
This involves assessing the operational requirements and ensuring that the bearings are appropriate for the expected loads.
Additionally, using tools and software to simulate load conditions can aid in designing systems that minimize stress on bearings.
Predicting Bearing Lifespan
Accurate lifespan prediction is essential for planning maintenance and preventing unplanned downtimes.
There are several methodologies and technologies available for predicting the life expectancy of rolling bearings.
Mathematical Models
Mathematical models are developed to calculate the bearing’s operational life based on theoretical considerations.
These models consider factors such as material characteristics, applied loads, and lubrication conditions.
By using these models, manufacturers and engineers can estimate the lifespan of a bearing under specific conditions.
Condition Monitoring
Condition monitoring involves the regular measurement and analysis of the operational parameters of bearings.
Tools such as vibration analysis, temperature monitoring, and oil analysis are commonly used to detect deviations from normal operating conditions.
This allows for early identification of potential issues, enabling timely maintenance and intervention.
Advanced Diagnostic Tools
Recent advancements in technology have led to the development of sophisticated diagnostic tools.
These tools employ sensors and software algorithms to continuously monitor and analyze the performance of bearings in real time.
By providing detailed insights into the condition of the bearing, these tools facilitate predictive maintenance strategies, reducing the risk of unexpected failures.
Diagnostic Technology for Bearings
Accurate diagnostic technology is key to maintaining the reliability and efficiency of rolling bearings.
Vibration Analysis
Vibration analysis involves measuring the vibration signal emitted by a bearing during operation.
By analyzing the frequency, amplitude, and other aspects of these signals, it is possible to detect abnormalities and diagnose potential issues.
This technique is highly effective in identifying wear, imbalance, or misalignment in bearing systems.
Infrared Thermography
Infrared thermography uses infrared cameras to detect heat emitted by machinery components, including bearings.
Anomalies in temperature can indicate issues such as excessive friction, inadequate lubrication, or misalignment.
Thermographic analysis provides a non-invasive method for assessing the condition of bearings in real-time.
Acoustic Emission Testing
Acoustic emission testing monitors the high-frequency sound waves produced by the materials in a bearing under stress.
This method is effective for detecting early-stage wear and damage.
Acoustic emission testing can identify faults that are not easily detectable by other means, providing an early warning signal for preventive maintenance.
Conclusion
Rolling bearings play an indispensable role in the performance and reliability of machinery.
Understanding the causes of bearing damage, implementing effective countermeasures, and utilizing advanced diagnostic and predictive technologies are crucial steps in ensuring their long lifespan and optimal performance.
By integrating these strategies into regular maintenance practices, industries can enhance operational efficiency, reduce downtime, and achieve significant cost savings.
資料ダウンロード
QCD管理受発注クラウド「newji」は、受発注部門で必要なQCD管理全てを備えた、現場特化型兼クラウド型の今世紀最高の受発注管理システムとなります。
ユーザー登録
受発注業務の効率化だけでなく、システムを導入することで、コスト削減や製品・資材のステータス可視化のほか、属人化していた受発注情報の共有化による内部不正防止や統制にも役立ちます。
NEWJI DX
製造業に特化したデジタルトランスフォーメーション(DX)の実現を目指す請負開発型のコンサルティングサービスです。AI、iPaaS、および先端の技術を駆使して、製造プロセスの効率化、業務効率化、チームワーク強化、コスト削減、品質向上を実現します。このサービスは、製造業の課題を深く理解し、それに対する最適なデジタルソリューションを提供することで、企業が持続的な成長とイノベーションを達成できるようサポートします。
製造業ニュース解説
製造業、主に購買・調達部門にお勤めの方々に向けた情報を配信しております。
新任の方やベテランの方、管理職を対象とした幅広いコンテンツをご用意しております。
お問い合わせ
コストダウンが利益に直結する術だと理解していても、なかなか前に進めることができない状況。そんな時は、newjiのコストダウン自動化機能で大きく利益貢献しよう!
(β版非公開)