- お役立ち記事
- Data-Driven Manufacturing: Shaping the Future with Predictive Analytics
Data-Driven Manufacturing: Shaping the Future with Predictive Analytics
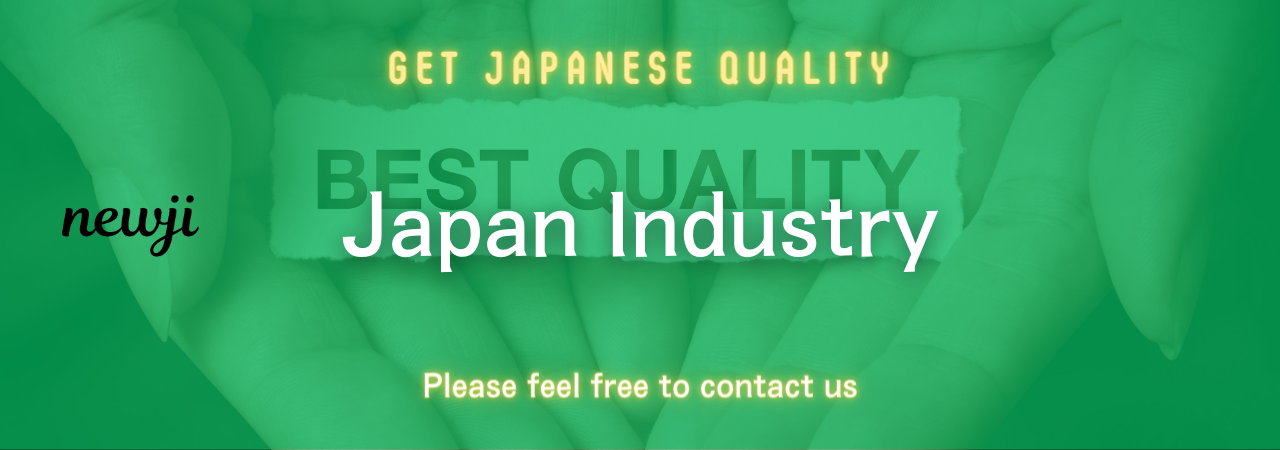
In today’s fast-paced world, industries across the globe are turning to data to improve their processes and products.
One sector that’s experiencing a significant transformation is manufacturing.
With the advent of predictive analytics, manufacturers are leveraging data to optimize operations, reduce downtime, and enhance product quality.
This shift towards data-driven manufacturing is revolutionizing the industry, making it more efficient and innovative.
目次
Understanding Predictive Analytics
Predictive analytics involves using historical data, machine learning techniques, and statistical algorithms to forecast future events.
In the context of manufacturing, it means predicting failures before they happen, optimizing maintenance schedules, and ensuring product quality.
This proactive approach is a game-changer because it allows manufacturers to make informed decisions and avoid unexpected disruptions.
The Role of Data in Manufacturing
Manufacturing processes generate vast amounts of data from various sources like machines, sensors, and production lines.
This data includes information about machine performance, production rates, and maintenance activities.
By analyzing this data, manufacturers gain valuable insights that can drive improvements across their operations.
Data-driven manufacturing uses these insights to enhance efficiency and productivity.
For instance, if a machine’s data indicates it’s likely to fail soon, predictive maintenance can be scheduled to avoid unexpected breakdowns.
This reduces downtime and keeps the production line running smoothly.
Benefits of Predictive Analytics in Manufacturing
The implementation of predictive analytics in manufacturing brings about numerous benefits, making it an indispensable tool for modern manufacturers.
1. Reduced Downtime
One of the most significant advantages of predictive analytics is the reduction of downtime.
By predicting when a machine or component is likely to fail, maintenance can be performed proactively.
This prevents unexpected breakdowns, ensuring continuous production and minimizing loss.
2. Improved Product Quality
Predictive analytics helps in maintaining consistent product quality.
By monitoring production processes in real-time, manufacturers can identify any deviations from the norm and correct them promptly.
This ensures that products meet quality standards and reduces the likelihood of defects reaching customers.
3. Cost Savings
Predictive maintenance is more cost-effective than reactive maintenance.
Scheduled maintenance based on predictive insights reduces the need for emergency repairs, which can be more expensive.
Additionally, by avoiding unplanned downtime, manufacturers save on both repair costs and lost production time.
4. Enhanced Decision-Making
With predictive analytics, manufacturers have access to actionable insights derived from their data.
These insights enable better decision-making at all levels, from the shop floor to the executive suite.
Whether it’s optimizing production schedules or planning for future capacity, data-driven decisions are more informed and strategic.
Implementing Predictive Analytics in Manufacturing
While the benefits of predictive analytics are clear, implementing it in a manufacturing setting requires a structured approach.
1. Data Collection and Integration
The first step is to collect and integrate data from various sources within the manufacturing environment.
This includes data from machines, sensors, ERP systems, and other relevant sources.
A robust data infrastructure is crucial for storing and managing this data effectively.
2. Data Analysis and Modeling
Once the data is collected, it needs to be analyzed using statistical and machine learning techniques.
This involves creating predictive models that can identify patterns and trends in the data.
Advanced analytics tools and software can help in building these models.
3. Implementation and Monitoring
After developing predictive models, the next step is to implement them in the production environment.
This involves integrating the models with existing systems and setting up monitoring mechanisms to track their performance.
Continuous monitoring ensures that the models are providing accurate predictions and allows for adjustments as needed.
Challenges in Adopting Predictive Analytics
While predictive analytics offers numerous benefits, there are challenges that manufacturers need to address to ensure successful implementation.
1. Data Quality and Availability
The accuracy of predictive models depends heavily on the quality and availability of data.
Manufacturers must ensure that they collect accurate, clean, and comprehensive data for analysis.
Incomplete or erroneous data can lead to incorrect predictions, impacting decision-making.
2. Integration with Existing Systems
Integrating predictive analytics with existing manufacturing systems can be complex.
Manufacturers need to ensure that data flows seamlessly between different systems and that the predictive models are compatible with the current infrastructure.
This may require significant investment in new technologies and systems.
3. Skillset and Expertise
Implementing predictive analytics requires specialized skills in data science, machine learning, and statistical analysis.
Manufacturers may need to invest in training their existing workforce or hiring new talent with the necessary expertise.
Building a team with the right skills is essential for successful adoption.
The Future of Data-Driven Manufacturing
As technology continues to advance, the role of predictive analytics in manufacturing is expected to grow even further.
The integration of artificial intelligence, the Internet of Things (IoT), and big data analytics will open up new possibilities for enhancing manufacturing processes.
Smart factories, where every aspect of production is interconnected and optimized using real-time data, are becoming a reality.
Manufacturers that embrace predictive analytics will be better positioned to compete in the global market.
By leveraging data to predict and prevent issues, optimize operations, and maintain product quality, they can achieve greater efficiency and innovation.
The future of manufacturing is data-driven, and predictive analytics is at the forefront of this transformation.
In conclusion, data-driven manufacturing with predictive analytics is shaping the future of the industry.
The ability to predict and prevent problems, improve product quality, and make informed decisions is revolutionizing manufacturing processes.
While there are challenges to overcome, the benefits far outweigh the obstacles.
By investing in the right technologies and expertise, manufacturers can embrace this transformation and secure a competitive edge in the market.
資料ダウンロード
QCD調達購買管理クラウド「newji」は、調達購買部門で必要なQCD管理全てを備えた、現場特化型兼クラウド型の今世紀最高の購買管理システムとなります。
ユーザー登録
調達購買業務の効率化だけでなく、システムを導入することで、コスト削減や製品・資材のステータス可視化のほか、属人化していた購買情報の共有化による内部不正防止や統制にも役立ちます。
NEWJI DX
製造業に特化したデジタルトランスフォーメーション(DX)の実現を目指す請負開発型のコンサルティングサービスです。AI、iPaaS、および先端の技術を駆使して、製造プロセスの効率化、業務効率化、チームワーク強化、コスト削減、品質向上を実現します。このサービスは、製造業の課題を深く理解し、それに対する最適なデジタルソリューションを提供することで、企業が持続的な成長とイノベーションを達成できるようサポートします。
オンライン講座
製造業、主に購買・調達部門にお勤めの方々に向けた情報を配信しております。
新任の方やベテランの方、管理職を対象とした幅広いコンテンツをご用意しております。
お問い合わせ
コストダウンが利益に直結する術だと理解していても、なかなか前に進めることができない状況。そんな時は、newjiのコストダウン自動化機能で大きく利益貢献しよう!
(Β版非公開)