- お役立ち記事
- Decoding HDC: Unraveling Its Role in Japanese Robot Controller Manufacturing
Decoding HDC: Unraveling Its Role in Japanese Robot Controller Manufacturing
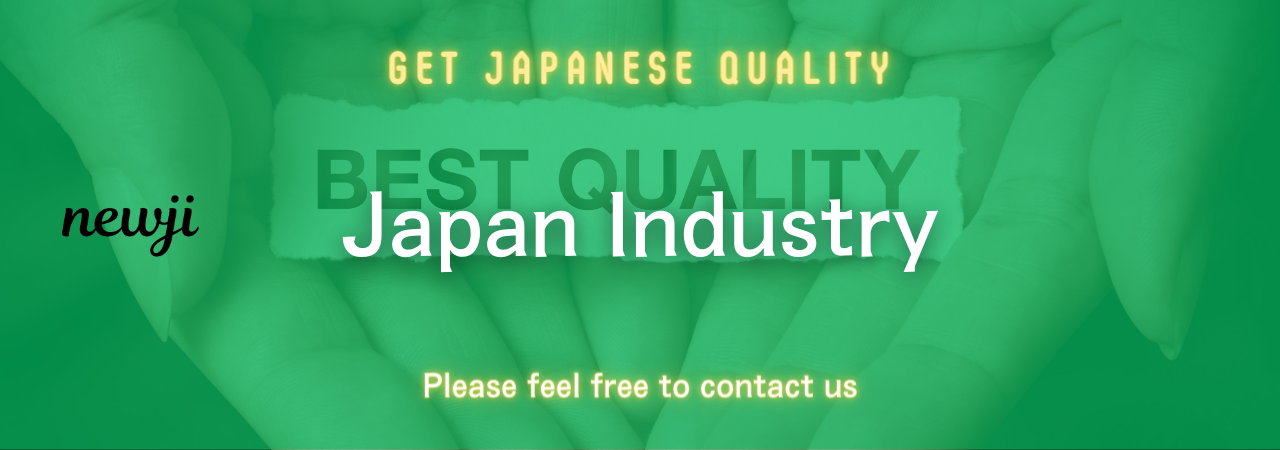
目次
Introduction to HDC in Japanese Robot Controller Manufacturing
Japanese manufacturing has long been synonymous with precision, reliability, and technological advancement. Central to this reputation is the role of high-definition controllers (HDC) in robot controller manufacturing. HDCs are pivotal in ensuring that robotic systems operate with exceptional accuracy and efficiency. This article delves into the intricacies of HDCs, exploring their significance, advantages, challenges, and best practices within the context of Japanese procurement and purchasing.
Understanding HDC: High-Definition Controllers
HDCs are advanced control systems designed to manage the operations of robotic machinery with high precision. Unlike standard controllers, HDCs offer enhanced resolution, faster processing speeds, and greater adaptability, making them ideal for complex manufacturing tasks.
Key Features of HDCs
HDCs are equipped with several features that set them apart from conventional controllers:
– **High Resolution:** Allows for finer control of robotic movements.
– **Rapid Processing:** Enables real-time adjustments and faster operational cycles.
– **Enhanced Connectivity:** Facilitates seamless integration with other manufacturing systems.
– **Advanced Diagnostics:** Provides detailed performance metrics and predictive maintenance capabilities.
The Role of HDC in Japanese Robot Manufacturing
In the competitive landscape of Japanese manufacturing, HDCs play a critical role in maintaining the industry’s edge. They contribute to the creation of highly efficient and reliable robotic systems used in various sectors, including automotive, electronics, and aerospace.
Precision and Quality Control
One of the primary roles of HDCs is to ensure that robots operate with high precision, which is essential for maintaining quality standards. This precision minimizes errors, reduces waste, and enhances the overall quality of the manufactured products.
Automation and Efficiency
HDCs enhance automation capabilities, allowing robots to perform complex tasks with minimal human intervention. This increases production efficiency, reduces labor costs, and accelerates manufacturing processes.
Adaptability and Flexibility
Modern manufacturing demands adaptability to rapidly changing market needs. HDCs provide the necessary flexibility for robots to switch between different tasks and adjust to varying production requirements seamlessly.
Advantages of Utilizing HDC in Procurement and Purchasing
Incorporating HDCs into procurement and purchasing strategies offers several advantages, particularly within the Japanese manufacturing context.
Enhanced Supplier Relationships
Japanese suppliers are renowned for their technological prowess. By sourcing HDCs from these suppliers, companies can establish strong, collaborative relationships that foster innovation and continuous improvement.
Cost Efficiency
While the initial investment in HDCs may be higher, the long-term benefits include lower maintenance costs, reduced downtime, and improved energy efficiency. These factors contribute to overall cost savings in the procurement lifecycle.
Quality and Reliability
HDCs from Japanese manufacturers are synonymous with quality and reliability. This ensures that the robotic systems perform consistently, reducing the risk of production interruptions and ensuring timely delivery of products.
Competitive Advantage
Adopting advanced HDCs provides a competitive edge by enabling manufacturers to offer superior products and services. This differentiation is crucial in markets where technological excellence is a key determinant of success.
Challenges in Procuring HDCs from Japanese Suppliers
Despite the numerous benefits, procuring HDCs from Japanese suppliers presents certain challenges that must be addressed to ensure a smooth procurement process.
Cultural and Language Barriers
Navigating the cultural nuances and language differences can be challenging. Effective communication is essential to avoid misunderstandings and ensure that specifications and expectations are clearly conveyed.
Supply Chain Complexity
The complexity of global supply chains can pose logistical challenges. Ensuring timely delivery and managing inventory levels requires meticulous planning and coordination with Japanese suppliers.
Cost Considerations
While HDCs offer long-term cost benefits, the upfront costs can be substantial. Balancing budget constraints with the need for advanced technology requires strategic financial planning.
Technological Integration
Integrating HDCs into existing manufacturing systems may require significant modifications. Ensuring compatibility and minimizing disruptions during the integration process is crucial for maintaining production continuity.
Supplier Negotiation Techniques for HDC Procurement
Effective negotiation with Japanese suppliers is key to securing favorable terms and ensuring the successful procurement of HDCs. Here are some strategies to enhance negotiation outcomes.
Building Strong Relationships
In Japanese business culture, relationships and trust are paramount. Investing time in building strong, respectful relationships with suppliers can lead to more favorable negotiation outcomes and long-term partnerships.
Understanding Supplier Priorities
Gaining insight into the supplier’s priorities and constraints allows for more effective negotiations. Understanding what the supplier values, whether it’s long-term contracts, volume commitments, or timely payments, can help in crafting mutually beneficial agreements.
Leveraging Volume and Long-Term Contracts
Offering larger order volumes or committing to long-term contracts can provide leverage in negotiations. Suppliers are often willing to offer discounts or better terms in exchange for guaranteed business.
Flexible Payment Terms
Negotiating flexible payment terms, such as extended payment periods or installment plans, can ease cash flow pressures and make the procurement process more manageable.
Technical Collaboration
Engaging in technical collaboration and co-development initiatives can strengthen partnerships. By working closely with suppliers on the development of HDCs, both parties can achieve better alignment and innovation.
Market Conditions Affecting HDC Procurement
Understanding the current market conditions is essential for effective procurement and purchasing strategies related to HDCs.
Technological Advancements
The rapid pace of technological advancements in robotics and automation necessitates staying abreast of the latest HDC developments. This ensures that manufacturers can leverage cutting-edge technology to maintain competitiveness.
Global Supply Chain Dynamics
Global supply chain disruptions, such as those caused by geopolitical tensions or natural disasters, can impact the availability and pricing of HDCs. Diversifying suppliers and maintaining flexibility in procurement strategies can mitigate these risks.
Demand Fluctuations
Fluctuations in demand for robotic systems influence the demand for HDCs. Understanding market trends and forecasting demand accurately helps in planning procurement activities effectively.
Regulatory Environment
Compliance with international and local regulations related to robotics and automation is essential. Staying informed about regulatory changes ensures that procured HDCs meet all necessary standards and certifications.
Best Practices in Procuring HDCs from Japanese Suppliers
Adopting best practices in the procurement of HDCs can lead to more efficient processes, cost savings, and stronger supplier relationships.
Comprehensive Supplier Evaluation
Conducting thorough evaluations of potential suppliers is critical. Assess factors such as quality certifications, technological capabilities, financial stability, and track record to select the most reliable partners.
Clear Specification and Documentation
Providing clear and detailed specifications ensures that suppliers understand the exact requirements. Accurate documentation minimizes the risk of errors and misinterpretations during the procurement process.
Effective Communication Channels
Establishing robust communication channels facilitates smooth interactions with suppliers. Regular updates, transparent information sharing, and prompt issue resolution contribute to effective procurement management.
Strategic Inventory Management
Implementing strategic inventory management practices, such as just-in-time (JIT) inventory, reduces holding costs and minimizes the risk of overstocking or stockouts. Close coordination with suppliers is essential for JIT to be successful.
Continuous Performance Monitoring
Monitoring supplier performance through key performance indicators (KPIs) such as delivery times, quality standards, and responsiveness allows for ongoing assessment and continuous improvement of the procurement process.
Strategies for Enhancing Factory Efficiency with HDCs
Integrating HDCs into factory operations can significantly enhance efficiency and productivity. Here are strategies to optimize their use.
Automation Optimization
Leveraging HDCs to optimize automation processes ensures that robotic systems operate at peak efficiency. Fine-tuning control parameters and utilizing real-time data analytics can enhance performance.
Predictive Maintenance
Using the advanced diagnostics capabilities of HDCs enables predictive maintenance. By anticipating equipment failures before they occur, manufacturers can reduce downtime and extend the lifespan of robotic systems.
Energy Management
HDCs contribute to better energy management by optimizing the power usage of robotic systems. Implementing energy-efficient practices not only reduces operational costs but also supports sustainability initiatives.
Training and Skill Development
Investing in training programs for staff ensures that they are proficient in operating and maintaining HDC-equipped robots. Skilled personnel are essential for maximizing the benefits of advanced control systems.
Data-Driven Decision Making
Utilizing the data generated by HDCs for informed decision-making enhances overall factory efficiency. Analyzing performance metrics and production data helps in identifying areas for improvement and implementing effective solutions.
Case Studies: Successful Implementation of HDCs in Japanese Manufacturing
Examining real-world examples provides valuable insights into the successful implementation of HDCs.
Automotive Manufacturing
A leading Japanese automotive manufacturer integrated HDCs into their assembly line robots. This integration led to a 20% increase in production speed and a significant reduction in assembly errors, enhancing overall product quality.
Electronics Assembly
In the electronics sector, a Japanese company adopted HDCs for precision component placement in circuit board manufacturing. The enhanced control capabilities resulted in higher placement accuracy and reduced defect rates.
Aerospace Component Production
An aerospace components manufacturer incorporated HDCs into their robotic welding systems. The improved control and precision ensured adherence to stringent industry standards, leading to increased reliability and safety of the final products.
The Future of HDCs in Japanese Robot Manufacturing
The future of HDCs in Japanese robot manufacturing looks promising, with ongoing advancements and evolving market demands shaping their development.
Integration with Artificial Intelligence
The convergence of HDCs with artificial intelligence (AI) will enable smarter and more autonomous robotic systems. AI-driven HDCs can learn and adapt to optimize performance continually.
Enhanced Connectivity and IoT
The Internet of Things (IoT) will further enhance the connectivity of HDCs, allowing for better data exchange and integration with broader smart manufacturing ecosystems.
Customization and Flexibility
Future HDCs will offer greater customization options, allowing manufacturers to tailor control systems to specific operational requirements and enhance flexibility in production processes.
Sustainability and Energy Efficiency
There will be a stronger emphasis on developing HDCs that support sustainable manufacturing practices. Energy-efficient control systems will contribute to reducing the environmental footprint of robotic operations.
Collaborative Robotics
HDCs will play a crucial role in the advancement of collaborative robotics (cobots). Improved control systems will enable safer and more efficient human-robot interactions in shared workspaces.
Conclusion
HDCs are integral to the success of Japanese robot controller manufacturing, driving precision, efficiency, and innovation. By understanding their role, leveraging their advantages, and addressing associated challenges, manufacturers can harness the full potential of HDCs. Effective procurement and purchasing strategies, coupled with best practices in supplier negotiation and market analysis, are essential for capitalizing on the benefits that HDCs offer. As technology continues to evolve, HDCs will remain at the forefront of advanced manufacturing, enabling Japanese industries to maintain their global leadership in robotics and automation.
資料ダウンロード
QCD調達購買管理クラウド「newji」は、調達購買部門で必要なQCD管理全てを備えた、現場特化型兼クラウド型の今世紀最高の購買管理システムとなります。
ユーザー登録
調達購買業務の効率化だけでなく、システムを導入することで、コスト削減や製品・資材のステータス可視化のほか、属人化していた購買情報の共有化による内部不正防止や統制にも役立ちます。
NEWJI DX
製造業に特化したデジタルトランスフォーメーション(DX)の実現を目指す請負開発型のコンサルティングサービスです。AI、iPaaS、および先端の技術を駆使して、製造プロセスの効率化、業務効率化、チームワーク強化、コスト削減、品質向上を実現します。このサービスは、製造業の課題を深く理解し、それに対する最適なデジタルソリューションを提供することで、企業が持続的な成長とイノベーションを達成できるようサポートします。
オンライン講座
製造業、主に購買・調達部門にお勤めの方々に向けた情報を配信しております。
新任の方やベテランの方、管理職を対象とした幅広いコンテンツをご用意しております。
お問い合わせ
コストダウンが利益に直結する術だと理解していても、なかなか前に進めることができない状況。そんな時は、newjiのコストダウン自動化機能で大きく利益貢献しよう!
(Β版非公開)