- お役立ち記事
- Deep drawing technology for aluminum alloys and its application in the automobile industry
月間77,185名の
製造業ご担当者様が閲覧しています*
*2025年2月28日現在のGoogle Analyticsのデータより
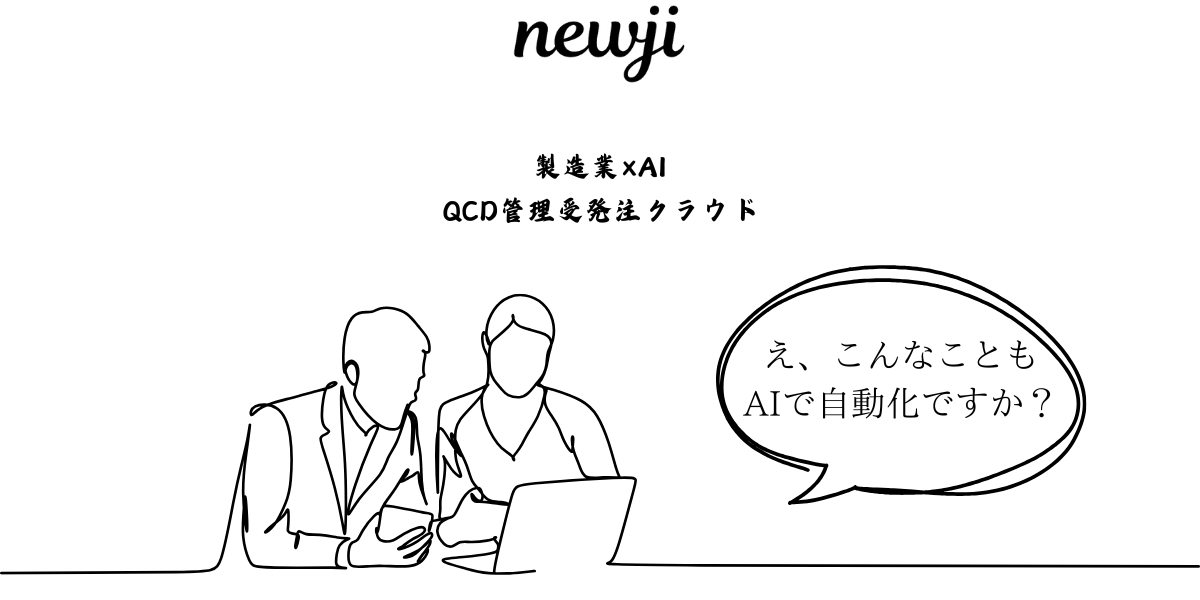
Deep drawing technology for aluminum alloys and its application in the automobile industry
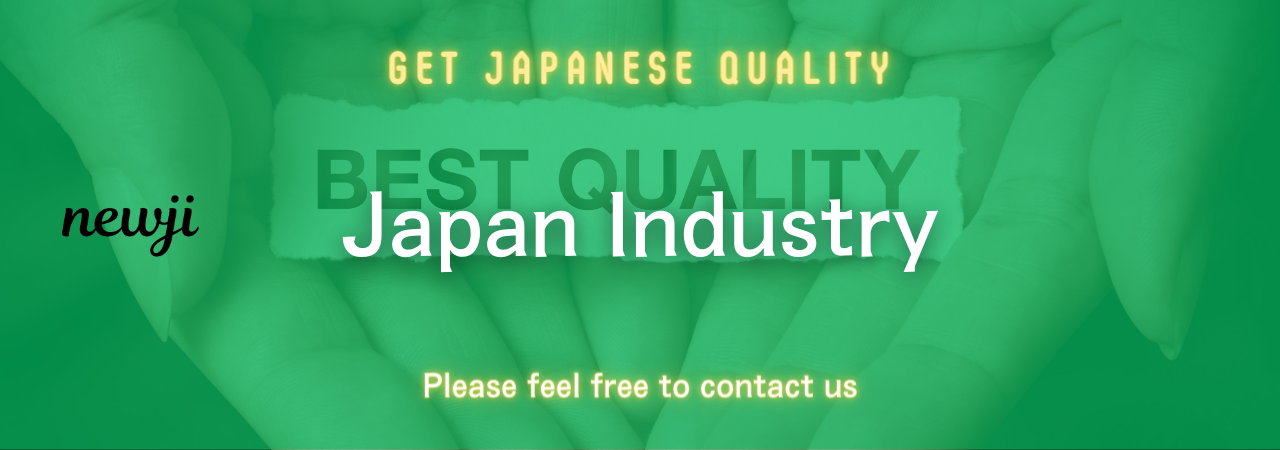
目次
Introduction to Deep Drawing Technology
Deep drawing is a widely used metal forming process that forms sheet metal into a desired shape.
By applying a mechanical force, the metal is drawn into a die to create cylindrical or complex geometrical designs.
Amongst various materials, aluminum alloys are particularly suitable for deep drawing due to their excellent formability and light weight.
Aluminum alloys, particularly those used in deep drawing, possess remarkable characteristics such as corrosion resistance, high strength-to-weight ratio, and thermal and electrical conductivity.
These attributes make aluminum an attractive option for consistent, durable, and cost-effective production.
Benefits of Using Aluminum Alloys in Deep Drawing
Aluminum alloys provide numerous benefits in deep drawing applications:
Cost-Effectiveness
Aluminum alloys are relatively inexpensive compared to other metals like copper or stainless steel.
Their abundance and recyclability contribute to a lower production cost, making them economically viable for mass production, especially in the automobile industry.
Lightweight Nature
One of the foremost advantages of using aluminum is its light weight.
Reducing the mass of automotive parts leads to more fuel-efficient vehicles, which is of particular interest in today’s drive for environmentally friendly transportation solutions.
High Formability
Aluminum alloys have superior elongation and ductility properties, allowing them to be stretched into intricate shapes without tearing.
This high formability makes it possible to manufacture complex automotive components with improved material utilization.
Deep Drawing Process for Aluminum Alloys
The deep drawing process involves several key steps:
Blank Preparation
Initially, a blank, typically a flat piece of aluminum alloy, is cut in specific dimensions corresponding to the final product requirements.
The quality of the blank is critical, as uneven surfaces can lead to defects during the drawing process.
Setup and Tooling
Next, the blank is positioned over a die and clamped in place by a blank holder.
The die and punch design must be precisely matched to the desired shape, ensuring a smooth forming process.
Drawing Process
The drawing process occurs as the punch pushes the blank into the die cavity with controlled pressure.
Proper lubrication is essential to reduce friction and prevent tearing or wrinkling during this stage.
The depth of the draw and the speed of the punch are carefully regulated to achieve a high-quality final product.
Trimming and Finishing
Once the metal has been drawn to shape, excess material is trimmed.
Additionally, surface treatments or coatings may be applied to enhance corrosion resistance and appearance, preparing the product for its intended application in vehicles.
Applications in the Automobile Industry
Deep drawing of aluminum alloys is pivotal in manufacturing various automotive components:
Car Body Panels
Aluminum alloys are extensively used in forming car hoods, doors, and roofs, capitalizing on their ability to reduce overall vehicle weight without compromising structural integrity.
Engine Components
In engines, components such as oil pans and valve covers benefit from aluminum’s heat conductivity and resistance to corrosion.
These properties ensure that engine parts maintain operational temperature efficiently and withstand harsh environmental conditions.
Chassis Structures
Aluminum is a popular choice for chassis and suspension components.
Its lightweight yet robust nature enhances vehicle performance and fuel efficiency, supporting the automotive sector’s shift towards more sustainable transportation.
Challenges and Future Developments
Despite its advantages, deep drawing of aluminum alloys is not without challenges:
Material Limitations
Certain aluminum alloys can become brittle when not treated correctly, leading to cracking during the drawing process.
Advancements in alloy compositions and heat treatment methods are ongoing to mitigate these risks.
Precision and Consistency
Achieving consistent precision in shaping across batch productions remains a significant challenge.
Innovations in machine technology and automation are being leveraged to enhance the accuracy and repeatability of deep drawing processes.
Technological Advancements
Emerging technologies, such as computer-aided simulations and AI-driven process optimizations, promise to revolutionize deep drawing by predicting potential defects, improving tool designs, and reducing waste.
Conclusion
Deep drawing technology for aluminum alloys is integral to automotive manufacturing.
As the demand for lightweight, fuel-efficient vehicles continues to rise, aluminum’s role is set to expand.
The ongoing challenges, however, require continuous innovation to overcome material limitations and improve production efficiency.
With technological advancements, deep drawing for aluminum alloys holds significant potential for future applications, paving the way for more sustainable and innovative vehicle designs.
資料ダウンロード
QCD管理受発注クラウド「newji」は、受発注部門で必要なQCD管理全てを備えた、現場特化型兼クラウド型の今世紀最高の受発注管理システムとなります。
ユーザー登録
受発注業務の効率化だけでなく、システムを導入することで、コスト削減や製品・資材のステータス可視化のほか、属人化していた受発注情報の共有化による内部不正防止や統制にも役立ちます。
NEWJI DX
製造業に特化したデジタルトランスフォーメーション(DX)の実現を目指す請負開発型のコンサルティングサービスです。AI、iPaaS、および先端の技術を駆使して、製造プロセスの効率化、業務効率化、チームワーク強化、コスト削減、品質向上を実現します。このサービスは、製造業の課題を深く理解し、それに対する最適なデジタルソリューションを提供することで、企業が持続的な成長とイノベーションを達成できるようサポートします。
製造業ニュース解説
製造業、主に購買・調達部門にお勤めの方々に向けた情報を配信しております。
新任の方やベテランの方、管理職を対象とした幅広いコンテンツをご用意しております。
お問い合わせ
コストダウンが利益に直結する術だと理解していても、なかなか前に進めることができない状況。そんな時は、newjiのコストダウン自動化機能で大きく利益貢献しよう!
(β版非公開)