- お役立ち記事
- Defect modes and pass/fail criteria for solder joints
Defect modes and pass/fail criteria for solder joints
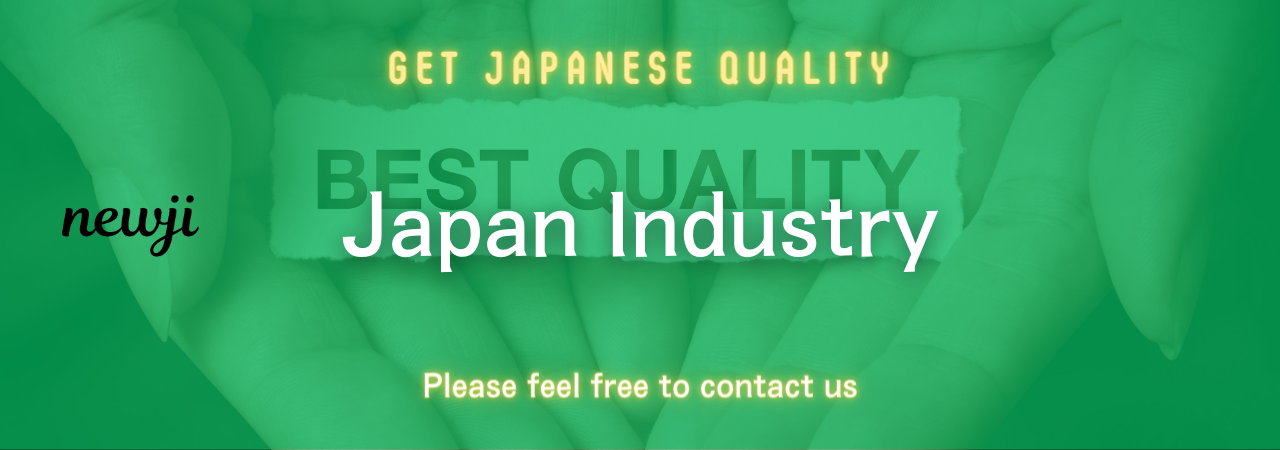
目次
Understanding Solder Joints
Solder joints are a critical component in electronic devices, serving as the physical and electrical connection between different parts of a printed circuit board (PCB).
Their reliability directly impacts the functionality and durability of electronic gadgets, from household appliances to complex computing systems.
Each solder joint must be meticulously designed and inspected to ensure that it meets both the functional and safety requirements of the device it supports.
Common Defect Modes in Solder Joints
Several defect modes can affect solder joints, undermining their performance and potentially leading to device failure.
1. Cold Joints
Cold joints occur when the solder does not melt completely during the soldering process, resulting in a weak connection.
This defect might happen due to insufficient heat being applied or not enough time allowed for the heat to properly melt the solder.
Cold joints can lead to intermittent connections that may fail under stress, impacting the reliability of the circuit.
2. Insufficient Wetting
Wetting is the ability of the solder to form a good bond between the components and the PCB.
Insufficient wetting results when the solder fails to properly adhere to the surfaces it’s supposed to connect.
This issue can be caused by dirty surfaces, incorrect solder paste application, or inadequate heating.
Insufficient wetting usually results in a poor bond strength, increasing the risk of mechanical and thermal failure.
3. Voids
Voids are air bubbles trapped in the solder, which can weaken the joint.
They may occur due to excessive moisture in the solder paste or improper heating profiles.
While tiny voids might be tolerable, larger ones can significantly reduce the mechanical and thermal performance of the solder joint, potentially causing it to fail prematurely.
4. Solder Balling
Solder balling is a defect where small solder balls form and separate from the main joint.
These can arise from excess solder paste or incorrect reflow profiles.
Solder balls can cause short circuits if they bridge connections that should be isolated, posing a risk of electronic failure.
5. Cracking
Cracks in solder joints can develop due to thermal cycling and mechanical stress, often exacerbated by poor joint design or improper soldering techniques.
These cracks compromise the structural integrity of the joint and can lead to open circuits or increased resistance over time.
Pass/Fail Criteria for Solder Joints
To ensure that solder joints function reliably throughout the life of a device, manufacturers employ specific pass/fail criteria.
These criteria help to evaluate whether a solder joint is fit for use or if it requires rework or replacement.
1. Visual Inspection
Visual inspection is often the first step in the evaluation process.
Using magnification tools, inspectors look for defects such as irregular shape, incomplete solder coverage, and visible defects like cracks or solder balls.
Clear guidelines define acceptable standards for both size and appearance, ensuring there’s no risk of mechanical dislodgement or electrical failure.
2. X-ray Inspection
For defects that are not visible on the surface, X-ray inspection can reveal internal issues such as voids or incomplete connections.
This nondestructive testing technique ensures that solder joints comply with internal quality standards and helps in identifying hidden flaws that could impact performance.
3. Electrical Testing
Electrical testing involves checking the electrical continuity and resistance of solder joints.
A proper solder joint should exhibit low resistance and ensure reliable electrical conductivity.
Any anomalies in these tests can indicate problems such as cold joints or partial connectivity, which require further investigation.
4. Mechanical Testing
Mechanical testing assesses the strength of solder joints under various stress conditions, such as shearing or tensile testing.
This ensures the joint can withstand the mechanical forces encountered during use and transportation.
Failure in these tests typically indicates a need for redesigning the joint or improving the soldering process.
5. Thermal Cycling Tests
Thermal cycling tests subject solder joints to temperature variations to simulate real-world operating conditions.
This test evaluates the joint’s ability to resist thermal expansion and contraction, crucial for ensuring long-term reliability in devices exposed to varying temperatures.
Ensuring High-Quality Solder Joints
Manufacturers must focus on process control and quality assurance to achieve solder joints that consistently meet pass/fail criteria.
Implementing advanced equipment and techniques, such as precision soldering tools and controlled reflow ovens, can help minimize defects.
Training personnel in proper soldering techniques and maintaining stringent cleanliness in the production environment are equally important to minimize contaminants that could impair solder adhesion.
Incorporating comprehensive inspection procedures at various stages of production, paired with rigorous testing, ensures that each solder joint is capable of withstanding both electrical and mechanical stresses.
Ultimately, attention to these details ensures the reliability and safety of the devices that rely on these critical connections.
資料ダウンロード
QCD調達購買管理クラウド「newji」は、調達購買部門で必要なQCD管理全てを備えた、現場特化型兼クラウド型の今世紀最高の購買管理システムとなります。
ユーザー登録
調達購買業務の効率化だけでなく、システムを導入することで、コスト削減や製品・資材のステータス可視化のほか、属人化していた購買情報の共有化による内部不正防止や統制にも役立ちます。
NEWJI DX
製造業に特化したデジタルトランスフォーメーション(DX)の実現を目指す請負開発型のコンサルティングサービスです。AI、iPaaS、および先端の技術を駆使して、製造プロセスの効率化、業務効率化、チームワーク強化、コスト削減、品質向上を実現します。このサービスは、製造業の課題を深く理解し、それに対する最適なデジタルソリューションを提供することで、企業が持続的な成長とイノベーションを達成できるようサポートします。
オンライン講座
製造業、主に購買・調達部門にお勤めの方々に向けた情報を配信しております。
新任の方やベテランの方、管理職を対象とした幅広いコンテンツをご用意しております。
お問い合わせ
コストダウンが利益に直結する術だと理解していても、なかなか前に進めることができない状況。そんな時は、newjiのコストダウン自動化機能で大きく利益貢献しよう!
(Β版非公開)