- お役立ち記事
- Defect observation and analysis technology for electronic components and application points for defect countermeasures
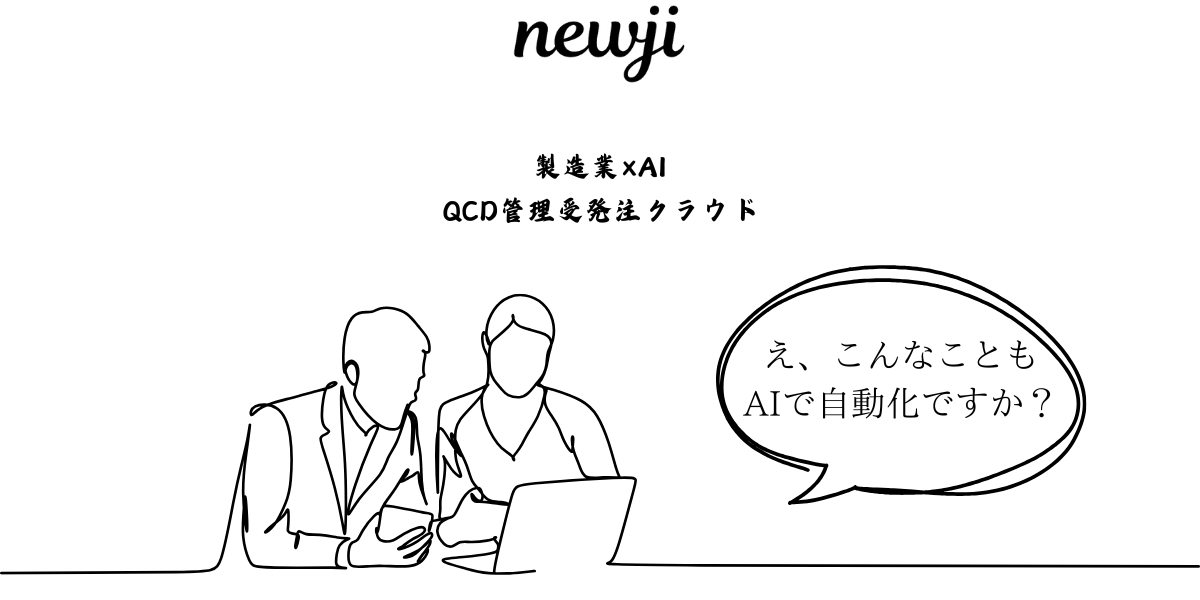
Defect observation and analysis technology for electronic components and application points for defect countermeasures
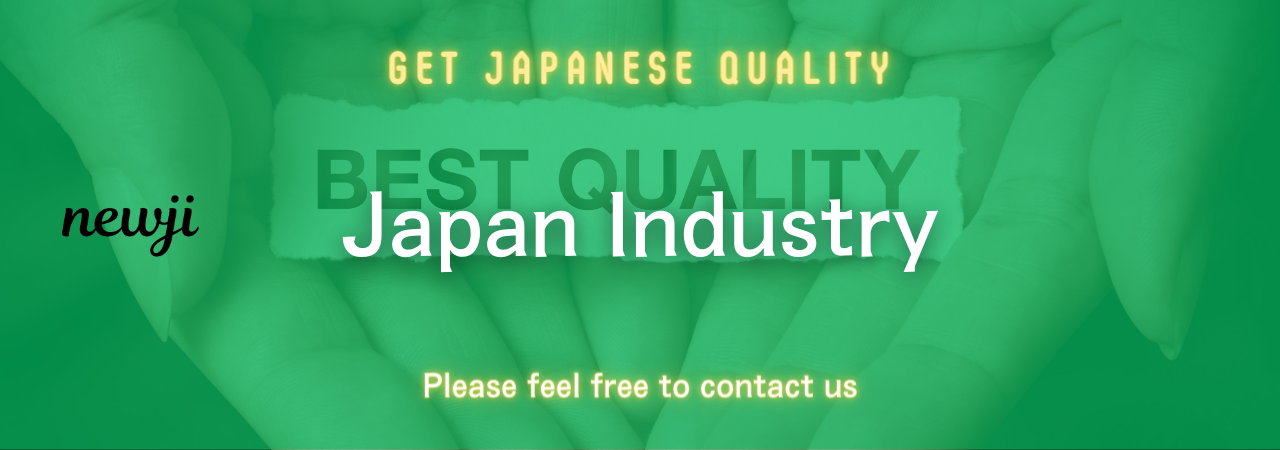
目次
Introduction to Defect Observation and Analysis Technology
In today’s fast-paced technological world, electronic components form the backbone of countless devices we use daily.
With their growing complexity and miniaturization, ensuring their reliability has become increasingly challenging.
Defect observation and analysis technology play a crucial role in identifying and mitigating issues that may compromise the performance and longevity of these electronic components.
This article aims to explore how these technologies are applied and what key points should be considered when developing defect countermeasures.
Understanding Defect Observation Techniques
Defect observation involves various methods employed to detect flaws in electronic components.
These flaws could range from minute structural anomalies to significant functional failures.
The primary aim is to identify defects early in the production process to prevent costly failure at later stages.
Visual Inspection
Visual inspection is one of the most straightforward methods of defect observation.
Technicians use magnification tools or automated optical inspection (AOI) systems to detect visible defects.
These could include component misalignment, soldering issues, or incomplete assembly.
X-ray Inspection
X-ray inspection is a non-destructive technique that allows for the examination of hidden structures within electronic components.
This method is particularly useful for inspecting solder joints and internal connections that are not visible to the naked eye.
By revealing issues such as voids or misalignments, X-ray inspection provides a deeper insight into the structural integrity of the component.
Ultrasonic Testing
Ultrasonic testing employs high-frequency sound waves to detect defects within materials.
This technique is particularly effective for identifying delaminations and voids in composite materials or multilayer electronic boards.
The sound waves reflect off discontinuities, enabling technicians to pinpoint the location and nature of the defect.
Thermal Imaging
Thermal imaging detects variations in temperature across an electronic component, often signaling an underlying defect.
This technique is useful for identifying hotspots caused by issues such as poor thermal dissipation or electrical shorts.
By visualizing thermal patterns, technicians can infer potential problem areas that need further investigation.
Analyzing Defects for Better Insights
Once defects are observed, analysis is the next step in understanding their cause and impact.
Effective analysis involves systematic evaluation of data gathered from observation techniques to make informed decisions.
Failure Mode and Effects Analysis (FMEA)
FMEA is a structured approach to identify potential failure modes within a system and assess their impact.
By analyzing each defect, FMEA helps prioritize issues based on their severity, occurrence, and detection difficulty.
This method enables manufacturers to focus on critical defects that could significantly affect the performance of electronic components.
Root Cause Analysis (RCA)
RCA is a problem-solving technique that seeks to identify the underlying causes of defects.
By tracing the sequence of events leading to a defect, RCA enables manufacturers to implement corrective actions that address the root cause rather than symptoms.
This approach is essential for preventing recurrence and improving overall product quality.
Statistical Analysis
Statistical analysis involves using data to identify patterns and trends associated with defects.
Techniques such as regression analysis, hypothesis testing, and control charts help quantify the relationship between various factors and defects.
This data-driven approach supports more accurate predictions and better-informed decision-making in defect management.
Application Points for Defect Countermeasures
Developing effective defect countermeasures is crucial for enhancing the reliability and performance of electronic components.
Here are some key application points to consider when implementing defect countermeasures.
Design for Manufacturability (DFM)
DFM is an approach that emphasizes designing products in a way that simplifies manufacturing and minimizes defects.
By considering manufacturing constraints during the design phase, engineers can reduce the likelihood of defects occurring during production.
DFM principles help create designs that are easier to produce, assemble, and test, leading to higher-quality outcomes.
Continuous Improvement
Continuous improvement involves adopting methodologies like Lean or Six Sigma to systematically eliminate waste and improve processes.
By fostering a culture of continuous improvement, organizations can consistently identify and rectify sources of defects.
This proactive approach leads to enhanced defect management and ongoing quality enhancements.
Supplier Collaboration
Collaborating with suppliers is vital for early detection and prevention of defects.
By establishing clear communication channels and quality standards, manufacturers can work closely with suppliers to ensure defect-free components.
Regular audits and feedback loops contribute to maintaining high-quality standards and reducing defect rates.
Implementing Robust Testing Protocols
Developing rigorous testing protocols is crucial for catching defects before they reach the customer.
These protocols should be comprehensive, covering various stages of production and different testing techniques.
By investing in robust testing methods, manufacturers can ensure the reliability and performance of their electronic components.
Conclusion
Defect observation and analysis technology are indispensable in the realm of electronic component manufacturing.
By effectively observing, analyzing, and countering defects, manufacturers can enhance product reliability and customer satisfaction.
Employing strategies such as FMEA, RCA, and continuous improvement ensures that the quality of electronic components meets industry standards.
By understanding and applying these techniques, manufacturers can proactively address defects, leading to better performance and extended product lifespans.
資料ダウンロード
QCD調達購買管理クラウド「newji」は、調達購買部門で必要なQCD管理全てを備えた、現場特化型兼クラウド型の今世紀最高の購買管理システムとなります。
ユーザー登録
調達購買業務の効率化だけでなく、システムを導入することで、コスト削減や製品・資材のステータス可視化のほか、属人化していた購買情報の共有化による内部不正防止や統制にも役立ちます。
NEWJI DX
製造業に特化したデジタルトランスフォーメーション(DX)の実現を目指す請負開発型のコンサルティングサービスです。AI、iPaaS、および先端の技術を駆使して、製造プロセスの効率化、業務効率化、チームワーク強化、コスト削減、品質向上を実現します。このサービスは、製造業の課題を深く理解し、それに対する最適なデジタルソリューションを提供することで、企業が持続的な成長とイノベーションを達成できるようサポートします。
オンライン講座
製造業、主に購買・調達部門にお勤めの方々に向けた情報を配信しております。
新任の方やベテランの方、管理職を対象とした幅広いコンテンツをご用意しております。
お問い合わせ
コストダウンが利益に直結する術だと理解していても、なかなか前に進めることができない状況。そんな時は、newjiのコストダウン自動化機能で大きく利益貢献しよう!
(Β版非公開)