- お役立ち記事
- Defect Prevention and Quality Control Methods for Multi-Injection Molding in SMEs
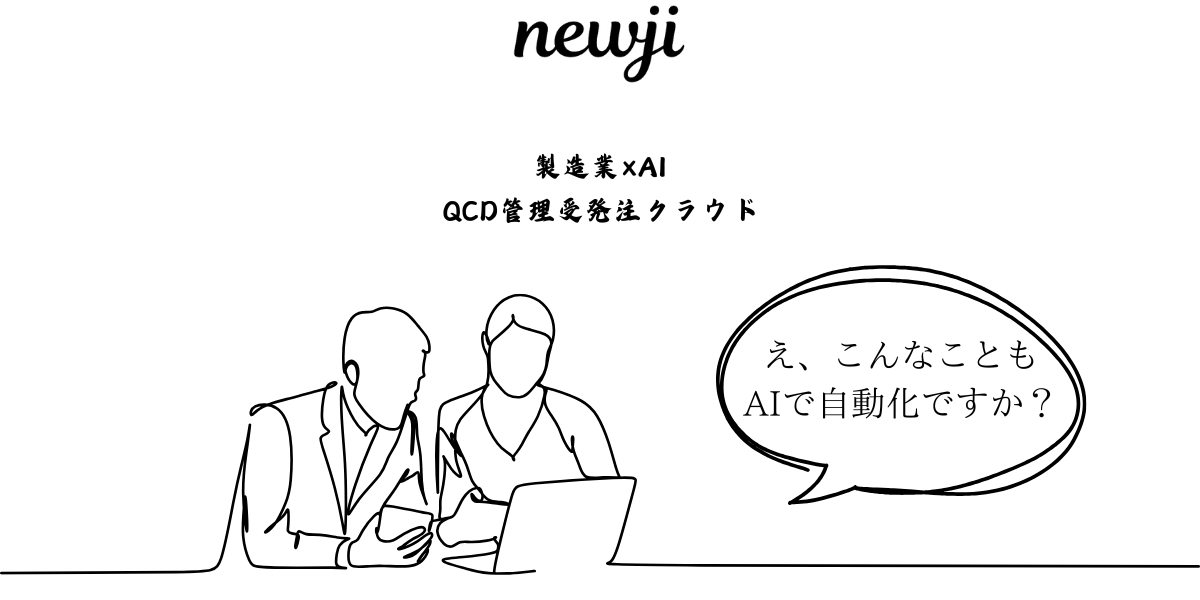
Defect Prevention and Quality Control Methods for Multi-Injection Molding in SMEs
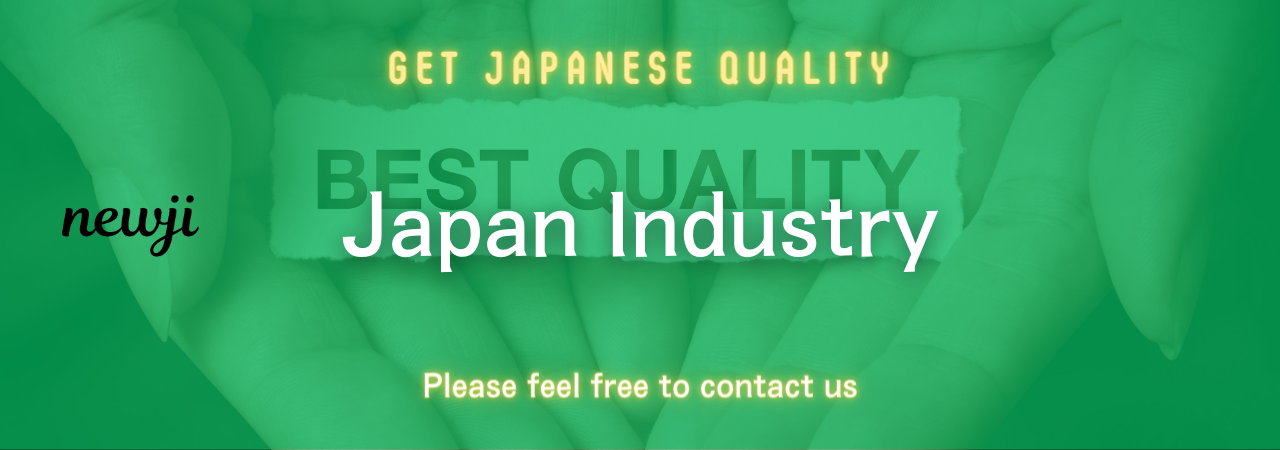
目次
Understanding Multi-Injection Molding
Multi-injection molding is a sophisticated manufacturing process used widely in small and medium enterprises (SMEs) to produce parts made from multiple materials or colors in a single operation.
This technology allows for innovative product designs and efficient production, making it a popular choice for creating complex plastic components.
However, with the advantages of multi-injection molding come challenges, particularly in defect prevention and quality control.
Understanding the process and implementing strategic measures can significantly enhance product quality and reduce wastage.
Common Defects in Multi-Injection Molding
When engaged in multi-injection molding, there are specific defects that SMEs frequently encounter.
These include color variations, poor bonding between materials, short shots, flash, and warpage.
Color variations occur when the consistency of color between different sections of a part isn’t uniform.
Poor bonding refers to inadequate adhesion between the different materials in the part, which can compromise the component’s structural integrity.
Short shots occur when the material doesn’t completely fill the mold cavity, leading to incomplete components. Flash involves excess material that protrudes from the edges of the molded part.
Finally, warpage refers to the unintended bending or twisting of molded parts due to uneven cooling or residual stresses.
Defect Prevention Strategies
Preventing defects in multi-injection molding requires a meticulous approach to both the preparation and execution stages of production.
Effective prevention starts with choosing the right materials.
Different materials have varying flow characteristics, shrinkage rates, and mechanical properties.
Selecting materials compatible with each other and suited for the specific product requirements is crucial to minimizing issues like poor bonding and warpage.
Correct mold design is another pivotal factor.
Each cavity and core should be precisely engineered to accommodate the materials’ flow and curing characteristics.
Incorporate proper venting and gating systems to ensure optimal material flow and reduce issues such as short shots and flash.
Regular mold maintenance is also necessary to prevent wear and tear, which can lead to defects.
Testing and simulation should be integral parts of the production process.
Before full-scale production, simulations can predict potential defects and identify ways to address them.
Using software tools that simulate the molding process can help in adjusting injection parameters, mold temperature, and cooling times to achieve the best outcomes.
Quality Control Techniques
Implementing stringent quality control measures is vital for ensuring high standards in multi-injection molding processes.
Frequent inspections during production can help detect issues early, preventing large quantities of defective products.
One effective technique is process monitoring.
Utilize advanced sensors and data analytics to monitor various parameters like temperature, pressure, and material flow in real-time.
This ensures that any deviation from the standard can be corrected immediately, thus maintaining consistent quality.
Regular sample testing should also be performed.
This involves selecting random samples from production batches to check for defects.
Utilizing both visual inspections and more advanced testing methods such as ultrasonic testing or X-ray inspection can reveal internal issues not visible to the naked eye.
Training and continuous improvement practices are essential for sustaining quality control.
Ensure that all involved personnel are well-trained in both the operation of equipment and the principles of defect prevention.
Having a culture of continuous improvement encourages workers to find and implement new solutions to recurring issues.
Leveraging Technology for Better Outcomes
The use of technology can make a significant difference in defect prevention and quality control in multi-injection molding.
Investing in cutting-edge equipment that offers precise control over every aspect of the molding process will lead to better quality products.
Automation can reduce human error by ensuring consistent and repeatable processes.
Robots and automatic systems for inserting and removing components can greatly enhance process efficiency and reliability.
Embracing Industry 4.0 concepts, such as the Internet of Things (IoT), can enable remote monitoring and predictive maintenance which further aids in maintaining high production standards.
IoT-connected machines can alert managers to potential issues before they lead to defects, allowing preemptive actions to be taken.
Collaborative Approaches
Quality in multi-injection molding is often a collaborative effort involving designers, engineers, and production staff.
Encourage collaboration from the design phase to ensure all considerations for defect prevention and quality control are integrated into the product development cycle.
Engage with suppliers to procure high-quality materials and components.
By working closely with them, you can ensure that all incoming materials meet the required specifications, drastically reducing the chances of defects arising from material issues.
Customer feedback is another valuable resource.
Gather information on how products perform in the field and use this data to improve and adapt processes.
By closing the feedback loop, SMEs can enhance both their products and customer satisfaction.
Conclusion
Preventing defects and controlling quality in multi-injection molding processes within SMEs necessitates a structured approach that begins with understanding the process and potential issues.
Through careful material selection, accurate mold design, rigorous quality control, and leveraging modern technology, SMEs can improve their manufacturing outcomes significantly.
Continuous learning, collaboration, and adaptation are key elements that aid in sustaining high-quality standards in this dynamic field.
By integrating these practices, SMEs can reduce costs associated with defects, improve efficiency, and deliver superior products to their customers.
資料ダウンロード
QCD調達購買管理クラウド「newji」は、調達購買部門で必要なQCD管理全てを備えた、現場特化型兼クラウド型の今世紀最高の購買管理システムとなります。
ユーザー登録
調達購買業務の効率化だけでなく、システムを導入することで、コスト削減や製品・資材のステータス可視化のほか、属人化していた購買情報の共有化による内部不正防止や統制にも役立ちます。
NEWJI DX
製造業に特化したデジタルトランスフォーメーション(DX)の実現を目指す請負開発型のコンサルティングサービスです。AI、iPaaS、および先端の技術を駆使して、製造プロセスの効率化、業務効率化、チームワーク強化、コスト削減、品質向上を実現します。このサービスは、製造業の課題を深く理解し、それに対する最適なデジタルソリューションを提供することで、企業が持続的な成長とイノベーションを達成できるようサポートします。
オンライン講座
製造業、主に購買・調達部門にお勤めの方々に向けた情報を配信しております。
新任の方やベテランの方、管理職を対象とした幅広いコンテンツをご用意しております。
お問い合わせ
コストダウンが利益に直結する術だと理解していても、なかなか前に進めることができない状況。そんな時は、newjiのコストダウン自動化機能で大きく利益貢献しよう!
(Β版非公開)